- お役立ち記事
- Mastering Precision: The Rise of Japanese Dry Etching Processing OEMs in Advanced Manufacturing
月間76,176名の
製造業ご担当者様が閲覧しています*
*2025年3月31日現在のGoogle Analyticsのデータより
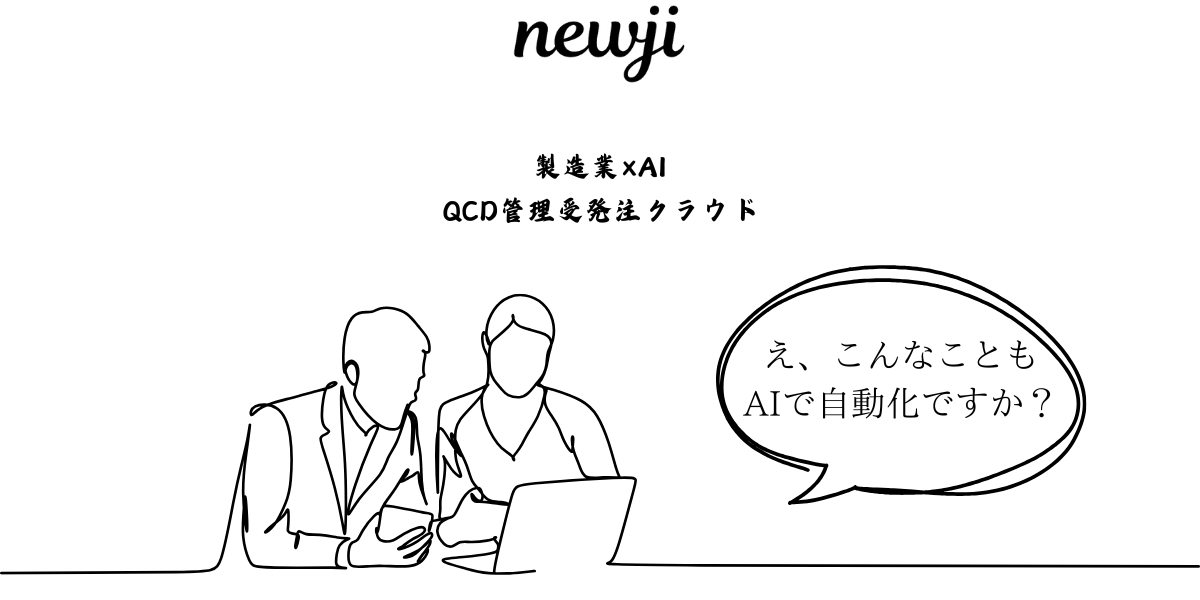
Mastering Precision: The Rise of Japanese Dry Etching Processing OEMs in Advanced Manufacturing
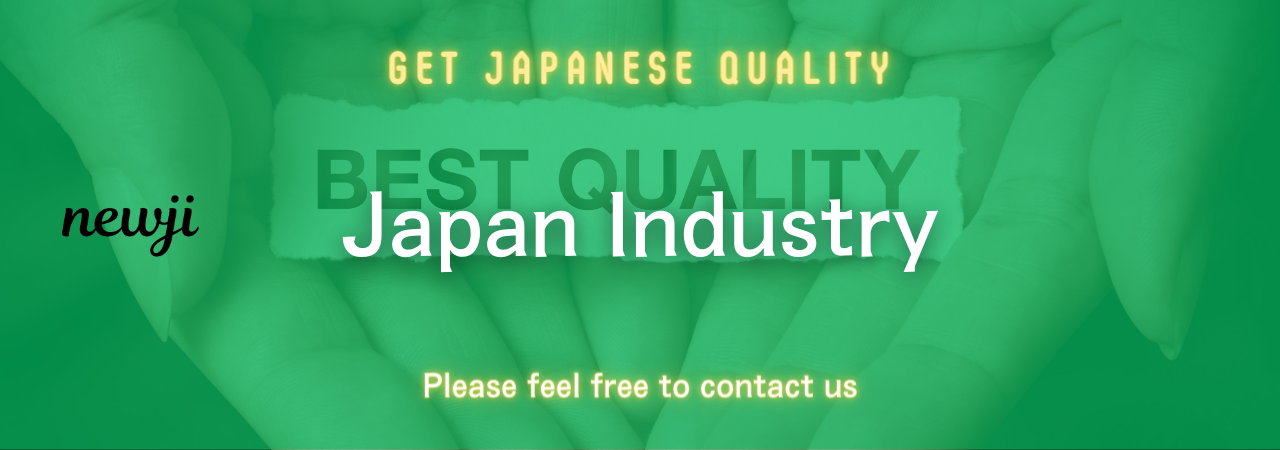
目次
Introduction to Japanese Dry Etching Processing OEMs
Dry etching has emerged as a cornerstone technology in advanced manufacturing, especially within semiconductor and precision component industries.
Japanese Original Equipment Manufacturers (OEMs) have led the charge, revolutionizing the field through their unparalleled craftsmanship and engineering expertise.
This article aims to shed light on the rise of Japanese dry etching processing OEMs, exploring their advantages and disadvantages while offering practical insights and best practices for effective supplier negotiation and procurement.
Understanding Dry Etching Processing
Dry etching is a technique used to precisely remove layers from a solid surface, typically conducted in a vacuum environment using gases like fluorocarbons.
The method is particularly indispensable in microfabrication processes, including the manufacture of semiconductor devices, microelectromechanical systems (MEMS), and other precision components.
Advantages of Dry Etching
*Precise Control*: The ability to achieve nano-level accuracy makes dry etching an ideal choice for producing intricate patterns and structures.
*High Anisotropy*: This allows for the creation of vertical sidewalls in microstructures, enhancing the performance of semiconductor devices.
*Reduced Contamination*: Conducting the process in a vacuum minimizes the risk of particle contamination, which is crucial in high-precision manufacturing.
Challenges of Dry Etching
*Complexity*: The intricate nature of dry etching requires highly specialized equipment and expertise.
*High Costs*: The sophisticated machinery and controlled environment contribute to higher operational costs.
*Process Sensitivity*: Even minor variations in process parameters can significantly impact the final product quality.
The Prowess of Japanese OEMs in Dry Etching
Japanese OEMs have solidified themselves as global leaders in dry etching technology.
Their success can be attributed to several key factors:
Commitment to Quality
Japanese manufacturers are renowned for their zero-defect mindset.
This philosophy permeates through their etching processes, ensuring unparalleled precision and consistency.
Advanced Technology
Integrating cutting-edge technology such as AI and machine learning, Japanese OEMs continually refine their etching systems, offering superior control and automation.
Skilled Workforce
The depth of technical expertise and continuous skill development programs in Japan ensure that engineers and operators are well-versed in the latest advancements and best practices in dry etching.
Advantages of Partnering with Japanese OEMs
State-of-the-Art Equipment
Japanese OEMs provide state-of-the-art etching equipment that guarantees high performance and reliability.
Their machines come equipped with sophisticated software for monitoring and controlling etching parameters, ensuring top-notch product quality.
Strong R&D Capabilities
Japanese firms invest heavily in research and development.
This focus on innovation enables them to stay ahead of technological trends and offer advanced etching solutions tailored to customer needs.
Technical Support and Training
Japanese suppliers typically offer comprehensive technical support and training programs.
Customers can rely on these services to ensure proper utilization and maintenance of etching equipment, minimizing downtime and optimizing efficiency.
Disadvantages to Consider
While the advantages of partnering with Japanese OEMs are significant, there are also some challenges that procurement professionals should be aware of:
High Initial Investment
The advanced equipment and technologies provided by Japanese OEMs often come with a high initial investment cost.
Organizations must be prepared for this financial commitment to reap the long-term benefits of enhanced performance and precision.
Supply Chain Complexity
Dealing with international suppliers can introduce complexities in the supply chain.
Procurement professionals must navigate potential issues related to lead times, shipping logistics, and customs regulations.
Cultural and Language Barriers
Although many Japanese firms have global operations, language and cultural differences can still pose challenges.
Effective communication and mutual understanding are crucial for fostering strong supplier relationships.
Supplier Negotiation Techniques
Developing effective negotiation strategies with Japanese OEMs can significantly enhance procurement outcomes.
Here are some practical techniques:
Understanding the Japanese Business Culture
Building trust is essential in Japanese business culture.
Demonstrating respect, patience, and understanding in interactions can lay the groundwork for successful negotiations.
Emphasizing Long-Term Partnerships
Japanese companies value long-term relationships over short-term gains.
Highlighting your organization’s commitment to a lasting partnership can create a positive negotiating environment.
Leveraging Technical Expertise
Showcasing a deep understanding of dry etching technology and communicating your specific requirements can lead to more favorable terms.
Japanese suppliers appreciate informed and technically proficient partners.
Market Conditions for Dry Etching Equipment
The market for dry etching equipment is highly competitive, with Japanese OEMs facing competition from suppliers in other countries, such as the U.S. and South Korea.
Global Demand
The demand for dry etching equipment is driven by the semiconductor and electronics industries.
With the advent of technologies like 5G, AI, and IoT, the need for precision etching continues to grow.
Technological Advancements
Continuous advancements in etching technology are shaping the market dynamics.
Emerging techniques such as plasma-enhanced atomic layer etching (PEALE) are expected to revolutionize precision etching processes.
Regulatory Environment
Stringent environmental regulations impact the manufacturing of dry etching equipment.
Japanese OEMs, known for their eco-friendly approaches, are well-positioned to navigate these regulatory challenges.
Best Practices for Effective Procurement
To maximize the benefits of procuring from Japanese dry etching OEMs, consider the following best practices:
Conduct Thorough Market Research
Stay informed about market trends, emerging technologies, and competitive offerings.
This knowledge equips you to make informed procurement decisions.
Build Strong Supplier Relationships
Invest time in understanding your suppliers and fostering open communication channels.
Strong relationships can lead to better collaboration and problem-solving.
Focus on Total Cost of Ownership (TCO)
While initial costs are important, consider the total cost of ownership.
Factor in maintenance, operating costs, and potential productivity gains over the equipment’s lifespan.
Maintain Quality Control Standards
Implement stringent quality control measures to ensure the equipment meets your organization’s standards.
Regular inspections and performance evaluations are vital.
Conclusion
Japanese OEMs have established themselves as leaders in the field of dry etching processing, offering unmatched precision, advanced technology, and robust technical support.
While the high initial investment and potential supply chain complexities are challenges to consider, the long-term benefits are substantial.
By understanding Japanese business culture, leveraging technical expertise, and fostering strong relationships, procurement professionals can navigate negotiations effectively and secure valuable partnerships.
With continuous advancements in technology and an ever-evolving market, staying informed and adopting best practices ensures successful procurement outcomes.
Partnering with Japanese dry etching OEMs can unlock unparalleled efficiency and quality, driving innovation and success in advanced manufacturing.
資料ダウンロード
QCD管理受発注クラウド「newji」は、受発注部門で必要なQCD管理全てを備えた、現場特化型兼クラウド型の今世紀最高の受発注管理システムとなります。
ユーザー登録
受発注業務の効率化だけでなく、システムを導入することで、コスト削減や製品・資材のステータス可視化のほか、属人化していた受発注情報の共有化による内部不正防止や統制にも役立ちます。
NEWJI DX
製造業に特化したデジタルトランスフォーメーション(DX)の実現を目指す請負開発型のコンサルティングサービスです。AI、iPaaS、および先端の技術を駆使して、製造プロセスの効率化、業務効率化、チームワーク強化、コスト削減、品質向上を実現します。このサービスは、製造業の課題を深く理解し、それに対する最適なデジタルソリューションを提供することで、企業が持続的な成長とイノベーションを達成できるようサポートします。
製造業ニュース解説
製造業、主に購買・調達部門にお勤めの方々に向けた情報を配信しております。
新任の方やベテランの方、管理職を対象とした幅広いコンテンツをご用意しております。
お問い合わせ
コストダウンが利益に直結する術だと理解していても、なかなか前に進めることができない状況。そんな時は、newjiのコストダウン自動化機能で大きく利益貢献しよう!
(β版非公開)