- お役立ち記事
- Mastering the Art of Flow Coat in Japanese Manufacturing: Achieving Perfect Surface Finishes
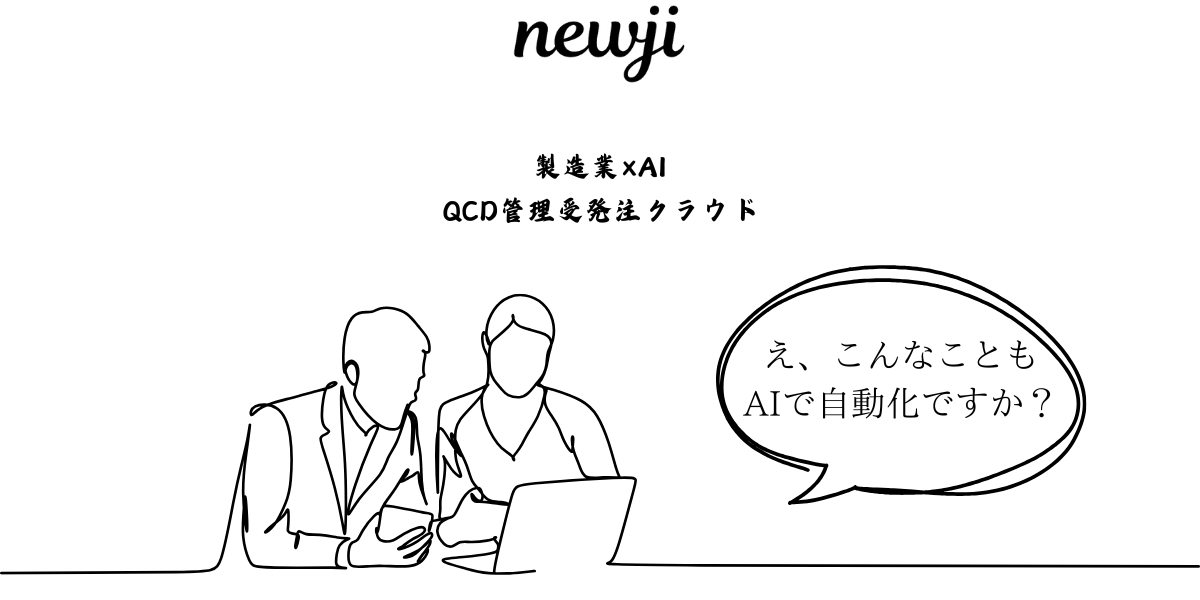
Mastering the Art of Flow Coat in Japanese Manufacturing: Achieving Perfect Surface Finishes
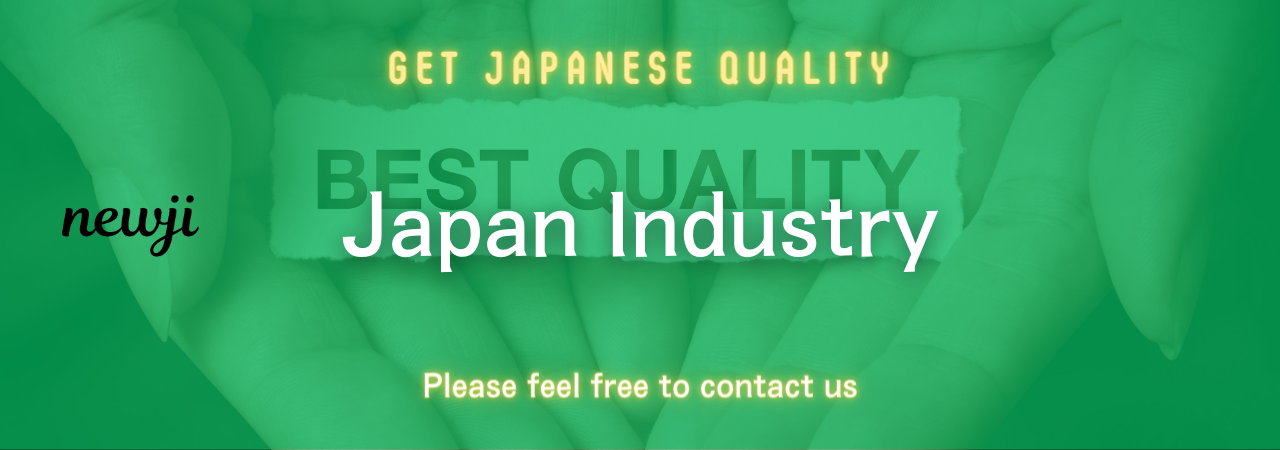
Flow coating is an indispensable technique in the realm of Japanese manufacturing, revered for its ability to achieve impeccable surface finishes. This article explores the nuanced art of flow coating, delving into practical insights, market conditions, and best practices from years of experience in international procurement and purchasing.
目次
The Essence of Flow Coating
Flow coating involves the controlled flow of a liquid finishing material over a substrate, which then allows excess material to drain away, leaving a perfectly coated surface.
Unlike traditional methods like spray coating or dip coating, flow coating offers enhanced uniformity and a superior finish, which is why it is heavily employed in high-precision sectors such as automotive, electronics, and aerospace manufacturing.
Advantages of Flow Coating
Flow coating has several significant advantages.
Firstly, uniformity is perhaps its greatest strength.
Given that the coating material uniformly flows across the surface and then drains, it ensures a smooth, even layer, minimizing imperfections.
Secondly, it is highly efficient.
Flow coating reduces material wastage compared to spray coating, where overspray can be a significant issue.
Thirdly, it offers environmental benefits.
Reduced wastage translates to fewer volatile organic compounds (VOCs) being released into the atmosphere, making it a more environmentally friendly option.
Moreover, collected excess material can often be filtered and reused, contributing to sustainability.
Lastly, flow coating systems can be automated with relative ease.
Automation enhances consistency, reduces labor costs, and improves throughput, making it a crucial option for mass production operations.
Disadvantages of Flow Coating
Despite its numerous advantages, flow coating is not without challenges.
Initial setup costs can be high.
The equipment used for flow coating, such as pumps, tanks, and drying ovens, can require a substantial upfront investment, which may be a barrier for smaller enterprises.
The process also requires a high level of control.
Any variations in the viscosity of the coating material, flow rate, or substrate surface can lead to defects such as runs or sags.
This necessitates strict quality control measures.
Additionally, it is primarily suitable for flat or very gently curved surfaces. Complex geometries can present significant challenges, often necessitating additional equipment or methods to ensure proper coverage.
Supplier Negotiation Techniques
When dealing with Japanese suppliers for flow coating materials or equipment, it is essential to comprehend the cultural nuances and market conditions to negotiate effectively.
Understanding Market Dynamics
Japan’s manufacturing sector is known for its emphasis on quality and innovation.
Suppliers often invest heavily in R&D, leading to the availability of cutting-edge technology and materials.
However, this also means that costs can be higher compared to suppliers from other regions.
Seasonal fluctuations and economic conditions also play a role.
For instance, the demand for automotive coatings typically spikes in conjunction with new model releases.
Keeping track of these market dynamics can give you leverage during negotiations.
Building Strong Relationships
In Japanese business culture, relationship-building is crucial.
Forming strong ties with your suppliers can lead to better terms and superior service.
Regular face-to-face meetings, respect for formalities, and demonstrating a long-term commitment can significantly enhance your negotiation position.
It’s also important to be patient.
Negotiations in Japan can be slow and meticulous, driven by a desire for mutual benefit and understanding.
Hastening the process can be perceived as disrespectful and counterproductive.
Technical Discussions
When negotiating, be prepared to engage in detailed technical discussions.
Japanese suppliers appreciate buyers who have a deep understanding of the products and processes.
This not only shows respect but also assures them that you value quality and are looking for a long-term partnership, not just the lowest price.
Best Practices in Flow Coating
Achieving optimal results with flow coating involves adhering to several best practices.
Material Selection
Start by selecting the right coating material.
The resin type, viscosity, and curing mechanism must align with the intended application and substrate.
Working closely with your supplier can help identify the most suitable materials.
Pre-Treatment
Surface preparation is critical.
Any contaminants like dust, grease, or moisture can interfere with the coating’s adhesion and finish.
Standard pre-treatment methods include cleaning, degreasing, and applying a primer layer.
Process Control
Maintaining consistent control over the process parameters is essential.
This includes monitoring the material’s viscosity, flow rate, ambient conditions, and the substrate’s temperature.
Automation can significantly aid in maintaining these parameters within optimal ranges.
Drying and Curing
Proper drying and curing are vital to the coating’s final properties.
Ensure that the ovens or curing chambers are calibrated correctly to provide uniform heat distribution and avoid any thermal shocks that could lead to defects.
Supplier Considerations for Optimal Flow Coating
Selecting the right supplier for your flow coating needs can vastly impact the quality and efficiency of your operations.
Here are some key considerations.
Reputation and Experience
Look for suppliers with a solid reputation and extensive experience in the industry.
Suppliers who have worked with high-profile clients in demanding sectors are more likely to provide reliable products and support.
Technical Support
Choose suppliers who offer robust technical support.
This can include assistance with setup, maintenance training, and troubleshooting.
Suppliers who provide comprehensive service can help minimize downtime and operational disruptions.
Quality Control
Ensure that your supplier has stringent quality control measures in place.
This extends beyond the finished product to encompass raw material sourcing and manufacturing processes.
Requesting quality certifications and audit reports can provide reassurance.
Flexibility and Customization
Opt for suppliers who can offer customized solutions tailored to your specific needs.
This flexibility can be particularly beneficial if you have unique requirements or are working on innovative projects.
Future Trends in Flow Coating
The landscape of flow coating is continually evolving, driven by advancements in technology and changes in market demands.
Digital Integration
Increasingly, flow coating systems are being integrated with digital technologies.
Smart sensors and IoT connectivity can provide real-time data on process parameters, enabling predictive maintenance and enhanced quality control.
This trend is expected to continue growing as manufacturers seek greater precision and efficiency.
Environmental Considerations
There is a rising emphasis on eco-friendly coatings.
Water-based coatings and low-VOC formulations are gaining traction as regulatory standards become more stringent and consumers demand more sustainable products.
Investing in such options can not only ensure compliance but also serve as a mark of corporate responsibility.
Automation and Robotics
Automation is becoming more sophisticated with the integration of robotics in flow coating processes.
Robots can ensure consistent application, reduce human error, and handle complex geometries more effectively.
Automation also enhances safety by limiting human exposure to potentially hazardous materials.
Advanced Materials
The development of advanced materials, such as nanocoatings, offers exciting possibilities for flow coating.
These materials can provide superior performance characteristics, including enhanced durability, corrosion resistance, and self-cleaning properties, thereby opening new application avenues.
Conclusion
Mastering the art of flow coating in Japanese manufacturing involves understanding its advantages and limitations, effectively negotiating with suppliers, and following industry best practices.
As you integrate this technique into your operations, leveraging the expertise of Japanese suppliers and staying abreast of future trends can significantly enhance your outcomes.
Ultimately, a well-implemented flow coating process can lead to superior product quality, operational efficiency, and increased market competitiveness.
資料ダウンロード
QCD調達購買管理クラウド「newji」は、調達購買部門で必要なQCD管理全てを備えた、現場特化型兼クラウド型の今世紀最高の購買管理システムとなります。
ユーザー登録
調達購買業務の効率化だけでなく、システムを導入することで、コスト削減や製品・資材のステータス可視化のほか、属人化していた購買情報の共有化による内部不正防止や統制にも役立ちます。
NEWJI DX
製造業に特化したデジタルトランスフォーメーション(DX)の実現を目指す請負開発型のコンサルティングサービスです。AI、iPaaS、および先端の技術を駆使して、製造プロセスの効率化、業務効率化、チームワーク強化、コスト削減、品質向上を実現します。このサービスは、製造業の課題を深く理解し、それに対する最適なデジタルソリューションを提供することで、企業が持続的な成長とイノベーションを達成できるようサポートします。
オンライン講座
製造業、主に購買・調達部門にお勤めの方々に向けた情報を配信しております。
新任の方やベテランの方、管理職を対象とした幅広いコンテンツをご用意しております。
お問い合わせ
コストダウンが利益に直結する術だと理解していても、なかなか前に進めることができない状況。そんな時は、newjiのコストダウン自動化機能で大きく利益貢献しよう!
(Β版非公開)