- お役立ち記事
- Mastering Japanese Craftsmanship: The Art and Precision of Lost wax in Modern Manufacturing
Mastering Japanese Craftsmanship: The Art and Precision of Lost wax in Modern Manufacturing
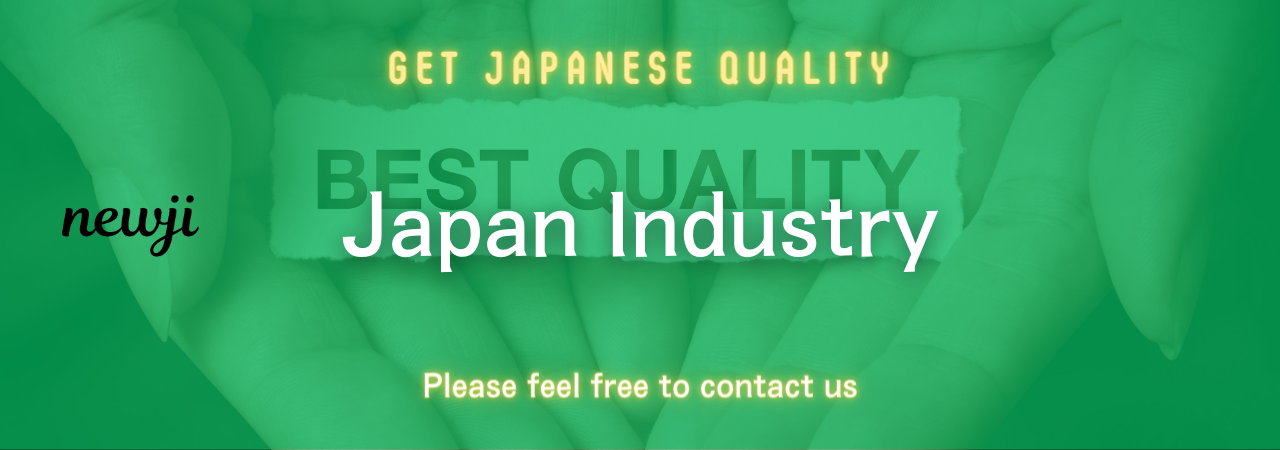
目次
Introduction to the Art and Precision of Lost wax Manufacturing
The intricate art of Lost wax, also known as lost-wax casting or investment casting, is an ancient technique that has been honed to perfection in Japan. This manufacturing process allows for the creation of highly detailed and complex components, catering to various industries ranging from aerospace to jewelry. In modern times, ロストワックス remains a critical process due to its precision and capability to produce parts with intricate geometries.
Understanding the Basics: What is Lost wax?
ロストワックス, or lost-wax casting, involves creating a wax model of the component to be manufactured. This wax model is encased in a ceramic shell or mold. Once the mold is hardened, the wax is melted and drained away, leaving a cavity that is then filled with molten metal to create the final product. This method is highly valued for its ability to produce parts with exceptional detail and accuracy.
The Historical Context
Lost-wax casting has a rich history that dates back thousands of years. Ancient civilizations, including the Egyptians and the Mesopotamians, used this technique to create intricate jewelry and statues. Over time, the process evolved, and different cultures, including Japanese craftsmen, have added their unique touches to improve and perfect this technique.
Advantages of Lost wax in Modern Manufacturing
Unmatched Precision and Detail
One of the main advantages of Lost wax is its capacity for precision. The technique can recreate highly detailed and intricate components that would be difficult to achieve through other manufacturing methods. This precision is particularly beneficial for industries that require exact specifications, such as aerospace and medical device manufacturing.
Material Versatility
Lost wax supports a wide range of materials, including steel, aluminum, titanium, and various alloys. This versatility makes it suitable for different applications, ensuring that the final product meets the specific requirements of its intended use.
High-Quality Surface Finish
The parts produced through lost-wax casting often have a superior surface finish compared to those manufactured through other methods. This minimizes the need for extensive post-production processing, thereby reducing production time and costs.
Economic Efficiency
While the initial setup for lost-wax casting, including mold creation, can be relatively costly, the technique becomes economically advantageous for large production runs. The ability to produce complex shapes without additional machining provides long-term cost benefits.
Reduction in Material Waste
The precision of the Lost wax process ensures that there is minimal material waste. Unlike other techniques that require extensive machining and material removal, lost-wax casting produces components that closely match the final dimensions, leading to efficient use of raw materials.
Disadvantages of Lost wax
High Initial Setup Costs
One of the primary challenges of lost-wax casting is the high initial costs associated with mold creation and the labor-intensive process of crafting the wax model. These costs can be a barrier for small production runs or companies with limited budgets.
Time-Consuming Process
The lost-wax casting process can be time-consuming, especially the stages involving mold creation and wax model production. This can lead to longer lead times compared to other manufacturing methods, which may not be suitable for urgent production requirements.
Size Limitations
Lost wax is generally more suited to smaller components. Large-scale parts can be challenging to produce due to complexities in mold handling and the risk of defects during the casting process.
Supplier Negotiation Techniques for Lost wax
Understanding Supplier Capabilities
Before entering negotiations with a supplier, it is vital to understand their capabilities in lost-wax casting. Reviewing their past work, technological capabilities, certifications, and quality control processes can provide invaluable insights into whether they meet your specific needs.
Establishing Quality Standards
Quality is non-negotiable when it comes to ロストワックス. Clearly outline your quality parameters and ensure the supplier can meet these standards. This includes material specifications, dimensional tolerances, and surface finish requirements.
Cost Negotiation
While it’s important to negotiate costs effectively, it’s equally vital to avoid compromising on quality. Request detailed quotations that break down the costs involved, from material sourcing to labor and overheads, so you understand where your money is going and identify potential areas for cost saving.
Lead Time and Delivery Terms
Ensure that the supplier can meet your delivery deadlines and discuss the penalties for any potential delays. This is crucial for maintaining production schedules and ensuring your operations are not adversely affected by supply chain issues.
Long-Term Relationships
Establishing a long-term relationship with a reliable supplier can lead to mutual benefits. Engage in ongoing communications, provide feedback, and work together to continuously improve the production process. This partnership can result in cost savings, improved quality, and better service over time.
Current Market Conditions for ロストワックス
Global Demand Trends
The global demand for lost-wax casting remains robust, driven by various industries seeking high-precision components. Sectors such as aerospace, automotive, medical devices, and luxury goods (e.g., jewelry) continue to demand the unique advantages that lost-wax casting offers.
Technological Advancements
Advancements in technology, including computer-aided design (CAD) and 3D printing, have significantly impacted lost-wax casting. These innovations have streamlined the process of creating wax models and molds, reducing production time and costs while increasing accuracy.
Challenges from Competing Methods
While lost-wax casting remains unparalleled in certain applications, it faces competition from other methods such as direct metal laser sintering (DMLS) and precision CNC machining. These alternative techniques offer their own sets of advantages and may be more suitable for specific applications.
Best Practices for Implementing ロストワックス
Collaborative Design
Engage in collaborative design with your suppliers. Sharing precise design specifications and understanding the limitations and capabilities of lost-wax casting can lead to optimized component designs that are easier and more cost-effective to produce.
Prototyping
Utilize prototyping extensively to identify and rectify potential issues before committing to full-scale production. Prototyping allows for testing different materials, designs, and processing techniques to ensure the final product meets your requirements.
Quality Control
Implement rigorous quality control measures throughout the production process. This includes inspections at various stages, from wax model creation to final casting. Non-destructive testing methods such as X-ray inspection and ultrasonic testing can help detect any internal defects.
Supplier Audits and Evaluations
Conduct regular audits and evaluations of your suppliers to ensure they consistently meet quality and delivery standards. These audits can include reviewing their manufacturing processes, quality control measures, and compliance with industry standards.
Continuous Improvement
Foster a culture of continuous improvement within your organization and with your suppliers. Regularly review processes, identify areas for enhancement, and implement improvements to increase efficiency, reduce costs, and enhance product quality.
Conclusion
Mastering the art and precision of ロストワックス offers immense benefits for modern manufacturing, from unmatched precision and detail to material versatility and economic efficiency. However, it also comes with challenges such as high initial setup costs and time-consuming processes.
By understanding the intricacies of supplier negotiations, staying abreast of market conditions, and implementing best practices, manufacturers can effectively leverage the advantages of this age-old technique to produce high-quality, intricate components that meet contemporary demands.
The expertise and commitment of Japanese suppliers in fostering meticulous craftsmanship can be a valuable asset in achieving exceptional results through lost-wax casting. Embrace the art of ロストワックス and unlock new possibilities for innovation and excellence in manufacturing.
資料ダウンロード
QCD調達購買管理クラウド「newji」は、調達購買部門で必要なQCD管理全てを備えた、現場特化型兼クラウド型の今世紀最高の購買管理システムとなります。
ユーザー登録
調達購買業務の効率化だけでなく、システムを導入することで、コスト削減や製品・資材のステータス可視化のほか、属人化していた購買情報の共有化による内部不正防止や統制にも役立ちます。
NEWJI DX
製造業に特化したデジタルトランスフォーメーション(DX)の実現を目指す請負開発型のコンサルティングサービスです。AI、iPaaS、および先端の技術を駆使して、製造プロセスの効率化、業務効率化、チームワーク強化、コスト削減、品質向上を実現します。このサービスは、製造業の課題を深く理解し、それに対する最適なデジタルソリューションを提供することで、企業が持続的な成長とイノベーションを達成できるようサポートします。
オンライン講座
製造業、主に購買・調達部門にお勤めの方々に向けた情報を配信しております。
新任の方やベテランの方、管理職を対象とした幅広いコンテンツをご用意しております。
お問い合わせ
コストダウンが利益に直結する術だと理解していても、なかなか前に進めることができない状況。そんな時は、newjiのコストダウン自動化機能で大きく利益貢献しよう!
(Β版非公開)