- お役立ち記事
- Mastering Precision: The Role of Measuring Tools in Japanese Manufacturing Excellence
Mastering Precision: The Role of Measuring Tools in Japanese Manufacturing Excellence
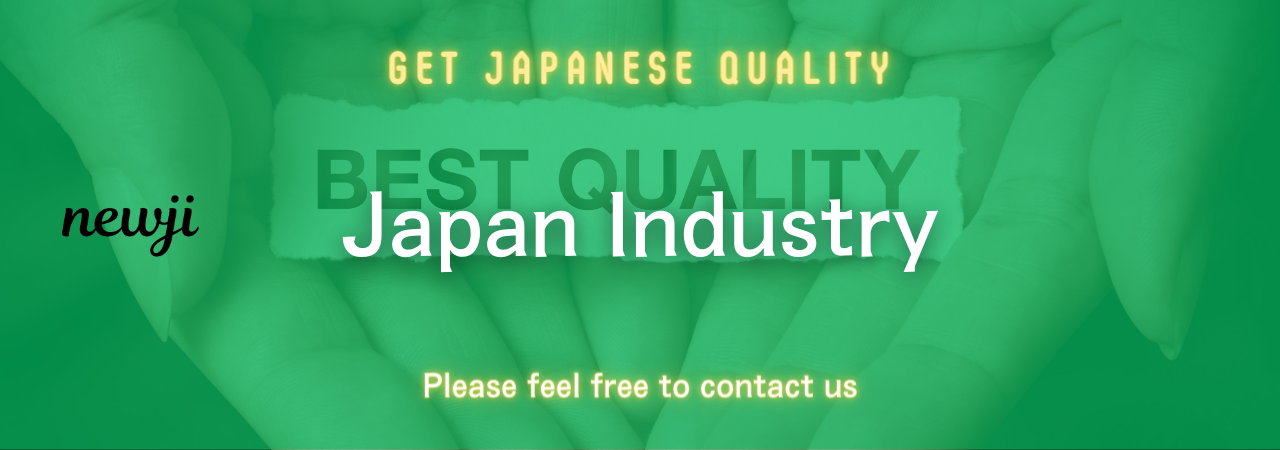
In the realm of global manufacturing, Japanese companies have long been synonymous with precision, quality, and unwavering commitment to craftsmanship.
At the core of this reputation lies an often-overlooked element: measuring tools.
Japanese manufacturing’s success can be largely attributed to the meticulous use of advanced measurement tools that ensure unparalleled product quality and consistency.
目次
The Importance of Measuring Tools in Japanese Manufacturing
Measuring tools play a critical role in Japanese manufacturing for several reasons.
They provide the means to achieve the high precision that defines Japanese products, maintain stringent quality control standards, and facilitate continuous improvement in production processes.
To appreciate the significance of measuring tools in this context, it is essential to understand how they contribute to various manufacturing stages.
Ensuring Precision and Accuracy
Japanese manufacturers prioritize precision and accuracy in every aspect of production.
Measuring tools are vital in achieving these goals by enabling manufacturers to make exact cuts, align components accurately, and maintain consistent product dimensions.
In industries like automotive, aerospace, and electronics, even the slightest deviation can result in subpar performance or system failures.
Using advanced measuring tools minimizes these risks by ensuring that every part meets the highest standards.
Maintaining Quality Control
Quality control is a cornerstone of Japanese manufacturing philosophy.
Measuring tools are indispensable in this regard, as they allow for continuous monitoring and verification of product quality throughout the production process.
From raw material inspection to final product assembly, these tools help identify defects, ensure compliance with specifications, and reduce waste.
This continuous attention to quality is a significant factor in why Japanese products are often considered superior in terms of reliability and durability.
Facilitating Continuous Improvement
The concept of “Kaizen” or continuous improvement is deeply ingrained in Japanese culture and manufacturing practices.
Measuring tools are essential in this pursuit as they provide precise data needed to identify areas for improvement.
By regularly analyzing measurement data, manufacturers can make informed decisions on optimizing processes, reducing cycle times, and enhancing overall efficiency.
This data-driven approach ensures that manufacturers remain competitive and can adapt to evolving market demands.
Types of Measuring Tools Commonly Used in Japanese Manufacturing
The variety and sophistication of measuring tools used in Japanese manufacturing are vast.
These tools can generally be categorized into several main types:
Calipers and Micrometers
Calipers and micrometers are fundamental measurement tools in manufacturing.
Calipers are versatile instruments used to measure internal and external dimensions and depths with high accuracy.
Micrometers, on the other hand, are used for more precise measurements of thicknesses and distances in the sub-millimeter range.
Both tools are critical in ensuring that components meet exact specifications.
CMM (Coordinate Measuring Machines)
Coordinate Measuring Machines (CMMs) are automated tools used to measure the geometry of physical objects by sensing discrete points on the surface.
CMMs are highly accurate and are instrumental in measuring complex geometries and ensuring adherence to tight tolerances.
They are commonly used in industries such as automotive and aerospace, where precision is paramount.
Laser Scanners and Optical Comparators
Laser scanners and optical comparators are used for non-contact measurement.
Laser scanners create detailed 3D models of parts and are particularly useful in reverse engineering and quality inspection.
Optical comparators project magnified images of parts onto a screen, allowing manufacturers to compare them against standard profiles.
These tools are valuable in detecting deviations that might not be visible to the naked eye.
Gauges and Standards
Gauges, such as ring gauges and plug gauges, are used to verify the conformity of manufactured parts to specified dimensions.
Standards, including gauge blocks, provide reference measurements for calibrating other measurement tools.
These tools ensure that measurements remain consistent and reliable across different production batches and facilities.
Advantages of Using Advanced Measuring Tools in Japanese Manufacturing
The deployment of advanced measuring tools in Japanese manufacturing offers several compelling advantages.
Enhanced Product Quality
The primary advantage of using high-precision measuring tools is the significant enhancement of product quality.
Accurate measurements ensure that each component conforms to design specifications, reducing the likelihood of defects and failures in the final product.
This emphasis on quality translates into greater customer satisfaction and brand loyalty.
Increased Production Efficiency
Measuring tools contribute to increased production efficiency by enabling faster and more accurate inspections.
Automated tools, such as CMMs and laser scanners, can quickly measure complex parts, reducing bottlenecks and minimizing downtime.
This efficiency allows manufacturers to meet tight deadlines and remain competitive in a global market.
Reduced Waste and Cost Savings
Accurate measurements help minimize material waste by ensuring that parts are produced correctly the first time.
This reduction in waste leads to significant cost savings in terms of materials, labor, and time.
Moreover, identifying defects early in the production process prevents costly rework and product recalls, further enhancing profitability.
Improved Compliance with Standards
In many industries, stringent regulatory standards must be met to ensure product safety and performance.
Advanced measuring tools facilitate compliance with these standards by providing reliable data for documentation and certification processes.
This compliance is crucial for accessing international markets and avoiding legal and financial penalties.
Challenges and Disadvantages of Using Measuring Tools in Japanese Manufacturing
While the advantages of using advanced measuring tools are clear, there are also several challenges and disadvantages to consider.
High Initial Investment
One of the primary disadvantages of adopting advanced measuring tools is the high initial investment required.
High-precision instruments, such as CMMs and laser scanners, can be expensive to purchase and install.
For small and medium-sized enterprises (SMEs), these costs can be prohibitive and may require careful financial planning.
Maintenance and Calibration Costs
Maintaining the accuracy of measuring tools requires regular calibration and servicing.
These activities incur ongoing costs and necessitate the allocation of resources to ensure that instruments remain in optimal condition.
Failing to maintain equipment can result in inaccurate measurements and compromised product quality.
Training and Skill Development
The effective use of advanced measuring tools requires specialized knowledge and skills.
Manufacturers must invest in training programs to equip their workforce with the necessary expertise.
This training can be time-consuming and may temporarily disrupt production activities.
Moreover, retaining skilled personnel is essential to leverage the full benefits of these instruments.
Integration with Existing Processes
Integrating new measuring tools with existing manufacturing processes can be challenging.
It may require modifications to workflows, production schedules, and data management systems.
Ensuring seamless integration is critical to maximizing the benefits of advanced measurement technology.
Supplier Negotiation Techniques for Measuring Tools
Acquiring the best measuring tools often involves negotiations with suppliers.
Effective negotiation techniques can secure favorable terms and ensure that manufacturers receive high-quality instruments at competitive prices.
Understand Market Conditions
Before entering negotiations, it is essential to understand the current market conditions for measuring tools.
Researching trends, supplier reputations, and technological advancements can provide valuable insights.
This knowledge allows manufacturers to make informed decisions and negotiate from a position of strength.
Specify Requirements Clearly
Clearly specifying requirements is crucial in negotiations.
Manufacturers should provide detailed specifications, including measurement accuracy, range, and environmental conditions.
Clear communication ensures that suppliers understand the manufacturer’s needs and can offer suitable solutions.
Compare Multiple Suppliers
Comparing offerings from multiple suppliers can yield significant advantages.
Requesting quotes and proposals from several vendors allows manufacturers to evaluate options and identify the best value.
This competitive approach can drive down costs and prompt suppliers to offer additional services or incentives.
Leverage Long-Term Relationships
Building long-term relationships with suppliers can facilitate better negotiation outcomes.
Established relationships often lead to improved trust and collaboration.
Suppliers may be more willing to provide discounts, favorable terms, or value-added services to maintain strong business ties.
Consider Total Cost of Ownership
When negotiating, it is crucial to consider the total cost of ownership rather than just the purchase price.
This includes maintenance, calibration, training, and support costs.
Evaluating the long-term financial impact ensures that manufacturers make cost-effective decisions.
Best Practices for Utilizing Measuring Tools in Japanese Manufacturing
To maximize the benefits of measuring tools, manufacturers should adopt best practices that ensure proper use, maintenance, and integration.
Regular Calibration and Maintenance
Regular calibration and maintenance are essential to maintaining the accuracy and reliability of measuring tools.
Establishing a routine schedule for calibration and servicing prevents deviations and ensures consistent performance.
Working with accredited calibration service providers can also enhance accuracy.
Invest in Training and Skill Development
Investing in employee training and skill development is critical.
Providing comprehensive training programs on the proper use of measuring tools and interpreting measurement data enhances workforce competency.
continued learning opportunities keep personnel updated on the latest technological advancements and measurement techniques.
Implement Data Management Systems
Effective data management systems are crucial for leveraging measurement data.
Implementing systems that capture, store, and analyze measurement data allows manufacturers to make informed decisions.
Integrating data management with other manufacturing processes, such as quality control and production planning, enhances overall efficiency.
Foster a Culture of Precision and Quality
Fostering a culture that values precision and quality is fundamental to the successful use of measuring tools.
Encouraging employees to prioritize accuracy and attention to detail ensures that measurement practices are upheld throughout the organization.
Recognizing and rewarding adherence to quality standards reinforces these values.
Engage in Continuous Improvement
Continuous improvement is a hallmark of Japanese manufacturing.
Regularly reviewing measurement data and processes allows manufacturers to identify areas for enhancement.
Implementing incremental improvements ensures sustained growth in productivity, efficiency, and quality.
The Future of Measuring Tools in Japanese Manufacturing
The future of measuring tools in Japanese manufacturing is shaped by technological advancements and evolving market demands.
Advancements in Digital and Automated Measurement
Digital and automated measurement tools are likely to become more prevalent.
Technologies such as machine vision, artificial intelligence, and the Internet of Things (IoT) are revolutionizing measurement practices.
These advancements enable real-time data collection, analysis, and decision-making, further enhancing precision and efficiency.
Increased Integration with Industry 4.0
The integration of measuring tools with Industry 4.0 principles is expected to continue.
Smart manufacturing environments that leverage interconnected devices and data analytics will become more common.
This integration allows for predictive maintenance, adaptive production processes, and enhanced traceability.
Sustainable Measurement Practices
Sustainability is becoming an increasingly important consideration in manufacturing.
Measuring tools will play a role in promoting sustainable practices by minimizing waste, optimizing resource use, and ensuring product longevity.
Developing eco-friendly measurement technologies and practices will be a priority.
Customization and Flexibility
Customization and flexibility in measuring tools will be in high demand.
Manufacturers will seek solutions tailored to their specific applications and production requirements.
Modular and scalable measuring systems that can adapt to changing needs will be highly valued.
In conclusion, measuring tools are indispensable in Japanese manufacturing, driving the precision, quality, and continuous improvement that define the industry.
The careful selection, use, and maintenance of these tools ensure that Japanese manufacturers maintain their competitive edge on the global stage.
By understanding the advantages, challenges, and best practices associated with measuring tools, manufacturers can harness their full potential and continue to deliver products of unparalleled excellence.
資料ダウンロード
QCD調達購買管理クラウド「newji」は、調達購買部門で必要なQCD管理全てを備えた、現場特化型兼クラウド型の今世紀最高の購買管理システムとなります。
ユーザー登録
調達購買業務の効率化だけでなく、システムを導入することで、コスト削減や製品・資材のステータス可視化のほか、属人化していた購買情報の共有化による内部不正防止や統制にも役立ちます。
NEWJI DX
製造業に特化したデジタルトランスフォーメーション(DX)の実現を目指す請負開発型のコンサルティングサービスです。AI、iPaaS、および先端の技術を駆使して、製造プロセスの効率化、業務効率化、チームワーク強化、コスト削減、品質向上を実現します。このサービスは、製造業の課題を深く理解し、それに対する最適なデジタルソリューションを提供することで、企業が持続的な成長とイノベーションを達成できるようサポートします。
オンライン講座
製造業、主に購買・調達部門にお勤めの方々に向けた情報を配信しております。
新任の方やベテランの方、管理職を対象とした幅広いコンテンツをご用意しております。
お問い合わせ
コストダウンが利益に直結する術だと理解していても、なかなか前に進めることができない状況。そんな時は、newjiのコストダウン自動化機能で大きく利益貢献しよう!
(Β版非公開)