- お役立ち記事
- Mastering Precision: How Error Correction Shapes the Future of Japanese Manufacturing
月間77,185名の
製造業ご担当者様が閲覧しています*
*2025年2月28日現在のGoogle Analyticsのデータより
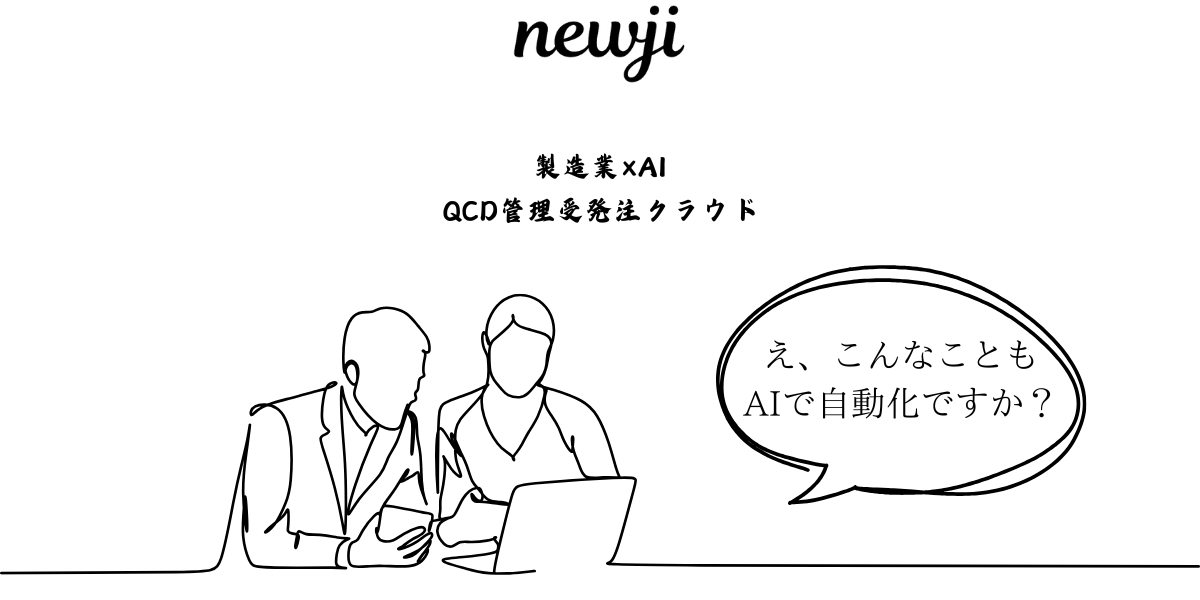
Mastering Precision: How Error Correction Shapes the Future of Japanese Manufacturing
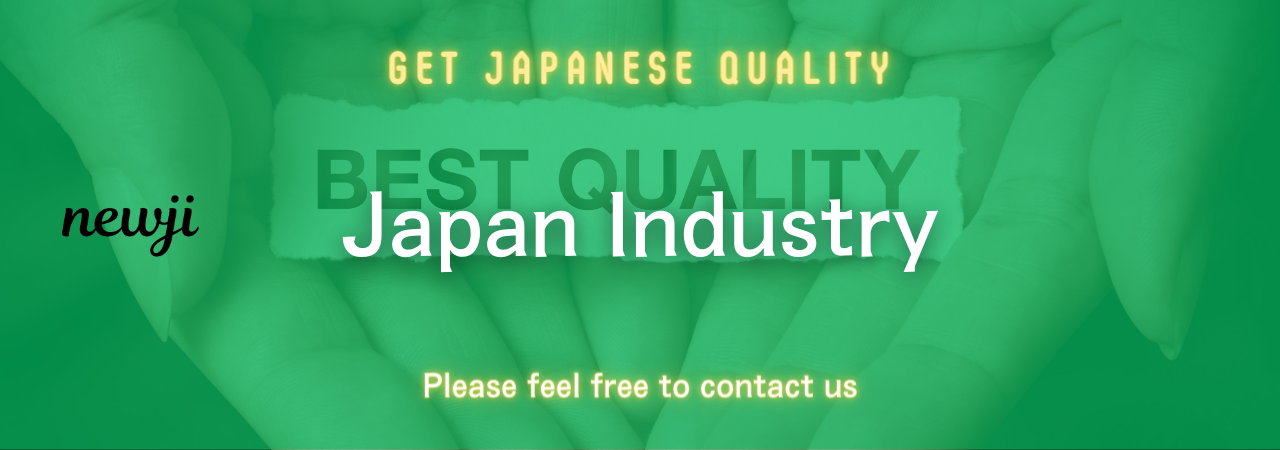
目次
Introduction to Precision in Japanese Manufacturing
Precision is the cornerstone of Japanese manufacturing, renowned worldwide for its meticulous attention to detail and unwavering commitment to quality.
The concept of precision extends beyond mere accuracy; it embodies a holistic approach to production that integrates various facets of the manufacturing process.
From procurement and purchasing to production management and quality control, every step is finely tuned to achieve optimal efficiency and excellence.
This dedication to precision not only enhances the quality of products but also drives innovation and shapes the future of manufacturing on a global scale.
The Role of Error Correction in Enhancing Manufacturing Quality
Error correction is a critical component in the manufacturing process, serving as a mechanism to identify and rectify deviations from desired standards.
In Japanese manufacturing, the emphasis on error correction is deeply ingrained in the organizational culture, ensuring that mistakes are addressed promptly and effectively.
This proactive approach mitigates the risk of defects, minimizes waste, and maintains the integrity of the production process.
By systematically analyzing errors and implementing corrective actions, manufacturers can continuously improve their processes and deliver superior products to the market.
Continuous Improvement through Kaizen
One of the foundational principles supporting error correction in Japanese manufacturing is Kaizen, or continuous improvement.
Kaizen encourages a culture where employees at all levels are actively involved in identifying areas for improvement and implementing solutions.
This collective effort fosters an environment where errors are not only corrected but also analyzed to prevent recurrence.
Through regular Kaizen activities, manufacturers can achieve incremental advancements that cumulatively lead to significant enhancements in quality and efficiency.
Implementation of Six Sigma Methodology
Another pivotal methodology utilized in error correction is Six Sigma, which focuses on eliminating defects and reducing variability in processes.
Japanese manufacturers adopt Six Sigma techniques to rigorously analyze production data, identify root causes of errors, and implement data-driven solutions.
The structured approach of Six Sigma ensures that error correction is not a one-time fix but a sustainable practice that contributes to long-term excellence.
Procurement and Purchasing Strategies in Japanese Manufacturing
Effective procurement and purchasing are essential for maintaining the high standards of precision in Japanese manufacturing.
These strategies ensure that manufacturers source the best materials and components, fostering strong relationships with suppliers and optimizing the supply chain.
Supplier Selection and Evaluation
Selecting the right suppliers is a critical aspect of procurement, as it directly impacts the quality and reliability of the final product.
Japanese manufacturers employ stringent criteria to evaluate potential suppliers, focusing on factors such as quality standards, delivery performance, financial stability, and technological capabilities.
Regular assessments and audits are conducted to ensure that suppliers adhere to the established standards, fostering trust and collaboration.
Building Long-Term Supplier Relationships
Long-term partnerships with suppliers are a hallmark of Japanese procurement practices.
By cultivating strong, enduring relationships, manufacturers can ensure consistent quality, secure favorable terms, and facilitate seamless communication.
These partnerships also encourage mutual growth, as suppliers are more invested in the success of their clients and are motivated to innovate and improve their offerings.
Advantages of Japanese Precision Manufacturing
The precision-focused approach of Japanese manufacturing offers numerous advantages that contribute to its global reputation for excellence.
High Quality and Reliability
Japanese manufacturers are renowned for producing high-quality and reliable products that meet stringent industry standards.
The emphasis on precision and error correction ensures that products are free from defects and perform consistently over their lifecycle.
This reliability builds consumer trust and enhances brand reputation, providing a competitive edge in the market.
Operational Efficiency
Precision in manufacturing translates to optimized operations, reducing waste, minimizing downtime, and maximizing productivity.
Efficient processes lower production costs and enable manufacturers to respond swiftly to market demands and changes.
This operational excellence allows Japanese manufacturers to maintain profitability while delivering superior products.
Innovation and Technological Advancement
The focus on precision drives continuous innovation and the adoption of advanced technologies.
Japanese manufacturers invest heavily in research and development, integrating cutting-edge technologies such as automation, robotics, and artificial intelligence into their production processes.
These innovations not only enhance precision but also lead to the development of new products and solutions that address evolving market needs.
Challenges in Maintaining Precision
While the precision-focused approach offers significant benefits, it also presents challenges that manufacturers must navigate to sustain their standards.
High Initial Investment
Achieving and maintaining high precision levels often require substantial initial investments in technology, training, and quality control systems.
These costs can be a barrier for smaller manufacturers or those operating in highly competitive markets with tight profit margins.
Balancing the need for precision with financial constraints is a critical challenge that requires strategic planning and efficient resource allocation.
Supply Chain Complexity
Managing a complex supply chain with multiple suppliers and components increases the risk of errors and disruptions.
Ensuring that all suppliers adhere to the same quality standards and maintaining seamless coordination can be demanding.
Manufacturers must implement robust supply chain management practices and leverage technology to monitor and control the entire supply chain effectively.
Skilled Workforce Requirements
Precision manufacturing demands a highly skilled and dedicated workforce capable of operating advanced machinery and adhering to strict quality protocols.
Recruiting, training, and retaining such talent can be challenging, particularly in industries experiencing labor shortages.
Investing in employee development and fostering a culture of continuous learning are essential to overcoming this hurdle.
Supplier Negotiation Techniques in Japanese Procurement
Effective negotiation with suppliers is pivotal to securing favorable terms and ensuring the consistent quality of materials and components.
Building Mutual Trust and Respect
Japanese procurement emphasizes building relationships based on trust and respect. Establishing mutual trust facilitates open communication and collaboration, making negotiations more constructive and less adversarial.
This approach often involves long-term commitment and understanding, which can lead to more favorable terms and cooperation during challenging times.
Value-Oriented Negotiation
Rather than focusing solely on price, Japanese procurement practices prioritize value creation.
Negotiations aim to achieve a balance between cost, quality, and delivery, ensuring that both parties benefit from the agreement.
This holistic approach fosters sustainable partnerships and encourages suppliers to continuously improve their offerings.
Leveraging Transparency and Open Communication
Transparent communication is integral to successful negotiations. Clearly articulating expectations, requirements, and constraints helps in aligning objectives and mitigating misunderstandings.
By maintaining openness, manufacturers and suppliers can work together to address challenges and find mutually beneficial solutions.
Market Conditions Impacting Japanese Manufacturing
Various market conditions influence the dynamics of Japanese manufacturing, shaping strategies and operations to maintain precision and competitiveness.
Globalization and Competition
The increasing globalization of markets has intensified competition, requiring Japanese manufacturers to continuously innovate and enhance precision to differentiate themselves.
Adapting to diverse customer needs and expanding into new markets necessitates flexibility and responsiveness, ensuring that quality standards are upheld across different regions.
Technological Advancements
Rapid technological advancements present both opportunities and challenges. Embracing new technologies can enhance precision and efficiency but also requires significant investment and adaptation.
Japanese manufacturers must stay abreast of technological trends and integrate relevant innovations to maintain their competitive edge.
Economic Fluctuations
Economic conditions, such as fluctuations in currency exchange rates and changes in consumer demand, impact manufacturing operations.
Japanese manufacturers must develop resilient strategies to navigate economic uncertainties, ensuring stability in production, procurement, and sales.
Best Practices for Achieving Precision in Manufacturing
To excel in precision manufacturing, Japanese companies adopt a set of best practices that enhance quality, efficiency, and innovation.
Implementing Total Quality Management (TQM)
Total Quality Management involves a comprehensive approach to quality, integrating all organizational processes and stakeholders.
By embedding quality into every aspect of the manufacturing process, TQM ensures that precision is a collective responsibility, leading to consistent excellence.
Utilizing Advanced Manufacturing Technologies
Investing in advanced technologies such as automation, robotics, and data analytics enables manufacturers to achieve higher precision and efficiency.
These technologies facilitate real-time monitoring, predictive maintenance, and streamlined operations, contributing to overall productivity and quality.
Fostering a Culture of Continuous Learning
A dedicated workforce is essential for maintaining precision. Encouraging continuous learning and professional development ensures that employees are skilled and knowledgeable.
Training programs, workshops, and collaborative projects foster innovation and adaptability, empowering employees to contribute effectively to precision manufacturing goals.
Enhancing Supply Chain Visibility
Achieving transparency and visibility across the supply chain allows manufacturers to monitor and control every aspect of procurement, production, and distribution.
Leveraging technologies such as blockchain and Internet of Things (IoT) can enhance traceability, reduce errors, and improve coordination with suppliers, ensuring that precision is maintained throughout the supply chain.
The Future of Precision in Japanese Manufacturing
As the manufacturing landscape evolves, the role of precision and error correction continues to be pivotal in shaping the future of Japanese industries.
Integration of Artificial Intelligence and Machine Learning
Artificial Intelligence (AI) and Machine Learning (ML) are set to revolutionize precision manufacturing by enabling predictive analytics, autonomous quality control, and intelligent decision-making.
These technologies can identify patterns, forecast potential errors, and optimize processes, further enhancing accuracy and efficiency.
Sustainable Manufacturing Practices
Sustainability is becoming increasingly important, and precision manufacturing plays a key role in minimizing waste and reducing environmental impact.
Japanese manufacturers are adopting eco-friendly practices and sustainable materials, aligning precision with environmental responsibility to meet evolving consumer and regulatory demands.
Customized and Flexible Production
The demand for customized products requires manufacturers to adopt flexible production systems that maintain precision while accommodating variations.
Advanced technologies such as additive manufacturing and flexible automation allow for high precision in small-batch and customized production, catering to diverse market needs.
Global Collaboration and Innovation Ecosystems
Collaborating with global partners and participating in innovation ecosystems can accelerate advancements in precision manufacturing.
Sharing knowledge, resources, and expertise enables manufacturers to harness collective strengths, fostering innovation and maintaining leadership in precision manufacturing on the global stage.
Conclusion
Precision and error correction are fundamental to the success and future of Japanese manufacturing.
Through meticulous procurement and purchasing strategies, robust quality control measures, and the adoption of advanced technologies, Japanese manufacturers continue to set global standards for excellence.
While challenges such as high initial investments and supply chain complexities persist, the unwavering commitment to precision ensures that Japanese manufacturing remains resilient, innovative, and competitive.
As the industry evolves, the integration of AI, sustainable practices, and flexible production systems will further solidify Japan’s position as a leader in precision manufacturing, shaping the future of the global manufacturing landscape.
資料ダウンロード
QCD管理受発注クラウド「newji」は、受発注部門で必要なQCD管理全てを備えた、現場特化型兼クラウド型の今世紀最高の受発注管理システムとなります。
ユーザー登録
受発注業務の効率化だけでなく、システムを導入することで、コスト削減や製品・資材のステータス可視化のほか、属人化していた受発注情報の共有化による内部不正防止や統制にも役立ちます。
NEWJI DX
製造業に特化したデジタルトランスフォーメーション(DX)の実現を目指す請負開発型のコンサルティングサービスです。AI、iPaaS、および先端の技術を駆使して、製造プロセスの効率化、業務効率化、チームワーク強化、コスト削減、品質向上を実現します。このサービスは、製造業の課題を深く理解し、それに対する最適なデジタルソリューションを提供することで、企業が持続的な成長とイノベーションを達成できるようサポートします。
製造業ニュース解説
製造業、主に購買・調達部門にお勤めの方々に向けた情報を配信しております。
新任の方やベテランの方、管理職を対象とした幅広いコンテンツをご用意しております。
お問い合わせ
コストダウンが利益に直結する術だと理解していても、なかなか前に進めることができない状況。そんな時は、newjiのコストダウン自動化機能で大きく利益貢献しよう!
(β版非公開)