- お役立ち記事
- Mastering Japanese Manufacturing: How Reference Design is Revolutionizing the Industry
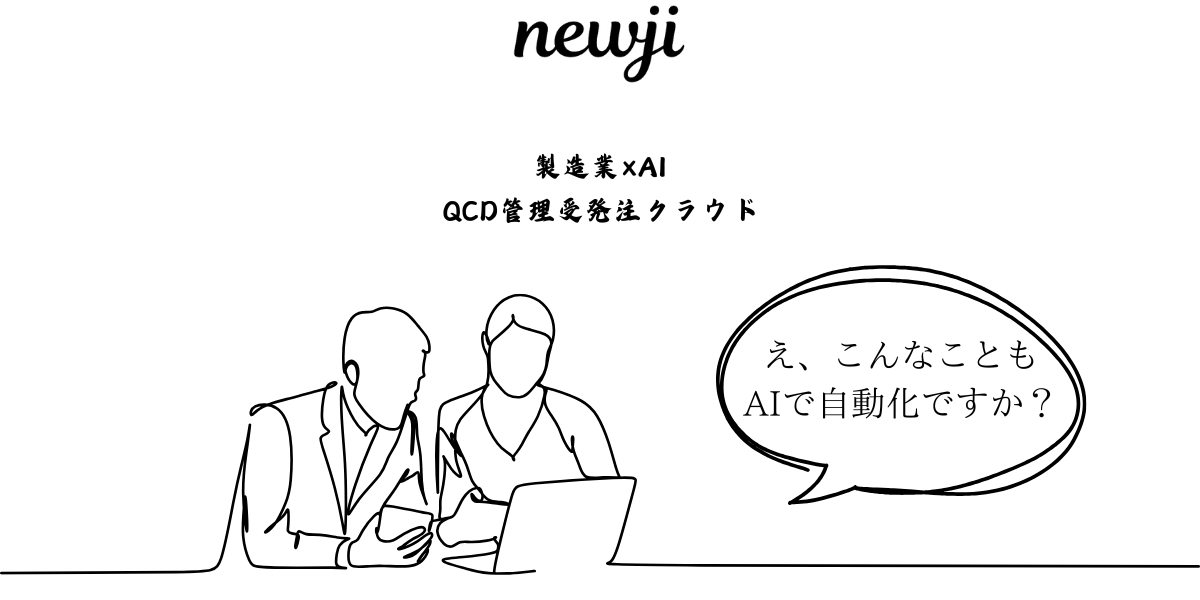
Mastering Japanese Manufacturing: How Reference Design is Revolutionizing the Industry
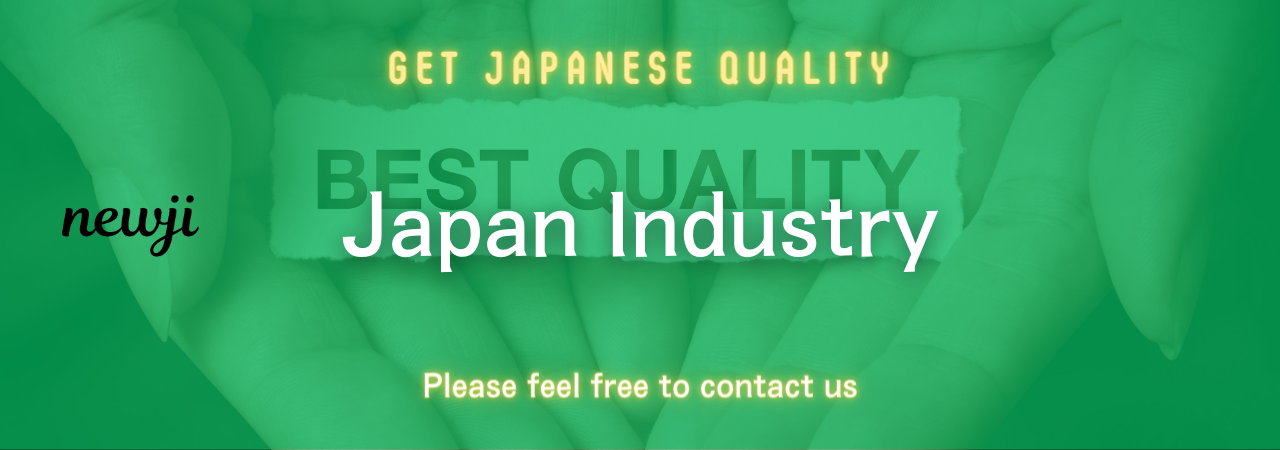
目次
Introduction to Japanese Manufacturing
Japanese manufacturing has long been synonymous with precision, quality, and innovation.
From the automotive sector to consumer electronics, Japanese products are renowned for their reliability and performance.
At the heart of this success lies a deep-rooted culture of continuous improvement, often referred to as **Kaizen**, and an unwavering commitment to high standards of quality control.
Amidst these traditional practices, a new trend is emerging that promises to further revolutionize the industry: reference design.
This concept, although not new, is being leveraged in innovative ways by Japanese manufacturing firms to streamline processes, encourage collaboration, and enhance product development.
Understanding Reference Design
Reference design refers to a proven framework or blueprint that companies use as a starting point for developing new products.
It serves as a foundational template that outlines the essential components, systems, and processes required to create a product.
By providing a clear baseline, reference designs help organizations accelerate development cycles, reduce costs, and ensure consistency and reliability in the final output.
Advantages of Reference Design
One of the primary advantages of reference design is its ability to simplify and standardize the product development process.
This approach helps engineers and designers avoid starting from scratch, thus saving valuable time and resources.
By utilizing a tried-and-tested blueprint, companies can reduce the risk of errors and streamline their production workflows.
Another significant benefit is the facilitation of collaboration between different stakeholders.
Reference designs provide a common language and understanding among engineers, designers, and suppliers, ensuring that everyone is aligned with the project’s objectives.
This level of clarity is particularly crucial in complex manufacturing environments where coordination and precision are paramount.
Additionally, reference design can lead to cost savings.
By starting with a predefined blueprint, companies can avoid unnecessary design iterations and modifications, thus reducing the expenses associated with prototyping and testing.
This approach also allows for better resource allocation, as teams can focus their efforts on enhancing and optimizing the existing framework rather than reinventing the wheel.
The Role of Japanese Suppliers in Reference Design
Japanese suppliers play a critical role in the successful implementation of reference designs.
Their expertise, craftsmanship, and commitment to quality make them ideal partners for companies seeking to adopt this approach.
By collaborating with Japanese suppliers, organizations can leverage their extensive knowledge and experience to create robust and reliable products.
Case Study: Automotive Industry
The automotive industry provides a compelling example of how Japanese suppliers and reference design can work in tandem.
Consider a scenario where an international car manufacturer aims to develop a new electric vehicle.
By utilizing a reference design from a reputable Japanese supplier, the manufacturer can significantly expedite the development process.
The reference design would include essential components such as the battery management system, powertrain, and electronic control units.
These elements are critical to the functionality and efficiency of an electric vehicle, and by adopting a proven blueprint, the manufacturer can ensure that these components meet the highest standards of performance and reliability.
Moreover, Japanese suppliers often provide comprehensive support and guidance throughout the development process.
Their deep understanding of the reference design allows them to offer valuable insights and recommendations, helping the manufacturer optimize the vehicle’s performance and achieve regulatory compliance.
Challenges and Mitigation
While reference design offers numerous advantages, it is not without its challenges.
One common concern is the potential lack of flexibility.
Since reference designs are predefined blueprints, there is a risk that they may not fully align with the unique requirements and specifications of a particular project.
To mitigate this challenge, companies can adopt a hybrid approach that combines the benefits of reference design with the flexibility of customization.
By starting with a reference design as a foundation, teams can then make necessary adjustments and modifications to tailor the product to their specific needs.
Another challenge is ensuring effective communication and collaboration among all stakeholders.
Given the global nature of manufacturing, teams often operate across different time zones and locations, making coordination a complex task.
To address this issue, organizations should invest in robust communication tools and platforms that facilitate real-time collaboration and knowledge sharing.
Best Practices for Implementing Reference Design
Successfully implementing reference design in a manufacturing environment requires careful planning and execution.
Here are some best practices to consider:
1. Select the Right Reference Design
Choosing the appropriate reference design is crucial to the success of the project.
Companies should conduct thorough research and evaluation to identify a blueprint that aligns with their product goals and requirements.
It is also beneficial to seek input and recommendations from industry experts and suppliers.
2. Foster Collaboration
Effective collaboration is key to maximizing the benefits of reference design.
Organizations should establish clear communication channels and foster a culture of teamwork and knowledge sharing.
Regular meetings and updates can help ensure that everyone is on the same page and working towards common objectives.
3. Leverage Supplier Expertise
Japanese suppliers possess a wealth of knowledge and experience that can significantly enhance the implementation process.
Companies should actively engage with their suppliers, seeking their guidance and leveraging their expertise to optimize the reference design.
This collaboration can lead to innovative solutions and improvements that may not have been possible otherwise.
4. Invest in Training
To fully harness the potential of reference design, teams need to have a strong understanding of its principles and methodologies.
Organizations should invest in training and development programs to equip their employees with the necessary skills and knowledge.
This investment will pay off in the long run by ensuring that the team can effectively utilize reference designs to drive innovation and efficiency.
5. Monitor and Evaluate
Continuous monitoring and evaluation are essential to maintaining the effectiveness of reference design.
Organizations should establish key performance indicators (KPIs) and metrics to track the progress and impact of the reference design.
Regular assessments can help identify areas for improvement and ensure that the project remains on track.
Market Conditions and Trends in Japanese Manufacturing
Understanding the market conditions and trends in Japanese manufacturing is essential for companies seeking to adopt reference design and collaborate with Japanese suppliers.
Several key factors and trends are shaping the landscape:
1. Technological Advancements
Japan is at the forefront of technological innovation, particularly in areas such as robotics, artificial intelligence, and the Internet of Things (IoT).
These advancements are driving new possibilities and applications for reference design, enabling companies to create smarter and more connected products.
2. Sustainability and Environmental Consciousness
There is a growing emphasis on sustainability and environmental consciousness in the manufacturing sector.
Japanese companies are increasingly adopting eco-friendly practices and developing green technologies.
Reference design can play a pivotal role in this transition by providing frameworks that prioritize sustainability and reduce waste.
3. Global Demand and Competition
The global demand for high-quality products continues to rise, and Japanese manufacturers face stiff competition from other countries.
To stay competitive, companies must leverage reference design to accelerate product development and enhance quality control.
This approach allows them to meet market demands more efficiently and maintain a competitive edge.
Conclusion
Japanese manufacturing is renowned for its precision, quality, and innovation, and the adoption of reference design is further revolutionizing the industry.
By leveraging proven blueprints and collaborating with experienced Japanese suppliers, companies can streamline their processes, reduce costs, and enhance product development.
While challenges exist, they can be mitigated through effective communication, flexibility, and leveraging supplier expertise.
Understanding market conditions and trends is essential for companies seeking to successfully implement reference design and thrive in the competitive landscape of Japanese manufacturing.
As technology continues to advance and sustainability becomes a priority, reference design will play an increasingly vital role in shaping the future of manufacturing.
資料ダウンロード
QCD調達購買管理クラウド「newji」は、調達購買部門で必要なQCD管理全てを備えた、現場特化型兼クラウド型の今世紀最高の購買管理システムとなります。
ユーザー登録
調達購買業務の効率化だけでなく、システムを導入することで、コスト削減や製品・資材のステータス可視化のほか、属人化していた購買情報の共有化による内部不正防止や統制にも役立ちます。
NEWJI DX
製造業に特化したデジタルトランスフォーメーション(DX)の実現を目指す請負開発型のコンサルティングサービスです。AI、iPaaS、および先端の技術を駆使して、製造プロセスの効率化、業務効率化、チームワーク強化、コスト削減、品質向上を実現します。このサービスは、製造業の課題を深く理解し、それに対する最適なデジタルソリューションを提供することで、企業が持続的な成長とイノベーションを達成できるようサポートします。
オンライン講座
製造業、主に購買・調達部門にお勤めの方々に向けた情報を配信しております。
新任の方やベテランの方、管理職を対象とした幅広いコンテンツをご用意しております。
お問い合わせ
コストダウンが利益に直結する術だと理解していても、なかなか前に進めることができない状況。そんな時は、newjiのコストダウン自動化機能で大きく利益貢献しよう!
(Β版非公開)