- お役立ち記事
- Mastering Precision: How Japanese Manufacturing Leads the Way in Analog Circuit Innovation
月間77,185名の
製造業ご担当者様が閲覧しています*
*2025年2月28日現在のGoogle Analyticsのデータより
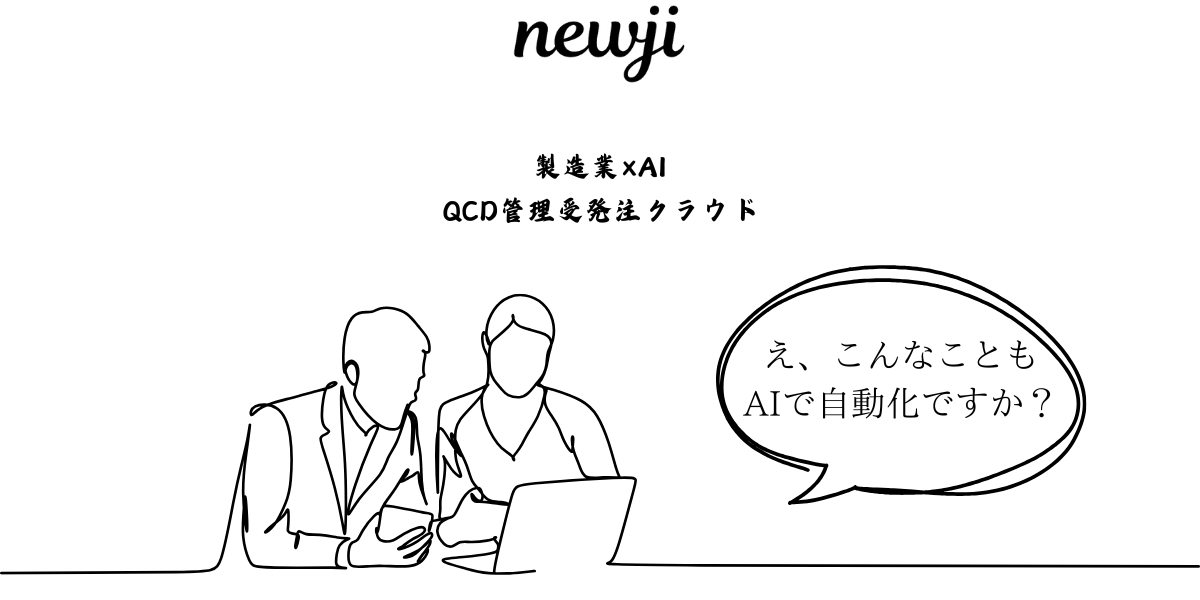
Mastering Precision: How Japanese Manufacturing Leads the Way in Analog Circuit Innovation
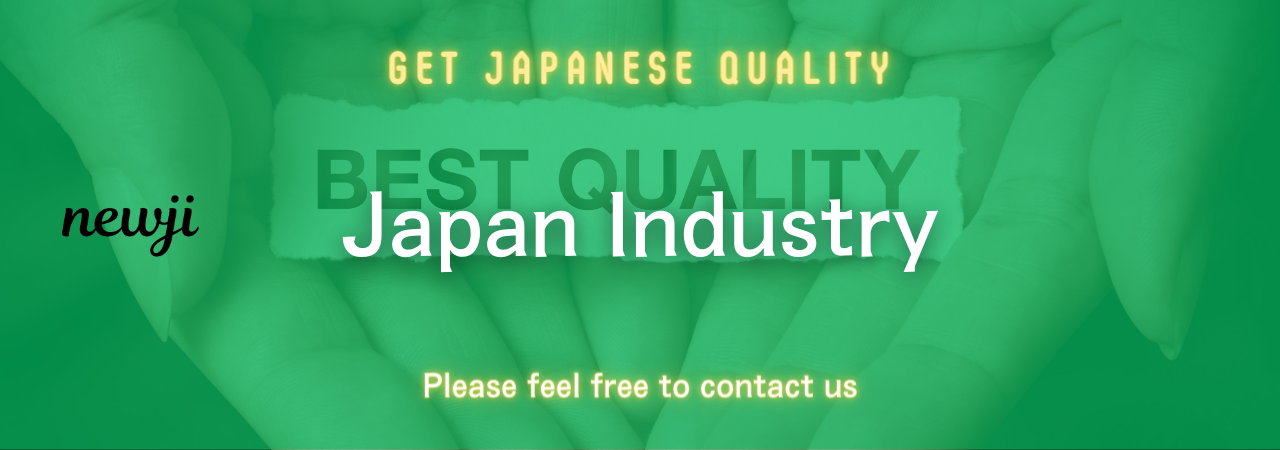
目次
Introduction to Japanese Precision in Analog Circuit Manufacturing
Japanese manufacturing has long been synonymous with precision and innovation. In the realm of analog circuit manufacturing, Japan has established itself as a global leader. This leadership is not accidental but the result of decades of dedication to quality, continuous improvement, and strategic procurement practices. Understanding how Japanese manufacturers excel in analog circuit innovation provides valuable insights for international companies seeking to enhance their own manufacturing processes.
The Pillars of Japanese Manufacturing Excellence
Commitment to Quality
Japanese manufacturers prioritize quality above all else. This commitment is embedded in the company culture, with every employee understanding the importance of producing defect-free products. Quality control processes are rigorous, and continual monitoring ensures that standards are consistently met. This relentless focus on quality reduces waste, minimizes rework, and ensures that the final product meets or exceeds customer expectations.
Continuous Improvement (Kaizen)
The philosophy of Kaizen, or continuous improvement, is deeply ingrained in Japanese manufacturing. Companies encourage employees at all levels to identify areas for improvement and implement incremental changes. This approach fosters an environment where innovation thrives, and processes are continually optimized for efficiency and effectiveness. In analog circuit manufacturing, Kaizen leads to the development of more precise production methods and the adoption of cutting-edge technologies.
Advanced Technology and Automation
Japanese manufacturers invest heavily in research and development, ensuring they remain at the forefront of technological advancements. Automation plays a critical role in enhancing precision and efficiency in analog circuit production. Automated systems reduce the likelihood of human error, increase production speed, and allow for greater consistency in product quality. The integration of advanced robotics and intelligent manufacturing systems enables Japanese companies to maintain their competitive edge.
Procurement and Purchasing Strategies
Strategic Supplier Relationships
Building strong, strategic relationships with suppliers is a cornerstone of Japanese procurement practices. Japanese companies view suppliers as partners rather than mere vendors. This collaborative approach ensures that suppliers are aligned with the manufacturer’s quality standards and business objectives. Long-term partnerships foster mutual trust, encourage knowledge sharing, and enable both parties to work together towards common goals, such as innovation and cost reduction.
Just-In-Time (JIT) Inventory Management
The Just-In-Time inventory system is a key component of Japanese procurement strategy. JIT emphasizes the delivery of materials and components precisely when they are needed in the production process. This approach minimizes inventory costs, reduces waste, and enhances flexibility. In analog circuit manufacturing, where precision is paramount, JIT ensures that high-quality materials are available without overstocking, which can lead to inefficiencies and increased costs.
Global Sourcing and Diversification
Japanese manufacturers adopt a global sourcing strategy to ensure access to the best materials and components worldwide. By diversifying their supplier base, they mitigate risks associated with supply chain disruptions, geopolitical issues, and market fluctuations. This diversification also allows Japanese companies to leverage competitive pricing and access innovative materials that may not be available domestically, thereby enhancing the quality and performance of their analog circuits.
Advantages of Japanese Manufacturing in Analog Circuits
Unmatched Precision and Reliability
Japanese analog circuit manufacturers are renowned for their precision and reliability. The meticulous attention to detail in every stage of production ensures that circuits perform consistently within specified parameters. This reliability is crucial for applications in industries such as automotive, aerospace, and medical devices, where performance failures can have significant consequences.
Innovative Design and Engineering
Japanese companies excel in research and development, driving innovation in analog circuit design and engineering. Advanced simulation tools, collaborative design processes, and a focus on cutting-edge technologies enable the creation of high-performance circuits that meet the evolving demands of various industries. This innovation leads to products that are not only more efficient but also more adaptable to changing market needs.
Efficient Production Processes
Efficiency is a hallmark of Japanese manufacturing, achieved through streamlined production processes and the elimination of waste. Techniques such as Lean manufacturing and Kaizen contribute to operational excellence, ensuring that analog circuits are produced cost-effectively without compromising on quality. This efficiency allows Japanese manufacturers to offer competitive pricing while maintaining high-profit margins.
Challenges and Disadvantages
High Initial Investment
One of the primary challenges of Japanese analog circuit manufacturing is the high initial investment required for advanced technology and automation. The cost of state-of-the-art equipment, research and development, and training can be substantial. While these investments lead to long-term benefits, they can be a barrier to entry for smaller companies or those with limited financial resources.
Cultural and Communication Barriers
International companies may encounter cultural and communication barriers when partnering with Japanese suppliers. Differences in business practices, language, and corporate culture can lead to misunderstandings and inefficiencies. Overcoming these barriers requires patience, cultural sensitivity, and effective communication strategies to ensure smooth collaboration.
Dependence on Key Suppliers
While strong supplier relationships are a strength, they can also pose risks. Dependence on key suppliers for critical components may lead to vulnerabilities in the supply chain. Disruptions such as natural disasters, economic downturns, or changes in supplier business practices can significantly impact production. Diversifying suppliers and developing contingency plans are essential strategies to mitigate this risk.
Supplier Negotiation Techniques
Building Long-Term Partnerships
Successful negotiation with Japanese suppliers often hinges on establishing long-term partnerships. Demonstrating a commitment to a mutually beneficial relationship encourages suppliers to offer better terms, prioritize your orders, and invest in understanding your specific needs. Trust and reliability are paramount in these negotiations, ensuring that both parties are committed to long-term success.
Emphasizing Mutual Benefits
Negotiations should focus on creating win-win scenarios where both the manufacturer and supplier benefit. Highlighting how your business can help the supplier grow, improve their processes, or enter new markets can lead to more favorable terms. Collaborative approaches that consider the supplier’s needs and challenges foster stronger relationships and more successful negotiations.
Leveraging Market Knowledge
Having in-depth knowledge of the market, including supplier capabilities, industry trends, and competitive pricing, strengthens your negotiating position. Understanding the supplier’s cost structure and profit margins allows for more informed negotiations, ensuring that you can negotiate fair prices while respecting the supplier’s business sustainability.
Market Conditions and Trends
Technological Advancements
The analog circuit market is continuously evolving with technological advancements. Innovations in materials, design methodologies, and manufacturing processes drive the development of higher-performance circuits. Japanese manufacturers stay ahead by investing in R&D and adopting emerging technologies, ensuring they meet the dynamic needs of various industries.
Global Supply Chain Dynamics
Global supply chain dynamics significantly impact the analog circuit market. Factors such as trade policies, geopolitical tensions, and economic shifts influence the availability and cost of components and materials. Japanese companies adapt by diversifying their supplier base, investing in domestic production capabilities, and developing flexible supply chain strategies to navigate these complexities.
Sustainability and Environmental Regulations
Increasing emphasis on sustainability and stringent environmental regulations are shaping the analog circuit manufacturing landscape. Japanese manufacturers incorporate eco-friendly practices, such as reducing waste, recycling materials, and minimizing energy consumption. Compliance with global environmental standards not only meets regulatory requirements but also appeals to environmentally conscious customers.
Best Practices in Japanese Analog Circuit Procurement
Thorough Supplier Evaluation
Effective procurement begins with a thorough evaluation of potential suppliers. Assessing factors such as quality control processes, technological capabilities, financial stability, and compliance with industry standards ensures that selected suppliers can meet your specific requirements. Site visits, audits, and reference checks are essential components of this evaluation process.
Clear Communication of Requirements
Clearly conveying your technical and business requirements to suppliers is crucial for successful procurement. Detailed specifications, performance criteria, and quality standards should be communicated to avoid misunderstandings and ensure that suppliers can deliver products that meet your expectations. Utilizing detailed contracts and agreements helps formalize these requirements and provides a reference point for both parties.
Implementing Robust Quality Assurance
Establishing robust quality assurance processes ensures that analog circuits meet or exceed specified standards. This includes setting up quality control checkpoints, conducting regular inspections, and implementing feedback loops for continuous improvement. Collaborating with suppliers to develop joint quality initiatives reinforces the commitment to excellence and helps identify and address quality issues proactively.
Case Studies: Japanese Manufacturing Success Stories
Case Study 1: Leading Automotive Electronics Supplier
A prominent Japanese manufacturer in the automotive industry leveraged advanced analog circuit technology to enhance vehicle safety systems. By partnering with local suppliers committed to quality and innovation, the company developed sophisticated sensors and control units that significantly improved vehicle performance and safety. This collaboration resulted in increased market share and recognition for technological excellence.
Case Study 2: Aerospace Communication Systems
In the aerospace sector, a Japanese manufacturer collaborated with international partners to produce high-precision analog communication systems. Through meticulous procurement practices and stringent quality controls, the company delivered reliable and advanced communication solutions trusted by major aerospace firms worldwide. This success was driven by a focus on continuous improvement and robust supplier relationships.
Future Outlook for Japanese Analog Circuit Manufacturing
Japanese analog circuit manufacturing is poised for continued growth and innovation. Emerging technologies such as artificial intelligence, the Internet of Things (IoT), and 5G connectivity are creating new opportunities for analog circuit applications. Japanese manufacturers are well-positioned to capitalize on these trends due to their expertise in precision engineering, commitment to quality, and strategic procurement practices.
Embracing Digital Transformation
Digital transformation is revolutionizing manufacturing processes, and Japanese companies are at the forefront of this shift. Implementing Industry 4.0 technologies such as IoT-enabled devices, data analytics, and smart manufacturing systems enhances production efficiency and enables real-time monitoring and optimization of analog circuit manufacturing processes.
Expanding Global Presence
Japanese manufacturers are expanding their global presence to better serve international markets. Establishing manufacturing facilities and partnerships in key regions allows companies to respond more swiftly to local demands, reduce lead times, and mitigate supply chain risks. This global expansion strategy reinforces Japan’s leadership in the analog circuit industry.
Conclusion
Japanese manufacturing excellence in analog circuit innovation is a testament to the power of quality, continuous improvement, and strategic procurement. By fostering strong supplier relationships, embracing advanced technologies, and maintaining a relentless focus on precision, Japanese companies have set the standard in the analog circuit industry. International manufacturers can learn valuable lessons from Japan’s approach, adopting best practices to enhance their own production capabilities and achieve success in a competitive global market.
資料ダウンロード
QCD管理受発注クラウド「newji」は、受発注部門で必要なQCD管理全てを備えた、現場特化型兼クラウド型の今世紀最高の受発注管理システムとなります。
ユーザー登録
受発注業務の効率化だけでなく、システムを導入することで、コスト削減や製品・資材のステータス可視化のほか、属人化していた受発注情報の共有化による内部不正防止や統制にも役立ちます。
NEWJI DX
製造業に特化したデジタルトランスフォーメーション(DX)の実現を目指す請負開発型のコンサルティングサービスです。AI、iPaaS、および先端の技術を駆使して、製造プロセスの効率化、業務効率化、チームワーク強化、コスト削減、品質向上を実現します。このサービスは、製造業の課題を深く理解し、それに対する最適なデジタルソリューションを提供することで、企業が持続的な成長とイノベーションを達成できるようサポートします。
製造業ニュース解説
製造業、主に購買・調達部門にお勤めの方々に向けた情報を配信しております。
新任の方やベテランの方、管理職を対象とした幅広いコンテンツをご用意しております。
お問い合わせ
コストダウンが利益に直結する術だと理解していても、なかなか前に進めることができない状況。そんな時は、newjiのコストダウン自動化機能で大きく利益貢献しよう!
(β版非公開)