- お役立ち記事
- “Mastering Japanese Manufacturing: Unleashing the Power of the PDCA Cycle for Continuous Improvement”
“Mastering Japanese Manufacturing: Unleashing the Power of the PDCA Cycle for Continuous Improvement”
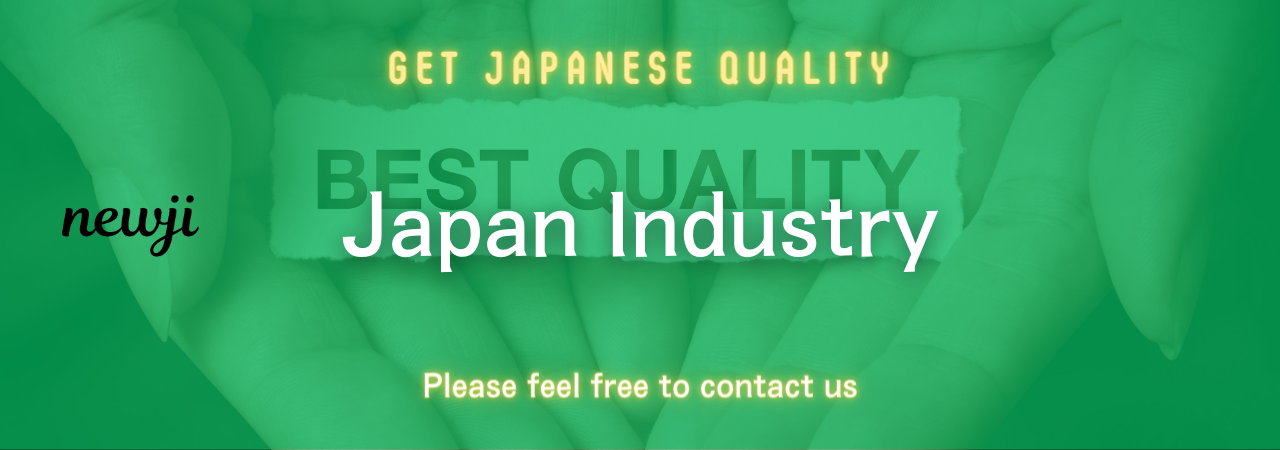
目次
Introduction
In the competitive landscape of global manufacturing, continuous improvement is not just a strategy but a necessity.
Japanese manufacturing has long been recognized for its exceptional quality and efficiency, largely owing to its adoption of the PDCA cycle.
This article delves deep into the PDCA cycle, its significance in Japanese manufacturing, and how mastering it can unleash unparalleled benefits for procurement and purchasing professionals.
Understanding the PDCA Cycle
What is the PDCA Cycle?
The PDCA cycle, also known as the Deming Cycle, is a four-step management method used for continuous improvement of processes and products.
PDCA stands for Plan, Do, Check, Act.
Each phase serves a distinct purpose in driving systematic enhancements.
Origins and Adoption in Japanese Manufacturing
The PDCA cycle was popularized by Dr. W. Edwards Deming, an American statistician who significantly influenced Japanese post-war industrial practices.
Japanese manufacturers embraced the PDCA cycle as a framework to foster a culture of quality and efficiency.
Over time, it became integral to methodologies like Total Quality Management (TQM) and Lean Manufacturing.
Importance of PDCA in Continuous Improvement
Continuous improvement, or Kaizen, is a cornerstone of Japanese manufacturing philosophy.
The PDCA cycle provides a structured approach to implementing Kaizen by ensuring that improvements are planned, executed, evaluated, and institutionalized effectively.
This iterative process helps organizations adapt to changes, resolve issues proactively, and sustain high-quality standards.
Implementing the PDCA Cycle in Procurement and Purchasing
Plan Phase
In the planning phase, procurement teams identify areas for improvement, set objectives, and develop strategies to achieve them.
This involves analyzing current procurement processes, assessing supplier performance, and understanding market trends.
Setting SMART (Specific, Measurable, Achievable, Relevant, Time-bound) goals ensures clarity and direction.
Do Phase
During the do phase, the planned strategies are implemented on a small scale to test their effectiveness.
This could involve negotiating new terms with suppliers, adopting new sourcing methods, or integrating advanced procurement technologies.
Pilot projects allow teams to gather data and observe the impact of changes before full-scale implementation.
Check Phase
The check phase involves monitoring and evaluating the outcomes of the implemented strategies.
Key performance indicators (KPIs) such as cost savings, supplier lead times, and quality metrics are analyzed to assess the success of the initiatives.
This phase identifies what worked well and what needs adjustment.
Act Phase
Based on the evaluation, the act phase entails making necessary adjustments to refine the strategies.
Successful practices are standardized and integrated into regular procurement processes.
Areas requiring further improvement are looped back into the next PDCA cycle, fostering an ongoing cycle of enhancement.
Advantages of Using PDCA in Japanese Manufacturing
Enhanced Efficiency
The PDCA cycle promotes systematic problem-solving and process optimization, leading to increased operational efficiency.
By continuously identifying and eliminating waste, manufacturers can streamline their supply chains and reduce lead times.
Quality Control
Implementing PDCA ensures rigorous quality checks at every stage of the procurement and production process.
This proactive approach minimizes defects, enhances product reliability, and boosts customer satisfaction.
Supplier Relationships
The PDCA cycle fosters collaborative relationships with suppliers by encouraging transparent communication and joint problem-solving.
Strong supplier partnerships lead to better terms, improved reliability, and mutual growth.
Disadvantages and Challenges
Resistance to Change
One of the primary challenges in implementing the PDCA cycle is overcoming resistance to change within the organization.
Employees accustomed to traditional methods may be hesitant to adopt new processes, necessitating effective change management strategies.
Time-Consuming Processes
The iterative nature of the PDCA cycle can be time-consuming, especially in environments where rapid decision-making is critical.
Balancing thorough analysis with the need for agility is essential to prevent delays in implementation.
Supplier Negotiation Techniques in Japanese Manufacturing
Building Trust
Trust is the foundation of successful supplier negotiations in Japanese manufacturing.
Developing long-term relationships based on mutual respect and reliability fosters cooperation and favorable outcomes.
Long-term Relationship Focus
Rather than prioritizing short-term gains, Japanese manufacturers emphasize long-term collaborations with suppliers.
This approach ensures stability, consistent quality, and shared growth objectives.
Consensus-based Decision Making
Negotiations often involve consensus-based decision-making, where all parties collaborate to reach mutually beneficial agreements.
This method enhances commitment and ensures that all stakeholders are aligned with the agreed-upon terms.
Market Conditions Influencing PDCA Implementation
Global Competition
Intense global competition drives the need for continuous improvement to maintain a competitive edge.
Japanese manufacturers leverage the PDCA cycle to innovate and uphold high standards in the face of international rivals.
Technological Advancements
Rapid technological advancements require manufacturers to adapt swiftly.
The PDCA cycle facilitates the integration of new technologies by providing a structured framework for evaluation and implementation.
Economic Factors
Economic fluctuations impact procurement strategies and resource allocation.
The PDCA cycle enables organizations to respond proactively to economic changes by adjusting plans and optimizing processes.
Best Practices for Mastering PDCA in Japanese Manufacturing
Continuous Training and Education
Investing in training programs ensures that employees are well-versed in the PDCA methodology and its application.
Continuous education fosters a culture of learning and adaptability, essential for sustained improvement.
Effective Communication
Clear and open communication channels are vital for the successful implementation of the PDCA cycle.
Ensuring that all team members understand their roles and the objectives of each phase enhances collaboration and efficiency.
Data-Driven Decision Making
Relying on accurate data is crucial for informed decision-making throughout the PDCA cycle.
Implementing robust data collection and analysis systems supports objective evaluations and effective strategy adjustments.
Case Studies
Successful Implementation in Automotive Manufacturing
A leading Japanese automotive manufacturer integrated the PDCA cycle into its procurement process to enhance supplier quality.
By systematically analyzing supplier performance, implementing targeted improvements, and fostering collaborative relationships, the company achieved significant reductions in defect rates and cost savings.
Electronics Sector Transformation
In the electronics industry, a major manufacturer employed the PDCA cycle to streamline its supply chain operations.
Through continuous monitoring and iterative improvements, the company optimized inventory management, reduced lead times, and improved overall supply chain resilience.
Conclusion
Mastering the PDCA cycle is instrumental in unlocking the full potential of Japanese manufacturing practices.
By embracing this structured approach, procurement and purchasing professionals can drive continuous improvement, enhance supplier relationships, and maintain a competitive edge in the global marketplace.
While challenges such as resistance to change and the time-consuming nature of the process exist, the long-term benefits of efficiency, quality, and collaboration make the PDCA cycle an invaluable tool for sustained success.
資料ダウンロード
QCD調達購買管理クラウド「newji」は、調達購買部門で必要なQCD管理全てを備えた、現場特化型兼クラウド型の今世紀最高の購買管理システムとなります。
ユーザー登録
調達購買業務の効率化だけでなく、システムを導入することで、コスト削減や製品・資材のステータス可視化のほか、属人化していた購買情報の共有化による内部不正防止や統制にも役立ちます。
NEWJI DX
製造業に特化したデジタルトランスフォーメーション(DX)の実現を目指す請負開発型のコンサルティングサービスです。AI、iPaaS、および先端の技術を駆使して、製造プロセスの効率化、業務効率化、チームワーク強化、コスト削減、品質向上を実現します。このサービスは、製造業の課題を深く理解し、それに対する最適なデジタルソリューションを提供することで、企業が持続的な成長とイノベーションを達成できるようサポートします。
オンライン講座
製造業、主に購買・調達部門にお勤めの方々に向けた情報を配信しております。
新任の方やベテランの方、管理職を対象とした幅広いコンテンツをご用意しております。
お問い合わせ
コストダウンが利益に直結する術だと理解していても、なかなか前に進めることができない状況。そんな時は、newjiのコストダウン自動化機能で大きく利益貢献しよう!
(Β版非公開)