- お役立ち記事
- Mastering Manufacturing: How Japan Revolutionizes Material Requirements Planning (MRP)
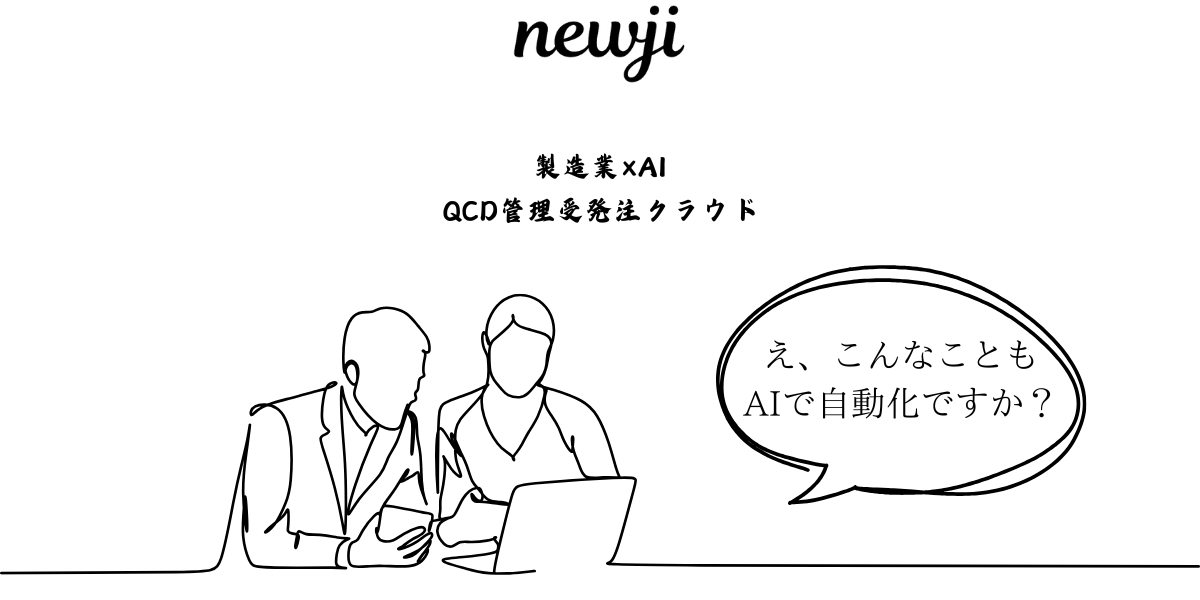
Mastering Manufacturing: How Japan Revolutionizes Material Requirements Planning (MRP)
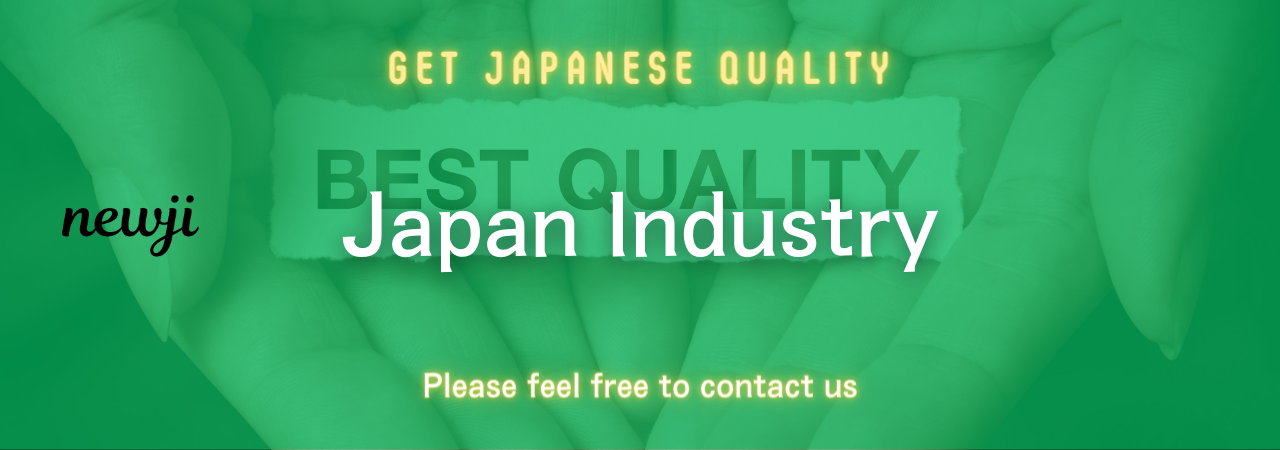
目次
Introduction to Material Requirements Planning (MRP)
Material Requirements Planning (MRP) is a critical component in manufacturing that ensures the efficient production and timely delivery of products. It involves the planning and control of inventory, scheduling of production processes, and coordination of procurement activities to meet the demand for finished goods. Effective MRP systems help manufacturers minimize costs, reduce waste, and maintain high levels of customer satisfaction.
Japan has long been recognized for its innovative manufacturing practices and advanced production systems. Japanese companies have revolutionized MRP through the integration of cutting-edge technologies, lean manufacturing principles, and a strong emphasis on continuous improvement. This article explores how Japan has transformed material requirements planning, the advantages and disadvantages of their approach, supplier negotiation techniques, market conditions, and best practices that can be adopted by manufacturers worldwide.
The Evolution of MRP in Japan
Historical Context
Japan’s journey in refining MRP began in the post-World War II era when the country focused on rebuilding its industrial base. Faced with limited resources, Japanese manufacturers were compelled to optimize their production processes and inventory management. This necessity led to the development of innovative methods that prioritized efficiency and waste reduction.
One of the significant milestones in Japan’s MRP evolution was the adoption of the Toyota Production System (TPS) in the 1950s and 1960s. TPS introduced concepts such as Just-In-Time (JIT) manufacturing, Kanban scheduling systems, and total quality management. These principles laid the foundation for modern MRP practices by emphasizing the importance of precise inventory control and seamless production scheduling.
Integration of Technology
As technology advanced, Japanese manufacturers began integrating sophisticated software solutions into their MRP systems. The adoption of Enterprise Resource Planning (ERP) systems allowed for the real-time tracking of inventory levels, production schedules, and supplier performance. These systems facilitated better decision-making and improved coordination across various departments within manufacturing organizations.
Moreover, the incorporation of automation and robotics in production lines further enhanced the efficiency of MRP processes. Automated systems reduced the likelihood of human error, increased production speed, and ensured consistent product quality. The synergy between advanced technology and MRP principles enabled Japanese manufacturers to achieve unparalleled levels of productivity and reliability.
Advantages of Japan’s MRP Approach
Enhanced Efficiency and Productivity
Japan’s MRP methodologies focus on maximizing efficiency and productivity. By implementing JIT manufacturing, companies minimize excess inventory and reduce lead times. This approach ensures that materials are available precisely when needed, preventing production delays and lowering storage costs.
Furthermore, the use of automated systems and real-time data analytics allows for continuous monitoring and optimization of production processes. Manufacturers can quickly identify and address bottlenecks, adjust production schedules, and streamline operations to maintain optimal performance levels.
High-Quality Standards
Quality control is a cornerstone of Japanese manufacturing. MRP systems in Japan incorporate rigorous quality assurance processes to ensure that every component and finished product meets stringent standards. Techniques such as Total Quality Management (TQM) and Six Sigma are often integrated into MRP frameworks to systematically eliminate defects and enhance product reliability.
This unwavering commitment to quality not only satisfies customer expectations but also reduces costs associated with rework, returns, and warranty claims. High-quality products build trust and foster long-term relationships with customers, contributing to sustained business success.
Flexibility and Responsiveness
Japanese MRP systems are designed to be highly flexible and responsive to changes in market demand. Advanced forecasting tools and agile production planning enable manufacturers to adjust their operations swiftly in response to fluctuations in customer orders or market trends.
This adaptability is crucial in today’s dynamic business environment, where consumer preferences and external factors can change rapidly. By maintaining a flexible MRP system, Japanese manufacturers can maintain a competitive edge, swiftly capitalize on new opportunities, and mitigate risks associated with demand volatility.
Disadvantages and Challenges
High Initial Investment
Implementing advanced MRP systems, particularly those integrated with ERP and automation technologies, requires significant initial investment. Japanese manufacturers often allocate substantial resources to acquire the necessary software, hardware, and training. This financial commitment can be a barrier for smaller companies or those with limited capital.
Additionally, the ongoing costs associated with system maintenance, updates, and support can strain budgets over time. Balancing the benefits of advanced MRP systems with their associated costs is a critical consideration for manufacturers seeking to adopt Japan’s MRP practices.
Cultural and Organizational Changes
The successful implementation of Japan’s MRP systems often necessitates substantial cultural and organizational shifts within a company. Concepts such as continuous improvement (Kaizen) and employee empowerment require a departure from traditional hierarchical structures and rigid processes.
Organizations must foster a culture of collaboration, accountability, and adaptability to fully leverage the advantages of advanced MRP systems. This transition can be challenging, particularly in companies with deeply ingrained practices and resistance to change.
Dependence on Technology
While technology enhances the efficiency of MRP systems, it also introduces a level of dependence that can pose risks. Technical failures, cyber threats, or software glitches can disrupt production processes, leading to delays and increased operational costs.
Japanese manufacturers mitigate these risks by investing in robust cybersecurity measures, regular system maintenance, and comprehensive backup protocols. However, the reliance on technology underscores the importance of maintaining up-to-date systems and ensuring the resilience of MRP infrastructure.
Supplier Negotiation Techniques
Building Long-Term Relationships
Japanese suppliers emphasize the importance of building long-term, mutually beneficial relationships with their clients. This approach fosters trust, encourages collaboration, and enhances the reliability of supply chains. Manufacturers often engage in regular communication, share forecasts, and collaborate on demand planning to ensure alignment and coordination.
Long-term partnerships also allow for better negotiation outcomes, as suppliers are more invested in the success of their clients and are willing to offer favorable terms, such as volume discounts, flexible payment terms, and priority allocation of resources during high-demand periods.
Emphasis on Quality and Reliability
In negotiations, Japanese suppliers prioritize quality and reliability over price alone. They demonstrate their commitment to delivering high-quality materials by showcasing certifications, adhering to stringent quality standards, and providing consistent performance records.
Manufacturers negotiating with Japanese suppliers can expect a focus on value rather than cost-cutting. By prioritizing quality and reliability, both parties establish a foundation for long-term success and customer satisfaction.
Win-Win Negotiation Strategies
Japanese negotiation techniques often embody the principles of Win-Win strategies, where both parties seek to achieve mutually beneficial outcomes. This approach contrasts with competitive bargaining, which can lead to adversarial relationships and short-term gains at the expense of long-term collaboration.
Effective Win-Win negotiations involve understanding the needs and constraints of the supplier, finding common ground, and exploring innovative solutions that satisfy both parties. This collaborative approach enhances trust, reduces conflicts, and fosters sustainable business relationships.
Market Conditions in Japan
High Competition and Innovation
Japan’s manufacturing sector is characterized by intense competition and a relentless pursuit of innovation. Companies continuously strive to improve their processes, develop new technologies, and offer superior products to gain a competitive edge. This environment drives the evolution of MRP systems, as manufacturers seek to enhance efficiency, reduce costs, and maintain high-quality standards.
Stable Economic Environment
Japan’s stable economic environment provides a conducive backdrop for the development and refinement of advanced MRP systems. Consistent economic policies, a strong infrastructure, and a skilled workforce support the growth and sustainability of manufacturing enterprises.
Moreover, Japan’s commitment to research and development fosters technological advancements that can be integrated into MRP systems, ensuring that manufacturers remain at the forefront of industry innovations.
Global Supply Chain Integration
Japanese manufacturers are deeply integrated into global supply chains, sourcing materials and components from around the world to meet their production needs. This global integration necessitates sophisticated MRP systems capable of managing complex supply networks, tracking international shipments, and coordinating with diverse suppliers.
Effective management of global supply chains through advanced MRP systems allows Japanese manufacturers to optimize their operations, reduce lead times, and respond swiftly to global market changes.
Best Practices from Japanese MRP Systems
Adoption of Lean Manufacturing Principles
Lean manufacturing principles, which focus on eliminating waste and optimizing processes, are integral to Japan’s MRP systems. Manufacturers apply these principles to streamline operations, reduce inventory levels, and enhance overall efficiency.
Implementing lean practices involves continuous assessment and improvement of production processes, empowering employees to identify and address inefficiencies, and fostering a culture of excellence and accountability.
Continuous Improvement (Kaizen)
Kaizen, a Japanese philosophy of continuous improvement, is a fundamental aspect of MRP systems. Manufacturers adopt Kaizen to drive incremental enhancements in every aspect of their operations, from procurement and production to quality control and logistics.
By encouraging a mindset of perpetual learning and adaptation, Kaizen enables manufacturers to stay ahead of industry trends, respond to evolving customer needs, and maintain a competitive advantage.
Integrated Technology Solutions
Japanese manufacturers leverage integrated technology solutions to enhance the functionality and effectiveness of their MRP systems. This includes the use of ERP software, advanced data analytics, automation technologies, and Internet of Things (IoT) devices.
Integration of these technologies allows for seamless data flow across departments, real-time monitoring of production processes, predictive analytics for demand forecasting, and automated control of inventory levels. These capabilities empower manufacturers to make informed decisions, optimize resource allocation, and maintain high levels of operational efficiency.
Supplier Collaboration and Transparency
Effective collaboration with suppliers is a hallmark of Japanese MRP systems. Manufacturers work closely with their suppliers to share information, align on production schedules, and address potential issues proactively.
Transparency in communication and data sharing enhances trust, reduces misunderstandings, and ensures that all parties are aligned with the overall production goals. Collaborative relationships with suppliers contribute to a more resilient and responsive supply chain.
Focus on Employee Training and Development
Japanese manufacturers invest heavily in employee training and development to ensure that their workforce possesses the skills and knowledge necessary to operate advanced MRP systems. Continuous education programs, cross-functional training, and skill development initiatives empower employees to contribute effectively to the manufacturing process.
A well-trained workforce enhances the functionality of MRP systems by ensuring that data is accurately entered, processes are correctly followed, and systems are efficiently managed. Investing in employee development fosters a culture of excellence and supports the sustained success of manufacturing operations.
Implementing Japanese MRP Practices: A Step-by-Step Guide
Assessing Current MRP Systems
The first step in adopting Japanese MRP practices is to conduct a comprehensive assessment of existing MRP systems. This involves evaluating the current processes, identifying strengths and weaknesses, and determining areas for improvement.
Key aspects to assess include inventory management, production scheduling, procurement processes, supplier relationships, and the integration of technology. Understanding the current state provides a baseline for implementing changes and measuring progress.
Defining Clear Objectives and Goals
Establishing clear objectives and goals is essential for guiding the implementation of Japanese MRP practices. Goals may include reducing lead times, minimizing inventory levels, improving product quality, enhancing supplier collaboration, or increasing overall operational efficiency.
Defining specific, measurable, achievable, relevant, and time-bound (SMART) goals helps ensure that the implementation process is focused and aligns with the organization’s strategic priorities.
Investing in Technology and Infrastructure
To emulate Japan’s advanced MRP systems, manufacturers must invest in the necessary technology and infrastructure. This includes acquiring ERP software, implementing automation tools, integrating IoT devices, and ensuring robust cybersecurity measures.
Selecting the right technology solutions that align with the organization’s needs and capabilities is critical. Manufacturers should consider scalability, compatibility with existing systems, and the potential for future enhancements when making technology investments.
Training and Empowering Employees
Successful implementation of Japanese MRP practices requires a skilled and knowledgeable workforce. Organizations should provide comprehensive training programs to educate employees on new systems, processes, and best practices.
Empowering employees to take ownership of their roles and encouraging continuous learning fosters a culture of excellence and supports the effective utilization of MRP systems. Regular training updates and skill development initiatives ensure that the workforce remains proficient and adaptable.
Fostering Supplier Relationships
Building strong, collaborative relationships with suppliers is a critical component of Japan’s MRP systems. Manufacturers should engage in regular communication, share relevant data, and involve suppliers in the planning and forecasting processes.
Collaborative relationships enable better coordination, improved reliability, and increased flexibility within the supply chain. Engaging suppliers as partners rather than mere vendors enhances the overall efficiency and resilience of the manufacturing operations.
Implementing Continuous Improvement Processes
Adopting continuous improvement processes, such as Kaizen, ensures that MRP systems remain effective and responsive to changing conditions. Organizations should establish mechanisms for regularly reviewing performance, identifying areas for enhancement, and implementing necessary changes.
Encouraging feedback from employees, suppliers, and other stakeholders facilitates the identification of improvement opportunities and supports the ongoing optimization of MRP processes.
Monitoring and Evaluating Performance
Continuous monitoring and evaluation of MRP system performance are essential for measuring progress and ensuring that goals are being met. Key performance indicators (KPIs) should be established to track metrics such as lead times, inventory turnover, production efficiency, and quality levels.
Regular performance reviews enable organizations to identify successes, recognize areas for improvement, and make data-driven decisions to enhance the effectiveness of their MRP systems.
Case Studies: Success Stories from Japanese Manufacturers
Toyota Motor Corporation
Toyota is renowned for its implementation of the Toyota Production System (TPS), which integrates advanced MRP practices. The company’s emphasis on JIT manufacturing, Kanban systems, and continuous improvement has enabled it to achieve exceptional operational efficiency and product quality.
Toyota’s collaborative approach with suppliers, focus on employee training, and adoption of integrated technology solutions serve as a benchmark for other manufacturers seeking to emulate Japanese MRP success.
Panasonic Corporation
Panasonic has leveraged sophisticated ERP systems and advanced data analytics to optimize its MRP processes. By integrating real-time data from production lines, Panasonic ensures accurate demand forecasting, efficient inventory management, and seamless coordination across its global supply chain.
The company’s commitment to quality and innovation, combined with its effective supplier collaboration strategies, has contributed to its sustained success in the competitive electronics market.
Honda Motor Co., Ltd.
Honda’s approach to MRP involves a strong focus on flexibility and responsiveness. The company’s agile production planning systems allow it to quickly adapt to changes in market demand and customer preferences.
Honda’s investment in automation technologies and its collaborative relationships with suppliers enable it to maintain high levels of production efficiency and product quality, ensuring its competitiveness in the global automotive industry.
Overcoming Implementation Challenges
Managing Change Resistance
Implementing Japanese MRP practices often requires significant organizational changes, which can encounter resistance from employees. To address this challenge, management should communicate the benefits of the new systems, involve employees in the implementation process, and provide support and training to ease the transition.
Creating a shared vision and demonstrating the positive impact of MRP changes on the organization’s success can help mitigate resistance and foster a culture of acceptance and enthusiasm.
Ensuring Data Accuracy and Integrity
Accurate data is the foundation of effective MRP systems. Inaccurate or incomplete data can lead to flawed planning, inventory mismatches, and production delays. To ensure data accuracy, organizations should implement stringent data entry protocols, conduct regular audits, and invest in reliable data management tools.
Training employees on the importance of data integrity and establishing accountability measures reinforces the commitment to maintaining high-quality data standards.
Balancing Standardization and Flexibility
While standardization is essential for consistency and efficiency, excessive rigidity can impede flexibility and responsiveness. Japanese MRP systems strike a balance between standardized processes and the ability to adapt to changing conditions.
Organizations should establish standardized frameworks for core MRP processes while allowing for flexibility in areas that require adaptability. This balance enables manufacturers to maintain operational efficiency while remaining responsive to market dynamics.
Future Trends in MRP
Integration of Artificial Intelligence and Machine Learning
Artificial Intelligence (AI) and Machine Learning (ML) are poised to revolutionize MRP systems by enabling more accurate demand forecasting, predictive maintenance, and autonomous decision-making. These technologies can analyze vast amounts of data to identify patterns, optimize production schedules, and anticipate potential disruptions.
Japanese manufacturers are at the forefront of integrating AI and ML into their MRP systems, enhancing their ability to adapt to complex and dynamic market conditions.
Emphasis on Sustainability
Sustainability is becoming increasingly important in manufacturing, and MRP systems are evolving to support environmentally responsible practices. This includes optimizing resource utilization, reducing waste, and ensuring compliance with environmental regulations.
Japanese MRP systems are integrating sustainability metrics and green manufacturing principles, enabling manufacturers to minimize their environmental footprint while maintaining operational efficiency.
Rise of Blockchain for Supply Chain Transparency
Blockchain technology offers enhanced transparency and traceability in supply chains, which can be integrated into MRP systems to ensure the authenticity and origin of materials. This technology can help prevent counterfeit products, ensure compliance with ethical standards, and improve the reliability of supplier information.
Japanese manufacturers are exploring blockchain applications to enhance the security and transparency of their supply chains, reinforcing trust with customers and stakeholders.
Conclusion
Japan’s revolutionization of Material Requirements Planning has set a benchmark for manufacturing excellence worldwide. Through the integration of advanced technologies, lean manufacturing principles, and a steadfast commitment to quality and continuous improvement, Japanese manufacturers have developed MRP systems that are both efficient and resilient.
While there are challenges associated with adopting these practices, such as high initial investments and the need for cultural and organizational changes, the benefits of enhanced efficiency, high-quality standards, and flexibility make it a worthwhile endeavor. By learning from Japan’s best practices and adapting them to their unique contexts, manufacturers globally can optimize their MRP systems, strengthen supplier relationships, and achieve sustained operational success.
Embracing the future trends of AI, sustainability, and blockchain will further propel MRP systems into new realms of capability, ensuring that manufacturers remain competitive and responsive in an ever-evolving global marketplace. As Japan continues to lead in manufacturing innovation, its strategies and approaches to material requirements planning offer valuable insights for organizations seeking to master the complexities of modern production management.
資料ダウンロード
QCD調達購買管理クラウド「newji」は、調達購買部門で必要なQCD管理全てを備えた、現場特化型兼クラウド型の今世紀最高の購買管理システムとなります。
ユーザー登録
調達購買業務の効率化だけでなく、システムを導入することで、コスト削減や製品・資材のステータス可視化のほか、属人化していた購買情報の共有化による内部不正防止や統制にも役立ちます。
NEWJI DX
製造業に特化したデジタルトランスフォーメーション(DX)の実現を目指す請負開発型のコンサルティングサービスです。AI、iPaaS、および先端の技術を駆使して、製造プロセスの効率化、業務効率化、チームワーク強化、コスト削減、品質向上を実現します。このサービスは、製造業の課題を深く理解し、それに対する最適なデジタルソリューションを提供することで、企業が持続的な成長とイノベーションを達成できるようサポートします。
オンライン講座
製造業、主に購買・調達部門にお勤めの方々に向けた情報を配信しております。
新任の方やベテランの方、管理職を対象とした幅広いコンテンツをご用意しております。
お問い合わせ
コストダウンが利益に直結する術だと理解していても、なかなか前に進めることができない状況。そんな時は、newjiのコストダウン自動化機能で大きく利益貢献しよう!
(Β版非公開)