- お役立ち記事
- Mastering Efficiency: The Art of Push Production in Japanese Manufacturing
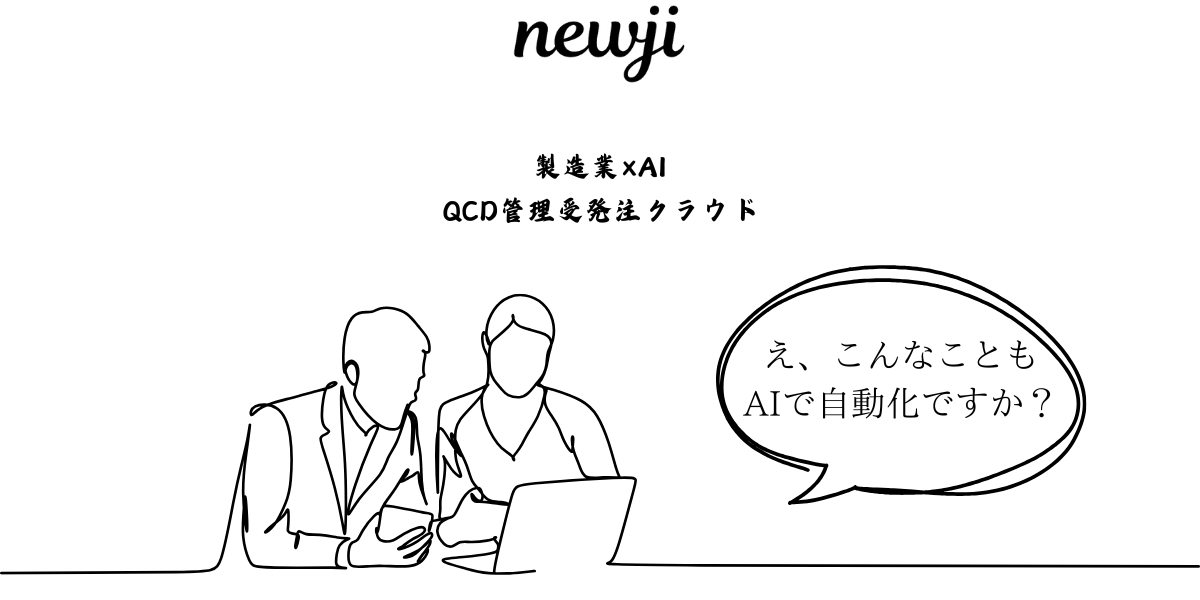
Mastering Efficiency: The Art of Push Production in Japanese Manufacturing
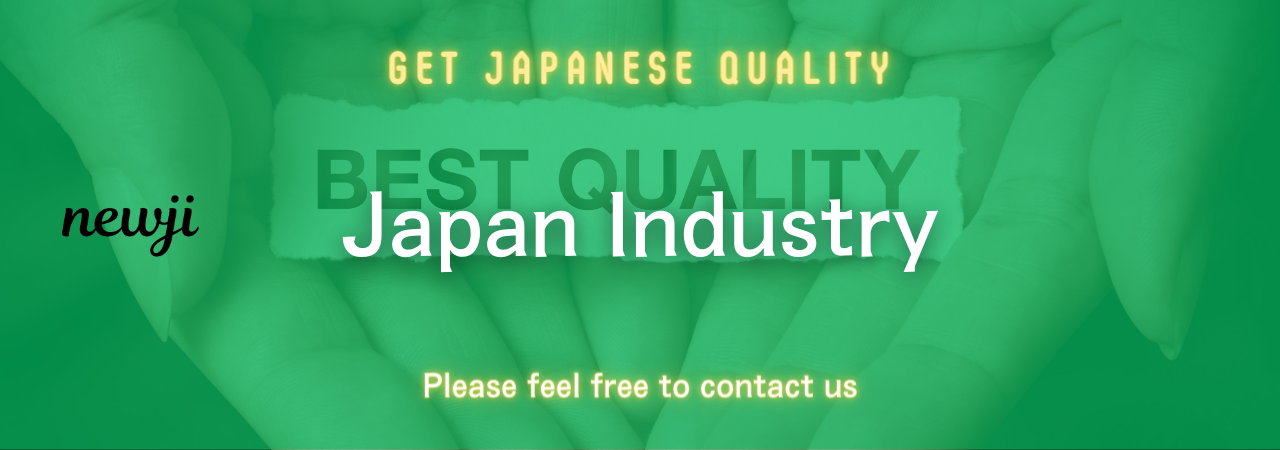
目次
Introduction to Push Production in Japanese Manufacturing
In the world of manufacturing, efficient production processes are crucial to meeting market demands and maintaining competitive advantage.
Push production, a method widely used in Japanese manufacturing, emphasizes the efficient use of resources by pushing products through the production line based on forecasted demand.
This approach contrasts with pull production, which focuses on producing goods in response to actual customer demand.
Understanding push production and its application in Japanese manufacturing can offer invaluable insights for procurement and purchasing professionals aiming to optimize their operations.
The Fundamentals of Push Production
Push production is driven by predictions and forecasts.
Manufacturers produce goods based on projected customer demand and inventory levels, which helps streamline resource allocation and optimize production schedules.
In Japanese manufacturing, this approach is finely tuned to minimize waste and maximize efficiency, embodying the principles of lean manufacturing and Just-In-Time (JIT) production.
Key components of push production include advance planning, scheduling, and performance monitoring to ensure that production stays aligned with market demands.
Advantages of Push Production
One of the primary advantages of push production is the ability to maintain steady production flow and reduce idle time in manufacturing facilities.
As production is planned in advance, manufacturers can achieve higher equipment utilization rates, lower unit costs, and increased output.
This approach also facilitates bulk purchasing of raw materials and components, often resulting in cost savings.
In Japanese manufacturing, push production is supported by sophisticated forecasting models and planning systems that allow companies to respond dynamically to changes in market conditions.
Implemented effectively, this method can improve inventory management, reduce lead times, and ensure reliable product availability.
Disadvantages and Challenges of Push Production
Despite its benefits, push production also presents certain challenges.
Foremost among these is the risk of overproduction, which can lead to excess inventory, increased storage costs, and wastage.
Additionally, inaccuracies in demand forecasting can result in stockouts or surplus, affecting customer satisfaction and tying up capital.
Japanese manufacturers address these challenges through advanced analytics and flexible manufacturing systems that adapt to fluctuations in demand.
The importance of maintaining balance in forecasting accuracy and responsiveness to market shifts is a critical component of successful push production.
Supplier Negotiation Techniques
When engaging with Japanese suppliers, manufacturers must adopt effective negotiation strategies to leverage the benefits of push production.
Building strong, collaborative relationships with suppliers is key to ensuring timely delivery of high-quality materials and components, which are crucial for smooth production operations.
Cultivating Trust and Long-Term Partnerships
Japanese business culture places a high value on trust and long-term partnerships.
Procurement professionals should prioritize establishing rapport and mutual respect with suppliers, fostering open communication, and developing a shared understanding of business goals.
This approach encourages collaborative problem-solving and supports continuous improvement in product quality and delivery efficiency.
Leveraging Just-In-Time (JIT) Principles
The adoption of JIT principles in supplier negotiations can significantly enhance push production efficiency.
By working closely with suppliers to synchronize delivery schedules with production needs, manufacturers can reduce inventory levels and minimize waste.
This collaborative approach requires transparent communication and the alignment of forecasting and logistics strategies to ensure seamless integration with the supplier’s operations.
Understanding Market Conditions and Cost Structures
Negotiating effectively with Japanese suppliers also involves a deep understanding of market conditions and industry cost structures.
Procurement professionals must stay informed about fluctuations in raw material prices, labor costs, and currency exchange rates to negotiate favorable terms and maintain competitive pricing.
By leveraging this knowledge, manufacturers can secure better deals and enhance their cost-efficiency in push production.
Best Practices for Implementing Push Production
To fully harness the potential of push production, manufacturers should adhere to proven best practices that enhance efficiency and foster continuous improvement.
Optimizing Production Planning and Scheduling
Effective production planning and scheduling are foundational to successful push production.
Manufacturers should utilize advanced forecasting tools and planning software to create accurate production schedules that align with demand projections.
Regular reviews and adjustments to production plans can help ensure responsiveness to changes in market conditions and customer requirements.
Emphasizing Workforce Training and Engagement
A well-trained and engaged workforce is essential for the smooth implementation of push production.
Investing in continuous employee training and development helps ensure that staff have the skills and knowledge necessary to operate efficiently and adapt to new manufacturing technologies and practices.
Encouraging employee involvement in improvement initiatives can also drive innovation and enhance production processes.
Implementing Robust Quality Control Measures
Quality control is a vital aspect of push production in Japanese manufacturing.
Manufacturers should implement comprehensive quality management systems that include regular inspections, testing, and feedback loops to identify and address defects promptly.
Adopting a culture of quality and continuous improvement helps maintain product standards and minimize rework and waste.
Utilizing Technology and Automation
Modern manufacturing technologies and automation play a crucial role in optimizing push production.
Japanese manufacturers leverage advanced robotics, data analytics, and IoT devices to enhance production efficiency, monitor performance, and ensure precision in manufacturing processes.
Integrating these technologies can lead to improved productivity, reduced operational costs, and higher product quality.
The Future of Push Production in Japanese Manufacturing
As global market dynamics continue to evolve, the future of push production in Japanese manufacturing will be shaped by emerging trends and innovations.
Manufacturers will need to adopt a proactive approach to adapting their push production strategies to remain competitive and sustainable in the long term.
Embracing Industry 4.0 Technologies
Industry 4.0 technologies, such as artificial intelligence, machine learning, and the Internet of Things, are poised to revolutionize push production in Japanese manufacturing.
These technologies enable manufacturers to collect and analyze vast amounts of data in real time, improving forecasting accuracy, optimizing production schedules, and enhancing decision-making processes.
By embracing these innovations, manufacturers can achieve unprecedented levels of efficiency and responsiveness.
Sustainability and Environmental Considerations
As environmental awareness grows, manufacturers must prioritize sustainability in their push production practices.
Japanese manufacturers are increasingly focusing on reducing energy consumption, minimizing waste, and using eco-friendly materials to align with environmental regulations and consumer expectations.
Sustainability initiatives not only benefit the planet but also contribute to long-term cost savings and improved brand reputation.
Global Supply Chain Integration
In an interconnected global economy, Japanese manufacturers will need to enhance their supply chain integration to support push production effectively.
Building resilient and agile supply chains that can respond swiftly to disruptions and opportunities will be crucial.
Collaboration across borders and adopting digital supply chain solutions will help manufacturers achieve seamless operations and strengthen their competitive edge.
Conclusion
Mastering the art of push production in Japanese manufacturing involves navigating a complex landscape of planning, negotiation, and innovation.
By understanding the fundamentals of push production, cultivating strong supplier relationships, and adopting best practices, manufacturers can optimize their operations and achieve lasting success.
As the industry continues to evolve, embracing new technologies and sustainable practices will be key to maintaining a competitive advantage and meeting future challenges head-on.
資料ダウンロード
QCD調達購買管理クラウド「newji」は、調達購買部門で必要なQCD管理全てを備えた、現場特化型兼クラウド型の今世紀最高の購買管理システムとなります。
ユーザー登録
調達購買業務の効率化だけでなく、システムを導入することで、コスト削減や製品・資材のステータス可視化のほか、属人化していた購買情報の共有化による内部不正防止や統制にも役立ちます。
NEWJI DX
製造業に特化したデジタルトランスフォーメーション(DX)の実現を目指す請負開発型のコンサルティングサービスです。AI、iPaaS、および先端の技術を駆使して、製造プロセスの効率化、業務効率化、チームワーク強化、コスト削減、品質向上を実現します。このサービスは、製造業の課題を深く理解し、それに対する最適なデジタルソリューションを提供することで、企業が持続的な成長とイノベーションを達成できるようサポートします。
オンライン講座
製造業、主に購買・調達部門にお勤めの方々に向けた情報を配信しております。
新任の方やベテランの方、管理職を対象とした幅広いコンテンツをご用意しております。
お問い合わせ
コストダウンが利益に直結する術だと理解していても、なかなか前に進めることができない状況。そんな時は、newjiのコストダウン自動化機能で大きく利益貢献しよう!
(Β版非公開)