- お役立ち記事
- Mastering Good Manufacturing Practice (GMP): Insights from Japanese Manufacturing Excellence
Mastering Good Manufacturing Practice (GMP): Insights from Japanese Manufacturing Excellence
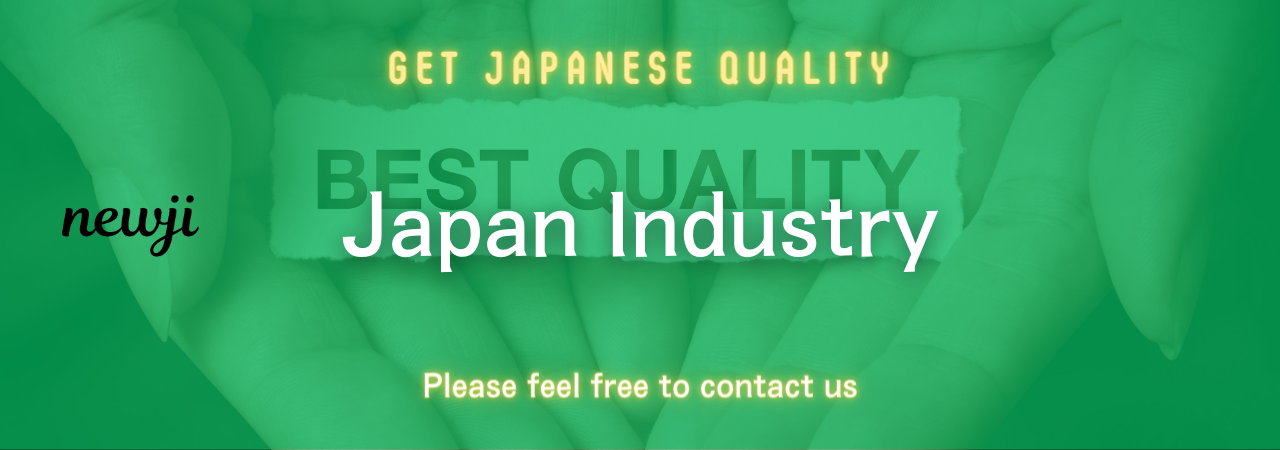
Good Manufacturing Practice (GMP) is a critical aspect of ensuring the quality and safety of products in the manufacturing sector.
Drawing from decades of experience, particularly with Japanese suppliers, offers unique insights into mastering these practices.
Having worked in procurement and purchasing, understanding Japanese manufacturing excellence provides a wealth of practical knowledge and techniques that can be immensely valuable.
Here, we will delve into various aspects of GMP, highlighting the advantages and disadvantages, supplier negotiation techniques, market conditions, and best practices.
目次
Understanding Good Manufacturing Practice (GMP)
Good Manufacturing Practice (GMP) encompasses a set of guidelines and regulations that manufacturers must follow to ensure their products are consistently produced and controlled according to quality standards.
These practices aim to minimize the risks involved in production that cannot be eliminated through testing the final product alone.
Key Elements of GMP
To master GMP, it is essential to understand its key elements, which include:
– Quality management: Establishing systems for managing quality throughout the supply chain.
– Personnel: Employing trained and competent staff to maintain GMP standards.
– Premises and equipment: Ensuring that manufacturing environments and tools are suitable and well-maintained.
– Documentation: Keeping accurate records to demonstrate compliance and traceability.
– Production: Maintaining strict controls over manufacturing processes.
– Quality control: Implementing rigorous testing to ensure product quality and safety.
– Audits: Regularly inspecting and auditing processes and facilities to ensure ongoing compliance.
Japanese Manufacturing Excellence
Japan has long been recognized for its exceptional manufacturing standards.
Several principles and practices contribute to this reputation, many of which align closely with GMP guidelines.
Understanding these principles can provide valuable lessons for companies looking to enhance their GMP compliance.
Kaizen: Continuous Improvement
Kaizen, or continuous improvement, is a cornerstone of Japanese manufacturing excellence.
This principle emphasizes small, incremental changes to processes and practices to improve efficiency, quality, and safety over time.
Incorporating kaizen into GMP can help ensure that standards are continuously enhanced, leading to better compliance and product quality.
Lean Manufacturing
Lean manufacturing focuses on minimizing waste while maximizing value.
This approach involves identifying and eliminating non-value-added activities, streamlining processes, and improving overall efficiency.
Implementing lean principles within a GMP framework can help reduce risks, improve product quality, and lower costs.
Jidoka: Automation with a Human Touch
Jidoka, or automation with a human touch, involves integrating automated systems with human oversight to ensure quality and safety.
This principle ensures that machines and processes are designed to detect and address issues automatically, while human workers provide oversight and intervention as needed.
Incorporating Jidoka into GMP practices can enhance quality control and reduce the risk of defects.
Respect for People
Japanese manufacturing excellence places a strong emphasis on respect for people, including employees, suppliers, and customers.
This principle involves creating a positive work environment, fostering collaboration, and ensuring that all stakeholders are treated with respect and dignity.
Incorporating this principle into GMP can help create a culture of quality and safety throughout the organization.
Advantages of Japanese Suppliers in GMP
Working with Japanese suppliers can provide several advantages when it comes to mastering GMP.
These benefits include:
High-Quality Standards
Japanese suppliers are known for their commitment to high-quality standards.
By partnering with such suppliers, companies can benefit from their rigorous quality control processes, ensuring that products meet or exceed GMP requirements.
Strong Focus on Continuous Improvement
Japanese suppliers often prioritize continuous improvement, making them well-suited to support GMP compliance.
Their dedication to kaizen ensures that processes are continually refined and enhanced, leading to better quality and safety outcomes.
Expertise in Lean Manufacturing
Japanese manufacturers are experts in lean manufacturing, which can help companies streamline their processes and reduce waste.
By working with these suppliers, companies can benefit from their expertise and incorporate lean principles into their GMP practices.
Collaborative Approach
Japanese suppliers often adopt a collaborative approach, working closely with their partners to achieve common goals.
This collaborative mindset can help foster strong relationships and ensure that GMP standards are consistently met.
Disadvantages of Japanese Suppliers in GMP
While there are many advantages to working with Japanese suppliers, there are also some potential disadvantages to consider.
Higher Costs
Japanese suppliers are known for their high-quality standards, which can come at a higher cost.
While the investment in quality may be worthwhile, companies need to carefully consider their budget and cost constraints.
Cultural Differences
Working with Japanese suppliers can sometimes be challenging due to cultural differences.
Understanding and navigating these differences is essential to ensure effective communication and collaboration.
Geographical Distance
Depending on the location of the company, working with Japanese suppliers may involve significant geographical distance.
This can lead to longer lead times and higher shipping costs, which need to be taken into account when planning procurement and production processes.
Supplier Negotiation Techniques
Effective negotiation with suppliers is critical to mastering GMP and ensuring successful procurement and purchasing outcomes.
Here are some techniques to consider when negotiating with Japanese suppliers.
Building Relationships
Building strong, long-term relationships with suppliers is crucial in Japanese business culture.
Invest time in getting to know your suppliers, understanding their needs and expectations, and demonstrating your commitment to mutual success.
Understanding Cultural Nuances
Take the time to understand cultural nuances and differences, such as communication styles and business etiquette.
This can help build rapport and foster a positive working relationship.
Preparing Thoroughly
Prepare thoroughly for negotiations by gathering detailed information about the supplier, their products, and their processes.
This will enable you to ask informed questions and make well-founded decisions.
Focusing on Win-Win Outcomes
Focus on achieving win-win outcomes that benefit both parties.
This collaborative approach can help build trust and ensure long-term success.
Negotiating Terms Fairly
Negotiate terms fairly and transparently, ensuring that both parties’ interests are considered.
This can help build a foundation of trust and mutual respect.
Market Conditions Impacting GMP
Understanding current market conditions is essential for mastering GMP and making informed procurement and purchasing decisions.
Several factors can impact GMP, including:
Regulatory Changes
Stay informed about regulatory changes that may impact GMP requirements.
This can help ensure that your practices remain compliant and up-to-date.
Technological Advancements
Technological advancements can have a significant impact on GMP.
Stay abreast of the latest developments in manufacturing technology and consider how they can be integrated into your processes to enhance quality and efficiency.
Global Supply Chain Dynamics
Global supply chain dynamics, such as fluctuations in raw material availability and transportation costs, can impact GMP.
Staying informed about these trends can help you make strategic decisions and mitigate risks.
Economic Conditions
Economic conditions, such as inflation and exchange rates, can also impact GMP.
Monitor these factors and adjust your procurement and purchasing strategies accordingly.
Best Practices for Mastering GMP
To master GMP, consider implementing the following best practices:
Develop a Robust Quality Management System (QMS)
A robust QMS is essential for ensuring GMP compliance.
Develop and implement a system that includes clear policies, procedures, and processes for managing quality throughout the supply chain.
Invest in Training and Development
Invest in training and development for all employees to ensure they understand GMP requirements and are equipped to maintain high standards.
Continuous education and skill development are key to maintaining compliance.
Implement Regular Audits and Inspections
Conduct regular audits and inspections of your processes, facilities, and suppliers to ensure ongoing GMP compliance.
Identify areas for improvement and take corrective actions as needed.
Foster a Culture of Quality
Create a culture of quality within your organization by emphasizing the importance of GMP and encouraging all employees to take ownership of quality and safety.
Leverage Technology
Leverage technology to enhance GMP compliance.
Invest in advanced manufacturing systems, data analytics, and automation to improve quality control and reduce risks.
Collaborate with Suppliers
Collaborate closely with suppliers to ensure they understand and adhere to GMP requirements.
Build strong relationships and work together to achieve common quality and safety goals.
Conclusion
Mastering Good Manufacturing Practice (GMP) is essential for ensuring product quality and safety in the manufacturing sector.
Drawing from the principles and practices of Japanese manufacturing excellence can provide valuable insights and techniques to enhance GMP compliance.
By understanding the key elements of GMP, leveraging the advantages of Japanese suppliers, and implementing best practices, companies can achieve higher standards of quality and safety, ultimately driving long-term success in the market.
資料ダウンロード
QCD調達購買管理クラウド「newji」は、調達購買部門で必要なQCD管理全てを備えた、現場特化型兼クラウド型の今世紀最高の購買管理システムとなります。
ユーザー登録
調達購買業務の効率化だけでなく、システムを導入することで、コスト削減や製品・資材のステータス可視化のほか、属人化していた購買情報の共有化による内部不正防止や統制にも役立ちます。
NEWJI DX
製造業に特化したデジタルトランスフォーメーション(DX)の実現を目指す請負開発型のコンサルティングサービスです。AI、iPaaS、および先端の技術を駆使して、製造プロセスの効率化、業務効率化、チームワーク強化、コスト削減、品質向上を実現します。このサービスは、製造業の課題を深く理解し、それに対する最適なデジタルソリューションを提供することで、企業が持続的な成長とイノベーションを達成できるようサポートします。
オンライン講座
製造業、主に購買・調達部門にお勤めの方々に向けた情報を配信しております。
新任の方やベテランの方、管理職を対象とした幅広いコンテンツをご用意しております。
お問い合わせ
コストダウンが利益に直結する術だと理解していても、なかなか前に進めることができない状況。そんな時は、newjiのコストダウン自動化機能で大きく利益貢献しよう!
(Β版非公開)