- お役立ち記事
- “Mastering Japanese Manufacturing: Understanding When to Use ‘Grinder’ vs. ‘Polishing Machine'”
月間76,176名の
製造業ご担当者様が閲覧しています*
*2025年3月31日現在のGoogle Analyticsのデータより
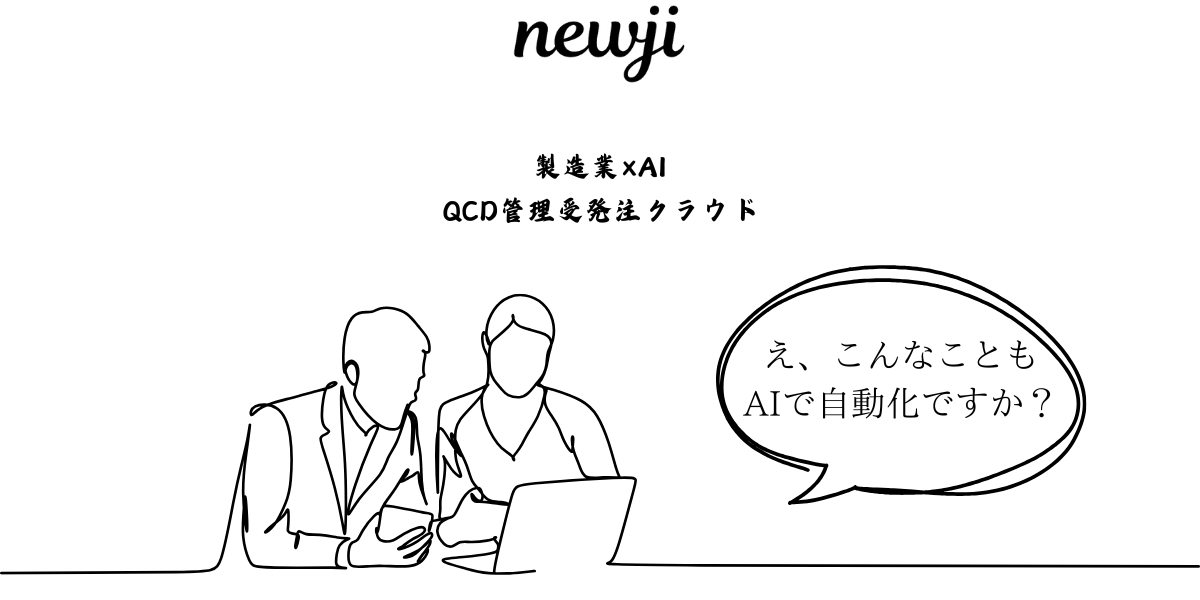
“Mastering Japanese Manufacturing: Understanding When to Use ‘Grinder’ vs. ‘Polishing Machine'”
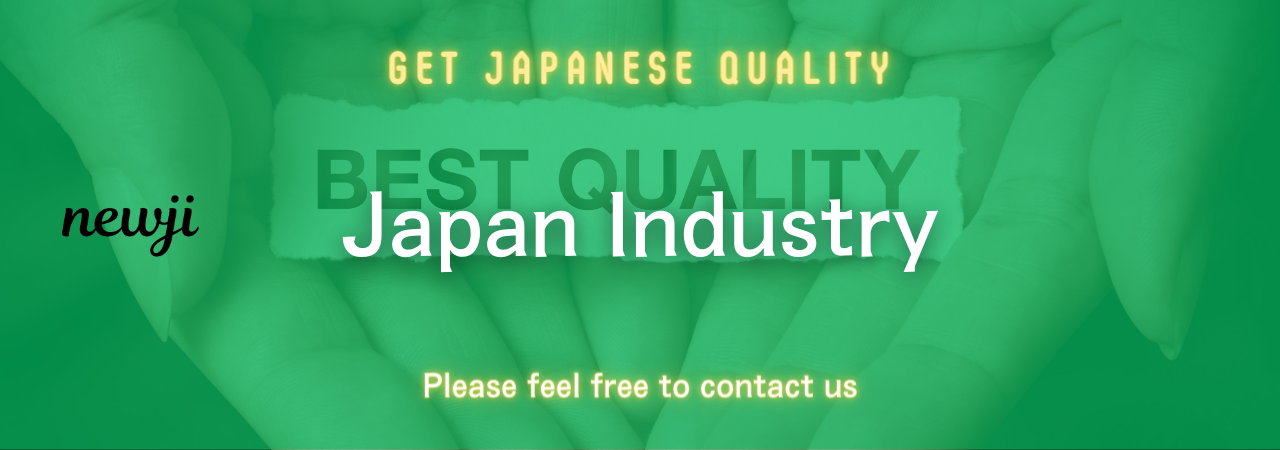
目次
Understanding the Basics
When it comes to manufacturing, achieving the desired surface finish and precision on a workpiece can make or break the product quality. Two essential tools in this aspect are the grinder and the polishing machine. As someone who has spent over two decades in the intricacies of procurement and production management, I’ve seen firsthand the importance of selecting the right machine for the right job.
Grinder: The Heavy-Duty Workhorse
A grinder is an industrial tool designed for the rapid removal of material to shape and prepare a workpiece for further finishing operations. Typically utilized in tasks that require substantial material removal, grinders come in various types, including surface grinders, cylindrical grinders, and tool and cutter grinders.
Types of Grinders
1. Surface Grinders
Surface grinders are used for creating a flat surface on a workpiece. With the ability to work with a coarser grit, they are ideal for initial phases of material removal.
2. Cylindrical Grinders
Cylindrical grinders are more specialized, utilized for grinding internal and external surfaces of cylindrical parts. This type is essential for achieving high tolerance and precise finishes.
3. Tool and Cutter Grinders
Tool and cutter grinders are versatile machines used to sharpen milling cutters, tool bits, and other complex cutting tools. They essentially prolong the life of tooling in manufacturing setups.
Applications of Grinders
Industrial grinders are indispensable in numerous fields, including automotive, aerospace, and heavy machinery. They are commonly used for:
– Preparing surfaces for welding or further machining
– Shaping parts to precise dimensions
– Removing excess material to bring a piece to a rough shape
– Sharpening tooling and cutting implements
Polishing Machines: The Finishers
While grinders focus on heavy-duty material removal, polishing machines are utilized to achieve a fine surface finish. The primary role of polishing machines is to enhance the aesthetic appeal and smoothness of a workpiece, making it visually and tactilely pleasing.
Types of Polishing Machines
1. Buffing Machines
Buffing machines employ wheels impregnated with polishing compounds to achieve a stunning, reflective finish. They are often used on metals, plastics, and other materials requiring a high sheen.
2. Suction Polishers
These machines are used to polish while simultaneously removing dust and debris through suction, making them particularly useful in applications requiring a clean process.
3. Magnetic Polishing Machines
Using fine magnetic particles and a rotating magnetic field, these machines are ideal for polishing intricately shaped parts, including those with internal cavities.
Applications of Polishing Machines
Polishing machines are crucial for industries where surface quality is pivotal, such as:
– Jewelry manufacturing where high gloss is required
– Medical devices that need smooth, tactile-friendly surfaces
– Automotive parts where the appearance contributes to consumer appeal
Advantages and Disadvantages of Grinders and Polishing Machines
Advantages of Grinders
1. **Versatility:** Suitable for a wide range of materials and shapes.
2. **Speed:** Capable of quick material removal.
3. **Precision:** High accuracy and tolerance achievable.
4. **Tool Life Extension:** Can hone and sharpen other tools.
Disadvantages of Grinders
1. **Heat Production:** Can generate considerable heat that may affect the material properties.
2. **Surface Finish:** Typically results in a rougher surface compared to polishing.
3. **Skill Requirement:** Operators need significant training and experience.
Advantages of Polishing Machines
1. **Surface Quality:** Provides a superior smooth and shiny finish.
2. **Usability:** Often simpler to use and require less skill compared to grinders.
3. **Specialization:** Excellent for finishing tasks post-grinding or machining.
Disadvantages of Polishing Machines
1. **Material Removal:** Inefficient for substantial material removal.
2. **Machine Wear:** Polishing compounds and wheels can wear quickly.
3. **Speed:** Slower compared to grinders, especially for initial shaping tasks.
When to Use a Grinder vs. Polishing Machine
Selecting between a grinder and a polishing machine depends on several factors:
Task Requirements
If the job involves initial shaping, large amounts of material removal, or preparation for subsequent operations, a grinder is essential. On the other hand, if the goal is to achieve a high-quality surface finish, a polishing machine is more appropriate.
Material Type
Harder materials such as metals often require the robust capabilities of grinders, while softer materials that need a fine finish, such as plastics or coatings, are better suited for polishing.
Final Product Specifications
Products with tight dimensional tolerances may need preliminary grinding for accuracy, followed by polishing for surface quality.
Best Practices for Using Grinders and Polishing Machines
For Grinders
1. **Coolant Usage:** Utilize coolant to minimize heat buildup.
2. **Wheel Selection:** Choose the appropriate grinding wheel material and grit size.
3. **Safety Measures:** Ensure the use of protective gear and proper machine guarding.
For Polishing Machines
1. **Compound Selection:** Use the right polishing compound for the material.
2. **Pressure Control:** Apply consistent pressure to avoid over-polishing or surface damage.
3. **Cleaning:** Regularly clean the polishing wheels to maintain effectiveness.
Supplier Negotiation Techniques
When dealing with Japanese suppliers, understanding their cultural nuances is vital for successful negotiations.
Building Relationships
Japanese business culture places a high value on relationships. Establish trust and show respect to foster long-term partnerships.
Communication
Be clear and precise in your needs. Japanese suppliers appreciate detailed and unambiguous requirements.
Negotiate with Patience
Expect negotiations to be detail-oriented. Patience and attentiveness can pay dividends in securing favorable terms.
Market Conditions
The market for grinders and polishing machines in Japan is highly competitive and technology-driven. Japanese manufacturers are known for precision and quality, ensuring that machines from Japan often outperform other international makes.
Technological Advancements
Stay abreast of the latest technological advancements from Japanese manufacturers. Innovations in automation and AI integration are particularly noteworthy.
Quality Assurance
Japanese suppliers often adhere to stringent quality control standards. Leverage this to ensure high-quality procurement of grinders and polishing machines.
Conclusion
Mastering the use of grinders and polishing machines requires understanding their distinct roles in manufacturing. Both tools are indispensable in achieving the double objectives of structural integrity and surface quality. By navigating these tools wisely and leveraging relationships with Japanese suppliers, manufacturing companies can enhance their production efficacy and quality, ensuring they remain competitive in global markets.
Remember, the key to effective procurement and application lies in understanding the nuances of each tool and capitalizing on the strengths of your suppliers. This nuanced approach will set you on the path to mastering Japanese manufacturing excellence.
資料ダウンロード
QCD管理受発注クラウド「newji」は、受発注部門で必要なQCD管理全てを備えた、現場特化型兼クラウド型の今世紀最高の受発注管理システムとなります。
ユーザー登録
受発注業務の効率化だけでなく、システムを導入することで、コスト削減や製品・資材のステータス可視化のほか、属人化していた受発注情報の共有化による内部不正防止や統制にも役立ちます。
NEWJI DX
製造業に特化したデジタルトランスフォーメーション(DX)の実現を目指す請負開発型のコンサルティングサービスです。AI、iPaaS、および先端の技術を駆使して、製造プロセスの効率化、業務効率化、チームワーク強化、コスト削減、品質向上を実現します。このサービスは、製造業の課題を深く理解し、それに対する最適なデジタルソリューションを提供することで、企業が持続的な成長とイノベーションを達成できるようサポートします。
製造業ニュース解説
製造業、主に購買・調達部門にお勤めの方々に向けた情報を配信しております。
新任の方やベテランの方、管理職を対象とした幅広いコンテンツをご用意しております。
お問い合わせ
コストダウンが利益に直結する術だと理解していても、なかなか前に進めることができない状況。そんな時は、newjiのコストダウン自動化機能で大きく利益貢献しよう!
(β版非公開)