- お役立ち記事
- Mastering Error Correction: The Secret Behind Japanese Manufacturing Excellence
Mastering Error Correction: The Secret Behind Japanese Manufacturing Excellence
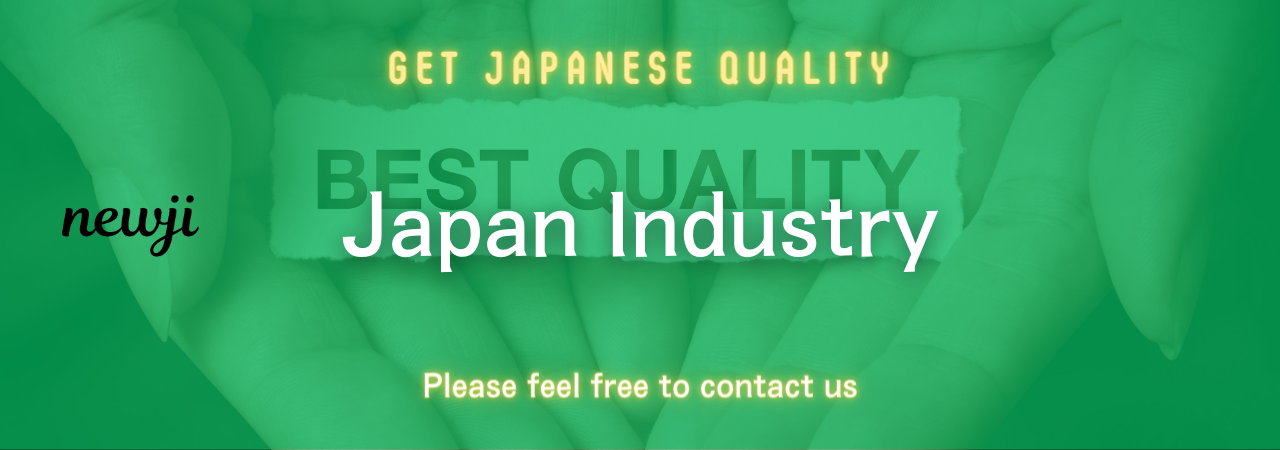
目次
Introduction to Japanese Manufacturing Excellence
Japanese manufacturing has long been synonymous with unparalleled quality, efficiency, and precision.
From the automotive giants like Toyota and Honda to consumer electronics leaders like Sony and Panasonic, Japanese manufacturers have consistently set global benchmarks in quality and innovation.
One of the critical factors behind their success is the mastery of error correction, a concept deeply rooted in Japanese manufacturing philosophies such as Kaizen, Jidoka, and Poka-Yoke.
These methodologies focus on identifying errors quickly, rectifying them efficiently, and preventing their recurrence, thereby ensuring a high level of quality control and continuous improvement.
This article delves into the nuances of error correction in Japanese manufacturing, offering practical insights and strategies to harness these principles effectively.
The Foundation of Error Correction in Japanese Manufacturing
Error correction in Japanese manufacturing is not just a process; it is a culture ingrained within the organizational fabric.
At the heart of this culture lies the principle of Kaizen, which translates to “continuous improvement.”
This philosophy encourages every employee, from top management to shop floor workers, to strive for constant betterment in their tasks.
Coupled with Jidoka, which emphasizes automation with a human touch, and Poka-Yoke, a mechanism for error-proofing processes, Japanese manufacturers have developed a robust framework for identifying and correcting errors efficiently.
Kaizen: The Continuous Improvement Culture
Kaizen advocates for incremental improvements rather than drastic changes, promoting a steady, methodical approach to problem-solving.
Employees are encouraged to identify issues, suggest solutions, and implement them within their scope of work.
This not only facilitates prompt error correction but also fosters a sense of ownership and accountability among the workforce.
Kaizen is often implemented through small group activities, known as quality circles, where employees collectively brainstorm and address operational inefficiencies.
Jidoka: Automation with a Human Touch
Jidoka, another cornerstone of Japanese manufacturing excellence, emphasizes the importance of integrating human intelligence and automation.
Machines and production lines are designed to automatically detect and stop when anomalies or defects are identified.
This empowers operators to rectify issues immediately, preventing defective products from advancing through the production process.
By integrating Jidoka, Japanese manufacturers ensure that quality is built into the process rather than relying on end-of-line inspections to catch errors.
Poka-Yoke: Error-Proofing Mechanisms
Poka-Yoke, which means “mistake-proofing,” incorporates simple and often inexpensive mechanisms to prevent errors from occurring.
These can be as straightforward as designing jigs and fixtures that only allow components to be assembled in the correct orientation or as complex as automated sensors that detect and reject defective parts.
The primary goal of Poka-Yoke is to eliminate the potential for human error, ensuring that processes are inherently error-resistant.
Advantages of Effective Error Correction
Mastering error correction offers several benefits that significantly enhance manufacturing performance and competitiveness.
Enhanced Product Quality
By promptly identifying and rectifying errors, Japanese manufacturers ensure that only high-quality products proceed through each production stage.
This reduces the incidence of defects reaching the end customer, thereby enhancing product reliability and customer satisfaction.
Increased Operational Efficiency
Effective error correction streamlines production processes, minimizing downtime and waste caused by defects.
This leads to improved throughput and operational efficiency, enabling manufacturers to produce more with less.
Cost Savings
Reducing defects and rework translates to substantial cost savings.
Resources are utilized more efficiently, and less scrap and rework mean lower material and labor costs, contributing to improved profitability.
Employee Empowerment and Engagement
Cultivating a culture of continuous improvement and error correction empowers employees to take an active role in problem-solving.
This fosters a sense of ownership and engagement, leading to a more motivated and committed workforce.
Challenges in Implementing Error Correction
While the benefits of effective error correction are significant, implementing these practices can pose challenges.
Understanding and addressing these hurdles is crucial for successful adoption.
Cultural Shift
Adopting a culture of continuous improvement and error correction often requires a significant shift in mindset.
Organizations must foster an environment where employees feel encouraged to identify and report errors without fear of blame or retribution.
This demands strong leadership commitment and consistent communication to nurture a culture of openness and accountability.
Training and Skill Development
Effective error correction relies on a skilled and knowledgeable workforce.
Organizations must invest in training and development programs to equip employees with the necessary skills to identify, analyze, and rectify errors.
Continuous training ensures that the workforce remains adept at utilizing error correction methodologies.
Integration with Existing Processes
Integrating error correction practices with existing production processes can be challenging.
Organizations must carefully assess and modify their processes to incorporate error detection and correction mechanisms without disrupting operations.
This may require collaboration between various departments, including engineering, production, and quality assurance.
Best Practices for Mastering Error Correction
To effectively harness the benefits of error correction, organizations can adopt several best practices.
Implement a Robust Quality Management System (QMS)
A comprehensive QMS provides a structured framework for identifying, documenting, analyzing, and rectifying errors.
It ensures systematic and consistent error correction practices across the organization.
Regular audits and reviews of the QMS help identify areas for improvement and ensure ongoing adherence to quality standards.
Empower Employees
Encourage employees at all levels to participate in error correction activities.
Provide them with the necessary tools, training, and resources to identify and address issues within their scope of work.
Recognize and reward employees for their contributions to error correction and continuous improvement initiatives.
Leverage Technology and Automation
Utilize technology and automation to enhance error detection and correction capabilities.
Implement automated inspection systems, sensors, and data analytics to identify and rectify errors in real-time.
Integrating advanced technologies can significantly improve the accuracy and efficiency of error correction processes.
Foster Collaboration and Communication
Promote collaboration and open communication between departments to facilitate seamless error correction.
Encourage cross-functional teams to work together to identify root causes of errors and develop effective solutions.
Regular meetings and feedback sessions ensure that issues are promptly addressed and that best practices are shared across the organization.
Supplier Negotiation Techniques for Error Correction
Effective supplier negotiation is critical for ensuring that error correction practices are seamlessly integrated into the supply chain.
Here are some key techniques:
Establish Clear Quality Expectations
Clearly communicate your quality expectations and error correction requirements to suppliers.
Set measurable quality standards and performance metrics to ensure alignment with your organization’s quality objectives.
Collaborate on Continuous Improvement Initiatives
Work collaboratively with suppliers to identify and address errors and inefficiencies.
Encourage suppliers to adopt continuous improvement practices and share insights and best practices.
Jointly develop and implement improvement plans that benefit both parties.
Regular Audits and Assessments
Conduct regular audits and assessments of supplier processes to ensure compliance with quality standards.
Identify areas for improvement and work collaboratively with suppliers to address any issues identified during audits.
Incentive Programs
Implement incentive programs to reward suppliers who consistently meet or exceed quality standards.
Recognize and reward suppliers who actively participate in continuous improvement and error correction initiatives.
Incentives can include preferred supplier status, longer-term contracts, and financial bonuses.
Market Conditions and Trends
Understanding market conditions and trends is essential for mastering error correction in Japanese manufacturing.
Here are some current trends:
Emphasis on Sustainability
There is a growing emphasis on sustainability and environmentally-friendly practices in manufacturing.
Organizations are increasingly adopting sustainable error correction practices that minimize waste and reduce environmental impact.
Digital Transformation
The digital transformation of manufacturing processes is accelerating, driven by advancements in Industry 4.0 technologies.
Smart factories and IoT-enabled devices offer enhanced error detection, data analytics, and real-time monitoring capabilities.
Organizations are leveraging these technologies to improve their error correction strategies.
Focus on Resilience
The COVID-19 pandemic has highlighted the importance of resilience in manufacturing.
Organizations are prioritizing error correction practices that enhance agility, flexibility, and responsiveness to disruptions.
Building resilient supply chains and production processes is critical for maintaining continuity and competitiveness.
Conclusion
Mastering error correction is the secret behind Japanese manufacturing excellence.
By integrating principles such as Kaizen, Jidoka, and Poka-Yoke, organizations can create a robust framework for identifying, rectifying, and preventing errors.
While implementing these practices poses challenges, the benefits in terms of enhanced quality, operational efficiency, cost savings, and employee engagement are significant.
By adopting best practices, fostering a culture of continuous improvement, and leveraging technology, organizations can effectively harness the power of error correction.
Additionally, effective supplier negotiation and staying abreast of market trends further contribute to successful error correction initiatives.
Ultimately, mastering error correction not only elevates product quality but also drives manufacturing excellence and competitiveness in the global market.
資料ダウンロード
QCD調達購買管理クラウド「newji」は、調達購買部門で必要なQCD管理全てを備えた、現場特化型兼クラウド型の今世紀最高の購買管理システムとなります。
ユーザー登録
調達購買業務の効率化だけでなく、システムを導入することで、コスト削減や製品・資材のステータス可視化のほか、属人化していた購買情報の共有化による内部不正防止や統制にも役立ちます。
NEWJI DX
製造業に特化したデジタルトランスフォーメーション(DX)の実現を目指す請負開発型のコンサルティングサービスです。AI、iPaaS、および先端の技術を駆使して、製造プロセスの効率化、業務効率化、チームワーク強化、コスト削減、品質向上を実現します。このサービスは、製造業の課題を深く理解し、それに対する最適なデジタルソリューションを提供することで、企業が持続的な成長とイノベーションを達成できるようサポートします。
オンライン講座
製造業、主に購買・調達部門にお勤めの方々に向けた情報を配信しております。
新任の方やベテランの方、管理職を対象とした幅広いコンテンツをご用意しております。
お問い合わせ
コストダウンが利益に直結する術だと理解していても、なかなか前に進めることができない状況。そんな時は、newjiのコストダウン自動化機能で大きく利益貢献しよう!
(Β版非公開)