- お役立ち記事
- Mastering Hard and Brittle Material Machining: A Deep Dive into Japanese Manufacturing Innovation
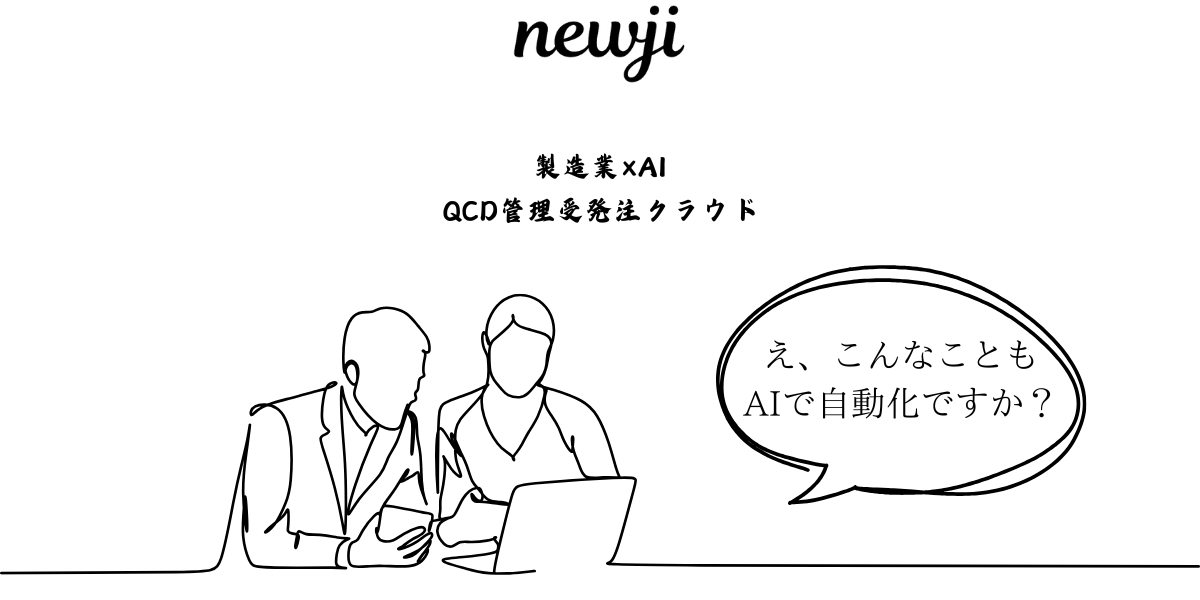
Mastering Hard and Brittle Material Machining: A Deep Dive into Japanese Manufacturing Innovation
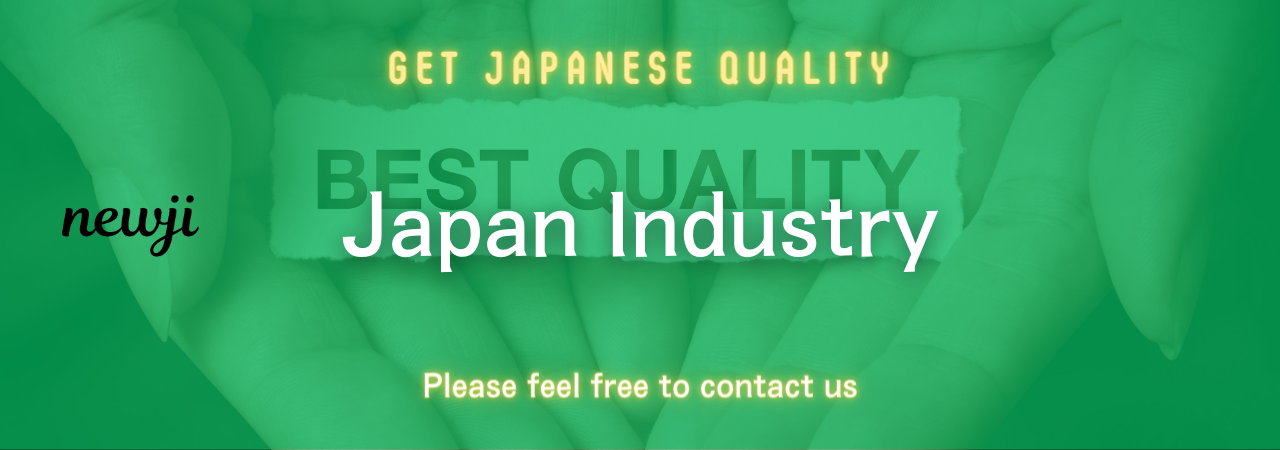
目次
Introduction to Hard and Brittle Material Machining
Hard and brittle materials, such as ceramics, glass, and certain metals, present unique challenges in the manufacturing sector. These materials are essential in various high-performance applications, including electronics, aerospace, and medical devices. Mastering the machining of these materials is crucial for maintaining the integrity and performance of the final product.
Japanese Manufacturing Innovation in Machining
Japan has long been recognized for its advancements in manufacturing technologies. The country’s focus on precision, efficiency, and quality has positioned it as a leader in the global manufacturing landscape, particularly in the machining of hard and brittle materials.
Advanced Tooling Techniques
Japanese manufacturers have developed specialized tooling techniques that enhance the precision and efficiency of machining hard and brittle materials. These techniques include the use of diamond-coated tools and advanced coolant systems that reduce heat generation and prevent material cracking.
Automation and Precision Engineering
Automation plays a significant role in Japanese manufacturing innovation. Automated machining centers ensure consistent quality and reduce human error. Precision engineering allows for the meticulous control of machining parameters, which is essential when working with materials that are prone to cracking and other forms of damage.
Procurement and Purchasing Strategies in Japanese Manufacturing
Effective procurement and purchasing strategies are vital for sourcing high-quality materials and components required for machining hard and brittle materials. Japanese manufacturers excel in establishing robust supply chains and maintaining long-term relationships with suppliers.
Advantages of Japanese Procurement Practices
Japanese procurement practices are characterized by their emphasis on quality, reliability, and sustainability. Manufacturers prioritize suppliers who adhere to strict quality standards and demonstrate a commitment to continuous improvement. This approach ensures the consistent availability of high-grade materials necessary for precision machining.
Disadvantages and Challenges
While Japanese procurement practices offer numerous advantages, they also present certain challenges. The stringent quality requirements can lead to higher costs and longer lead times. Additionally, establishing and maintaining relationships with Japanese suppliers may require significant cultural and operational adjustments for international companies.
Supplier Negotiation Techniques
Successful negotiations with Japanese suppliers require a deep understanding of their business culture and practices. Building trust and demonstrating a commitment to long-term partnerships are essential elements of effective negotiation strategies.
Understanding Japanese Business Culture
Japanese business culture places a strong emphasis on respect, harmony, and consensus. Negotiations are typically collaborative rather than confrontational. Understanding and respecting these cultural nuances can facilitate more productive negotiations and foster stronger supplier relationships.
Building Long-Term Relationships
Japanese suppliers value long-term partnerships over short-term gains. Demonstrating reliability, consistency, and a genuine interest in mutual growth can enhance negotiation outcomes. Investing time in relationship-building activities, such as regular visits and open communication, is crucial for establishing trust and cooperation.
Market Conditions and Trends
The global market for hard and brittle material machining is influenced by various factors, including technological advancements, demand fluctuations, and economic conditions. Monitoring these trends is essential for making informed procurement and purchasing decisions.
Technological Advancements
Continuous advancements in machining technologies, such as computer numerical control (CNC) systems and additive manufacturing, are reshaping the landscape of hard and brittle material machining. Japanese manufacturers are at the forefront of these innovations, integrating cutting-edge technologies to enhance precision and efficiency.
Economic and Supply Chain Considerations
Economic fluctuations and supply chain disruptions can impact the availability and cost of materials. Japanese manufacturers mitigate these risks through diversified sourcing strategies and maintaining strategic inventories. Understanding these approaches can help international companies better navigate market uncertainties.
Best Practices in Procurement and Purchasing
Implementing best practices in procurement and purchasing can significantly enhance the efficiency and effectiveness of sourcing hard and brittle materials from Japanese suppliers.
Quality Management Systems
Adopting robust quality management systems, such as ISO 9001, ensures that both the purchaser and supplier maintain high standards in material quality and machining processes. Regular audits and continuous improvement initiatives help sustain these standards over time.
Collaborative Planning and Forecasting
Collaborative planning and forecasting with suppliers enable better alignment of production schedules and inventory management. Sharing demand forecasts and production plans fosters transparency and reduces the risk of stockouts or excess inventory.
Leveraging Technology for Supply Chain Integration
Utilizing advanced supply chain management software facilitates real-time communication and data sharing between purchasers and suppliers. This integration enhances visibility, improves coordination, and enables more responsive decision-making.
Advantages of Japanese Machining Expertise
Japanese machining expertise offers several advantages that contribute to high-quality outcomes in hard and brittle material manufacturing.
Precision and Accuracy
Japanese manufacturers are renowned for their precision and accuracy in machining processes. Rigorous quality control measures and advanced machinery ensure that components meet exact specifications, minimizing waste and rework.
Innovation and Continuous Improvement
A culture of continuous improvement, or Kaizen, drives innovation in Japanese manufacturing. This approach encourages ongoing refinement of processes and technologies, leading to enhanced efficiency and product quality.
Reliability and Consistency
Japanese suppliers are known for their reliability and consistency in delivering high-quality materials and components. This dependability is crucial for maintaining production schedules and ensuring the seamless operation of manufacturing processes.
Disadvantages and Mitigation Strategies
Despite the numerous benefits, there are certain disadvantages associated with sourcing and machining hard and brittle materials from Japanese suppliers.
Higher Costs
The high quality and precision offered by Japanese manufacturers often come at a premium cost. To mitigate this, companies can negotiate long-term contracts to secure better pricing or explore bulk purchasing options to achieve economies of scale.
Cultural and Communication Barriers
Differences in language and business practices can pose challenges in communication and collaboration. Investing in cross-cultural training and employing bilingual staff can bridge these gaps and enhance mutual understanding.
Long Lead Times
Japanese suppliers may have longer lead times due to their emphasis on meticulous manufacturing processes. Planning ahead and maintaining buffer inventories can help manage production schedules and minimize the impact of delays.
Case Studies of Successful Japanese Procurement
Examining real-world examples of successful procurement from Japanese suppliers provides valuable insights into effective strategies and best practices.
Case Study 1: Automotive Industry
A leading automotive manufacturer partnered with a Japanese supplier to source high-precision ceramic components for engine parts. Through collaborative planning and joint quality initiatives, the companies achieved significant improvements in component durability and performance.
Case Study 2: Electronics Sector
An electronics company sourced glass substrates from a Japanese supplier for use in display manufacturing. By implementing integrated supply chain management systems, both parties enhanced inventory accuracy and reduced lead times, leading to increased production efficiency.
Future Outlook and Opportunities
The future of hard and brittle material machining holds promising opportunities, driven by ongoing technological advancements and evolving market demands. Japanese manufacturers are well-positioned to capitalize on these trends through innovation and strategic partnerships.
Emerging Technologies
Advancements in materials science, such as the development of new ceramics and composite materials, are expanding the applications of hard and brittle materials. Japanese manufacturers are investing in research and development to stay at the forefront of these innovations.
Sustainability and Green Manufacturing
Sustainability is becoming increasingly important in manufacturing. Japanese suppliers are adopting eco-friendly practices, such as reducing waste and optimizing energy use, which align with the growing demand for sustainable products.
Global Expansion and Collaboration
As global markets continue to expand, opportunities for collaboration between Japanese suppliers and international purchasers will increase. Building strategic alliances can facilitate the exchange of knowledge and technology, fostering mutual growth and success.
Conclusion
Mastering the machining of hard and brittle materials is a complex but essential aspect of modern manufacturing. Japanese manufacturing innovation, characterized by precision, efficiency, and a commitment to quality, offers valuable lessons and opportunities for international companies. By adopting effective procurement and purchasing strategies, leveraging advanced technologies, and fostering strong supplier relationships, manufacturers can achieve superior outcomes and maintain a competitive edge in the global market.
資料ダウンロード
QCD調達購買管理クラウド「newji」は、調達購買部門で必要なQCD管理全てを備えた、現場特化型兼クラウド型の今世紀最高の購買管理システムとなります。
ユーザー登録
調達購買業務の効率化だけでなく、システムを導入することで、コスト削減や製品・資材のステータス可視化のほか、属人化していた購買情報の共有化による内部不正防止や統制にも役立ちます。
NEWJI DX
製造業に特化したデジタルトランスフォーメーション(DX)の実現を目指す請負開発型のコンサルティングサービスです。AI、iPaaS、および先端の技術を駆使して、製造プロセスの効率化、業務効率化、チームワーク強化、コスト削減、品質向上を実現します。このサービスは、製造業の課題を深く理解し、それに対する最適なデジタルソリューションを提供することで、企業が持続的な成長とイノベーションを達成できるようサポートします。
オンライン講座
製造業、主に購買・調達部門にお勤めの方々に向けた情報を配信しております。
新任の方やベテランの方、管理職を対象とした幅広いコンテンツをご用意しております。
お問い合わせ
コストダウンが利益に直結する術だと理解していても、なかなか前に進めることができない状況。そんな時は、newjiのコストダウン自動化機能で大きく利益貢献しよう!
(Β版非公開)