- お役立ち記事
- Mastering Japanese Manufacturing: The Revolution of Friction Stir Welding (FSW) in OEM Processing
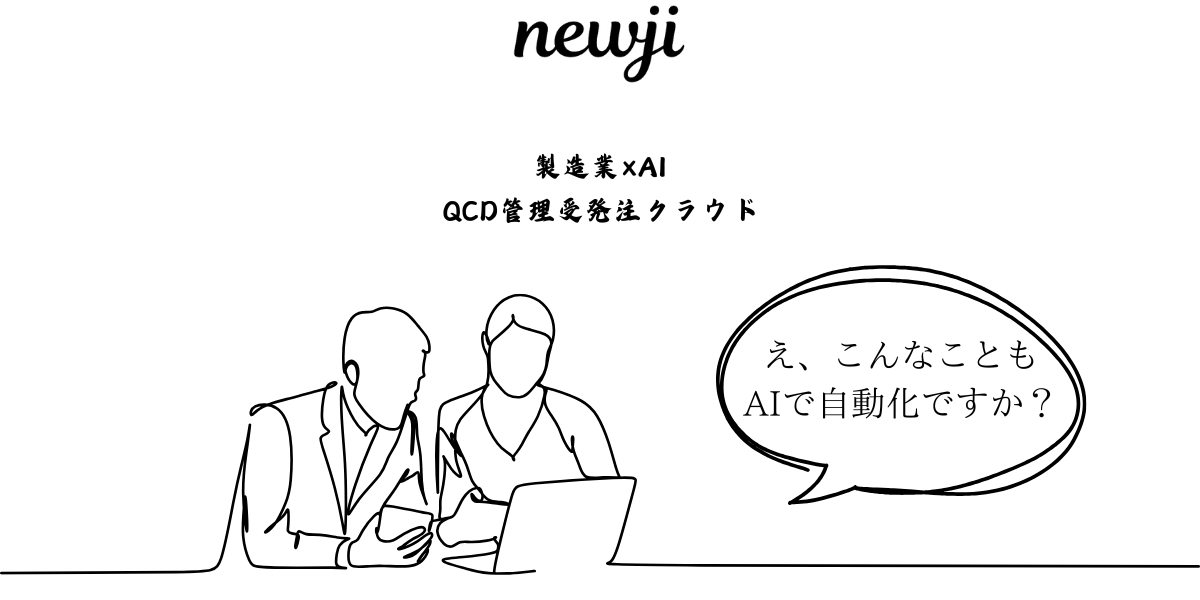
Mastering Japanese Manufacturing: The Revolution of Friction Stir Welding (FSW) in OEM Processing
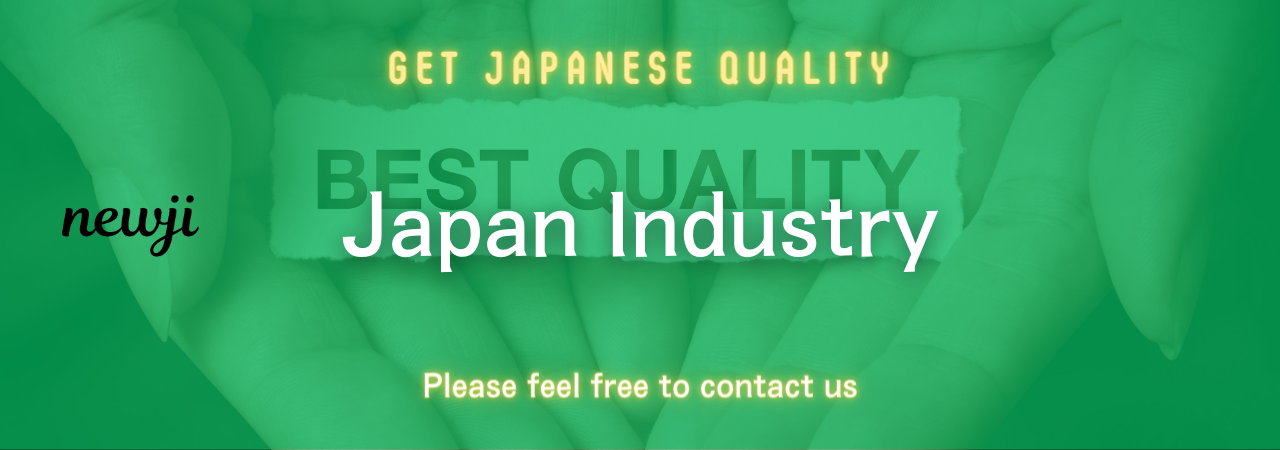
目次
Introduction to Friction Stir Welding (FSW)
Friction Stir Welding (FSW) is a solid-state joining process that has revolutionized the manufacturing landscape, particularly in the Original Equipment Manufacturing (OEM) sector.
Originally developed by The Welding Institute (TWI) in 1991, FSW has since become a pivotal technology in industries ranging from automotive to aerospace.
In contrast to traditional welding methods, which involve melting the base materials, FSW produces joints without reaching the melting point.
This results in a stronger, defect-free weld.
As such, it has garnered substantial attention and investment, particularly from Japanese manufacturing companies renowned for their commitment to quality and innovation.
The Significance of FSW in OEM Processing
Advantages of FSW
One of the primary reasons Japanese suppliers have embraced Friction Stir Welding is due to its myriad advantages over traditional welding techniques.
These include:
– **Superior Strength and Durability**: FSW produces joints that are often stronger than the base materials themselves.
This is especially vital in high-stress applications like automotive chassis and aerospace components.
– **Reduced Defects**: Since FSW doesn’t involve melting, issues such as porosity and solidification cracking are virtually eliminated.
This leads to higher-quality welds and fewer rejects.
– **Energy Efficiency**: FSW requires significantly less energy than traditional welding processes, translating to lower operational costs and a reduced environmental footprint.
– **Versatility**: The process is highly adaptable and can be used on a variety of materials, including aluminum, copper, magnesium, and even steel.
Disadvantages of FSW
Despite its many advantages, FSW is not without its drawbacks.
Potential disadvantages include:
– **Initial Investment**: The machinery and setup costs for FSW are relatively high, which can be a barrier for small manufacturers.
– **Material Thickness Limitations**: FSW is less effective for welding very thick materials, thus limiting its application in certain industries.
– **Skilled Labor Requirement**: While FSW is automated, it still requires skilled operators to manage and troubleshoot the process, which can add to training and labor costs.
Supplier Negotiation Techniques
When engaging with Japanese suppliers for FSW services, effective negotiation is key to attaining favorable terms and fostering a long-term partnership.
Research and Preparation
Before entering negotiations, extensive research is crucial.
Understand the supplier’s capabilities, past projects, and reputation.
Familiarize yourself with industry benchmarks and standards.
Arming yourself with this knowledge will allow you to build a more compelling case during negotiations.
Building Relationships
Japanese business culture places a strong emphasis on building relationships.
Formal meetings often start with casual conversations aimed at establishing rapport.
Be prepared to invest time in nurturing these relationships, as they can significantly impact your negotiation outcomes.
Emphasize Quality and Reliability
Japanese suppliers pride themselves on quality and reliability.
When negotiating, focus on these aspects and highlight how your company values these attributes.
This alignment in core values can pave the way for more favorable terms.
Long-term Contracts
Japanese suppliers prefer long-term commitments over short-term gains.
Proposing a long-term contract can provide security for both parties and may result in more competitive pricing and priority service.
Market Conditions
Understanding the current market conditions is essential for making informed procurement decisions.
Several factors influence the FSW market in Japan:
Technological Advancements
Japan has been at the forefront of FSW technological advancements.
Continuous improvements in FSW tools and machines contribute to better efficiency and lower costs.
Staying abreast of these developments can offer strategic advantages.
Economic Climate
Japan’s economy, like others, is subject to fluctuations.
Economic factors such as inflation, exchange rates, and trade policies can impact costs.
Keeping an eye on these indicators can help in timing your procurement to capitalize on favorable conditions.
Supply Chain Stability
Japan has a well-established supply chain network, but disruptions can still occur due to natural disasters, geopolitical tensions, or pandemics.
Assessing the stability of the supply chain and having contingency plans can mitigate risks.
Best Practices in FSW Procurement
Procurement professionals can adopt several best practices to optimize their FSW sourcing strategy:
Supplier Audits
Regular audits of supplier facilities are essential for assessing their capabilities and ensuring compliance with standards.
This also helps identify areas for improvement and fosters transparency.
Quality Assurance Programs
Implementing robust quality assurance programs can help in maintaining high standards.
This involves regular testing of welds, adherence to ISO standards, and continuous improvement initiatives.
Cost-Benefit Analysis
Conduct thorough cost-benefit analyses to compare FSW with other welding methods.
Consider all factors, including upfront costs, long-term savings, and potential quality improvements.
Training and Development
Investing in training your team on the nuances of FSW can yield significant dividends.
A well-informed team can make better procurement decisions and effectively manage supplier relationships.
Conclusion
Friction Stir Welding represents a significant leap forward in the manufacturing sector, offering unparalleled advantages in terms of weld quality, energy efficiency, and versatility.
Japanese suppliers, with their dedication to quality and innovation, are well-positioned to leverage this technology to its fullest potential.
For procurement and purchasing professionals, understanding the intricacies of FSW and effectively navigating supplier relationships is key to unlocking the benefits this technology offers.
By adopting best practices, staying informed about market conditions, and honing negotiation techniques, your organization can master the art of FSW procurement, ensuring superior products and competitive edge in the market.
資料ダウンロード
QCD調達購買管理クラウド「newji」は、調達購買部門で必要なQCD管理全てを備えた、現場特化型兼クラウド型の今世紀最高の購買管理システムとなります。
ユーザー登録
調達購買業務の効率化だけでなく、システムを導入することで、コスト削減や製品・資材のステータス可視化のほか、属人化していた購買情報の共有化による内部不正防止や統制にも役立ちます。
NEWJI DX
製造業に特化したデジタルトランスフォーメーション(DX)の実現を目指す請負開発型のコンサルティングサービスです。AI、iPaaS、および先端の技術を駆使して、製造プロセスの効率化、業務効率化、チームワーク強化、コスト削減、品質向上を実現します。このサービスは、製造業の課題を深く理解し、それに対する最適なデジタルソリューションを提供することで、企業が持続的な成長とイノベーションを達成できるようサポートします。
オンライン講座
製造業、主に購買・調達部門にお勤めの方々に向けた情報を配信しております。
新任の方やベテランの方、管理職を対象とした幅広いコンテンツをご用意しております。
お問い合わせ
コストダウンが利益に直結する術だと理解していても、なかなか前に進めることができない状況。そんな時は、newjiのコストダウン自動化機能で大きく利益貢献しよう!
(Β版非公開)