- お役立ち記事
- Mastering Precision: How Japanese Manufacturing Excels at the Art of Tapping
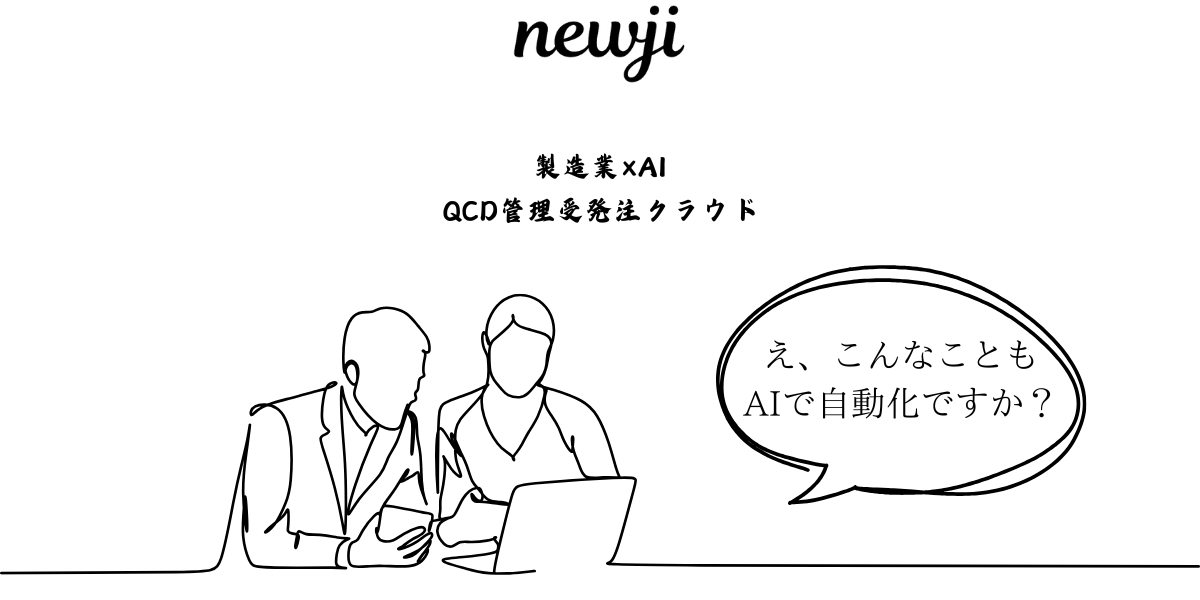
Mastering Precision: How Japanese Manufacturing Excels at the Art of Tapping
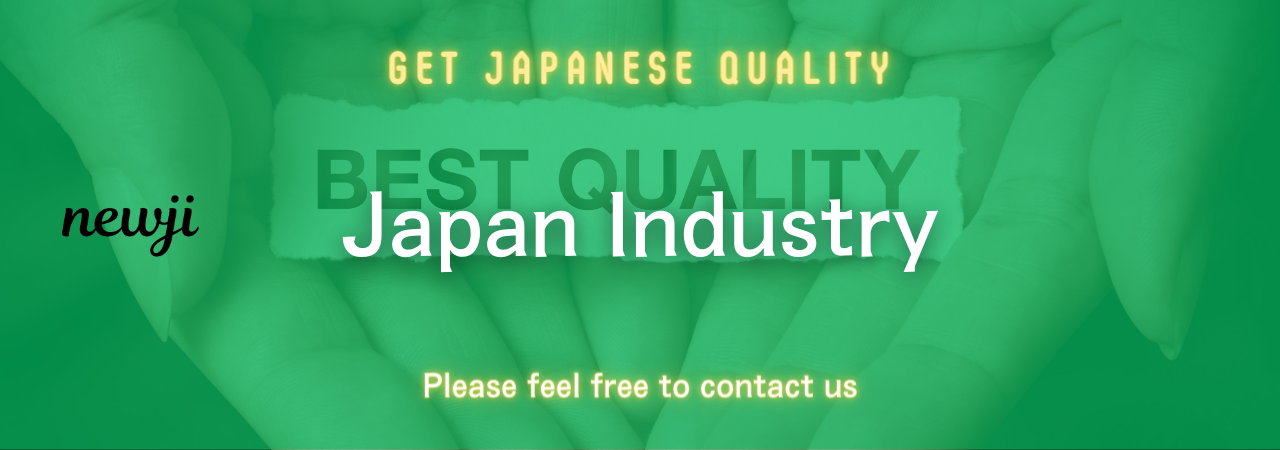
目次
Understanding the Art of Tapping in Japanese Manufacturing
Tapping is a critical process in manufacturing, involving the creation of internal threads in a material. Japanese manufacturing has perfected this art, setting standards for precision and efficiency. This mastery stems from a combination of advanced technology, skilled craftsmanship, and rigorous quality control. Understanding how Japanese manufacturers excel in tapping provides valuable insights for procurement and purchasing professionals seeking to leverage these capabilities.
Advantages of Japanese Tapping Techniques
Precision and Consistency
Japanese manufacturers prioritize precision in every aspect of tapping. Advanced machinery and meticulous processes ensure consistent thread quality across batches. This level of precision reduces the likelihood of defects, enhancing the overall reliability of the manufactured components.
Advanced Technology Integration
The integration of cutting-edge technology, such as Computer Numerical Control (CNC) machines and automation systems, allows for high-speed and high-accuracy tapping operations. These technologies enable manufacturers to maintain tight tolerances and adapt quickly to changing production requirements.
Skilled Workforce
Japan places a strong emphasis on workforce training and development. Skilled technicians and engineers bring a deep understanding of tapping techniques, enabling them to troubleshoot issues and optimize processes effectively. This expertise contributes significantly to the high standards of Japanese manufacturing.
Quality Control and Continuous Improvement
Japanese manufacturing principles, such as Kaizen (continuous improvement) and Total Quality Management (TQM), ensure that tapping processes are continuously evaluated and refined. Rigorous quality control measures are implemented at every stage, from material selection to final inspection, guaranteeing superior product quality.
Disadvantages and Challenges
Higher Production Costs
The advanced technologies and skilled labor required for precision tapping can result in higher production costs. While the quality benefits are substantial, companies may face increased expenses compared to manufacturers using less sophisticated processes.
Longer Lead Times
Achieving the highest levels of precision often requires longer production times. In industries where speed is critical, this can be a disadvantage. Balancing quality and efficiency remains a key challenge for Japanese manufacturers.
Complex Supply Chains
Japanese manufacturing often involves intricate supply chains with multiple suppliers and stringent quality requirements. Managing these complex networks can be challenging, especially in times of global disruptions or supply shortages.
Supplier Negotiation Techniques
Building Long-Term Relationships
Japanese suppliers value long-term partnerships over short-term gains. Establishing trust and demonstrating commitment can lead to more favorable terms and collaborative problem-solving. Procurement professionals should focus on fostering strong, enduring relationships with suppliers.
Transparent Communication
Open and honest communication is essential in negotiations. Clearly articulating expectations, requirements, and potential challenges helps build mutual understanding and facilitates smoother negotiations. Japanese suppliers appreciate transparency and responsiveness from their partners.
Leveraging Quality Standards
Highlighting adherence to stringent quality standards can be a strong negotiating point. Japanese manufacturers take pride in their quality certifications and processes, and emphasizing the mutual benefits of maintaining high standards can lead to better negotiation outcomes.
Flexibility and Adaptability
Being flexible in negotiations, such as being willing to adjust order volumes or delivery schedules, can enhance the relationship with Japanese suppliers. Demonstrating adaptability shows respect for the supplier’s capabilities and constraints, fostering a more collaborative partnership.
Market Conditions and Trends
Globalized Supply Chains
Japanese manufacturing operates within highly globalized supply chains, which can be both an advantage and a vulnerability. Understanding the dynamics of these global networks is crucial for procurement professionals to navigate potential disruptions and optimize sourcing strategies.
Technological Advancements
Continuous technological innovation is a hallmark of Japanese manufacturing. Staying abreast of advancements in tapping technology and related fields enables companies to maintain a competitive edge and meet evolving market demands.
Sustainability and Environmental Regulations
Increasing emphasis on sustainability and environmental responsibility is shaping manufacturing practices. Japanese manufacturers are at the forefront of implementing eco-friendly processes and materials, aligning with global trends towards sustainability.
Economic Fluctuations
Economic conditions, both domestic and international, impact manufacturing activities. Understanding how economic fluctuations affect Japanese suppliers can inform more resilient procurement strategies and risk management practices.
Best Practices in Procurement and Purchasing
Comprehensive Supplier Evaluation
Conduct thorough evaluations of potential Japanese suppliers, considering factors such as their technological capabilities, quality control measures, financial stability, and compliance with industry standards. This ensures the selection of reliable partners capable of meeting your manufacturing needs.
Collaborative Planning
Engage in joint planning efforts with suppliers to align production schedules, forecast demand, and identify opportunities for process improvements. Collaborative planning fosters a more synchronized and efficient supply chain.
Investing in Technology Integration
Leverage technology to enhance procurement processes. Implementing digital tools for supplier management, order tracking, and quality assurance can streamline operations and improve communication with Japanese manufacturers.
Fostering Continuous Improvement
Adopt a continuous improvement mindset in procurement practices. Regularly review and refine purchasing strategies, seek feedback from suppliers, and stay updated on industry best practices to drive ongoing enhancements in supply chain performance.
Implementing Japanese Tapping Techniques in Your Operations
Assessing Your Current Capabilities
Evaluate your existing tapping processes and identify areas where Japanese techniques could enhance precision and efficiency. Understanding your starting point is essential for successful integration of new methodologies.
Investing in Training and Development
Provide training for your workforce to develop the skills necessary for advanced tapping techniques. Investing in education and professional development ensures your team can effectively implement and maintain high-precision processes.
Adopting Advanced Machinery and Tools
Upgrade your manufacturing equipment to incorporate the latest tapping technologies used by Japanese manufacturers. High-precision machinery and automated systems can significantly improve the accuracy and consistency of your tapping operations.
Implementing Rigorous Quality Controls
Establish stringent quality control protocols to monitor and maintain thread precision. Regular inspections, testing, and adherence to quality standards are critical for achieving the desired level of manufacturing excellence.
Case Studies: Success Stories from Japanese Manufacturing
Toyota’s Precision Manufacturing
Toyota exemplifies the application of precise tapping techniques in automotive manufacturing. By integrating advanced technology and fostering a culture of continuous improvement, Toyota ensures high-quality thread formations that contribute to the overall durability and performance of their vehicles.
Panasonic’s Electronics Excellence
Panasonic utilizes precise tapping in the production of electronic components. Their commitment to precision ensures reliable connections and long-lasting performance in their electronic devices, reinforcing their reputation for quality and innovation.
Hitachi’s Industrial Solutions
Hitachi applies precise tapping in their industrial machinery manufacturing. The accuracy of thread creation in their products ensures seamless assembly and operation, highlighting the importance of precision in industrial applications.
Future Outlook: The Evolution of Tapping in Japanese Manufacturing
Integration of Artificial Intelligence
The future of tapping in Japanese manufacturing will likely see greater integration of artificial intelligence (AI) and machine learning. These technologies can optimize tapping processes, predict maintenance needs, and enhance overall operational efficiency.
Sustainable Manufacturing Practices
As sustainability becomes increasingly important, Japanese manufacturers are expected to adopt more eco-friendly tapping processes. This includes using sustainable materials, reducing waste, and implementing energy-efficient technologies.
Global Collaboration and Innovation
Continued global collaboration will drive innovation in tapping techniques. By partnering with international experts and embracing diverse perspectives, Japanese manufacturers can push the boundaries of precision and efficiency even further.
Conclusion
Japanese manufacturing’s excellence in the art of tapping is a testament to their commitment to precision, quality, and continuous improvement. For procurement and purchasing professionals, understanding and leveraging these advanced techniques can lead to significant benefits in terms of product quality, reliability, and operational efficiency. By adopting best practices, fostering strong supplier relationships, and staying attuned to market trends, companies can harness the strengths of Japanese manufacturing to enhance their own operations and achieve sustained success in the global marketplace.
資料ダウンロード
QCD調達購買管理クラウド「newji」は、調達購買部門で必要なQCD管理全てを備えた、現場特化型兼クラウド型の今世紀最高の購買管理システムとなります。
ユーザー登録
調達購買業務の効率化だけでなく、システムを導入することで、コスト削減や製品・資材のステータス可視化のほか、属人化していた購買情報の共有化による内部不正防止や統制にも役立ちます。
NEWJI DX
製造業に特化したデジタルトランスフォーメーション(DX)の実現を目指す請負開発型のコンサルティングサービスです。AI、iPaaS、および先端の技術を駆使して、製造プロセスの効率化、業務効率化、チームワーク強化、コスト削減、品質向上を実現します。このサービスは、製造業の課題を深く理解し、それに対する最適なデジタルソリューションを提供することで、企業が持続的な成長とイノベーションを達成できるようサポートします。
オンライン講座
製造業、主に購買・調達部門にお勤めの方々に向けた情報を配信しております。
新任の方やベテランの方、管理職を対象とした幅広いコンテンツをご用意しております。
お問い合わせ
コストダウンが利益に直結する術だと理解していても、なかなか前に進めることができない状況。そんな時は、newjiのコストダウン自動化機能で大きく利益貢献しよう!
(Β版非公開)