- お役立ち記事
- Mastering On-site EMC Testing: A Crucial Component in Japanese Manufacturing Excellence
Mastering On-site EMC Testing: A Crucial Component in Japanese Manufacturing Excellence
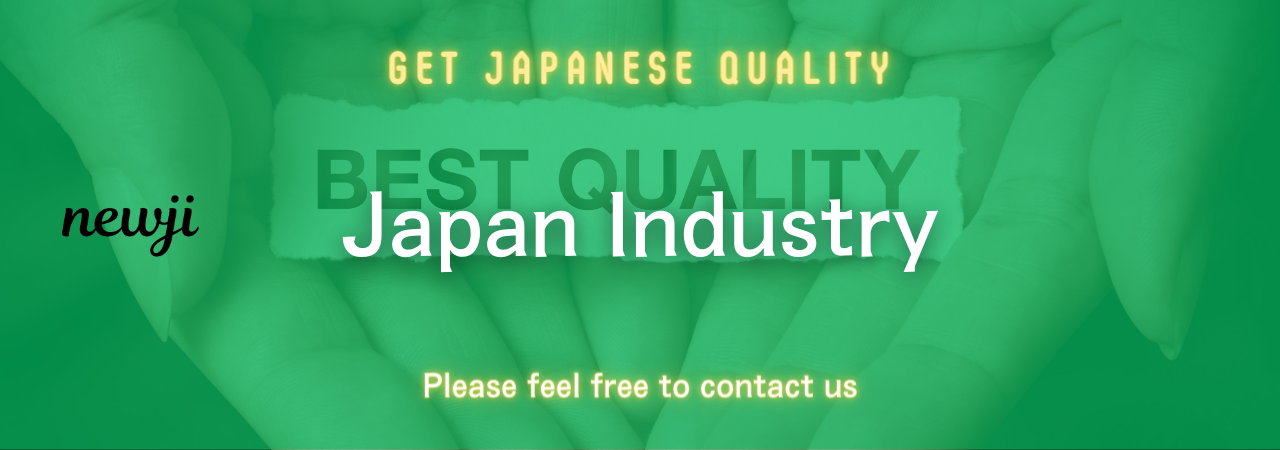
目次
Introduction to On-site EMC Testing in Japanese Manufacturing
Electromagnetic Compatibility (EMC) testing is a pivotal process in the manufacturing sector, ensuring that electronic devices operate without causing or succumbing to electromagnetic interference. In the realm of Japanese manufacturing, renowned for its precision and high standards, mastering on-site EMC testing is essential for maintaining excellence and competitive advantage. This article delves into the intricacies of on-site EMC testing, exploring its significance, practical applications, advantages and disadvantages, supplier negotiation techniques, market conditions, and best practices from the perspective of procurement and purchasing.
The Importance of EMC Testing in Manufacturing
EMC testing ensures that electronic devices are free from electromagnetic interference (EMI) and can coexist harmoniously within their operating environments. This is critical for:
Ensuring Compliance
Manufacturers must adhere to international and local EMC standards to enter various markets. Non-compliance can lead to product recalls, legal penalties, and reputational damage.
Enhancing Product Reliability
EMC testing verifies that products function reliably under electromagnetic disturbances, thereby reducing the likelihood of malfunctions in real-world applications.
Facilitating Innovation
Understanding EMC allows engineers to design more advanced and efficient products, fostering innovation and technological advancement.
Role of On-site Testing
On-site EMC testing involves evaluating products within the manufacturing facility rather than in external laboratories. This approach offers several advantages:
Immediate Feedback
Testing on-site allows for real-time adjustments and optimizations during the manufacturing process, reducing delays and enhancing efficiency.
Cost Efficiency
By integrating testing into the production line, manufacturers can save costs associated with outsourcing and repeated testing cycles.
Enhanced Collaboration
On-site testing fosters better communication between different departments, such as engineering, quality control, and procurement, leading to more cohesive and effective manufacturing processes.
Advantages of On-site EMC Testing
Integrating EMC testing within the manufacturing process offers numerous benefits:
Improved Quality Control
On-site testing ensures that each product meets quality standards before it leaves the facility, minimizing defects and returns.
Faster Time-to-Market
By streamlining the testing process, manufacturers can accelerate production timelines and bring products to market more swiftly.
Customization and Flexibility
On-site testing facilities can be tailored to specific manufacturing needs, allowing for greater flexibility in testing different products and configurations.
Cost Savings
Reducing reliance on external testing services can lead to significant cost savings, particularly for large-scale manufacturing operations.
Enhanced Problem-Solving
Immediate access to testing data enables quicker identification and resolution of manufacturing issues, improving overall operational efficiency.
Disadvantages of On-site EMC Testing
Despite its advantages, on-site EMC testing presents certain challenges:
High Initial Investment
Setting up an on-site EMC testing facility requires substantial upfront investment in equipment, training, and infrastructure.
Space Constraints
Dedicated testing areas consume valuable manufacturing space, which could otherwise be utilized for production activities.
Maintenance and Upkeep
Maintaining high-tech testing equipment necessitates ongoing maintenance and calibration to ensure accurate results, adding to operational costs.
Technical Expertise Required
Successful on-site EMC testing demands specialized knowledge and skills, necessitating continuous training and professional development for staff.
Supplier Negotiation Techniques for EMC Testing Services
Effective negotiation with suppliers is crucial for securing high-quality EMC testing services at competitive prices. Here are key strategies:
Understand Supplier Capabilities
Assess the technical expertise, equipment quality, and reliability of potential suppliers to ensure they can meet your EMC testing requirements.
Leverage Volume Discounts
Negotiate bulk testing rates if you have large-scale or ongoing testing needs, leveraging your purchasing power to secure better terms.
Build Long-term Relationships
Establishing strong, long-term relationships with suppliers can lead to more favorable pricing, priority service, and collaborative problem-solving.
Identify Alternative Suppliers
Having multiple supplier options enhances your bargaining position, allowing you to negotiate more effectively by demonstrating alternatives.
Clarify Contract Terms
Ensure that all aspects of the EMC testing services are clearly defined in contracts, including timelines, deliverables, pricing structures, and quality standards to prevent misunderstandings and disputes.
Market Conditions Affecting EMC Testing
Understanding the broader market conditions is essential for effective procurement and purchasing strategies in EMC testing:
Technological Advancements
Rapid advancements in electronics and communication technologies continually evolve EMC testing requirements, necessitating updated equipment and methodologies.
Regulatory Changes
Shifts in international and local EMC regulations can impact testing standards and practices, requiring manufacturers to stay informed and adaptable.
Global Supply Chain Dynamics
Global events, such as supply chain disruptions or geopolitical tensions, can affect the availability and cost of EMC testing equipment and services.
Competitive Landscape
Intense competition in the manufacturing sector drives the need for superior EMC testing capabilities to differentiate products and ensure market success.
Economic Factors
Economic fluctuations influence budgeting for EMC testing, with periods of economic growth allowing for more investment in quality control, while downturns may necessitate cost-cutting measures.
Best Practices for On-site EMC Testing
Implementing best practices in on-site EMC testing ensures optimal results and efficiency:
Establish Clear Testing Protocols
Develop and document standardized testing procedures to ensure consistency and reliability across all testing activities.
Invest in High-Quality Equipment
Utilize state-of-the-art EMC testing equipment to achieve accurate and comprehensive assessments of product compliance and performance.
Train and Certify Staff
Ensure that personnel involved in EMC testing receive thorough training and hold relevant certifications to maintain high testing standards.
Integrate Testing with Production
Seamlessly incorporate EMC testing into the manufacturing workflow to enhance efficiency and minimize production delays.
Continuous Improvement
Adopt a continuous improvement mindset by regularly reviewing and refining EMC testing processes based on feedback, technological advancements, and changing regulatory requirements.
Procurement Strategies for Effective EMC Testing
Effective procurement strategies are vital for acquiring the necessary resources and services for EMC testing:
Supplier Evaluation and Selection
Conduct comprehensive evaluations of potential EMC testing suppliers based on their technical capabilities, reliability, and cost-effectiveness.
Cost-Benefit Analysis
Assess the financial implications of various EMC testing options, weighing the costs against the benefits to determine the most economical and effective approach.
Strategic Sourcing
Adopt a strategic sourcing approach by identifying and partnering with key suppliers who align with your quality standards and business objectives.
Risk Management
Identify and mitigate potential risks associated with EMC testing procurement, such as supplier reliability, technological obsolescence, and regulatory compliance.
Contract Management
Effectively manage supplier contracts to ensure that all agreed-upon terms and conditions are met, and address any issues promptly to maintain a stable supply of EMC testing services.
Integrating EMC Testing with Quality Control Systems
Integrating EMC testing into broader quality control systems enhances overall product quality and reliability:
Holistic Quality Management
Incorporate EMC testing results into your quality management systems to provide a comprehensive view of product performance and compliance.
Data Integration
Synchronize EMC testing data with other quality metrics to facilitate data-driven decision-making and continuous improvement initiatives.
Cross-Functional Collaboration
Foster collaboration between engineering, quality control, procurement, and other departments to ensure that EMC considerations are integrated into all phases of product development and manufacturing.
Performance Monitoring
Regularly monitor and analyze EMC testing performance to identify trends, track improvements, and address any emerging issues promptly.
Future Trends in EMC Testing
Staying ahead of future trends in EMC testing is crucial for maintaining manufacturing excellence:
Automation and AI
The integration of automation and artificial intelligence in EMC testing can enhance efficiency, accuracy, and predictive maintenance capabilities.
Advanced Materials
Emerging materials with unique electromagnetic properties require innovative EMC testing methodologies to ensure proper compliance and performance.
Remote and Virtual Testing
Advancements in remote testing technologies enable more flexible and scalable EMC testing solutions, accommodating the evolving needs of global manufacturing operations.
Sustainability and Green Manufacturing
Sustainable manufacturing practices drive the need for EMC testing solutions that are energy-efficient and environmentally friendly, aligning with broader corporate social responsibility goals.
Customization and Flexibility
The future of EMC testing will likely see more customized and flexible testing solutions tailored to specific industry needs and technological advancements.
Conclusion
Mastering on-site EMC testing is a crucial component of Japanese manufacturing excellence, underpinning the high standards of quality, reliability, and innovation that define the industry. By understanding the importance of EMC testing, leveraging its advantages, navigating its challenges, and implementing best practices in procurement and quality control, manufacturers can enhance their competitive edge and ensure their products meet the rigorous standards of the global market.
Effective supplier negotiation, staying abreast of market conditions, and embracing future trends are essential strategies for maintaining excellence in EMC testing. As the manufacturing landscape continues to evolve, the integration of advanced EMC testing practices will remain a cornerstone of success, driving continuous improvement and fostering technological advancement in Japanese manufacturing.
資料ダウンロード
QCD調達購買管理クラウド「newji」は、調達購買部門で必要なQCD管理全てを備えた、現場特化型兼クラウド型の今世紀最高の購買管理システムとなります。
ユーザー登録
調達購買業務の効率化だけでなく、システムを導入することで、コスト削減や製品・資材のステータス可視化のほか、属人化していた購買情報の共有化による内部不正防止や統制にも役立ちます。
NEWJI DX
製造業に特化したデジタルトランスフォーメーション(DX)の実現を目指す請負開発型のコンサルティングサービスです。AI、iPaaS、および先端の技術を駆使して、製造プロセスの効率化、業務効率化、チームワーク強化、コスト削減、品質向上を実現します。このサービスは、製造業の課題を深く理解し、それに対する最適なデジタルソリューションを提供することで、企業が持続的な成長とイノベーションを達成できるようサポートします。
オンライン講座
製造業、主に購買・調達部門にお勤めの方々に向けた情報を配信しております。
新任の方やベテランの方、管理職を対象とした幅広いコンテンツをご用意しております。
お問い合わせ
コストダウンが利益に直結する術だと理解していても、なかなか前に進めることができない状況。そんな時は、newjiのコストダウン自動化機能で大きく利益貢献しよう!
(Β版非公開)