- お役立ち記事
- Mastering Energy Efficiency: The Role of Compressor Inverters in Japanese Manufacturing
月間76,176名の
製造業ご担当者様が閲覧しています*
*2025年3月31日現在のGoogle Analyticsのデータより
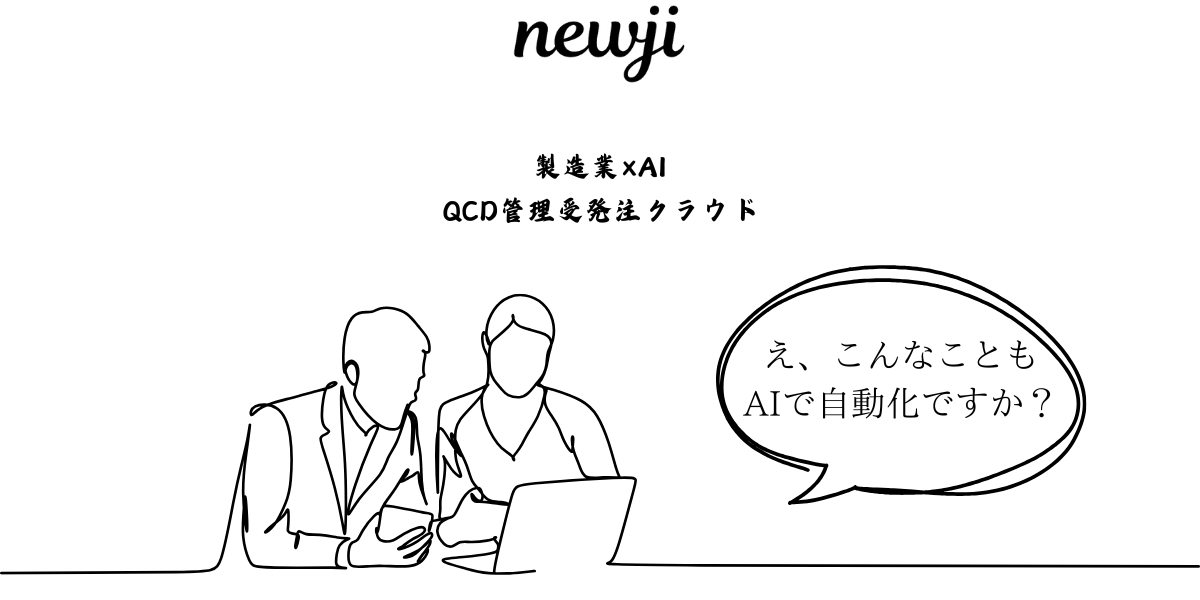
Mastering Energy Efficiency: The Role of Compressor Inverters in Japanese Manufacturing
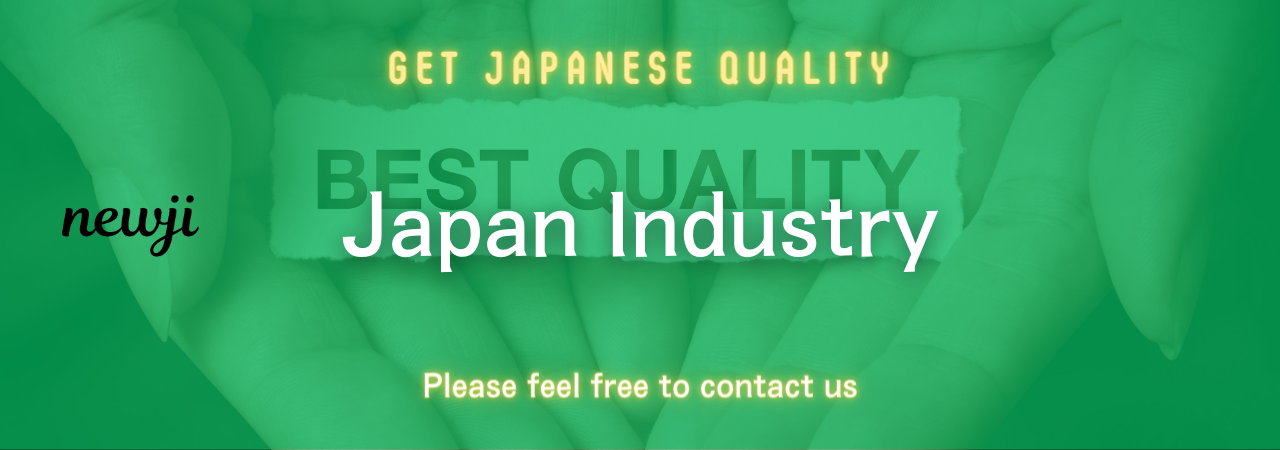
目次
Understanding Compressor Inverters
Before diving into the role of compressor inverters in Japanese manufacturing, it’s crucial to establish a fundamental understanding of what compressor inverters are and how they function.
Compressor inverters, often referred to as variable speed drives (VSD), are devices that adjust the speed and power of a compressor motor.
By managing the motor’s speed to match the varying demand for compressed air, these inverters bring significant energy savings and operational benefits.
The Importance of Energy Efficiency in Manufacturing
Energy efficiency is a priority in modern manufacturing for numerous reasons.
Reducing energy consumption not only slashes operational costs but also contributes to an organization’s environmental sustainability goals.
In Japan, with its strong focus on energy conservation and technology-driven solutions, compressor inverters have become an essential tool in the quest for efficient manufacturing operations.
The Economic Imperative
Energy represents a substantial portion of manufacturing costs.
For instance, in energy-intensive industries like automobile manufacturing and electronics production, electricity can account for up to 30% of total operating expenses.
Compressor inverters help reduce these costs by optimizing motor performance and minimizing energy waste.
Environmental Responsibility
Japan has stringent regulations regarding energy use and carbon emissions.
By adopting compressor inverters, companies can comply with these regulations while also enhancing their corporate social responsibility (CSR) profiles.
Lower energy consumption directly translates to reduced greenhouse gas emissions, positioning companies as environmentally responsible entities.
Advantages of Using Compressor Inverters
The adoption of compressor inverters in Japanese manufacturing comes with multiple benefits.
Here are some of the most notable advantages:
Energy Savings
The most direct benefit of compressor inverters is energy savings.
Traditional compressors operate at a constant speed, which can lead to energy inefficiencies when the air demand fluctuates.
Compressor inverters adjust the motor speed in response to real-time demand, thus optimizing energy consumption.
Extended Equipment Lifespan
Inverters alleviate the stress on compressors by reducing the start-stop cycle frequency.
This results in less wear and tear, thereby extending the lifespan of the equipment.
Over time, this means lower maintenance costs and less frequent equipment replacement.
Increased System Stability
Optimized motor speed management ensures consistent air pressure, enhancing the overall stability of the compressed air system.
Steady air pressure can improve production quality and reduce the incidence of defects, which is critical in high-precision manufacturing sectors.
Noise Reduction
Variable speed operation often results in quieter compressor functioning.
This can lead to a more pleasant working environment for employees, potentially increasing productivity and morale.
Challenges and Disadvantages
Despite the numerous advantages, the implementation of compressor inverters is not without its challenges.
Understanding these potential downsides is crucial for making informed procurement decisions.
Initial Cost
The upfront cost of compressor inverters can be significant.
This includes not only the expense of the inverter itself but also the costs associated with installation and potential system modifications.
However, many companies find that the energy savings and reduced maintenance costs offer a favorable Return on Investment (ROI) over time.
Complexity of Implementation
Integrating compressor inverters into existing systems can be complex.
It often requires specialized knowledge and skills, both of which might necessitate hiring additional personnel or investing in training for current employees.
Moreover, system downtime during installation and testing must be managed to minimize disruption to ongoing operations.
Maintenance Requirements
While compressor inverters can reduce wear and tear on compressors, the inverters themselves require regular maintenance.
Ensuring that personnel are trained to maintain these systems is necessary to avoid unexpected downtimes and costly repairs.
Best Practices for Supplier Negotiation
When dealing with suppliers of compressor inverters, several best practices can help ensure a successful procurement process.
Detailed Technical Specifications
Be clear about your technical requirements and operating conditions.
Provide detailed specifications to potential suppliers to ensure that the products they offer are suitable for your needs.
This step helps prevent future performance issues and compatibility problems.
Energy Efficiency Analysis
Request an energy efficiency analysis from suppliers.
This analysis should include potential energy savings, ROI estimates, and comparisons with traditional compressor systems.
Such data can be critical in justifying the initial investment to stakeholders.
Supplier History and Reputation
Investigate the supplier’s history and reputation in the industry.
Look for references or case studies from other Japanese manufacturers who have implemented similar solutions.
A supplier with a proven track record is more likely to deliver reliable products and services.
After-sales Support
Evaluate the after-sales support offered by suppliers.
This includes warranties, maintenance services, and the availability of spare parts.
A robust support system can significantly reduce the long-term costs and risks associated with compressor inverters.
Market Conditions and Trends
Staying abreast of market conditions and trends is essential for effective procurement and purchasing decisions.
Technological Advancements
The field of compressor inverters is continually evolving, with new advancements aimed at improving efficiency and reducing costs.
Keeping up with these technological developments ensures that you can leverage the latest solutions for maximum benefit.
Regulatory Environment
Japan’s regulatory environment regarding energy consumption and efficiency is stringent.
Being aware of current and upcoming regulations can help you stay compliant and avoid potential fines or operational disruptions.
Economic Factors
Economic conditions, such as fluctuations in energy prices and currency exchange rates, can impact the cost-effectiveness of compressor inverters.
Monitoring these factors helps in making timely and financially sound purchasing decisions.
Case Studies and Real-World Applications
Examining case studies and real-world applications can provide valuable insights into the practical benefits and challenges of compressor inverter implementation.
Automotive Industry
In the automotive industry, where precise air pressure is crucial for various manufacturing processes, the adoption of compressor inverters has led to remarkable improvements in both efficiency and product quality.
Manufacturers have reported significant energy savings and enhanced operational stability.
Electronics Manufacturing
For electronics manufacturers, maintaining consistent air quality and pressure is vital for product integrity.
Compressor inverters have been instrumental in achieving these goals, resulting in lower defect rates and higher production yields.
Conclusion
Mastering energy efficiency through the use of compressor inverters is a strategy that offers substantial benefits for Japanese manufacturing companies.
While there are challenges to be considered, the advantages in terms of energy savings, equipment longevity, and operational stability make compressor inverters a valuable investment.
By following best practices in supplier negotiation and keeping informed about market trends and technological advancements, manufacturers can effectively leverage this technology to enhance their operations.
The commitment to energy efficiency not only drives economic performance but also strengthens environmental stewardship, ensuring a sustainable future for the manufacturing industry.
資料ダウンロード
QCD管理受発注クラウド「newji」は、受発注部門で必要なQCD管理全てを備えた、現場特化型兼クラウド型の今世紀最高の受発注管理システムとなります。
ユーザー登録
受発注業務の効率化だけでなく、システムを導入することで、コスト削減や製品・資材のステータス可視化のほか、属人化していた受発注情報の共有化による内部不正防止や統制にも役立ちます。
NEWJI DX
製造業に特化したデジタルトランスフォーメーション(DX)の実現を目指す請負開発型のコンサルティングサービスです。AI、iPaaS、および先端の技術を駆使して、製造プロセスの効率化、業務効率化、チームワーク強化、コスト削減、品質向上を実現します。このサービスは、製造業の課題を深く理解し、それに対する最適なデジタルソリューションを提供することで、企業が持続的な成長とイノベーションを達成できるようサポートします。
製造業ニュース解説
製造業、主に購買・調達部門にお勤めの方々に向けた情報を配信しております。
新任の方やベテランの方、管理職を対象とした幅広いコンテンツをご用意しております。
お問い合わせ
コストダウンが利益に直結する術だと理解していても、なかなか前に進めることができない状況。そんな時は、newjiのコストダウン自動化機能で大きく利益貢献しよう!
(β版非公開)