- お役立ち記事
- Mastering Failure Analysis: Insights from Japanese Manufacturing Excellence
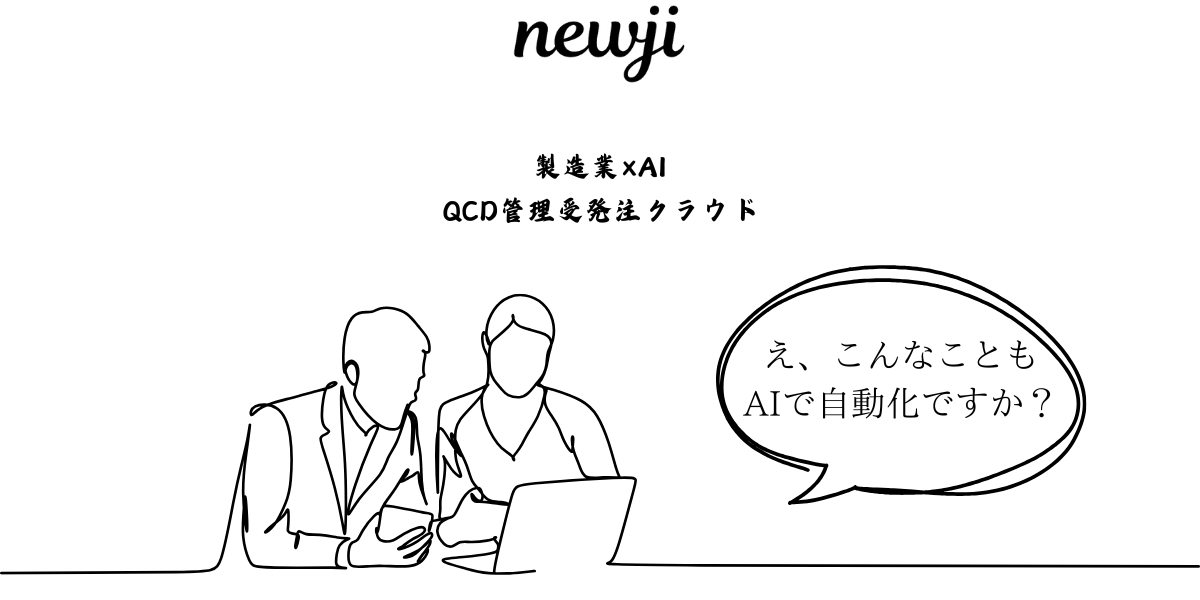
Mastering Failure Analysis: Insights from Japanese Manufacturing Excellence
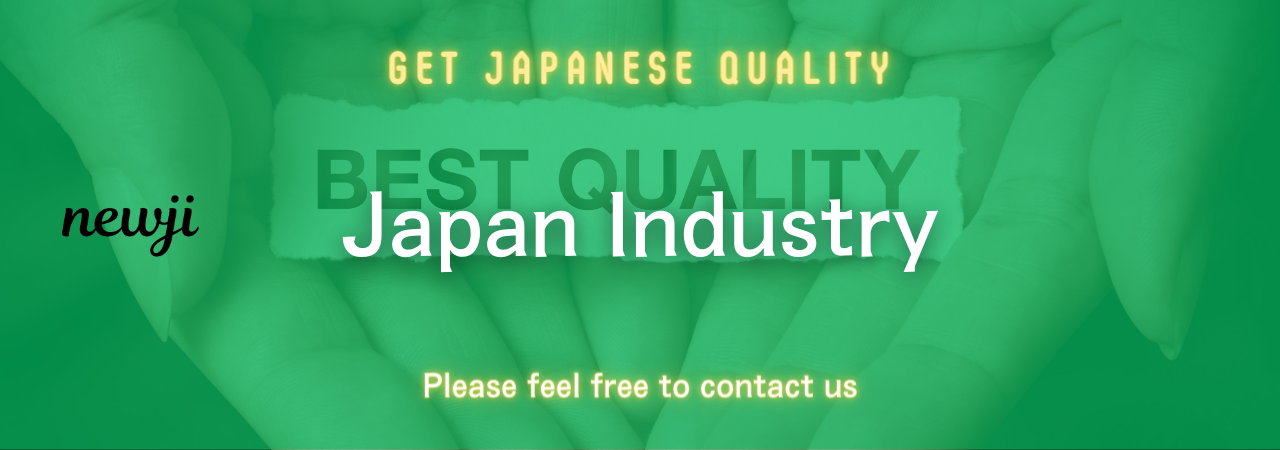
目次
Introduction
Failure analysis is an indispensable aspect of manufacturing that determines the root cause of product failures and mitigates the accompanying risks. Japanese manufacturing companies have long been at the forefront of this practice with their relentless dedication to quality, precision, and efficiency. This article provides a detailed exploration of failure analysis from the perspective of Japanese manufacturing excellence, focusing on practical techniques, benefits, and best practices.
The Importance of Failure Analysis in Manufacturing
Failure analysis is essential in manufacturing for several reasons. It ensures product reliability, enhances safety, and promotes customer satisfaction by preventing recurrent defects. Understanding why a product or component fails can lead to the development of more robust design and manufacturing processes. Moreover, failure analysis contributes to reducing costs associated with recalls, rework, and warranty claims.
Types of Failures
Failures in manufacturing can be broadly classified into three categories:
– **Material Failures:** These are due to defects or degradation in the materials used.
– **Design Failures:** Occur when there are inherent flaws in the product design.
– **Process Failures:** Stem from issues in the production process, such as contamination or equipment malfunction.
Japanese Approaches to Failure Analysis
Japanese manufacturing companies employ various methodologies to understand and resolve product failures. Their approach is characterized by thoroughness, a high level of detail, and continuous improvement.
Root Cause Analysis (RCA)
Root Cause Analysis is a fundamental component of failure analysis. Japanese companies often use the 5 Whys technique, a problem-solving method that involves asking “Why?” five times or more until the fundamental cause of a problem is identified. This technique ensures that the analysis goes beyond superficial symptoms to determine the true underlying issues.
Kepner-Tregoe Problem Solving and Decision-Making
This method involves a systematic approach to problem-solving by distinguishing between the symptoms of a problem and the actual cause. It helps teams to prioritize issues and manage problem complexity effectively. Japanese manufacturers rely on this technique for its structured nature and its ability to produce clear, actionable results.
Advantages of Using Japanese Failure Analysis Techniques
Precision and Detail
Japanese manufacturing is renowned for its meticulous attention to detail. This focus ensures that failure analysis is comprehensive and leaves no stone unturned. Identifying the exact point of failure allows for the implementation of precise corrective measures, enhancing product quality.
Continuous Improvement (Kaizen)
The philosophy of continuous improvement, or Kaizen, is deeply ingrained in Japanese manufacturing practices. It emphasizes small, incremental changes that cumulatively lead to significant improvements over time. This perspective ensures that failure analysis is not a one-time activity but an ongoing process that contributes to long-term success.
Cross-Functional Collaboration
In Japanese companies, failure analysis often involves cross-functional teams comprising members from different departments. This collaboration brings diverse perspectives and skills into the analysis, leading to more thorough and innovative solutions.
Challenges and Limitations
Despite its numerous advantages, the Japanese approach to failure analysis is not without challenges.
Time-Consuming Process
The detailed and methodical nature of Japanese failure analysis can be time-consuming. While this ensures comprehensive results, it may not always be practical for companies with tight deadlines and fast-paced production schedules.
Initial High Costs
Implementing robust failure analysis techniques requires investment in training, technology, and manpower. The initial costs can be high, which may deter small and medium-sized enterprises from adopting these methods.
Cultural Adaptation
The success of the Japanese approach is partly rooted in the country’s unique cultural values, including discipline, precision, and teamwork. Companies in other regions may need to adapt these techniques to align with their own cultural contexts, which can be challenging.
Practical Implementation of Failure Analysis Techniques
Implementing failure analysis techniques effectively requires a structured approach. Here are some best practices based on Japanese manufacturing excellence:
1. Establish a Dedicated Team
Create a cross-functional team dedicated to failure analysis. This team should include members from engineering, production, quality control, and procurement to ensure diverse inputs and comprehensive analysis.
2. Training and Development
Invest in training programs to familiarize your team with various failure analysis methods and tools. Education and regular workshops can help in building the required expertise and keeping the team updated with the latest techniques.
3. Document Findings and Share Knowledge
Documenting the findings of each failure analysis session is crucial. This documentation should be stored in a centralized repository and shared across the organization to disseminate knowledge and avoid repeating the same mistakes.
4. Use Advanced Tools and Software
Leverage advanced analytical tools and software to aid the failure analysis process. Technologies like scanning electron microscopes (SEM), X-ray diffraction (XRD), and Finite Element Analysis (FEA) can provide deeper insights into the causes of failures, leading to more accurate solutions.
5. Incorporate Customer Feedback
Include customer feedback in your failure analysis process. Understanding customer complaints and issues can provide real-world insights that might be missed during internal analysis. Regularly communicate with customers and incorporate their feedback to improve product quality.
Case Studies: Lessons from Japanese Manufacturing
Examining case studies from Japanese manufacturing companies can provide valuable insights into practical failure analysis applications.
Case Study 1: Toyota’s Approach to Quality Control
Toyota, a leader in automotive manufacturing, has set benchmarks with its failure analysis methodology. The company employs the Toyota Production System (TPS), which integrates continuous improvement principles and meticulous quality control. By using techniques like the 5 Whys and Fishbone Diagram (Ishikawa or Cause-and-Effect Diagram), Toyota has consistently identified root causes of failures and implemented effective corrective actions, cementing its reputation for reliability.
Case Study 2: Sony’s Innovation in Electronics Manufacturing
Sony, known for its high-quality electronics, integrates robust failure analysis into its research and development processes. The company focuses on early-stage failure analysis to anticipate potential issues during product design and development. This proactive approach has allowed Sony to innovate continuously while maintaining high standards of product quality and reliability.
Future Trends in Failure Analysis
As technology continues to evolve, so do the methods and tools for failure analysis. Here are some trends that are likely to shape the future of this vital practice:
Artificial Intelligence and Machine Learning
AI and machine learning are revolutionizing failure analysis by enabling more accurate and faster identification of failure patterns. Predictive analytics can foresee potential failures before they occur, allowing for preemptive action. This technology can process vast amounts of data far more efficiently than human analysts.
Integration of IoT
The Internet of Things (IoT) is enhancing the failure analysis process by providing real-time data from connected devices and machinery. This constant stream of data helps in monitoring performance, detecting anomalies, and conducting real-time failure analysis, thereby reducing downtime.
Advanced Material Analysis Techniques
Innovations in material analysis techniques, such as nanotechnology and advanced microscopy, are providing unprecedented insights into material failures at the microscopic level. These techniques enable the detection of minute defects that could lead to significant failures, allowing for more effective corrective measures.
Conclusion
Mastering failure analysis is a critical aspect of achieving manufacturing excellence. The Japanese approach, characterized by meticulous detail, continuous improvement, and cross-functional collaboration, offers valuable lessons for manufacturers worldwide.
While the initial implementation of these techniques may be challenging, the long-term benefits in terms of enhanced product quality, reduced costs, and increased customer satisfaction are well worth the effort. By adopting and adapting these practices, companies can significantly improve their failure analysis processes and overall manufacturing performance.
資料ダウンロード
QCD調達購買管理クラウド「newji」は、調達購買部門で必要なQCD管理全てを備えた、現場特化型兼クラウド型の今世紀最高の購買管理システムとなります。
ユーザー登録
調達購買業務の効率化だけでなく、システムを導入することで、コスト削減や製品・資材のステータス可視化のほか、属人化していた購買情報の共有化による内部不正防止や統制にも役立ちます。
NEWJI DX
製造業に特化したデジタルトランスフォーメーション(DX)の実現を目指す請負開発型のコンサルティングサービスです。AI、iPaaS、および先端の技術を駆使して、製造プロセスの効率化、業務効率化、チームワーク強化、コスト削減、品質向上を実現します。このサービスは、製造業の課題を深く理解し、それに対する最適なデジタルソリューションを提供することで、企業が持続的な成長とイノベーションを達成できるようサポートします。
オンライン講座
製造業、主に購買・調達部門にお勤めの方々に向けた情報を配信しております。
新任の方やベテランの方、管理職を対象とした幅広いコンテンツをご用意しております。
お問い合わせ
コストダウンが利益に直結する術だと理解していても、なかなか前に進めることができない状況。そんな時は、newjiのコストダウン自動化機能で大きく利益貢献しよう!
(Β版非公開)