- お役立ち記事
- Mastering Quality Control in Japanese Manufacturing: The Seven QC Tools Explained
Mastering Quality Control in Japanese Manufacturing: The Seven QC Tools Explained
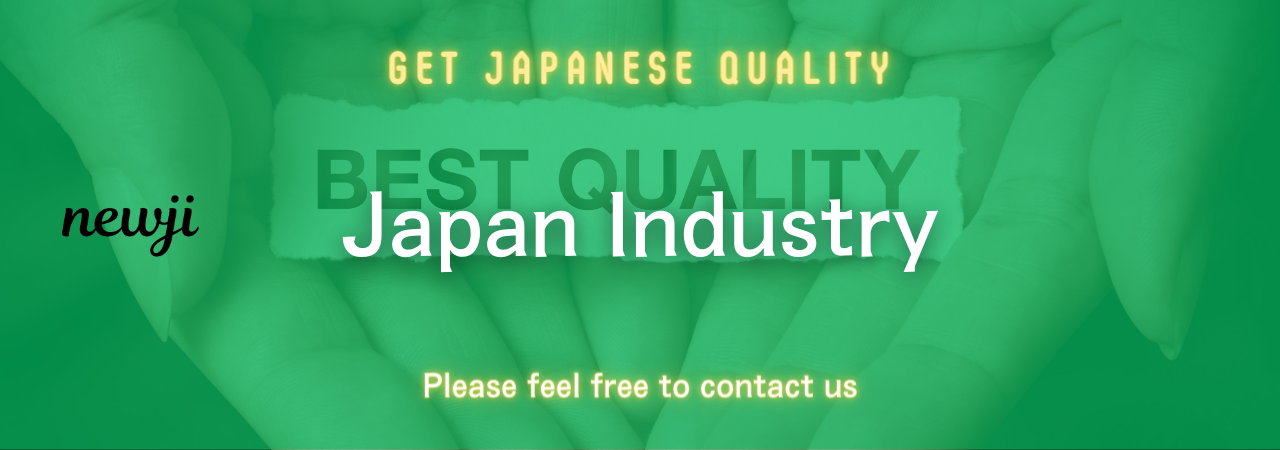
Understanding and mastering quality control in manufacturing has never been more crucial than in today’s highly competitive global market.
Japanese manufacturing, with its renowned focus on quality and continuous improvement, provides a comprehensive framework to ensure products meet the highest standards.
Central to this framework are the Seven QC (Quality Control) Tools, which are invaluable for any procurement and purchasing professional aiming to enhance factory efficiency and product quality.
目次
Introduction to Quality Control in Japanese Manufacturing
Japanese manufacturing is synonymous with meticulous attention to quality and efficiency.
This dedication has positioned Japan as a global leader in various sectors, from automotive to electronics.
Understanding the principles and tools used in Japanese manufacturing can offer significant benefits to companies seeking to improve their own production processes.
The Importance of Quality Control
Quality control is fundamental in manufacturing, serving to ensure that products meet specified standards and customer expectations.
It involves systematic processes for detecting and addressing defects, thereby reducing waste and improving efficiency.
In Japanese manufacturing, this is often linked to the concept of ‘Kaizen’ or continuous improvement.
Kaizen focuses on small, incremental changes that collectively lead to significant improvements over time.
Effective quality control not only enhances product reliability but also strengthens a company’s reputation, reducing costs associated with rework, recalls, and customer complaints.
Japanese manufacturers have long recognized these benefits, employing comprehensive quality control measures to maintain their competitive edge.
Overview of the Seven QC Tools
The Seven QC Tools are a set of fundamental techniques used to solve quality-related issues in manufacturing.
Developed by Kaoru Ishikawa, these tools are essential for any quality improvement initiative.
They are simple yet effective, enabling teams to identify, analyze, and rectify problems efficiently.
1. Pareto Chart
What is a Pareto Chart?
A Pareto chart is a bar graph that represents the frequency or impact of problems or causes in a process.
The principle behind it, often called the 80/20 rule, suggests that roughly 80% of effects come from 20% of causes.
By focusing on these critical causes, companies can achieve significant improvements with minimal effort.
Practical Application
In procurement and purchasing, a Pareto chart can help identify the most frequent supplier issues, such as delays or defects.
This allows for prioritizing which suppliers or issues need immediate attention to enhance overall supply chain efficiency.
2. Cause-and-Effect Diagram
What is a Cause-and-Effect Diagram?
Also known as the Ishikawa or Fishbone Diagram, this tool helps identify root causes of a problem.
By categorizing potential causes into major categories (such as materials, methods, machines, manpower, measurements, and environment), it provides a structured approach to problem-solving.
Practical Application
In production management, this diagram can be used to investigate why a certain defect is occurring, enabling teams to address the contributing factors systematically.
This method fosters a deeper understanding of the interplay between different process elements.
3. Check Sheet
What is a Check Sheet?
A check sheet is a structured form for collecting and analyzing data.
It is typically used to record the frequency of specific events or defects.
Practical Application
In quality control, a check sheet can be employed to track occurrences of defects during production.
This data can then be used to identify patterns and areas that require improvement.
For purchasing departments, it can track supplier performance metrics, helping in selecting and negotiating with suppliers.
4. Control Chart
What is a Control Chart?
A control chart is a graphical tool used to monitor changes in a process over time.
It displays upper and lower control limits and helps determine whether a process is in control or needs adjustment.
Practical Application
In production engineering, control charts are essential for tracking process stability and identifying variability that could affect product quality.
For logistics, these charts can monitor the consistency of delivery times, ensuring that supply chains remain efficient and responsive.
5. Histogram
What is a Histogram?
A histogram is a bar graph that shows the distribution of data points across a specified range or category.
It provides a visual depiction of data trends and variability.
Practical Application
In quality control, histograms can be used to analyze the distribution of defect rates or measurement variations.
They help in understanding the underlying variability in processes, leading to more informed decision-making.
6. Scatter Diagram
What is a Scatter Diagram?
A scatter diagram displays the relationship between two variables, helping to identify potential correlations.
Practical Application
In production management, scatter diagrams can be used to explore relationships between factors such as machine settings and defect rates or to correlate supplier delivery performance with defect occurrences.
This tool aids in establishing cause-and-effect relationships, crucial for process optimization.
7. Flow Chart
What is a Flow Chart?
A flow chart maps out the steps in a process, providing a visual representation of the workflow.
This tool is crucial for identifying inefficiencies and areas for improvement.
Practical Application
In logistics, a flow chart can outline the steps from order placement to delivery, highlighting any bottlenecks or redundant processes.
For production, it maps out the manufacturing steps, making it easier to identify and address inefficiencies.
Advantages of Utilizing the Seven QC Tools
Integrating these tools into your quality control processes offers several significant advantages:
Enhanced Problem-Solving Capabilities
The Seven QC Tools provide a structured approach to diagnosing and addressing quality issues, leading to more effective problem resolution.
Data-Driven Decisions
These tools encourage the use of quantitative data in decision-making, reducing reliance on intuition and guesswork, and leading to more accurate and reliable outcomes.
Employee Engagement
By involving employees in quality control efforts, these tools foster a culture of continuous improvement and collective responsibility for quality.
Improved Supplier Relationships
Regularly using these tools to assess and communicate with suppliers helps build stronger partnerships based on clearly understood quality standards and expectations.
Disadvantages and Challenges
However, there are also challenges and potential disadvantages to be aware of:
Initial Resistance to Change
Introducing new quality control tools and processes can meet resistance from employees accustomed to traditional methods.
Training Requirements
Effective use of the Seven QC Tools requires proper training.
Without it, the benefits may not be fully realized.
Data Overload
Collecting and analyzing large amounts of data can be overwhelming and may require significant time and resources.
Supplier Negotiation Techniques
Utilizing the Seven QC Tools can also enhance supplier negotiations, a critical aspect of procurement and purchasing.
Leverage Data
Armed with data from your quality control tools, you can present a compelling case to suppliers regarding their performance and areas needing improvement.
Collaborative Problem-Solving
Use tools like the Cause-and-Effect Diagram to involve suppliers in identifying and addressing root causes of issues, fostering a collaborative approach to quality improvement.
Benchmarking
Employing histograms and control charts allows for benchmarking supplier performance, helping to set clear expectations and drive improvements.
Best Practices for Implementing the Seven QC Tools
To maximize the benefits of these tools, consider the following best practices:
Executive Support
Ensure that key executives understand and support the use of the Seven QC Tools, fostering a top-down commitment to quality.
Employee Training
Invest in thorough training for employees at all levels to ensure they understand how to use the tools effectively.
Continuous Improvement
Encourage a culture of Kaizen, where continuous improvement is a shared goal, and employees are regularly seeking ways to enhance quality.
Regular Reviews
Schedule regular reviews of quality control data to identify trends, measure progress, and make informed decisions.
Clear Communication
Maintain clear and open communication with suppliers regarding quality expectations and performance, using data from the Seven QC Tools to support discussions.
Conclusion
Mastering quality control is essential for any company aiming to compete in today’s global market.
Japanese manufacturers have long set the standard for excellence, and the Seven QC Tools are a testament to their systematic and effective approach to quality control.
By understanding and implementing these tools, procurement and purchasing professionals can enhance supplier relationships, reduce costs, and improve overall product quality.
Adopting these best practices ensures that quality control efforts are not only effective but also a cornerstone of a company’s long-term success.
資料ダウンロード
QCD調達購買管理クラウド「newji」は、調達購買部門で必要なQCD管理全てを備えた、現場特化型兼クラウド型の今世紀最高の購買管理システムとなります。
ユーザー登録
調達購買業務の効率化だけでなく、システムを導入することで、コスト削減や製品・資材のステータス可視化のほか、属人化していた購買情報の共有化による内部不正防止や統制にも役立ちます。
NEWJI DX
製造業に特化したデジタルトランスフォーメーション(DX)の実現を目指す請負開発型のコンサルティングサービスです。AI、iPaaS、および先端の技術を駆使して、製造プロセスの効率化、業務効率化、チームワーク強化、コスト削減、品質向上を実現します。このサービスは、製造業の課題を深く理解し、それに対する最適なデジタルソリューションを提供することで、企業が持続的な成長とイノベーションを達成できるようサポートします。
オンライン講座
製造業、主に購買・調達部門にお勤めの方々に向けた情報を配信しております。
新任の方やベテランの方、管理職を対象とした幅広いコンテンツをご用意しております。
お問い合わせ
コストダウンが利益に直結する術だと理解していても、なかなか前に進めることができない状況。そんな時は、newjiのコストダウン自動化機能で大きく利益貢献しよう!
(Β版非公開)