- お役立ち記事
- Mastering Maintenance Management: Lessons from Japanese Manufacturing Excellence
Mastering Maintenance Management: Lessons from Japanese Manufacturing Excellence
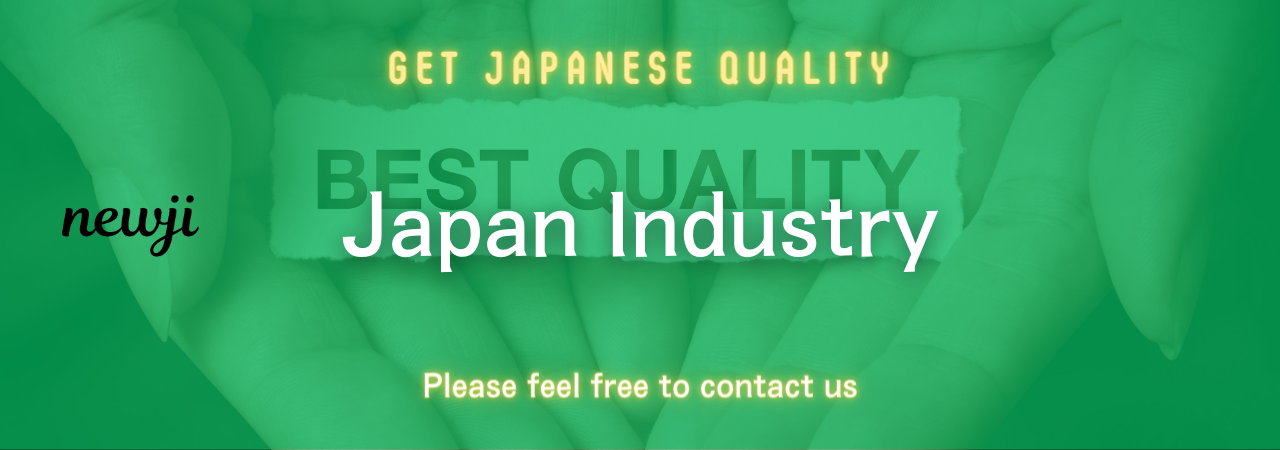
目次
The Foundations of Japanese Manufacturing Excellence
Japanese manufacturing has long been a benchmark for excellence in the global industry.
The foundation of this success lies in a combination of cultural principles and innovative management practices.
Understanding these foundations is crucial for mastering maintenance management inspired by Japanese methodologies.
Lean Manufacturing Principles
Lean manufacturing is a cornerstone of Japanese production techniques.
It emphasizes the elimination of waste, continuous improvement, and efficiency.
By focusing on value-added activities, Japanese manufacturers optimize their processes and resources.
This approach not only reduces costs but also enhances product quality and customer satisfaction.
Total Productive Maintenance (TPM)
TPM is a proactive maintenance strategy aimed at maximizing the operational efficiency of equipment.
It involves all employees in maintenance activities, fostering a culture of shared responsibility.
Japanese companies implement TPM to prevent equipment failures, reduce downtime, and extend machinery lifespan.
This collaborative effort between maintenance and production teams leads to seamless operations and high productivity.
Procurement and Purchasing Strategies
Effective procurement and purchasing strategies are vital for sustaining manufacturing excellence.
Japanese companies excel in these areas by adopting meticulous and strategic approaches.
These strategies ensure a reliable supply chain, cost-effectiveness, and quality assurance.
Building Long-term Supplier Relationships
Japanese manufacturers prioritize long-term partnerships with suppliers.
This approach fosters trust, reliability, and mutual growth.
By investing in supplier development and maintaining open communication, companies ensure consistent quality and timely deliveries.
Long-term relationships also enable better negotiation terms and collaborative problem-solving.
Supplier Selection and Evaluation
The selection process in Japanese procurement is rigorous and thorough.
Suppliers are evaluated based on quality, reliability, financial stability, and their ability to innovate.
Regular assessments and performance reviews ensure that only the best suppliers remain in the supply chain.
This meticulous selection process minimizes risks and maintains high standards across the supply network.
Advantages of Japanese Maintenance Management
Japanese maintenance management practices offer numerous benefits that contribute to overall manufacturing excellence.
These advantages enhance quality control, efficiency, and productivity, positioning Japanese companies as industry leaders.
Enhanced Quality Control
Japanese maintenance management emphasizes stringent quality control measures.
Regular inspections, preventive maintenance, and continuous monitoring ensure that equipment operates at peak performance.
This focus on quality reduces defects, minimizes waste, and guarantees the reliability of final products.
Increased Efficiency and Productivity
Efficient maintenance practices lead to higher operational uptime and productivity.
By preventing unexpected breakdowns and optimizing maintenance schedules, Japanese companies achieve smooth and uninterrupted production flows.
This efficiency translates to faster turnaround times, increased output, and better utilization of resources.
Challenges and Disadvantages
While Japanese maintenance management offers significant advantages, there are also challenges and potential drawbacks to consider.
Understanding these can help organizations navigate and mitigate potential issues when adopting similar practices.
Cultural and Communication Barriers
Cultural differences can pose challenges in implementing Japanese maintenance practices.
Language barriers, differing work ethics, and varied communication styles may hinder effective collaboration.
Overcoming these barriers requires cultural sensitivity, language training, and fostering an inclusive work environment.
Dependency on Suppliers
Relying heavily on long-term suppliers can lead to dependency.
This dependency may limit flexibility and responsiveness to market changes or disruptions.
Diversifying the supplier base and developing contingency plans are essential to mitigate the risks associated with supplier dependency.
Supplier Negotiation Techniques
Effective negotiation with suppliers is critical for maintaining a robust supply chain.
Japanese negotiation techniques emphasize collaboration, transparency, and mutual benefit.
These strategies foster strong partnerships and ensure favorable terms for both parties.
Collaborative Negotiation Approach
Japanese negotiations focus on building consensus and long-term relationships.
Rather than adopting a confrontational stance, both parties work together to find solutions that benefit everyone.
This collaborative approach enhances trust and paves the way for sustainable partnerships.
Win-Win Strategies
Win-win negotiation strategies aim to create value for both the manufacturer and the supplier.
By aligning interests and addressing the needs of both parties, negotiations result in mutually beneficial agreements.
This approach leads to increased cooperation, loyalty, and long-term success.
Market Conditions and Their Impact
Market conditions play a significant role in shaping maintenance management and procurement strategies.
Japanese manufacturers adeptly navigate these conditions to maintain their competitive edge.
Adapting to Changing Market Dynamics
The global market is constantly evolving, presenting both opportunities and challenges.
Japanese companies stay ahead by being adaptable and responsive to changes in demand, technology, and competition.
Flexibility in operations and strategic planning enable them to thrive in diverse market environments.
Supply Chain Resilience
Building a resilient supply chain is essential for mitigating risks associated with market fluctuations.
Japanese manufacturers invest in robust supply chain management practices, including diversification and risk assessment.
This resilience ensures continuity in production and minimizes the impact of unforeseen disruptions.
Best Practices for Maintenance Management
Adopting best practices from Japanese maintenance management can significantly enhance operational efficiency and reliability.
These practices focus on continuous improvement, preventive measures, and employee involvement.
Continuous Improvement (Kaizen)
Kaizen, or continuous improvement, is a fundamental principle in Japanese management.
It involves making incremental changes to processes and practices to enhance efficiency and quality.
By fostering a culture of ongoing improvement, companies can achieve sustained growth and excellence.
Preventive and Predictive Maintenance
Preventive maintenance focuses on regular inspections and servicing to prevent equipment failures.
Predictive maintenance uses data and analytics to predict potential issues before they occur.
Combining both approaches ensures timely interventions, reduces downtime, and extends equipment lifespan.
Lessons Learned and Implementation Strategies
Implementing Japanese maintenance management practices requires careful planning and adaptation to specific organizational contexts.
The following strategies can facilitate successful adoption and integration.
Adopting Japanese Practices in Diverse Environments
Organizations must tailor Japanese maintenance practices to fit their unique cultural and operational contexts.
This involves understanding the underlying principles and adapting them to align with local practices and employee behaviors.
Customized implementation ensures that the practices are effective and sustainable.
Training and Employee Engagement
Effective implementation relies on comprehensive training and active employee engagement.
Employees should be educated on the importance of maintenance practices and empowered to contribute to continuous improvement.
Engaged and knowledgeable staff are crucial for the successful execution of maintenance strategies.
Conclusion
Mastering maintenance management through the lessons of Japanese manufacturing excellence offers immense benefits for organizations.
By embracing principles such as lean manufacturing, TPM, and Kaizen, companies can enhance quality, efficiency, and productivity.
Effective procurement and purchasing strategies, coupled with collaborative supplier negotiations, strengthen the supply chain and foster long-term partnerships.
While challenges such as cultural barriers and supplier dependency exist, they can be mitigated through thoughtful strategies and adaptation.
Adopting best practices and focusing on continuous improvement ensure sustained operational excellence.
Japanese manufacturing provides valuable insights that, when appropriately implemented, can drive significant advancements in maintenance management and overall organizational success.
資料ダウンロード
QCD調達購買管理クラウド「newji」は、調達購買部門で必要なQCD管理全てを備えた、現場特化型兼クラウド型の今世紀最高の購買管理システムとなります。
ユーザー登録
調達購買業務の効率化だけでなく、システムを導入することで、コスト削減や製品・資材のステータス可視化のほか、属人化していた購買情報の共有化による内部不正防止や統制にも役立ちます。
NEWJI DX
製造業に特化したデジタルトランスフォーメーション(DX)の実現を目指す請負開発型のコンサルティングサービスです。AI、iPaaS、および先端の技術を駆使して、製造プロセスの効率化、業務効率化、チームワーク強化、コスト削減、品質向上を実現します。このサービスは、製造業の課題を深く理解し、それに対する最適なデジタルソリューションを提供することで、企業が持続的な成長とイノベーションを達成できるようサポートします。
オンライン講座
製造業、主に購買・調達部門にお勤めの方々に向けた情報を配信しております。
新任の方やベテランの方、管理職を対象とした幅広いコンテンツをご用意しております。
お問い合わせ
コストダウンが利益に直結する術だと理解していても、なかなか前に進めることができない状況。そんな時は、newjiのコストダウン自動化機能で大きく利益貢献しよう!
(Β版非公開)