- お役立ち記事
- Mastering the Art of Grinding: Unveiling Japan’s Precision Manufacturing Techniques
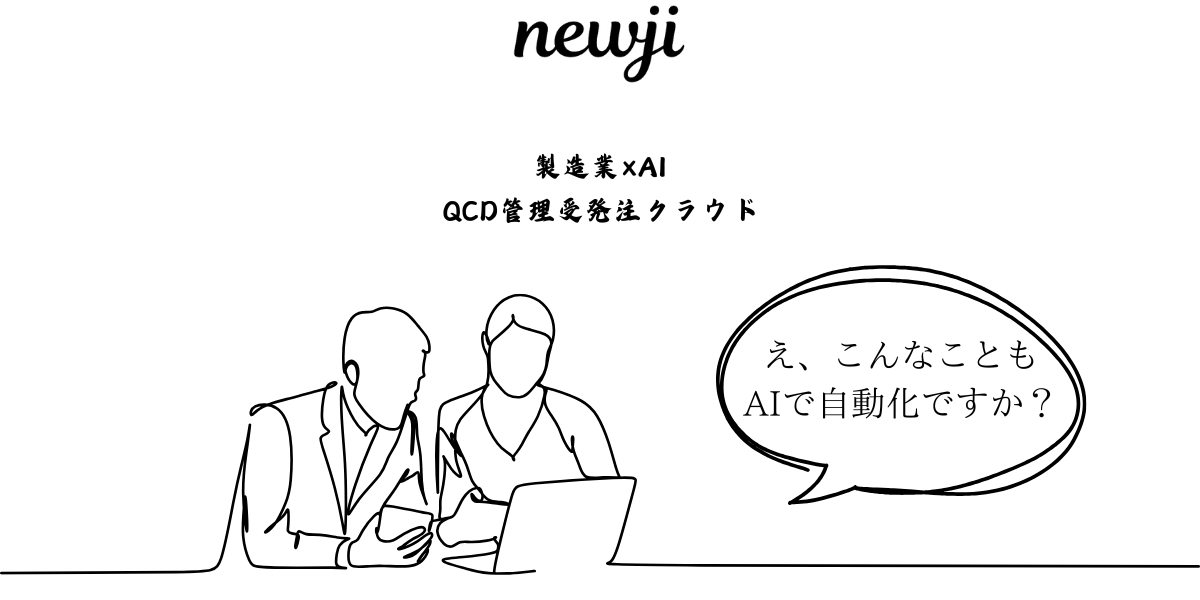
Mastering the Art of Grinding: Unveiling Japan’s Precision Manufacturing Techniques
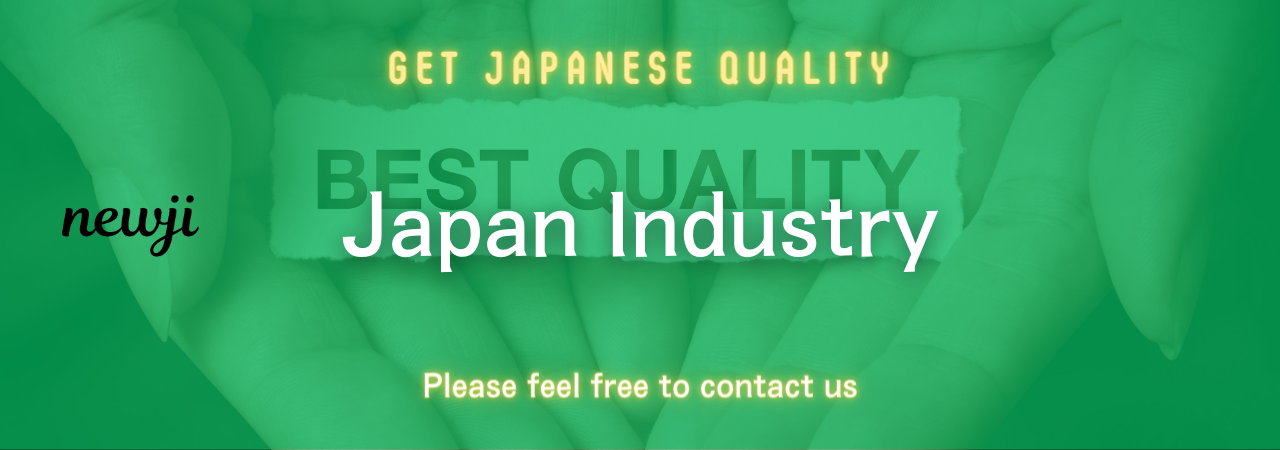
目次
Understanding Grinding in Japan’s Manufacturing
Japan has long been recognized as a global leader in precision manufacturing. Central to this reputation is the mastery of grinding techniques, which are essential for producing components with exacting specifications. Grinding, a material removal process, plays a critical role in achieving the high dimensional accuracy and surface finish that Japanese products are renowned for. This section delves into the history, evolution, and key technologies that underpin Japan’s expertise in grinding.
History and Evolution
The roots of Japan’s precision manufacturing can be traced back to the country’s post-war industrial boom. Faced with the challenge of rebuilding its economy, Japan invested heavily in developing advanced manufacturing techniques. Grinding technology was a focal point, as it enabled the production of high-precision components necessary for industries such as automotive, aerospace, and electronics.
Over the decades, Japanese manufacturers have continually refined grinding processes, integrating innovations that enhance efficiency and precision. The adoption of computer numerical control (CNC) machines, advancements in abrasive materials, and the incorporation of automation have transformed grinding from a manual craft into a sophisticated, high-tech operation.
Key Technologies and Techniques
Japanese precision manufacturing leverages several cutting-edge technologies in grinding, including:
– **CNC Grinding Machines:** These machines offer unparalleled control over the grinding process, allowing for the production of complex shapes with tight tolerances.
– **Superabrasive Wheels:** Utilization of diamonds and cubic boron nitride (CBN) in grinding wheels enhances material removal rates and surface finishes.
– **In-process Measurement Systems:** Real-time monitoring and feedback systems ensure that each component meets stringent quality standards.
– **Automation and Robotics:** Integration of automated systems reduces human error and increases production efficiency.
These technologies collectively enable Japanese manufacturers to maintain high standards of precision and consistency in their products.
Advantages
Partnering with Japanese precision manufacturers offers numerous advantages. This section explores the key benefits, including quality, efficiency, and innovation, that make Japanese suppliers highly sought after in the global market.
High Quality and Precision
Japanese manufacturers prioritize quality at every stage of the production process. Rigorous quality control systems, adherence to international standards, and a culture of continuous improvement ensure that components meet exacting specifications. Precision grinding techniques facilitate the production of components with minimal tolerances, which is essential for industries where performance and reliability are paramount.
Efficiency and Automation
Efficiency is a hallmark of Japanese manufacturing. The integration of automation and advanced machinery reduces production times and minimizes waste. Automated grinding systems ensure consistent performance, while real-time monitoring allows for immediate adjustments, enhancing overall productivity. This focus on efficiency not only lowers costs but also accelerates time-to-market for products.
Innovation and Continuous Improvement
Japanese companies are renowned for their commitment to innovation and the principle of “Kaizen,” or continuous improvement. In the realm of grinding, this translates to ongoing research and development aimed at refining techniques, improving machine capabilities, and developing new materials. Such innovation ensures that Japanese manufacturers stay at the forefront of precision manufacturing technology.
Disadvantages
While there are significant advantages to procuring from Japanese suppliers, there are also challenges that businesses must navigate. This section examines the potential drawbacks, including cost considerations, cultural barriers, and supply chain dependencies.
Cost Considerations
Japanese precision manufacturing is often associated with higher costs compared to competitors from other regions. The high level of craftsmanship, advanced technology, and stringent quality control contribute to increased production expenses. While the initial investment may be higher, the long-term benefits of superior quality and reduced defect rates can offset these costs.
Cultural and Communication Barriers
Cultural differences can pose challenges in business interactions. Japanese business culture emphasizes formality, respect, and indirect communication, which may differ from Western business practices. Misunderstandings can arise if these cultural nuances are not acknowledged and respected. Effective communication strategies and cultural sensitivity are essential for successful collaborations.
Supply Chain Dependence
Relying heavily on Japanese suppliers can introduce vulnerabilities in the supply chain. Factors such as geopolitical tensions, natural disasters, or global economic fluctuations can disrupt the availability of critical components. Diversifying supply sources and developing contingency plans are necessary strategies to mitigate these risks.
Procurement Strategies
Effective procurement strategies are crucial for maximizing the benefits of partnering with Japanese precision manufacturers. This section outlines key approaches, including supplier selection, negotiation techniques, and relationship building, that facilitate successful procurement.
Supplier Selection
Selecting the right supplier is the foundation of a successful procurement strategy. Criteria for selection should include the supplier’s technical capabilities, quality certifications, production capacity, and track record of reliability. Conducting thorough due diligence, including site visits and performance evaluations, helps in identifying suppliers that align with your company’s standards and requirements.
Negotiation Techniques
Negotiating with Japanese suppliers requires an understanding of their business culture and values. Emphasize long-term partnerships over short-term gains, and approach negotiations with patience and respect. Highlight mutual benefits and demonstrate a commitment to quality and reliability. Building trust is essential, as Japanese suppliers are more inclined to offer favorable terms to partners they view as reliable and respectful.
Building Long-term Relationships
Long-term relationships are highly valued in Japanese business culture. Investing time in developing strong, trust-based relationships with suppliers can lead to better collaboration, preferred pricing, and priority in production. Regular communication, visits, and collaborative problem-solving initiatives reinforce these relationships and ensure ongoing alignment of objectives.
Best Practices
Adhering to best practices when engaging with Japanese suppliers enhances the effectiveness of procurement efforts. This section provides actionable guidelines on understanding business culture, effective communication, and quality assurance.
Understanding Japanese Business Culture
A deep understanding of Japanese business etiquette is essential. This includes appropriate greeting protocols, respecting hierarchy, and demonstrating patience in negotiations. Familiarize yourself with concepts such as “Nemawashi” (informal consensus-building) and “Wa” (harmony), which emphasize the importance of collaborative decision-making and maintaining positive relationships.
Effective Communication
Clear and respectful communication is paramount. Utilize professional translators or bilingual staff if necessary to bridge language gaps. Be explicit about requirements and expectations, and ensure that all specifications are clearly documented. Regular meetings and updates help maintain transparency and prevent misunderstandings.
Quality Control and Assurance
Implement stringent quality control measures to ensure that supplied components meet your standards. Collaborate with suppliers to establish quality benchmarks and conduct regular audits. Utilize in-process measurement systems and feedback loops to identify and address any deviations promptly, ensuring consistency and reliability in the final products.
Market Conditions
Understanding the current market conditions and trends in precision manufacturing is vital for strategic procurement. This section explores the prevailing trends, the impact of global supply chain dynamics, and how these factors influence procurement decisions.
Current Trends in Precision Manufacturing
The precision manufacturing sector is witnessing several key trends, including the adoption of Industry 4.0 technologies, increased focus on sustainability, and the integration of artificial intelligence (AI) and machine learning in production processes. These advancements drive improvements in efficiency, accuracy, and adaptability, enabling manufacturers to meet the evolving demands of various industries.
Impact of Global Supply Chain Dynamics
Global supply chains are increasingly influenced by factors such as geopolitical tensions, trade policies, and technological advancements. The recent disruptions caused by the COVID-19 pandemic have underscored the importance of supply chain resilience and diversification. Japanese manufacturers are adapting by enhancing their supply chain transparency, investing in local production capabilities, and forming strategic alliances to mitigate risks and maintain consistent supply.
Case Studies
Analyzing real-world examples provides valuable insights into effective procurement practices and the benefits of engaging with Japanese precision manufacturers. This section presents case studies highlighting successful collaborations and the lessons learned from these experiences.
Successful Procurement from Japanese Grinder Manufacturers
One notable case involves a leading automotive company that partnered with a Japanese grinding equipment manufacturer to enhance its production capabilities. By leveraging the supplier’s advanced CNC grinding machines and expertise, the automotive company achieved significant improvements in component precision and reduction in production lead times. The collaboration led to enhanced product quality and a competitive edge in the market.
Lessons Learned
Key takeaways from this case include the importance of thorough supplier evaluation, the benefits of investing in long-term relationships, and the value of integrating advanced technologies. Additionally, the case underscores the need for clear communication and collaborative problem-solving to overcome challenges and achieve mutual success.
Conclusion
Mastering the art of grinding through Japan’s precision manufacturing techniques offers substantial benefits for businesses seeking high-quality components and advanced manufacturing solutions. The combination of superior quality, efficiency, and continuous innovation positions Japanese suppliers as valuable partners in the global market. However, navigating the associated challenges, such as higher costs and cultural differences, requires strategic procurement approaches and a commitment to building strong, long-term relationships.
By understanding the nuances of Japanese business culture, implementing effective communication strategies, and adhering to best practices in quality control, businesses can unlock the full potential of Japan’s precision manufacturing capabilities. Staying informed about current market trends and maintaining supply chain resilience further enhances the advantages of sourcing from Japanese suppliers. Embracing these strategies not only ensures the acquisition of top-tier components but also fosters collaborative partnerships that drive sustained success in the competitive landscape of global manufacturing.
資料ダウンロード
QCD調達購買管理クラウド「newji」は、調達購買部門で必要なQCD管理全てを備えた、現場特化型兼クラウド型の今世紀最高の購買管理システムとなります。
ユーザー登録
調達購買業務の効率化だけでなく、システムを導入することで、コスト削減や製品・資材のステータス可視化のほか、属人化していた購買情報の共有化による内部不正防止や統制にも役立ちます。
NEWJI DX
製造業に特化したデジタルトランスフォーメーション(DX)の実現を目指す請負開発型のコンサルティングサービスです。AI、iPaaS、および先端の技術を駆使して、製造プロセスの効率化、業務効率化、チームワーク強化、コスト削減、品質向上を実現します。このサービスは、製造業の課題を深く理解し、それに対する最適なデジタルソリューションを提供することで、企業が持続的な成長とイノベーションを達成できるようサポートします。
オンライン講座
製造業、主に購買・調達部門にお勤めの方々に向けた情報を配信しております。
新任の方やベテランの方、管理職を対象とした幅広いコンテンツをご用意しております。
お問い合わせ
コストダウンが利益に直結する術だと理解していても、なかなか前に進めることができない状況。そんな時は、newjiのコストダウン自動化機能で大きく利益貢献しよう!
(Β版非公開)