- お役立ち記事
- Mastering Precision: Exploring the Role of the Hand Riveter in Japanese Manufacturing
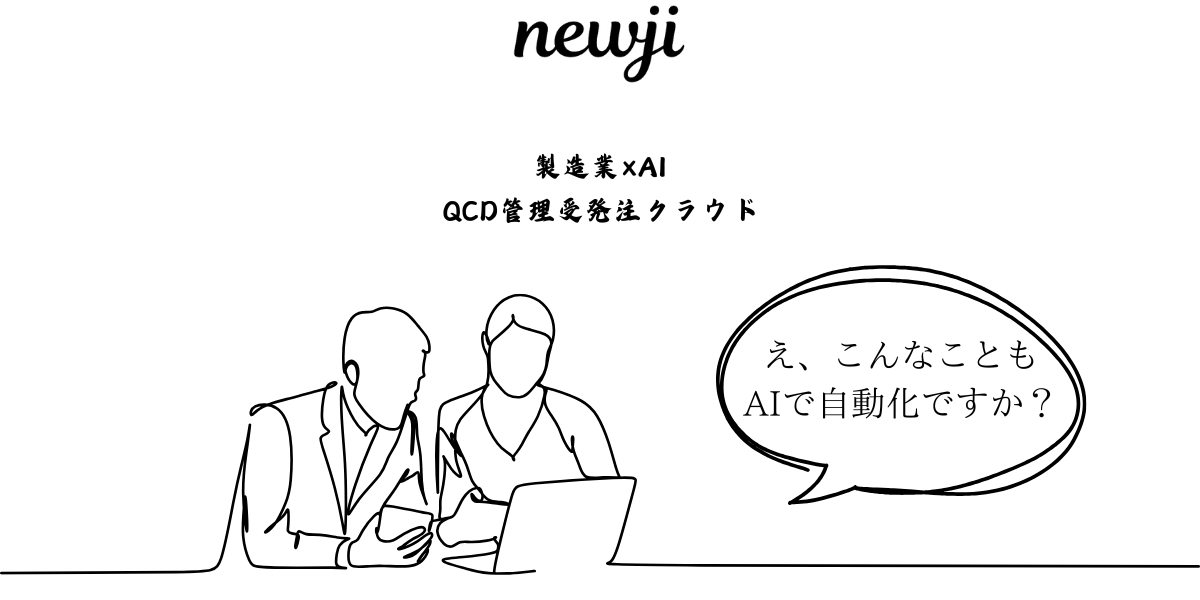
Mastering Precision: Exploring the Role of the Hand Riveter in Japanese Manufacturing
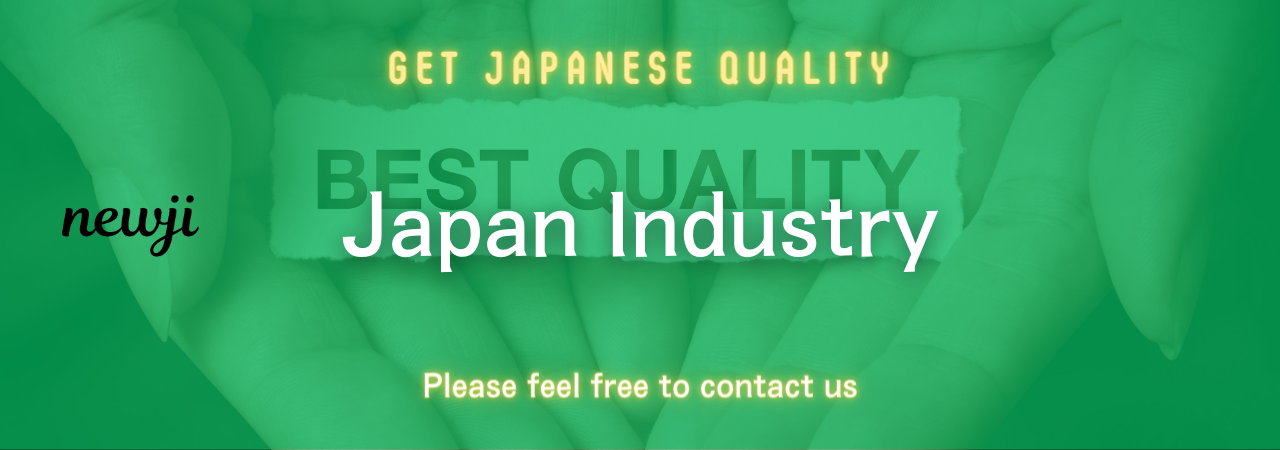
目次
Introduction to Hand Riveters in Japanese Manufacturing
Japanese manufacturing is renowned for its precision, efficiency, and quality. Central to achieving these standards is the utilization of specialized tools and equipment, among which the hand riveter plays a pivotal role. This article delves into the significance of hand riveters in Japanese manufacturing, exploring their functions, advantages, disadvantages, and best practices. Additionally, it provides insights into supplier negotiation techniques, market conditions, and practical content from the field perspective of procurement and purchasing.
The Role of Hand Riveters in Manufacturing Processes
Understanding Hand Riveting
Hand riveting is a manual fastening process where rivets are used to join two or more materials together. Unlike automated riveting systems, hand riveters require skilled operators to ensure precision and quality in the assembly process. This technique is especially prevalent in industries where bespoke and intricate assemblies are necessary, such as automotive, aerospace, and electronics manufacturing.
Applications in Japanese Manufacturing
In Japanese manufacturing, hand riveters are employed in various applications, including:
– **Automotive Assembly:** Hand riveting is used to attach panels, components, and structural elements in vehicle manufacturing.
– **Electronics Manufacturing:** Precise fastening of circuit boards and electronic components.
– **Aerospace Components:** Ensuring lightweight and strong assemblies through manual riveting techniques.
– **Consumer Goods:** Assembly of high-quality consumer products that require meticulous craftsmanship.
These applications highlight the versatility and necessity of hand riveters in maintaining the high standards expected in Japanese manufacturing.
Advantages of Using Hand Riveters
Precision and Control
One of the primary advantages of hand riveters is the level of precision and control they offer. Skilled operators can make minute adjustments, ensuring that each rivet is placed accurately, which is crucial for products that demand high quality and reliability.
Flexibility in Production
Hand riveters provide flexibility in manufacturing processes. They can be easily adapted to different tasks without the need for extensive retooling or programming, making them ideal for small batch productions or custom assemblies.
Cost-Effectiveness
For certain applications, especially those requiring low-volume production, hand riveters can be more cost-effective compared to automated riveting systems. The initial investment and maintenance costs are generally lower, making them accessible for various manufacturing scales.
Enhanced Quality Control
Manual riveting allows for real-time quality checks during the assembly process. Operators can identify and rectify issues immediately, ensuring that the final product meets stringent quality standards.
Disadvantages of Hand Riveters
Labor Intensive
Hand riveting is a labor-intensive process that requires skilled operators. This can lead to higher labor costs and dependency on human expertise, which may not always be scalable for large-scale productions.
Consistency Challenges
Maintaining consistency across all riveted joints can be challenging with manual processes. Variations in operator skill and technique can lead to inconsistencies in rivet placement and quality.
Limited Throughput
Compared to automated systems, hand riveters have a lower throughput rate. For high-volume manufacturing, this can become a bottleneck, potentially affecting overall production timelines and efficiency.
Ergonomic Issues
Repeated manual tasks can lead to operator fatigue and ergonomic issues, increasing the risk of errors and impacting overall productivity and job satisfaction.
Supplier Negotiation Techniques for Hand Riveters
Understanding Supplier Capabilities
Before entering negotiations, it is crucial to understand the supplier’s capabilities, including their production capacity, quality standards, and technological advancements. This knowledge provides leverage during negotiations and ensures that the supplier can meet your specific requirements.
Building Long-Term Relationships
In Japanese business culture, building strong, long-term relationships with suppliers is essential. Emphasizing mutual benefits and trust can lead to more favorable terms, better quality control, and reliable supply chains.
Leveraging Volume Discounts
Negotiating volume discounts can significantly reduce costs. By committing to larger orders, buyers can secure better pricing and terms, benefiting from economies of scale.
Quality Assurance Agreements
Establishing clear quality assurance agreements ensures that the supplier adheres to the required standards. This may include regular quality inspections, certifications, and adherence to industry-specific regulations.
Flexible Payment Terms
Negotiating flexible payment terms, such as extended credit periods or milestone-based payments, can improve cash flow management and reduce financial strain on the purchasing company.
Market Conditions Affecting Hand Riveter Procurement
Global Supply Chain Dynamics
Global supply chain disruptions can impact the availability and pricing of hand riveters. Factors such as geopolitical tensions, trade policies, and transportation bottlenecks can influence procurement strategies and supplier choices.
Technological Advancements
Advancements in manufacturing technology, including automation and robotics, affect the demand for manual tools like hand riveters. Staying abreast of technological trends ensures that procurement strategies align with industry developments.
Economic Factors
Economic fluctuations, including inflation rates, currency exchange rates, and overall economic growth, influence the cost and availability of hand riveters. Understanding these factors helps in making informed procurement decisions.
Environmental Regulations
Increasing environmental regulations may affect the materials and processes used in manufacturing hand riveters. Compliance with these regulations is essential, requiring procurement strategies to prioritize suppliers that adhere to sustainable practices.
Best Practices in Procuring Hand Riveters
Comprehensive Supplier Evaluation
Conduct thorough evaluations of potential suppliers, assessing their technical capabilities, quality standards, financial stability, and reputation in the market. This ensures the selection of reliable partners who can consistently meet your procurement needs.
Implementing Just-In-Time (JIT) Inventory
Adopting JIT inventory practices can reduce holding costs and minimize waste. Coordinating closely with suppliers to ensure timely deliveries aligns with production schedules, enhancing overall efficiency.
Continuous Improvement and Feedback
Establishing a continuous feedback loop with suppliers promotes ongoing improvements in quality, delivery, and service. Regularly reviewing performance metrics and addressing issues promptly fosters a culture of excellence.
Training and Development
Investing in training programs for operators ensures that they are proficient in using hand riveters, enhancing precision and reducing the likelihood of errors. Skilled operators contribute to higher quality and increased productivity.
Leveraging Technology for Procurement
Utilize procurement software and technologies to streamline the purchasing process, manage supplier relationships, and analyze market trends. Technology integration enhances decision-making and operational efficiency.
Quality Control in Hand Riveting
Establishing Robust Quality Standards
Define clear quality standards for hand riveting processes, including specifications for rivet types, materials, and placement precision. These standards serve as benchmarks for evaluating supplier performance and ensuring consistency.
Regular Inspections and Audits
Conduct regular inspections and audits of both the manufacturing processes and the suppliers. This proactive approach identifies potential issues early, allowing for timely corrective actions.
Employee Training and Certification
Ensure that operators are adequately trained and certified in hand riveting techniques. Skilled personnel are essential for maintaining high-quality outcomes and adhering to established standards.
Implementing Statistical Process Control (SPC)
Utilize SPC methods to monitor and control the hand riveting process. Analyzing process data helps in identifying variations and implementing measures to maintain consistent quality.
Supplier Quality Agreements
Develop comprehensive quality agreements with suppliers, outlining expectations, responsibilities, and corrective actions. These agreements formalize the commitment to quality and provide a framework for accountability.
Enhancing Factory Efficiency with Hand Riveters
Optimizing Workflows
Analyze and optimize workflows to ensure that hand riveting operations are seamlessly integrated into the overall production process. Streamlined workflows reduce bottlenecks and enhance productivity.
Ergonomic Tool Design
Select hand riveters designed with ergonomics in mind to minimize operator fatigue and reduce the risk of injuries. Comfortable tools improve efficiency and contribute to a safer working environment.
Maintenance and Calibration
Regular maintenance and calibration of hand riveters ensure their optimal performance and longevity. Scheduled upkeep prevents unexpected downtimes and maintains consistent quality.
Implementing Lean Manufacturing Principles
Adopting lean manufacturing principles, such as eliminating waste and continuously improving processes, enhances the efficiency of hand riveting operations. Lean practices contribute to cost savings and higher quality outputs.
Integrating Automation Where Possible
While hand riveting is inherently manual, integrating partial automation, such as tool holders or alignment aids, can enhance efficiency without compromising precision. This hybrid approach leverages the strengths of both manual and automated techniques.
Logistics Considerations in Hand Riveter Procurement
Supplier Location and Lead Times
Consider the geographical location of suppliers and the associated lead times for delivery. Proximity to manufacturing facilities can reduce transportation costs and lead times, contributing to more responsive supply chains.
Inventory Management
Implement effective inventory management strategies to balance the availability of hand riveters with the costs of holding inventory. Techniques such as economic order quantity (EOQ) and safety stock calculations can optimize inventory levels.
Shipping and Handling
Ensure that shipping and handling processes are efficient and that hand riveters are adequately protected during transit. Proper packaging and handling reduce the risk of damage and ensure timely delivery.
Customs and Import Regulations
Understand the customs and import regulations of the countries involved in the procurement process. Compliance with these regulations prevents delays and additional costs associated with non-compliance.
Risk Management
Identify and mitigate risks associated with logistics, such as transportation disruptions, supplier reliability, and geopolitical factors. Developing contingency plans enhances resilience in the supply chain.
Production Engineering and Hand Riveters
Design for Manufacturability
Incorporate hand riveting considerations into the design phase to ensure that products are easily assembled using manual techniques. Design for manufacturability reduces assembly time and enhances the feasibility of using hand riveters.
Tool Selection and Compatibility
Select hand riveters that are compatible with the materials and rivet types used in production. Proper tool selection ensures efficient assembly and maintains product integrity.
Process Optimization
Continuously analyze and optimize hand riveting processes to improve speed, accuracy, and quality. Process optimization contributes to higher production rates and reduces the likelihood of defects.
Integration with Other Assembly Processes
Ensure that hand riveting operations are seamlessly integrated with other assembly processes, such as welding, fastening, and surface finishing. Integration enhances overall production flow and efficiency.
Feedback Mechanisms
Establish feedback mechanisms between production engineering and operators to identify and address issues in real-time. This collaboration fosters continuous improvement and innovation in hand riveting techniques.
Automation and the Future of Hand Riveting
Hybrid Assembly Systems
The future of hand riveting lies in hybrid assembly systems that combine manual and automated processes. These systems leverage the precision of automation with the flexibility of manual operations, enhancing overall efficiency.
Robotic Assistance
Integrating robotic assistance in hand riveting can improve consistency and reduce operator fatigue. Robots can handle repetitive tasks, allowing operators to focus on precision and quality control.
Smart Tools and IoT Integration
Smart hand riveters equipped with sensors and connected to the Internet of Things (IoT) can provide real-time data on usage, performance, and maintenance needs. This data-driven approach enhances tool management and operational efficiency.
Augmented Reality (AR) for Training
Utilizing augmented reality for training operators can accelerate the learning process and improve skill levels. AR applications provide interactive and immersive training experiences, enhancing proficiency in hand riveting techniques.
Sustainable Practices
Future developments in hand riveting will likely focus on sustainability, including the use of eco-friendly materials and energy-efficient processes. Emphasizing sustainability aligns with global trends and regulatory requirements.
Conclusion
Hand riveters continue to play a crucial role in Japanese manufacturing, underpinning the precision and quality that the industry is known for. While the manual nature of hand riveting presents certain challenges, such as labor intensity and consistency issues, the advantages of flexibility, control, and cost-effectiveness make it an indispensable tool in various manufacturing applications.
Effective procurement and purchasing strategies, including supplier negotiation techniques and comprehensive quality control measures, are essential in optimizing the use of hand riveters. Understanding market conditions and implementing best practices in inventory management, logistics, and production engineering further enhance factory efficiency and product quality.
As technology advances, the integration of automation and smart tools with traditional hand riveting methods will shape the future of this essential manufacturing process. Embracing these innovations while maintaining the core principles of precision and craftsmanship will ensure that hand riveters remain a vital component of Japanese manufacturing excellence.
資料ダウンロード
QCD調達購買管理クラウド「newji」は、調達購買部門で必要なQCD管理全てを備えた、現場特化型兼クラウド型の今世紀最高の購買管理システムとなります。
ユーザー登録
調達購買業務の効率化だけでなく、システムを導入することで、コスト削減や製品・資材のステータス可視化のほか、属人化していた購買情報の共有化による内部不正防止や統制にも役立ちます。
NEWJI DX
製造業に特化したデジタルトランスフォーメーション(DX)の実現を目指す請負開発型のコンサルティングサービスです。AI、iPaaS、および先端の技術を駆使して、製造プロセスの効率化、業務効率化、チームワーク強化、コスト削減、品質向上を実現します。このサービスは、製造業の課題を深く理解し、それに対する最適なデジタルソリューションを提供することで、企業が持続的な成長とイノベーションを達成できるようサポートします。
オンライン講座
製造業、主に購買・調達部門にお勤めの方々に向けた情報を配信しております。
新任の方やベテランの方、管理職を対象とした幅広いコンテンツをご用意しております。
お問い合わせ
コストダウンが利益に直結する術だと理解していても、なかなか前に進めることができない状況。そんな時は、newjiのコストダウン自動化機能で大きく利益貢献しよう!
(Β版非公開)