- お役立ち記事
- Mastering Anodizing Processing OEM: Unveiling the Excellence of Japanese Manufacturing
月間77,185名の
製造業ご担当者様が閲覧しています*
*2025年2月28日現在のGoogle Analyticsのデータより
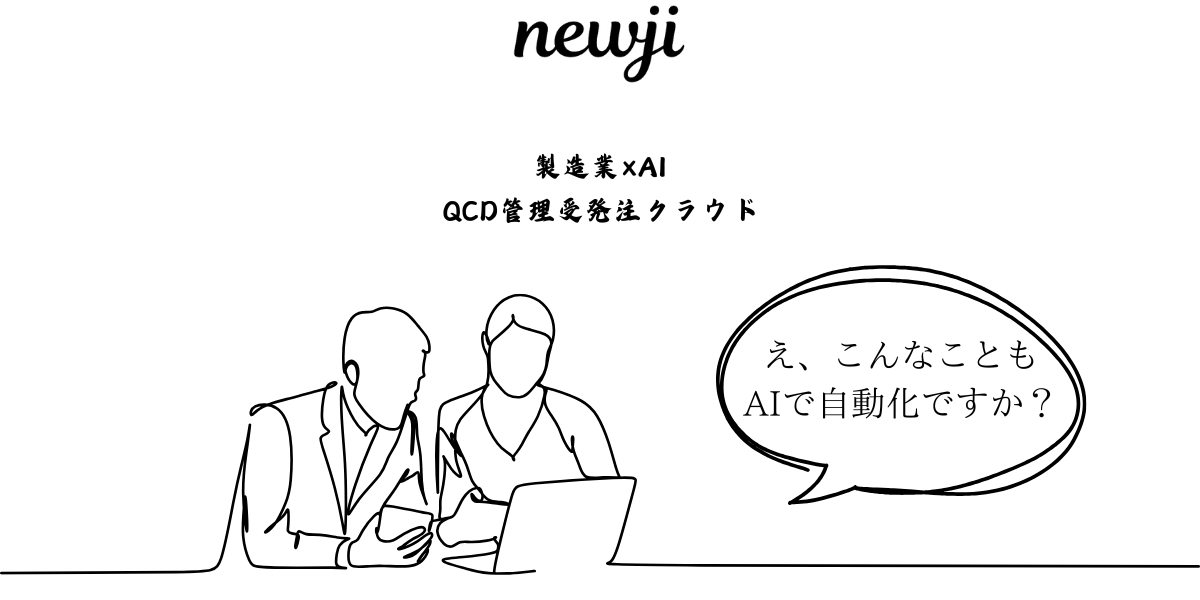
Mastering Anodizing Processing OEM: Unveiling the Excellence of Japanese Manufacturing
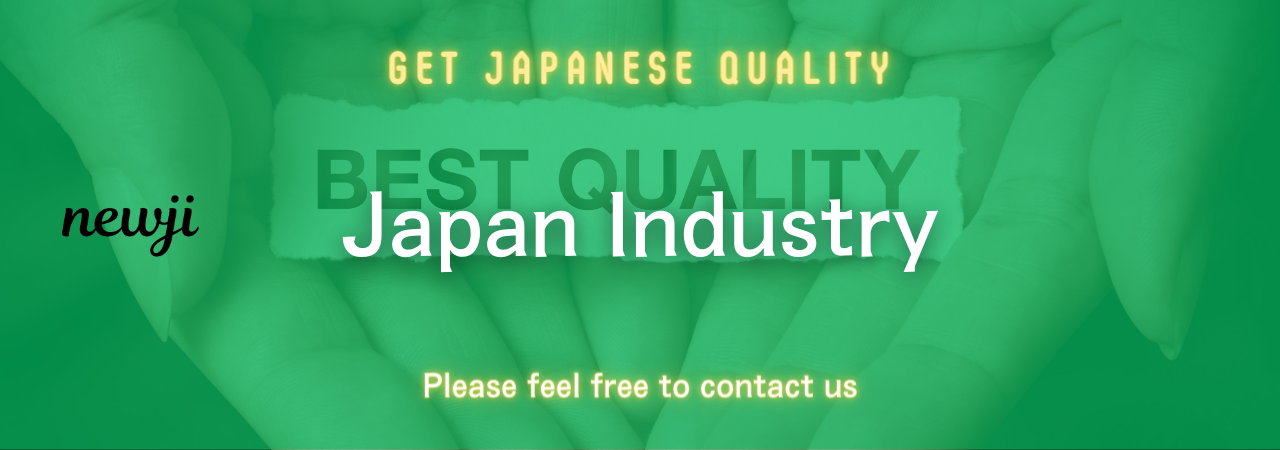
目次
Introduction to Anodizing Processing OEM in Japanese Manufacturing
Japanese manufacturing has long been celebrated for its precision, quality, and efficiency. In the realm of anodizing processing OEM (Original Equipment Manufacturing), Japan stands out as a beacon of excellence. This article delves into the nuances of mastering anodizing processing OEM, highlighting the strengths of Japanese manufacturing and providing practical insights for procurement and purchasing professionals.
Understanding Anodizing Processing OEM
Anodizing is an electrochemical process that enhances the natural oxide layer on metal surfaces, improving corrosion resistance and surface hardness. OEM refers to the partnership where a company designs and manufactures products that are rebranded and sold by another company. In the context of anodizing processing OEM, Japanese manufacturers collaborate with global companies to produce high-quality anodized components tailored to specific requirements.
The Role of OEM in Modern Manufacturing
OEM partnerships are crucial in modern manufacturing as they allow companies to leverage specialized expertise and advanced technologies. By collaborating with Japanese OEMs, businesses can access superior anodizing processes that adhere to stringent quality standards, ensuring the final products meet or exceed market expectations.
Advantages of Partnering with Japanese Anodizing OEMs
Japan’s reputation for manufacturing excellence is built on several key advantages that make its OEMs highly sought after in the anodizing sector.
1. Superior Quality Control
Japanese manufacturers implement rigorous quality control measures at every stage of the anodizing process. This meticulous attention to detail ensures consistent product quality and minimizes defects, providing clients with reliable and durable anodized components.
2. Advanced Technology and Innovation
Japan is at the forefront of technological advancements in anodizing. Japanese OEMs invest heavily in research and development, constantly refining their processes to enhance performance and efficiency. This commitment to innovation results in high-quality finishes and extended product lifespans.
3. Efficient Production Processes
Japanese manufacturing is renowned for its efficiency and lean production methodologies. OEM partners in Japan excel in minimizing waste, optimizing resource utilization, and reducing production lead times, thereby offering cost-effective solutions without compromising quality.
4. Expertise and Skilled Workforce
The technical prowess and expertise of the Japanese workforce are unparalleled. Skilled engineers and technicians ensure that the anodizing processes are executed with precision, addressing complex challenges and delivering superior outcomes.
Challenges and Considerations
While partnering with Japanese anodizing OEMs offers numerous benefits, it’s essential to be aware of potential challenges and considerations to ensure a successful collaboration.
1. Language and Cultural Barriers
Effective communication is vital in any OEM partnership. Language differences and cultural nuances can pose challenges in understanding specifications and expectations. It’s crucial to establish clear communication channels and possibly engage bilingual personnel to facilitate smooth interactions.
2. Higher Initial Costs
Japanese OEMs may have higher initial costs compared to counterparts in other regions. However, the long-term benefits of superior quality, durability, and efficiency often justify the investment, leading to reduced maintenance and replacement costs over time.
3. Navigating Regulatory Requirements
Different countries have varying regulatory standards for anodized products. Ensuring compliance with both Japanese manufacturing standards and the target market’s regulations requires diligent coordination and understanding of the applicable guidelines.
Supplier Negotiation Techniques
Successfully negotiating with Japanese anodizing OEMs requires a strategic approach that respects cultural practices and emphasizes mutual benefits.
1. Building Long-Term Relationships
Japanese business culture places a high value on long-term relationships and trust. Investing time in building a rapport with OEM partners can lead to more favorable terms, better collaboration, and reliable support.
2. Clear and Detailed Specifications
Providing comprehensive and precise specifications prevents misunderstandings and ensures that the OEM fully comprehends the requirements. Detailed documentation, including drawings, material specifications, and quality standards, is essential for effective negotiations.
3. Value-Based Negotiation
Rather than focusing solely on price, emphasize the value that your partnership brings. Highlight aspects such as mutual growth, potential for future collaborations, and the benefits of high-quality outcomes to create a win-win scenario.
4. Flexibility and Adaptability
Demonstrating flexibility in negotiations, such as being open to alternative solutions and adaptable to changing circumstances, can enhance the negotiation process and lead to more amicable agreements.
Market Conditions and Trends
Staying informed about market conditions and emerging trends is crucial for effective procurement and purchasing in the anodizing sector.
1. Growing Demand for Sustainable Practices
There is an increasing emphasis on environmentally friendly manufacturing processes. Japanese OEMs are leading the way in implementing sustainable anodizing practices, such as reducing energy consumption and minimizing hazardous waste, aligning with global sustainability goals.
2. Technological Advancements
Advancements in anodizing technologies, such as digital monitoring and automation, are enhancing process precision and efficiency. Japanese manufacturers are at the cutting edge of integrating these technologies, offering clients state-of-the-art solutions.
3. Global Supply Chain Dynamics
The global supply chain landscape is continually evolving, with factors such as geopolitical shifts and economic fluctuations impacting availability and pricing. Japanese OEMs have demonstrated resilience and adaptability, maintaining consistent supply and quality despite these challenges.
4. Customization and Personalization
The demand for customized anodized products is on the rise. Japanese OEMs excel in providing tailored solutions that meet specific client needs, allowing for greater product differentiation in the market.
Best Practices for Effective Procurement and Purchasing
To maximize the benefits of partnering with Japanese anodizing OEMs, procurement and purchasing professionals should adopt best practices that foster successful collaborations.
1. Conduct Thorough Supplier Evaluations
Evaluate potential OEM partners based on their technical capabilities, quality certifications, production capacity, and reputation in the industry. Thorough assessments help in selecting partners that align with your company’s standards and objectives.
2. Establish Clear Communication Channels
Effective communication is the cornerstone of successful OEM partnerships. Utilize regular meetings, detailed reports, and collaborative platforms to ensure that all parties are aligned and informed throughout the process.
3. Implement Comprehensive Contracts
Drafting detailed contracts that outline specifications, quality standards, delivery schedules, pricing, and terms of payment is essential. Clear contractual agreements prevent misunderstandings and provide a framework for resolving potential disputes.
4. Foster Continuous Improvement
Encourage a culture of continuous improvement by regularly reviewing processes, soliciting feedback, and implementing enhancements. Collaborative efforts to refine anodizing processes can lead to better quality and increased efficiency.
5. Monitor and Manage Performance
Regularly monitor the performance of OEM partners through audits, quality inspections, and key performance indicators (KPIs). Effective performance management ensures that standards are maintained and any issues are promptly addressed.
Leveraging Technical Skills of Japanese Manufacturers
Japanese OEMs bring a wealth of technical expertise that can be leveraged to enhance product quality and performance.
1. Precision Engineering
Japanese manufacturers are renowned for their precision engineering capabilities. This expertise ensures that anodized components meet exact specifications and perform reliably under various conditions.
2. Advanced Surface Treatments
Beyond standard anodizing, Japanese OEMs offer advanced surface treatment options, such as hard anodizing and colored anodizing, providing enhanced aesthetics and functional properties.
3. Integration of Automation
The integration of automation in anodizing processes minimizes human error, increases consistency, and boosts production efficiency. Japanese OEMs’ proficiency in automation technologies ensures high-quality, scalable production.
4. Expertise in Material Science
Japanese manufacturers possess deep knowledge of material science, allowing them to select appropriate alloys and optimize anodizing parameters for different applications, resulting in superior product performance.
Enjoying the Benefits of Procurement from Japan
Procurement from Japanese anodizing OEMs offers numerous benefits that can enhance your company’s competitive edge.
1. Enhanced Product Quality
Access to high-quality anodized components ensures that your products meet customer expectations and stand out in the market for their reliability and durability.
2. Innovation and Competitive Advantage
Partnering with technologically advanced Japanese OEMs allows your company to incorporate cutting-edge features and innovations, providing a significant competitive advantage.
3. Cost Efficiency in the Long Run
While initial costs may be higher, the longevity and reduced maintenance needs of high-quality anodized products lead to cost savings over time, improving overall profitability.
4. Strengthened Brand Reputation
Associating with reputable Japanese manufacturers enhances your brand’s credibility and reputation for quality, fostering customer trust and loyalty.
Case Studies: Success Stories in Anodizing OEM Partnerships
Examining real-world examples of successful OEM partnerships with Japanese anodizing manufacturers provides valuable insights into best practices and the tangible benefits of such collaborations.
Case Study 1: Automotive Industry Collaboration
A leading automotive company partnered with a Japanese anodizing OEM to produce lightweight, corrosion-resistant components for electric vehicles. The collaboration resulted in improved vehicle performance and extended battery life, contributing to the company’s success in the competitive EV market.
Case Study 2: Consumer Electronics Enhancement
A global electronics brand engaged a Japanese OEM to anodize aluminum casings for its premium smartphones. The high-quality finish not only enhanced the aesthetic appeal but also provided additional durability, leading to increased consumer satisfaction and brand loyalty.
Case Study 3: Aerospace Component Manufacturing
An aerospace manufacturer collaborated with a Japanese anodizing partner to produce critical engine components. The superior quality and reliability of the anodized parts met stringent industry standards, ensuring safety and performance in demanding aerospace applications.
Conclusion
Mastering anodizing processing OEM through Japanese manufacturing excellence offers significant advantages for businesses seeking high-quality, reliable, and innovative anodized components. By understanding the strengths and challenges, employing effective negotiation techniques, staying abreast of market trends, and adhering to best practices in procurement and purchasing, companies can fully leverage the benefits of partnering with Japanese OEMs. Embracing this collaboration not only enhances product quality and performance but also strengthens brand reputation and fosters long-term success in the global market.
資料ダウンロード
QCD管理受発注クラウド「newji」は、受発注部門で必要なQCD管理全てを備えた、現場特化型兼クラウド型の今世紀最高の受発注管理システムとなります。
ユーザー登録
受発注業務の効率化だけでなく、システムを導入することで、コスト削減や製品・資材のステータス可視化のほか、属人化していた受発注情報の共有化による内部不正防止や統制にも役立ちます。
NEWJI DX
製造業に特化したデジタルトランスフォーメーション(DX)の実現を目指す請負開発型のコンサルティングサービスです。AI、iPaaS、および先端の技術を駆使して、製造プロセスの効率化、業務効率化、チームワーク強化、コスト削減、品質向上を実現します。このサービスは、製造業の課題を深く理解し、それに対する最適なデジタルソリューションを提供することで、企業が持続的な成長とイノベーションを達成できるようサポートします。
製造業ニュース解説
製造業、主に購買・調達部門にお勤めの方々に向けた情報を配信しております。
新任の方やベテランの方、管理職を対象とした幅広いコンテンツをご用意しております。
お問い合わせ
コストダウンが利益に直結する術だと理解していても、なかなか前に進めることができない状況。そんな時は、newjiのコストダウン自動化機能で大きく利益貢献しよう!
(β版非公開)