- お役立ち記事
- Mastering Inventory Optimization in Japanese Manufacturing: Boost Efficiency and Cut Costs
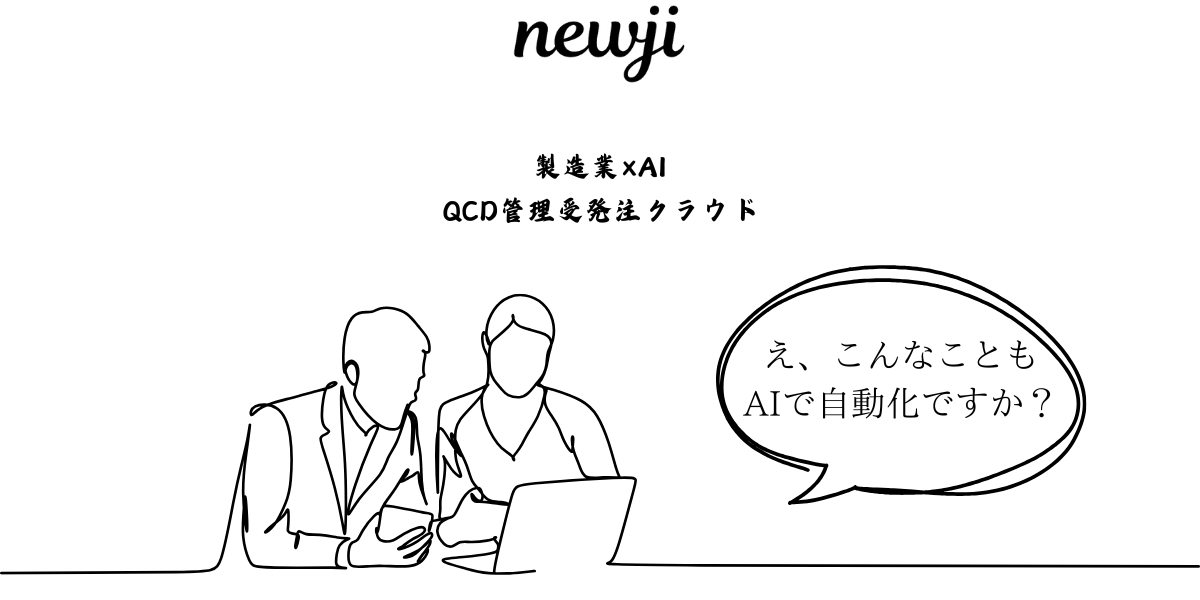
Mastering Inventory Optimization in Japanese Manufacturing: Boost Efficiency and Cut Costs
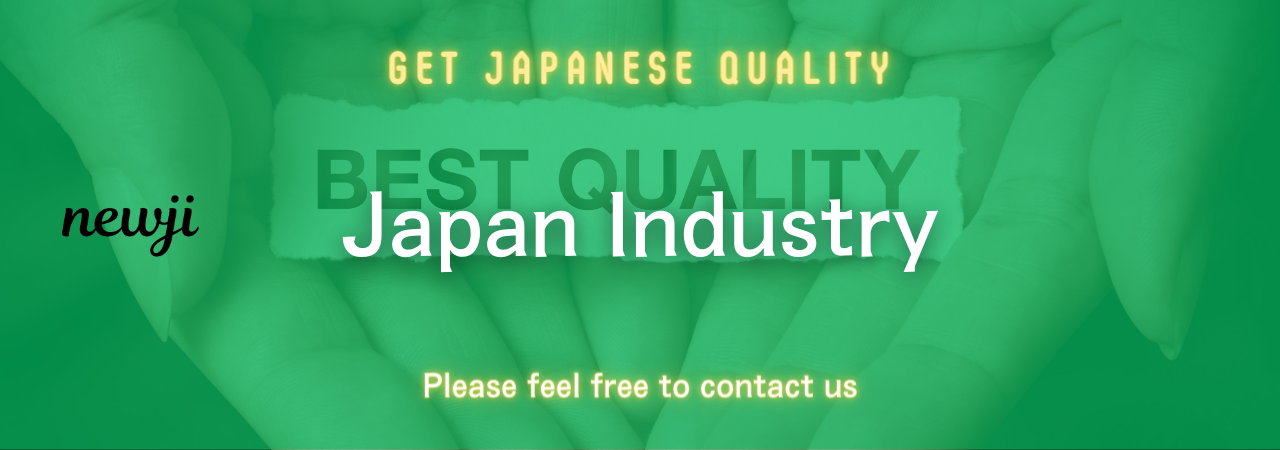
目次
Introduction
Inventory optimization is a critical aspect of manufacturing that can significantly impact a company’s bottom line. This is particularly true in the highly competitive and quality-driven arena of Japanese manufacturing. Leveraging the technical skills and expertise of Japanese suppliers, optimizing inventory can help businesses enhance efficiency, reduce costs, and maintain a distinct competitive edge.
The Importance of Inventory Optimization
Inventory management is essential to ensure that a manufacturing plant runs smoothly. It involves having the right amount of raw materials and finished products to meet customer demand without overstocking or facing stock-outs. Proper inventory optimization minimizes costs while maximizing profits.
In the context of Japanese manufacturing, inventory optimization holds even greater significance due to its focus on maintaining high-quality standards, reducing waste, and promoting efficiency. Japanese methodologies such as ‘Just-in-Time’ (JIT) and ‘Kanban’ are globally recognized for their effectiveness in driving inventory optimization.
Advantages of Inventory Optimization
Cost Reduction
Reducing inventory levels decreases storage costs, minimizes pilferage, and lowers insurance costs. It also frees up capital that can be used in other areas of the business.
Efficient Space Utilization
Optimized inventory allows for better utilization of warehouse space, transforming it into a more organized and efficient working environment.
Improved Cash Flow
With less money tied up in inventory, businesses can enjoy improved cash flow, allowing for greater financial flexibility and stability.
Enhanced Customer Satisfaction
Having the right products in stock to meet demand ensures timely deliveries, which can significantly enhance customer satisfaction and loyalty.
Higher Quality Control
By maintaining optimal inventory levels, businesses can more effectively manage shelf life and reduce the risk of obsolescence, ensuring that all products meet high quality standards.
Risk Management
Optimal inventory levels reduce the risk of products becoming obsolete and thus protect the company from sudden market changes or fluctuations in demand.
Challenges and Disadvantages in Inventory Optimization
Accurate Demand Forecasting
One of the biggest challenges in inventory optimization is accurately predicting customer demand. Inaccurate forecasts can lead to overstocking or stockouts, both of which can have financial repercussions.
Initial Investment
Implementing sophisticated inventory management systems might require substantial initial investments in technology and training. This can be a barrier, especially for smaller manufacturers.
Ensuring Supply Chain Coordination
Effective inventory optimization requires seamless coordination with suppliers and other stakeholders in the supply chain. Misalignment can lead to disruptions, impacting production schedules.
Complexity in Implementation
Adopting and integrating advanced inventory management techniques may require substantial changes in business processes and workflows, which can be complex and time-consuming.
Japanese Inventory Management Practices
Japanese manufacturing practices are renowned for their rigor and efficiency. The key methodologies that drive inventory optimization in Japan include Just-in-Time (JIT) and Kanban.
Just-in-Time (JIT)
JIT manufacturing aims to reduce waste by receiving goods only when they are needed in the production process. This minimizes inventory costs, avoids overproduction, and enhances operational efficiency.
Kanban System
The Kanban system is a scheduling system that works in tandem with JIT. It involves signaling the need to restock materials only when they are used up. This ensures that inventory levels are kept at optimal levels, preventing both excess inventory and stockouts.
Lean Manufacturing
Lean manufacturing focuses on reducing waste and improving productivity. By identifying and eliminating non-value-added activities, lean practices enhance efficiency and ensure optimal inventory levels.
5S Methodology
The 5S methodology (Sort, Set in order, Shine, Standardize, and Sustain) is a system for organizing and maintaining a clean and efficient workspace. It supports inventory optimization by ensuring all materials are properly organized and easily accessible.
Supplier Negotiation Techniques for Inventory Optimization
Building Strong Relationships
Establishing strong relationships with suppliers is crucial in inventory optimization. Trust and open communication can ensure that suppliers are willing to provide flexibility in terms of lead times, order quantities, and pricing.
Consignment Inventory
Negotiating consignment inventory agreements with suppliers can reduce the burden of holding inventory. Suppliers retain ownership of inventory until it is used, thereby reducing storage and capital costs for the manufacturer.
Bulk Purchasing and Discounts
When demand forecasts are reliable, negotiating bulk purchase agreements can lead to significant cost savings. However, it is crucial to balance bulk purchasing with the risk of holding excess inventory.
Supplier Managed Inventory (SMI)
In an SMI arrangement, suppliers take responsibility for maintaining the necessary inventory levels at the manufacturer’s site. This can lead to more efficient inventory management and reduce the risk of stockouts.
Creating Flexibility Agreements
Negotiating flexible contracts that allow for changes in order quantities and delivery schedules can help manufacturers better manage inventory levels in response to fluctuating demand.
Market Conditions Impacting Inventory Optimization
Economic Factors
Economic conditions such as inflation, exchange rates, and customer spending habits affect demand and inventory levels. Understanding these factors helps businesses forecast more accurately and optimize inventory accordingly.
Technological Advancements
The advent of advanced technologies like AI, machine learning, and IoT has revolutionized inventory optimization. These technologies enable real-time inventory tracking, predictive analytics, and automation, leading to more efficient inventory management.
Global Supply Chain Dynamics
Globalization has expanded supply chains but also introduced complexities such as longer lead times and geopolitical risks. Staying informed about global supply chain trends is crucial for effective inventory management.
Regulatory Changes
Regulatory changes can impact inventory management practices. Staying compliant while adapting to new regulations ensures smooth operations and prevents disruptions.
Best Practices for Mastering Inventory Optimization in Japanese Manufacturing
Implement Advanced Inventory Management Systems
Investing in advanced inventory management systems like ERP and automated inventory tracking can provide real-time visibility into inventory levels and streamline operations.
Regular Monitoring and Analysis
Regularly monitoring inventory levels and analyzing data can help identify trends and areas for improvement. This enables more accurate forecasting and better decision-making.
Adopt Lean and Agile Practices
Adopting lean and agile manufacturing practices can enhance efficiency and responsiveness. This includes reducing lead times, minimizing waste, and improving flexibility to adapt to changes in demand.
Collaborate with All Stakeholders
Collaboration with suppliers, customers, and other stakeholders is crucial for effective inventory optimization. Sharing information and working together can lead to more efficient inventory management.
Embrace Continuous Improvement
Continuous improvement is a cornerstone of Japanese manufacturing practices. Regularly reviewing and refining inventory management processes can lead to long-term benefits and sustained competitiveness.
Train and Empower Employees
Investing in training and empowering employees ensures they are equipped with the knowledge and skills to manage inventory effectively. Engaged and informed employees are more likely to identify and act on opportunities for improvement.
Conclusion
Mastering inventory optimization in Japanese manufacturing is a multifaceted endeavor that requires a strategic approach and commitment to excellence.
By leveraging tried-and-true Japanese manufacturing practices like JIT, Kanban, and lean methodologies, businesses can significantly enhance efficiency, reduce costs, and maintain high quality standards.
Navigating challenges such as accurate demand forecasting, ensuring supply chain coordination, and embracing technological advancements is essential for achieving optimal inventory levels.
By implementing best practices, fostering strong supplier relationships, and embracing continuous improvement, manufacturers can master inventory optimization and enjoy the myriad benefits it brings.
資料ダウンロード
QCD調達購買管理クラウド「newji」は、調達購買部門で必要なQCD管理全てを備えた、現場特化型兼クラウド型の今世紀最高の購買管理システムとなります。
ユーザー登録
調達購買業務の効率化だけでなく、システムを導入することで、コスト削減や製品・資材のステータス可視化のほか、属人化していた購買情報の共有化による内部不正防止や統制にも役立ちます。
NEWJI DX
製造業に特化したデジタルトランスフォーメーション(DX)の実現を目指す請負開発型のコンサルティングサービスです。AI、iPaaS、および先端の技術を駆使して、製造プロセスの効率化、業務効率化、チームワーク強化、コスト削減、品質向上を実現します。このサービスは、製造業の課題を深く理解し、それに対する最適なデジタルソリューションを提供することで、企業が持続的な成長とイノベーションを達成できるようサポートします。
オンライン講座
製造業、主に購買・調達部門にお勤めの方々に向けた情報を配信しております。
新任の方やベテランの方、管理職を対象とした幅広いコンテンツをご用意しております。
お問い合わせ
コストダウンが利益に直結する術だと理解していても、なかなか前に進めることができない状況。そんな時は、newjiのコストダウン自動化機能で大きく利益貢献しよう!
(Β版非公開)