- お役立ち記事
- Mastering the Art of Anodizing: How Japanese OEMs are Revolutionizing the Manufacturing Industry
月間77,185名の
製造業ご担当者様が閲覧しています*
*2025年2月28日現在のGoogle Analyticsのデータより
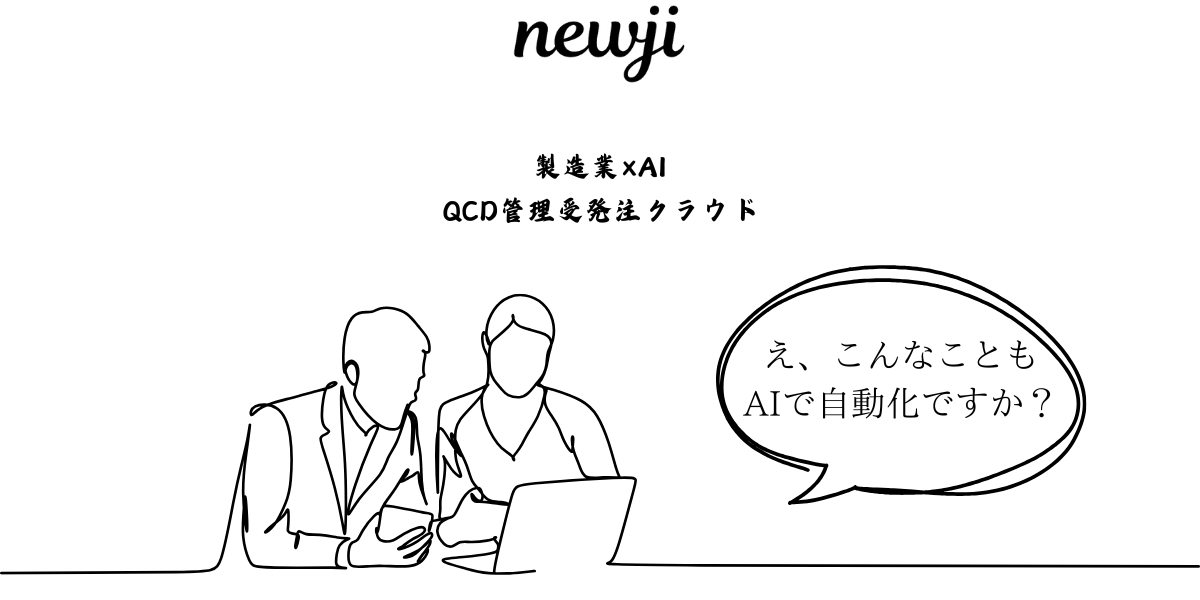
Mastering the Art of Anodizing: How Japanese OEMs are Revolutionizing the Manufacturing Industry
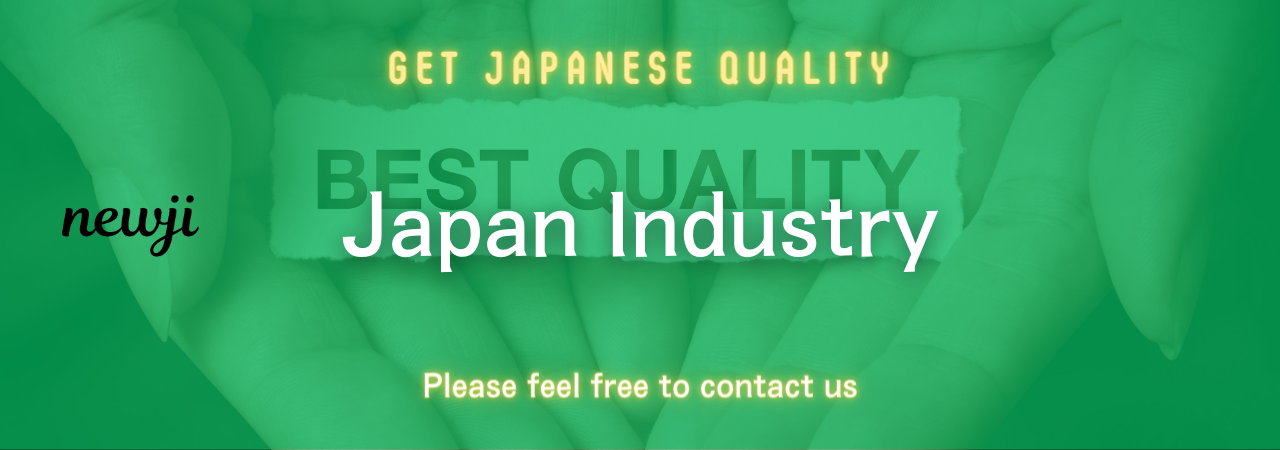
目次
Introduction to Anodizing
Anodizing is an electrochemical process that enhances the natural oxide layer on the surface of metal parts.
This process increases corrosion resistance and surface hardness, while also allowing for decorative finishes.
Anodizing is widely used in various industries, including automotive, aerospace, electronics, and consumer goods.
Understanding the intricacies of anodizing is crucial for manufacturers aiming to improve product quality and longevity.
The Role of Japanese OEMs in Revolutionizing Anodizing
Japanese Original Equipment Manufacturers (OEMs) have spearheaded advancements in anodizing techniques.
Their commitment to quality and innovation has set new standards in the manufacturing industry.
Japanese OEMs integrate precision engineering with advanced anodizing processes to deliver superior products.
This integration has significantly impacted global manufacturing practices, pushing competitors to elevate their standards.
Emphasis on Quality Control
Japanese OEMs prioritize stringent quality control measures in their anodizing processes.
They employ state-of-the-art technology to monitor and maintain consistency throughout production.
This focus ensures that anodized products meet high-performance requirements and aesthetic standards.
By maintaining rigorous quality checks, Japanese OEMs minimize defects and enhance customer satisfaction.
Innovation in Anodizing Technologies
Continuous innovation is a hallmark of Japanese OEMs in the anodizing sector.
They invest heavily in research and development to explore new techniques and materials.
Innovations include advancements in dyeing processes, sealing methods, and the use of environmentally friendly chemicals.
These technological breakthroughs contribute to more efficient and sustainable anodizing practices.
Integration of Automation and Precision Engineering
Automation plays a pivotal role in Japanese OEMs’ anodizing operations.
Automated systems ensure precise control over the anodizing process, leading to uniform results.
Precision engineering facilitates the production of complex and intricate designs with high accuracy.
The synergy between automation and precision engineering enhances overall manufacturing efficiency and product quality.
Advantages of Anodizing in Manufacturing
Anodizing offers numerous benefits that make it a preferred choice in various manufacturing applications.
Enhanced Corrosion Resistance
Anodizing significantly improves the corrosion resistance of metal parts.
The thickened oxide layer acts as a protective barrier against environmental factors such as moisture and chemicals.
This protection extends the lifespan of components, reducing the need for frequent replacements.
Enhanced corrosion resistance is particularly beneficial in industries exposed to harsh conditions.
Improved Surface Hardness
The anodizing process increases the surface hardness of metals.
This enhanced hardness makes parts more resistant to wear and abrasion.
As a result, anodized components maintain their integrity and functionality over prolonged use.
Improved surface hardness is essential for applications where durability is critical.
Aesthetic Appeal
Anodizing allows for a wide range of color options and finishes.
This versatility enables manufacturers to create visually appealing products that meet specific design requirements.
The ability to achieve consistent and vibrant colors enhances the marketability of anodized components.
Aesthetic appeal is a valuable asset in consumer-facing industries where product appearance influences purchasing decisions.
Environmentally Friendly Process
Anodizing is an environmentally friendly surface treatment method.
The process generates minimal waste and utilizes water-based solutions, reducing environmental impact.
Additionally, anodized coatings are inert and do not leach harmful substances during use.
Manufacturers seeking sustainable production methods find anodizing to be an ideal choice.
Disadvantages of Anodizing
While anodizing offers numerous benefits, it also presents certain challenges that manufacturers must address.
Initial Setup Costs
Establishing anodizing facilities requires significant initial investment.
Costs include purchasing specialized equipment, setting up controlled environments, and training personnel.
These upfront expenses can be a barrier for small to medium-sized enterprises looking to adopt anodizing.
Limited Material Compatibility
Anodizing is primarily effective on aluminum and its alloys.
Other metals, such as steel and titanium, are less suitable for anodizing processes.
This limitation restricts the applicability of anodizing to specific materials, influencing material selection in manufacturing.
Process Sensitivity
Anodizing is sensitive to various process parameters, including temperature, current density, and bath composition.
Minor deviations can result in inconsistent coating quality and potential defects.
Maintaining precise control over these parameters is essential, adding complexity to the anodizing process.
Surface Preparation Requirements
Effective anodizing necessitates thorough surface preparation to eliminate contaminants and oxidation.
This preparation involves cleaning, degreasing, and etching, which can be time-consuming and labor-intensive.
Inadequate surface preparation can compromise coating adhesion and overall product quality.
Supplier Negotiation Techniques in Anodizing Procurement
Negotiating with suppliers is a critical aspect of procurement in the anodizing sector.
Effective negotiation techniques can lead to better pricing, improved quality, and stronger supplier relationships.
Establishing Clear Requirements
Before engaging with suppliers, define clear specifications for anodized products.
This includes material types, coating thickness, color preferences, and performance criteria.
Clear requirements facilitate precise communication and help suppliers understand expectations.
Building Strong Relationships
Fostering strong relationships with anodizing suppliers is essential for long-term success.
Open communication, mutual trust, and collaborative problem-solving enhance partnership effectiveness.
Strong relationships can lead to preferential treatment, such as priority production scheduling and favorable terms.
Leveraging Bulk Purchasing
Negotiating bulk purchasing agreements can result in cost savings and favorable pricing structures.
By committing to larger order volumes, manufacturers can secure discounts and better payment terms.
Bulk purchasing also ensures a consistent supply of anodized components, enhancing production stability.
Requesting Competitive Bids
Soliciting competitive bids from multiple suppliers fosters a competitive environment.
This approach encourages suppliers to offer their best prices and terms to win contracts.
Comparing bids provides insights into market rates and helps identify the most advantageous offers.
Understanding Supplier Capabilities
Assessing the capabilities and reliability of potential suppliers is crucial during negotiations.
Evaluate factors such as production capacity, quality control measures, and industry reputation.
Choosing suppliers with proven track records ensures consistent quality and timely delivery of anodized products.
Market Conditions Affecting Anodizing Procurement
Various market conditions influence the procurement process for anodized components.
Understanding these factors helps manufacturers make informed purchasing decisions.
Supply and Demand Dynamics
Fluctuations in supply and demand impact the availability and pricing of anodizing services.
High demand can lead to increased prices and longer lead times, while oversupply may result in competitive pricing.
Monitoring market trends allows manufacturers to anticipate changes and adjust procurement strategies accordingly.
Raw Material Availability
The availability of raw materials, such as aluminum, affects anodizing production and costs.
Scarcity or increased costs of aluminum can lead to higher prices for anodized products.
Manufacturers must consider raw material sourcing and explore alternatives to mitigate supply risks.
Technological Advancements
Advancements in anodizing technologies influence market competitiveness and procurement options.
Innovative processes can enhance efficiency, reduce costs, and improve product quality.
Staying updated on technological developments enables manufacturers to leverage new opportunities in the market.
Regulatory Environment
Compliance with environmental and industry regulations is essential in the anodizing sector.
Regulations may govern the use of specific chemicals, waste disposal methods, and emission standards.
Understanding and adhering to these regulations ensures legal compliance and avoids potential penalties.
Global Economic Factors
Global economic conditions, such as exchange rates and trade policies, affect procurement decisions.
Currency fluctuations can influence the cost of imported anodizing services, while trade agreements may impact tariffs and duties.
Manufacturers need to factor in economic variables when planning procurement strategies for anodized components.
Best Practices in Anodizing Procurement and Purchasing
Adopting best practices in procurement and purchasing enhances efficiency and ensures the acquisition of high-quality anodized products.
Comprehensive Supplier Evaluation
Conduct thorough evaluations of potential anodizing suppliers before making purchasing decisions.
Consider factors such as quality certifications, production capabilities, delivery reliability, and financial stability.
A comprehensive evaluation process helps identify suppliers that align with the manufacturer’s requirements and standards.
Establishing Clear Communication Channels
Maintain open and transparent communication with anodizing suppliers throughout the procurement process.
Clearly articulate expectations, specifications, and deadlines to prevent misunderstandings and ensure smooth collaboration.
Effective communication fosters a cooperative environment and facilitates prompt resolution of any issues that arise.
Implementing Quality Assurance Protocols
Develop and implement robust quality assurance protocols for anodized products.
This includes regular inspections, testing procedures, and adherence to industry standards.
Quality assurance ensures that anodized components meet the desired performance and durability criteria.
Negotiating Favorable Contracts
Secure favorable contract terms with anodizing suppliers through strategic negotiations.
Include clauses that address pricing, payment terms, delivery schedules, and quality standards.
Well-structured contracts protect the interests of both parties and provide a clear framework for the business relationship.
Diversifying Supplier Base
Diversify the supplier base to reduce dependency on a single anodizing provider.
Having multiple suppliers ensures a stable supply of anodized products and mitigates risks associated with supplier disruptions.
Diversification also provides flexibility in negotiating better terms and facilitates access to a broader range of technologies and expertise.
Monitoring Market Trends
Stay informed about market trends and developments in the anodizing industry.
Regularly review industry reports, attend trade shows, and engage with industry experts to gather insights.
Monitoring market trends enables manufacturers to anticipate changes and adapt procurement strategies to maintain a competitive edge.
Investing in Supplier Relationships
Invest time and resources in building strong relationships with anodizing suppliers.
Engage in regular meetings, provide feedback, and collaborate on continuous improvement initiatives.
Strong supplier relationships lead to enhanced cooperation, innovation, and mutual growth opportunities.
Utilizing Technology in Procurement
Leverage technology to streamline the procurement process for anodized products.
Implement procurement management systems, use data analytics for informed decision-making, and automate routine tasks.
Technology integration enhances efficiency, reduces errors, and provides valuable insights into procurement activities.
Conclusion
Mastering the art of anodizing is pivotal for manufacturers aiming to produce high-quality, durable, and aesthetically pleasing products.
Japanese OEMs have been at the forefront of revolutionizing the manufacturing industry through their innovative anodizing practices.
By emphasizing quality control, embracing technological advancements, and fostering strong supplier relationships, Japanese manufacturers set exemplary standards.
While anodizing presents certain challenges, such as initial setup costs and process sensitivity, the advantages it offers in terms of corrosion resistance, surface hardness, and environmental sustainability make it a compelling choice.
Effective procurement and purchasing strategies, including clear communication, comprehensive supplier evaluation, and leveraging technological tools, are essential for successfully integrating anodizing into manufacturing processes.
Understanding market conditions and adopting best practices further enhance the efficiency and effectiveness of anodizing procurement.
As the manufacturing landscape continues to evolve, mastering anodizing will remain a key factor in achieving excellence and maintaining a competitive edge in the industry.
資料ダウンロード
QCD管理受発注クラウド「newji」は、受発注部門で必要なQCD管理全てを備えた、現場特化型兼クラウド型の今世紀最高の受発注管理システムとなります。
ユーザー登録
受発注業務の効率化だけでなく、システムを導入することで、コスト削減や製品・資材のステータス可視化のほか、属人化していた受発注情報の共有化による内部不正防止や統制にも役立ちます。
NEWJI DX
製造業に特化したデジタルトランスフォーメーション(DX)の実現を目指す請負開発型のコンサルティングサービスです。AI、iPaaS、および先端の技術を駆使して、製造プロセスの効率化、業務効率化、チームワーク強化、コスト削減、品質向上を実現します。このサービスは、製造業の課題を深く理解し、それに対する最適なデジタルソリューションを提供することで、企業が持続的な成長とイノベーションを達成できるようサポートします。
製造業ニュース解説
製造業、主に購買・調達部門にお勤めの方々に向けた情報を配信しております。
新任の方やベテランの方、管理職を対象とした幅広いコンテンツをご用意しております。
お問い合わせ
コストダウンが利益に直結する術だと理解していても、なかなか前に進めることができない状況。そんな時は、newjiのコストダウン自動化機能で大きく利益貢献しよう!
(β版非公開)