- お役立ち記事
- Mastering Quality Control in Japanese Manufacturing with FMEA: Streamlining Success through Failure Modes and Effects Analysis
月間76,176名の
製造業ご担当者様が閲覧しています*
*2025年3月31日現在のGoogle Analyticsのデータより
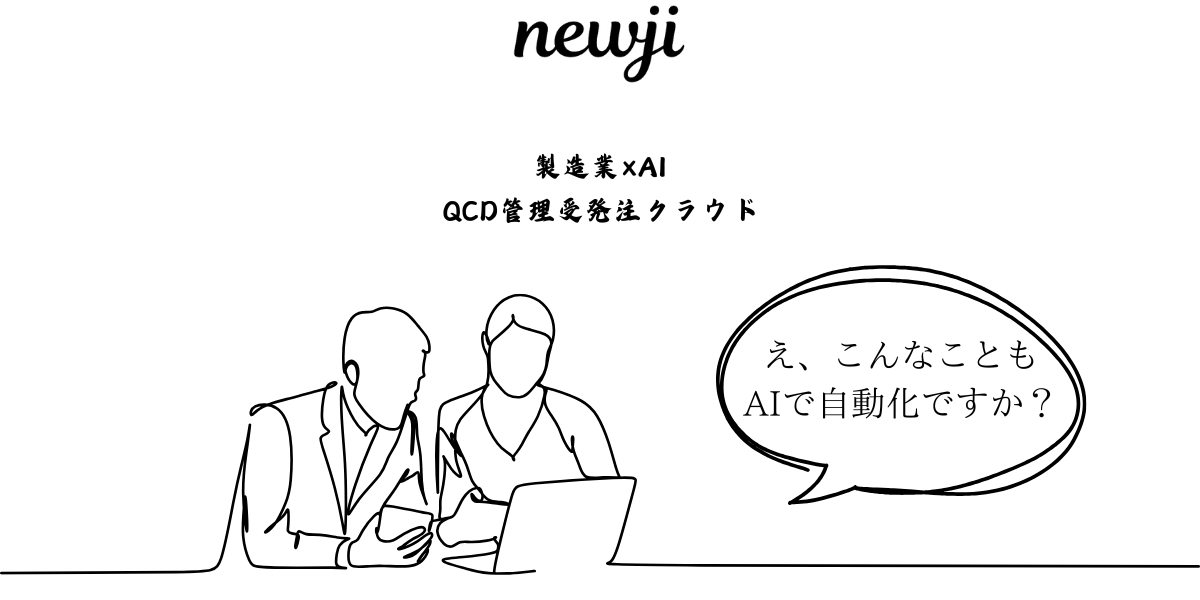
Mastering Quality Control in Japanese Manufacturing with FMEA: Streamlining Success through Failure Modes and Effects Analysis
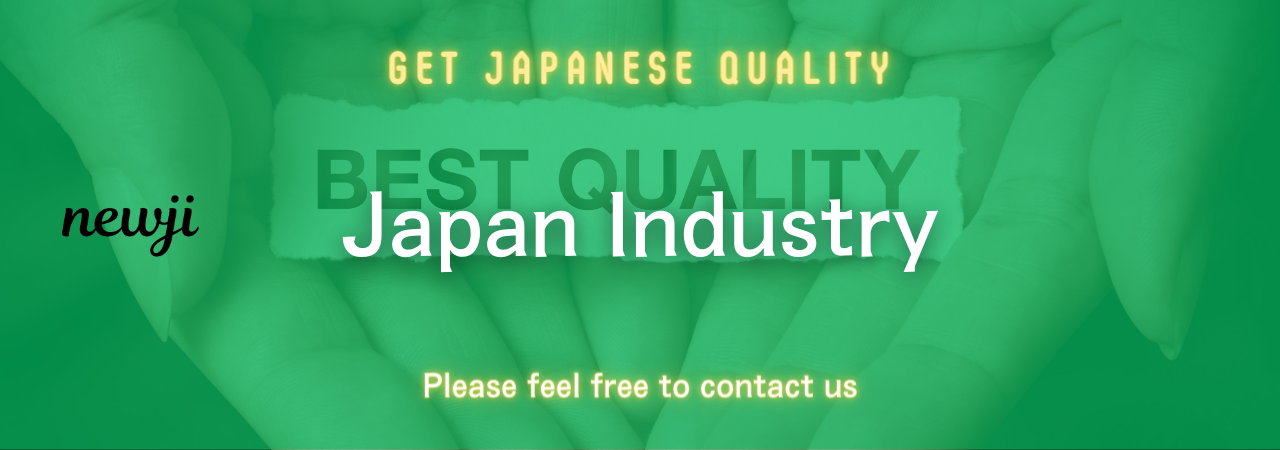
目次
Understanding the Importance of Quality Control in Japanese Manufacturing
In the dynamic landscape of global manufacturing, maintaining high-quality standards is paramount. Japanese manufacturers have long been revered for their exemplary commitment to quality control. This obsession with quality is deeply ingrained in their production processes and corporate philosophies. At the heart of this quality-centric approach lies Failure Modes and Effects Analysis (FMEA).
FMEA is a systematic method for identifying potential failure modes within a process, assessing their potential impact on product quality, and prioritizing them for corrective action. The integration of FMEA into Japanese quality control processes exemplifies how manufacturers in Japan continually strive for perfection.
The Significance of FMEA in Quality Control
FMEA is an indispensable tool in the arsenal of Japanese manufacturers. It serves as a proactive measure to prevent defects and improve product reliability. By identifying potential failure points before they escalate into major issues, FMEA ensures a higher degree of trustworthiness in manufactured goods.
Incorporating FMEA into the production process allows manufacturers to:
1. Enhance Product Reliability and Safety
With FMEA, potential failure modes are identified in the design and development phases. This early detection allows for changes and improvements that significantly enhance the reliability and safety of the product.
2. Minimize Costs Associated with Failures
By addressing failures early in the process, companies can avoid costly recalls and warranty claims. This proactive approach translates into substantial financial savings.
3. Streamline Continuous Improvement
FMEA facilitates continuous improvement by providing a structured framework for analyzing failures and implementing corrective actions. This commitment to constant enhancement ensures that products remain competitive and meet evolving market demands.
Advantages of Integrating FMEA in Japanese Manufacturing
The benefits of adopting FMEA in Japanese manufacturing are multifaceted and contribute to the overall success of their quality control systems.
1. Culture of Quality
Japanese manufacturers have a deeply rooted culture of quality that permeates every aspect of their operations. FMEA aligns seamlessly with this culture, reinforcing the focus on excellence at every stage of production.
2. Standardization and Consistency
FMEA provides a standardized methodology for evaluating potential failure modes. This consistency ensures that quality control measures are uniformly applied, leading to predictable and dependable outcomes.
3. Risk Mitigation
With FMEA, manufacturers can systematically identify and mitigate risks before they affect the final product. This proactive stance minimizes disruptions and enhances overall efficiency.
4. Enhanced Customer Trust
The rigorous application of FMEA instills confidence in customers. Products that undergo thorough failure analysis and subsequent improvements are more likely to meet or exceed customer expectations.
Challenges and Disadvantages of FMEA
While FMEA offers numerous advantages, it is essential to acknowledge and address potential challenges and drawbacks.
1. Time-Consuming Process
FMEA can be a time-intensive process, requiring significant resources for thorough analysis and documentation. However, the long-term benefits often outweigh the initial investment.
2. Requires Expertise
Effective implementation of FMEA necessitates a deep understanding of both the product and the manufacturing process. Training and expertise are crucial for accurate identification and assessment of failure modes.
3. Potential for Over-Engineering
There is a risk of over-engineering solutions when addressing potential failure modes. Striking the right balance between necessary improvements and overcomplication is essential.
Best Practices for Implementing FMEA in Japanese Manufacturing
To maximize the benefits of FMEA, Japanese manufacturers follow several best practices that have been refined through years of experience.
1. Cross-Functional Collaboration
FMEA is most effective when conducted with input from various departments, including design, engineering, production, and quality control. This collaborative approach ensures a comprehensive analysis.
2. Early Integration
Integrating FMEA in the initial stages of product development allows manufacturers to identify and address potential issues early. This proactive stance minimizes disruptions later in the process.
3. Continuous Review and Updates
FMEA is not a one-time exercise. Regular reviews and updates are essential to account for changes in processes, technologies, and market conditions. This dynamic approach maintains the relevance of the analysis.
4. Documentation and Training
Thorough documentation of FMEA findings and actions taken is crucial. Additionally, continuous training for employees ensures they stay proficient in applying FMEA principles.
Practical Insights from Japanese Manufacturing
Drawing from decades of experience in dealing with Japanese suppliers, several practical insights can be gleaned.
1. Emphasis on Preventive Measures
Japanese manufacturers prioritize preventive measures over reactive solutions. FMEA serves as a preventive tool, aligning perfectly with this philosophy.
2. Supplier Collaboration
Japanese companies often collaborate closely with their suppliers to implement FMEA. This partnership ensures that quality control measures are integrated throughout the supply chain.
3. Lean Manufacturing Principles
FMEA complements lean manufacturing principles, such as waste reduction and continuous improvement. This synergy enhances overall efficiency and quality.
Navigating Supplier Negotiations
Effectively negotiating with Japanese suppliers requires a deep understanding of their commitment to quality and their approach to FMEA.
1. Highlighting Mutual Benefits
Emphasize how implementing FMEA can mutually benefit both parties by improving product quality, reducing costs, and enhancing customer satisfaction.
2. Building Long-Term Relationships
Japanese business culture values long-term relationships built on trust and mutual respect. Demonstrating a commitment to quality through FMEA can strengthen these relationships.
3. Transparency and Communication
Maintaining open and transparent communication is crucial. Regular updates on FMEA findings and improvements build trust and ensure alignment with supplier expectations.
Conclusion: Achieving Success through FMEA in Japanese Manufacturing
Mastering quality control in Japanese manufacturing with FMEA is a journey towards excellence. By embracing this powerful tool, manufacturers can achieve higher product reliability, minimize costs, and build lasting customer trust.
The integration of FMEA into Japanese quality control practices exemplifies their unwavering commitment to perfection. As global market conditions continue to evolve, the lessons learned from Japanese manufacturing and their application of FMEA remain invaluable.
By adopting best practices, navigating supplier negotiations, and continually focusing on improvement, manufacturers worldwide can leverage FMEA to streamline success and maintain a competitive edge in the industry.
資料ダウンロード
QCD管理受発注クラウド「newji」は、受発注部門で必要なQCD管理全てを備えた、現場特化型兼クラウド型の今世紀最高の受発注管理システムとなります。
ユーザー登録
受発注業務の効率化だけでなく、システムを導入することで、コスト削減や製品・資材のステータス可視化のほか、属人化していた受発注情報の共有化による内部不正防止や統制にも役立ちます。
NEWJI DX
製造業に特化したデジタルトランスフォーメーション(DX)の実現を目指す請負開発型のコンサルティングサービスです。AI、iPaaS、および先端の技術を駆使して、製造プロセスの効率化、業務効率化、チームワーク強化、コスト削減、品質向上を実現します。このサービスは、製造業の課題を深く理解し、それに対する最適なデジタルソリューションを提供することで、企業が持続的な成長とイノベーションを達成できるようサポートします。
製造業ニュース解説
製造業、主に購買・調達部門にお勤めの方々に向けた情報を配信しております。
新任の方やベテランの方、管理職を対象とした幅広いコンテンツをご用意しております。
お問い合わせ
コストダウンが利益に直結する術だと理解していても、なかなか前に進めることができない状況。そんな時は、newjiのコストダウン自動化機能で大きく利益貢献しよう!
(β版非公開)