- お役立ち記事
- Mastering Japanese Innovation: How “Cell Balancer” Technology Is Revolutionizing Modern Manufacturing
月間77,185名の
製造業ご担当者様が閲覧しています*
*2025年2月28日現在のGoogle Analyticsのデータより
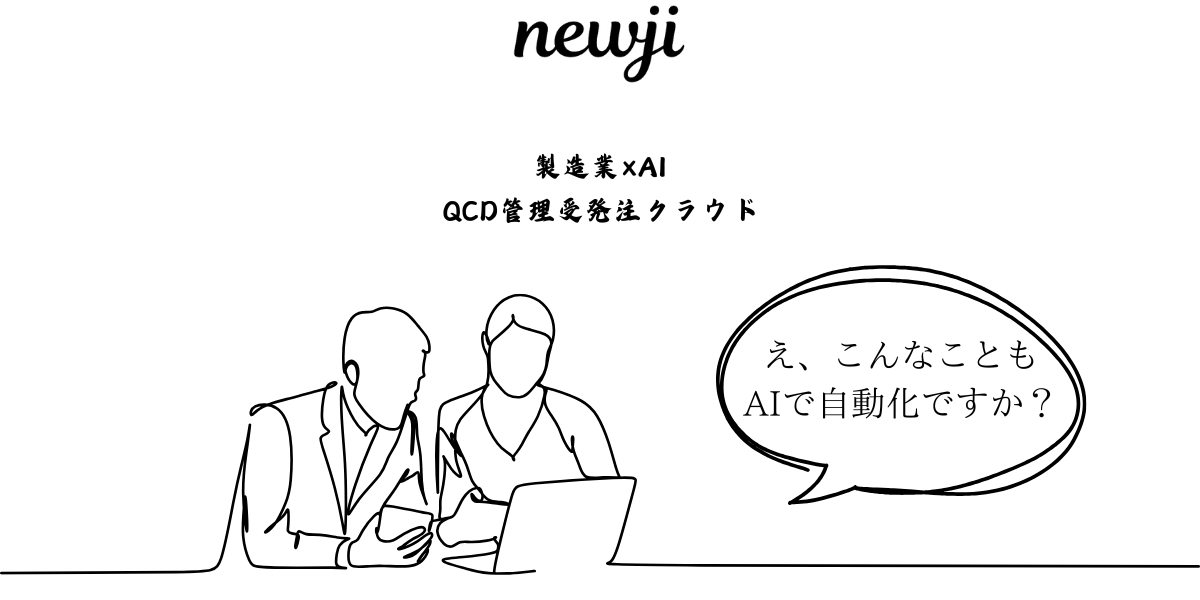
Mastering Japanese Innovation: How “Cell Balancer” Technology Is Revolutionizing Modern Manufacturing
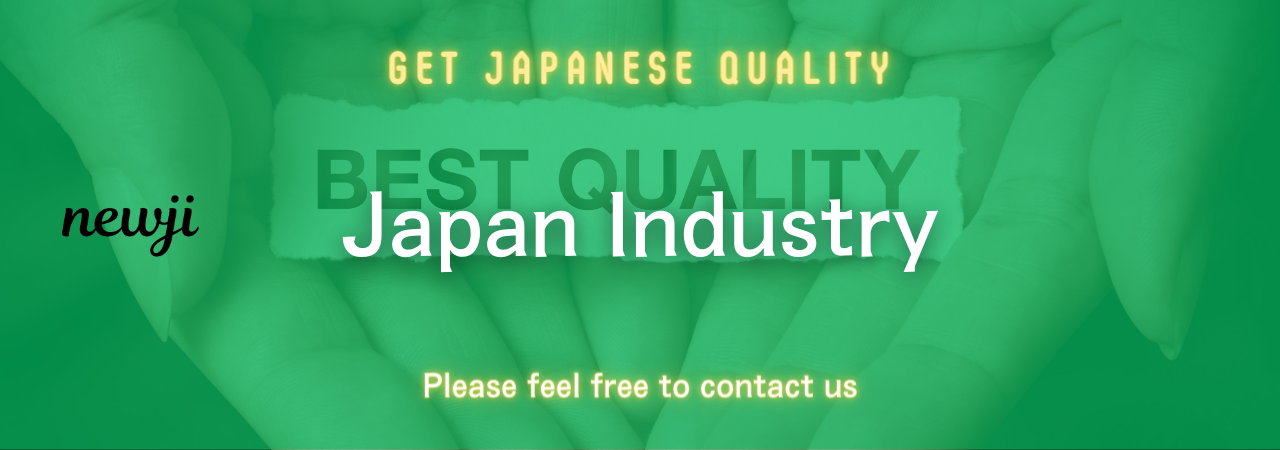
目次
Understanding Cell Balancer Technology
Cell Balancer technology represents a significant advancement in modern manufacturing, particularly within the Japanese industrial sector. At its core, Cell Balancer is designed to optimize the workflow within manufacturing cells, ensuring that each section of the production process operates at peak efficiency. This technology leverages real-time data analytics and automation to adjust and balance workloads, minimizing bottlenecks and enhancing overall productivity.
The concept of a manufacturing cell involves grouping different machines and processes into a single, cohesive unit that can operate semi-independently. Cell Balancer takes this a step further by continuously monitoring the performance of each component within the cell. By doing so, it can dynamically redistribute tasks and resources to maintain optimal balance, ensuring that no single part of the cell becomes a limiting factor in production.
In the context of Japanese manufacturing, where precision and efficiency are paramount, Cell Balancer technology aligns perfectly with industry standards. Japanese companies have long been leaders in implementing Just-In-Time (JIT) and Lean Manufacturing principles, and Cell Balancer enhances these methodologies by providing a more refined and responsive approach to production management.
Advantages of Cell Balancer in Manufacturing
Enhanced Efficiency and Productivity
One of the primary benefits of Cell Balancer technology is the significant boost in efficiency and productivity it offers. By constantly analyzing the performance of each part of the manufacturing cell, Cell Balancer ensures that resources are allocated where they are needed most. This dynamic adjustment minimizes downtime and maximizes output, leading to higher production rates without the need for additional labor or equipment.
Improved Quality Control
Quality control is another area where Cell Balancer excels. By maintaining a balanced workflow, the technology reduces the likelihood of errors and defects that can occur when certain processes are rushed or overloaded. Consistent production rates allow for better oversight and more effective quality assurance measures, resulting in higher standards of finished products.
Cost Reduction
Implementing Cell Balancer technology can lead to significant cost savings. By optimizing resource allocation and minimizing waste, manufacturers can reduce operational costs. Additionally, the increased efficiency translates to lower labor costs and decreased need for excess inventory, further enhancing the cost-effectiveness of production processes.
Flexibility and Scalability
Cell Balancer provides manufacturers with the flexibility to adapt to changing market demands and production requirements. The technology can easily be scaled to accommodate varying levels of production, making it suitable for both small-scale operations and large manufacturing plants. This adaptability is particularly valuable in industries where demand can fluctuate rapidly.
Challenges and Disadvantages
Initial Implementation Costs
Despite its numerous benefits, implementing Cell Balancer technology can be costly. The initial investment required for purchasing the technology, training staff, and integrating it into existing systems can be significant. For some manufacturers, particularly smaller firms, these upfront costs may be a barrier to adoption.
Complexity of Integration
Integrating Cell Balancer into established manufacturing processes can be complex. It requires a thorough understanding of both the technology and the current production workflows. In some cases, existing machinery and systems may need to be upgraded or replaced to be compatible with Cell Balancer, adding to the complexity and cost of implementation.
Dependence on Technology
Relying heavily on Cell Balancer technology also introduces a level of dependence on automated systems. In the event of a system failure or technical issue, production could come to a halt, potentially causing significant disruptions. Manufacturers must therefore ensure robust maintenance and backup systems are in place to mitigate this risk.
Training and Skill Requirements
Effective use of Cell Balancer technology requires personnel to have specialized training and skills. Manufacturers may need to invest in ongoing training programs to ensure that their workforce can effectively operate and maintain the technology. This requirement can add to the overall cost and complexity of adopting Cell Balancer.
Procurement Strategies for Cell Balancer Technology
Identifying Reliable Suppliers
When procuring Cell Balancer technology, it is essential to identify reliable suppliers who have a proven track record in delivering high-quality products and services. Suppliers should be evaluated based on their experience, reputation in the industry, and the level of support they offer during and after the implementation process.
Evaluating Total Cost of Ownership
Manufacturers should conduct a comprehensive analysis of the total cost of ownership (TCO) when procuring Cell Balancer technology. This evaluation should include not only the initial purchase price but also ongoing maintenance costs, training expenses, and potential costs associated with system upgrades or integrations.
Negotiating Terms and Conditions
Effective negotiation is crucial in procurement to ensure favorable terms and conditions. Manufacturers should seek to negotiate aspects such as payment terms, warranty periods, and post-implementation support. Building a strong relationship with the supplier can also lead to better terms and more collaborative problem-solving in the long run.
Assessing Supplier Capabilities
Assessing the capabilities of suppliers is key to successful procurement. This includes evaluating their ability to provide timely delivery, their capacity to scale with the manufacturer’s needs, and the quality of their customer support services. Manufacturers should also consider the supplier’s commitment to innovation and their ability to keep up with technological advancements.
Supplier Negotiation Techniques
Building Strong Relationships
Establishing strong relationships with suppliers can lead to more favorable negotiation outcomes. By fostering trust and open communication, manufacturers can collaborate more effectively with suppliers, leading to better terms, enhanced support, and a more collaborative approach to problem-solving.
Leveraging Bulk Purchasing
Negotiating bulk purchasing agreements can provide significant cost savings. Manufacturers should explore opportunities to purchase Cell Balancer technology in larger quantities, which can often lead to discounts and more favorable pricing structures. This approach benefits both the manufacturer and the supplier by ensuring steady demand and volume.
Exploring Long-Term Contracts
Long-term contracts can be advantageous for both parties. For manufacturers, securing a long-term agreement can provide stability and predictability in pricing and supply. Suppliers, in turn, benefit from guaranteed business and the potential for ongoing partnerships. Negotiating favorable terms within these contracts is crucial for maximizing benefits.
Understanding Supplier Constraints
Understanding the constraints and limitations faced by suppliers can enhance negotiation effectiveness. By recognizing factors such as production capacity, lead times, and cost structures, manufacturers can tailor their negotiation strategies to address these challenges, leading to more realistic and achievable agreements.
Market Conditions for Cell Balancer Technology
Current Market Trends
The market for Cell Balancer technology is influenced by several key trends, including the increasing demand for automation, the push towards Industry 4.0, and the globalization of manufacturing supply chains. These trends drive the adoption of advanced technologies like Cell Balancer, as manufacturers seek to enhance efficiency and remain competitive.
Competitive Landscape
The competitive landscape for Cell Balancer technology includes both established players and emerging innovators. Japanese companies, in particular, are at the forefront of developing and implementing Cell Balancer solutions. Understanding the strengths and offerings of different suppliers is essential for manufacturers looking to make informed procurement decisions.
Economic Factors
Economic factors such as fluctuations in currency exchange rates, changes in trade policies, and global economic conditions can impact the market for Cell Balancer technology. Manufacturers must stay informed about these factors to anticipate potential challenges and adjust their procurement strategies accordingly.
Technological Advancements
Rapid technological advancements are continually shaping the market for Cell Balancer technology. Innovations in artificial intelligence, machine learning, and data analytics are enhancing the capabilities of Cell Balancer systems, making them more efficient and adaptable. Manufacturers should consider the latest technological developments when selecting and implementing Cell Balancer solutions.
Best Practices in Implementing Cell Balancer
Comprehensive Planning
Successful implementation of Cell Balancer technology begins with comprehensive planning. Manufacturers should conduct a thorough analysis of their current production processes, identifying areas where Cell Balancer can provide the most significant benefits. Detailed planning ensures that the technology is seamlessly integrated into existing workflows, minimizing disruptions.
Employee Training and Engagement
Effective implementation requires that employees are properly trained and engaged with the new technology. Providing ongoing training programs and encouraging feedback can help ensure that staff members are comfortable using Cell Balancer and understand its benefits. Engaged employees are more likely to embrace the technology and contribute to its successful integration.
Continuous Monitoring and Evaluation
After implementation, continuous monitoring and evaluation are essential to maintain the effectiveness of Cell Balancer technology. Regularly assessing performance metrics and making necessary adjustments can help sustain optimal efficiency and productivity. Manufacturers should establish a system for ongoing evaluation to identify and address any issues promptly.
Collaborative Approach
Taking a collaborative approach to implementation can enhance the success of Cell Balancer technology. This involves working closely with suppliers, technology providers, and internal teams to ensure that all aspects of the implementation are addressed. Collaboration fosters a supportive environment where challenges can be addressed collectively, leading to more effective solutions.
Conclusion
Cell Balancer technology is revolutionizing modern manufacturing by introducing a new level of efficiency, quality control, and flexibility. Japanese innovation in this area has set a high standard, demonstrating the significant advantages that can be achieved through the integration of advanced technologies. While there are challenges associated with implementation, such as initial costs and the need for specialized training, the long-term benefits often outweigh these obstacles.
For manufacturers looking to stay competitive in an increasingly automated and data-driven industry, adopting Cell Balancer technology offers a strategic advantage. By focusing on effective procurement strategies, strong supplier relationships, and best practices in implementation, companies can harness the full potential of Cell Balancer to enhance their production processes and drive sustained growth.
As the manufacturing landscape continues to evolve, technologies like Cell Balancer will play a crucial role in shaping the future of production. Embracing these innovations will not only improve operational efficiencies but also ensure that manufacturers can meet the demands of a dynamic and competitive global market.
資料ダウンロード
QCD管理受発注クラウド「newji」は、受発注部門で必要なQCD管理全てを備えた、現場特化型兼クラウド型の今世紀最高の受発注管理システムとなります。
ユーザー登録
受発注業務の効率化だけでなく、システムを導入することで、コスト削減や製品・資材のステータス可視化のほか、属人化していた受発注情報の共有化による内部不正防止や統制にも役立ちます。
NEWJI DX
製造業に特化したデジタルトランスフォーメーション(DX)の実現を目指す請負開発型のコンサルティングサービスです。AI、iPaaS、および先端の技術を駆使して、製造プロセスの効率化、業務効率化、チームワーク強化、コスト削減、品質向上を実現します。このサービスは、製造業の課題を深く理解し、それに対する最適なデジタルソリューションを提供することで、企業が持続的な成長とイノベーションを達成できるようサポートします。
製造業ニュース解説
製造業、主に購買・調達部門にお勤めの方々に向けた情報を配信しております。
新任の方やベテランの方、管理職を対象とした幅広いコンテンツをご用意しております。
お問い合わせ
コストダウンが利益に直結する術だと理解していても、なかなか前に進めることができない状況。そんな時は、newjiのコストダウン自動化機能で大きく利益貢献しよう!
(β版非公開)