- お役立ち記事
- Mastering the Art of High-Pressure Heat Lamination: The Japanese Secret to Superior Manufacturing
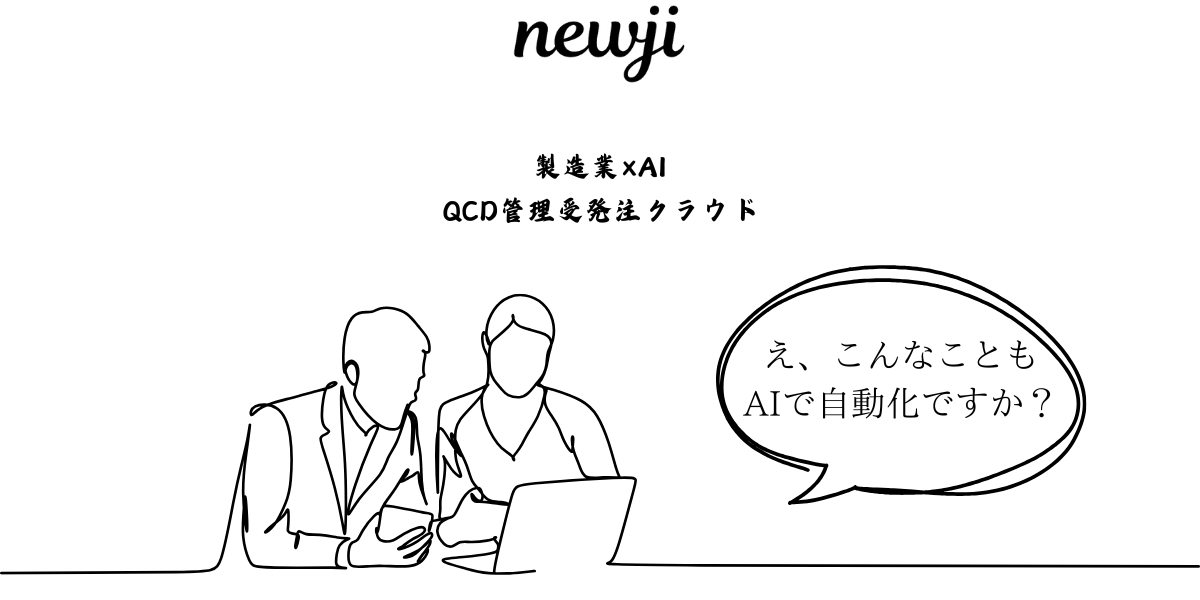
Mastering the Art of High-Pressure Heat Lamination: The Japanese Secret to Superior Manufacturing
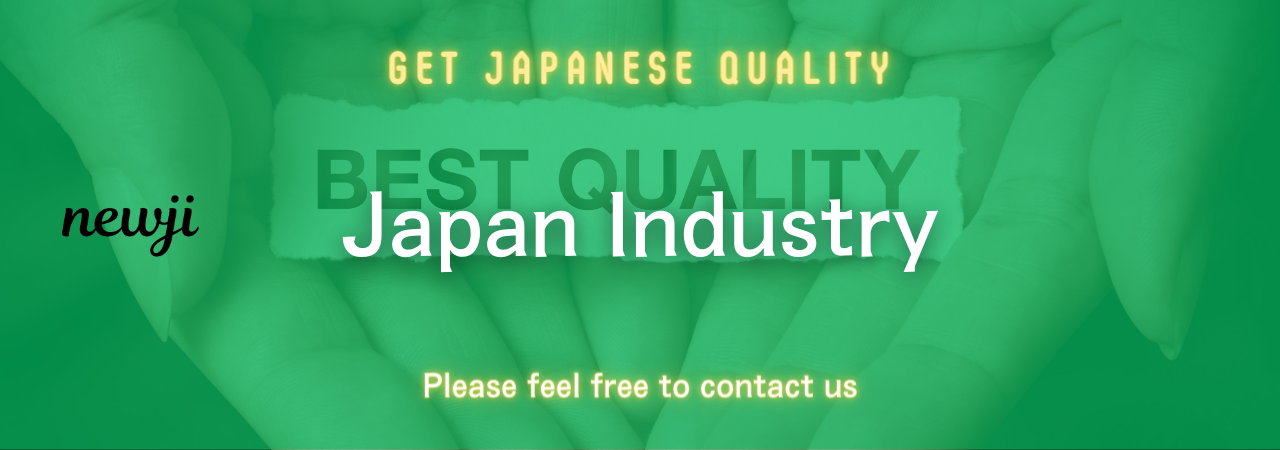
目次
Introduction to High-Pressure Heat Lamination
High-pressure heat lamination is a critical process in modern manufacturing, enhancing product durability, appearance, and functionality. Originating from advanced manufacturing techniques, this method involves applying heat and pressure to bond layers of materials together seamlessly. Japanese manufacturers have perfected this art, leveraging precision engineering and meticulous quality control to achieve superior results. This article delves into the intricacies of high-pressure heat lamination, exploring its advantages, disadvantages, supplier negotiation techniques, market conditions, and best practices, particularly from the perspective of procurement and purchasing in the Japanese manufacturing sector.
The Fundamentals of High-Pressure Heat Lamination
What is High-Pressure Heat Lamination?
High-pressure heat lamination is a process where layers of material, such as plastics, metals, or composites, are bonded together under controlled heat and pressure. This technique ensures a strong, uniform bond, enhancing the structural integrity and aesthetic appeal of the final product. Common applications include automotive parts, electronics, packaging, and textiles.
Key Components and Equipment
The high-pressure heat lamination process requires specialized equipment that can precisely control temperature, pressure, and timing. Key components include:
– **Heat Press Machines:** These apply consistent heat and pressure across the material layers.
– **Control Systems:** Advanced control systems allow for precise adjustments to temperature and pressure settings.
– **Material Feed Systems:** Automated systems ensure the consistent delivery of material layers into the lamination process.
The Japanese Secret to Superior Manufacturing
Precision Engineering
Japanese manufacturers are renowned for their precision engineering. This meticulous attention to detail ensures that each layer in the lamination process is perfectly aligned, minimizing defects and maximizing the strength of the bond. Precision engineering extends to the maintenance and calibration of lamination equipment, ensuring consistent performance and longevity.
Lean Manufacturing Principles
Adopting lean manufacturing principles, Japanese companies focus on minimizing waste and maximizing efficiency. In high-pressure heat lamination, this translates to optimized material usage, reduced energy consumption, and streamlined production processes. Continuous improvement (Kaizen) is a fundamental aspect, encouraging ongoing enhancements in quality and efficiency.
Quality Control and Assurance
Stringent quality control measures are integral to Japanese manufacturing. During high-pressure heat lamination, multiple inspection points ensure that each product meets exacting standards. From material selection to final product inspection, every step is monitored to maintain consistency and reliability.
Advantages of High-Pressure Heat Lamination
Enhanced Product Durability
One of the primary benefits of high-pressure heat lamination is the significant increase in product durability. The strong bonds created through this process ensure that products can withstand physical stresses, environmental factors, and prolonged use without degradation.
Improved Aesthetic Appeal
High-pressure heat lamination results in smooth, uniform surfaces that enhance the visual appeal of products. This is particularly important in consumer goods, where aesthetics play a crucial role in market acceptance and brand perception.
Increased Efficiency in Production
By streamlining the lamination process, manufacturers can achieve higher production speeds without compromising quality. Automation and precise control systems reduce manual intervention, minimizing errors and increasing overall efficiency.
Versatility in Applications
The high-pressure heat lamination process is versatile, accommodating a wide range of materials and applications. Whether it’s bonding different types of plastics, metals, or composites, this method can be adapted to suit diverse manufacturing needs.
Disadvantages and Challenges
High Initial Investment
Setting up a high-pressure heat lamination process requires substantial initial investment in specialized equipment and training. For small to medium-sized enterprises, this can be a significant barrier to entry.
Energy Consumption
The process involves considerable energy usage due to the need for maintaining high temperatures and consistent pressure. This can lead to increased operational costs and environmental impact if not managed efficiently.
Complex Maintenance Requirements
Maintaining the precision and reliability of lamination equipment demands regular maintenance and calibration. This requires skilled technicians and can result in additional operational costs.
Material Limitations
Not all materials are suitable for high-pressure heat lamination. Some materials may degrade under high temperatures or may not bond effectively under pressure, limiting the process’s applicability in certain scenarios.
Supplier Negotiation Techniques
Building Strong Relationships
In Japanese business culture, building long-term relationships with suppliers is paramount. Trust and mutual respect are foundational, leading to more favorable negotiation outcomes and reliable supply chains.
Understanding Supplier Capabilities
A deep understanding of a supplier’s technical capabilities and production processes is essential. This knowledge allows for more informed negotiations, ensuring that suppliers can meet quality standards and delivery schedules.
Leveraging Volume and Commitment
Committing to higher order volumes or long-term contracts can provide leverage in negotiations. Suppliers may offer better pricing, priority production slots, or enhanced support in exchange for guaranteed business.
Emphasizing Quality and Consistency
Japanese manufacturers prioritize quality and consistency. Highlighting these priorities during negotiations ensures that suppliers understand the importance of maintaining high standards, thereby aligning their capabilities with your expectations.
Implementing Transparent Communication
Clear and transparent communication is crucial in negotiations. Establishing open lines of dialogue helps prevent misunderstandings and fosters a collaborative environment where both parties can work towards mutually beneficial agreements.
Market Conditions and Trends
Technological Advancements
Advancements in materials science and automation are continually evolving the high-pressure heat lamination landscape. Staying abreast of these trends allows manufacturers to adopt cutting-edge techniques, enhancing product quality and production efficiency.
Global Supply Chain Dynamics
Global supply chain fluctuations, influenced by geopolitical events and economic shifts, impact the availability and cost of materials used in lamination. Japanese suppliers, known for their resilience and adaptability, are well-positioned to navigate these challenges.
Sustainability and Environmental Concerns
There is a growing emphasis on sustainable manufacturing practices. High-pressure heat lamination processes are being optimized to reduce energy consumption and waste, aligning with global sustainability goals.
Customization and Flexibility
Market demand is shifting towards more customized and flexible manufacturing solutions. High-pressure heat lamination processes are being adapted to accommodate smaller production runs and bespoke product requirements without sacrificing efficiency.
Best Practices in High-Pressure Heat Lamination
Material Selection and Preparation
Choosing the right materials is crucial for successful lamination. Factors such as thermal resistance, compatibility, and mechanical properties must be considered. Proper preparation, including cleaning and surface treatment, ensures optimal bonding.
Precision in Process Control
Maintaining precise control over temperature, pressure, and timing is essential. Automated control systems should be calibrated regularly to ensure consistent process parameters, reducing variability and enhancing product quality.
Regular Equipment Maintenance
Preventive maintenance schedules help maintain equipment performance and extend its lifespan. Regular inspections and timely repairs prevent unexpected downtimes and ensure continuous production flow.
Training and Skill Development
Investing in employee training ensures that the workforce is proficient in operating sophisticated lamination equipment. Skilled operators can troubleshoot issues, optimize processes, and uphold quality standards.
Quality Assurance Protocols
Implementing comprehensive quality assurance protocols at every stage of the lamination process ensures that defects are identified and addressed promptly. This includes material inspection, in-process monitoring, and final product testing.
Continuous Improvement and Innovation
Adopting a mindset of continuous improvement encourages ongoing enhancements in the lamination process. Encouraging feedback, experimenting with new techniques, and staying informed about industry advancements foster innovation and competitive advantage.
Procurement and Purchasing Strategies
Strategic Sourcing
Strategic sourcing involves identifying and partnering with suppliers who can provide high-quality materials at competitive prices. This requires a thorough analysis of the supplier market, evaluating factors such as reliability, capacity, and technological capabilities.
Cost Management
Effective cost management strategies, including bulk purchasing and negotiating favorable terms, help reduce overall procurement costs. Additionally, monitoring market trends and anticipating price fluctuations enable proactive budgeting and cost control.
Supplier Evaluation and Selection
A rigorous supplier evaluation process ensures that selected partners meet the required quality and reliability standards. Criteria for evaluation may include certifications, past performance, financial stability, and adherence to sustainability practices.
Risk Mitigation
Identifying potential risks in the supply chain, such as supplier insolvency or geopolitical instability, allows for the development of contingency plans. Diversifying the supplier base and maintaining strong relationships with multiple partners mitigate these risks.
Leveraging Technology in Procurement
Utilizing procurement software and data analytics enhances decision-making by providing insights into supplier performance, market trends, and cost structures. Technology facilitates more efficient and strategic procurement processes.
Case Studies: Japanese Excellence in High-Pressure Heat Lamination
Automotive Industry
Japanese automotive manufacturers utilize high-pressure heat lamination to produce lightweight, durable components. By integrating advanced lamination techniques, companies achieve enhanced fuel efficiency and vehicle performance, setting industry standards for quality and innovation.
Electronics Manufacturing
In the electronics sector, high-pressure heat lamination is employed to create reliable circuit boards and protective casings. Japanese firms excel in producing components that meet stringent electrical and mechanical specifications, ensuring the reliability of electronic devices.
Packaging Solutions
Japanese packaging companies leverage high-pressure heat lamination to produce superior packaging materials that offer excellent barrier properties and aesthetic appeal. This enhances product protection and shelf presence, driving consumer preference and sales.
Future Outlook and Innovations
Integration of IoT and Smart Manufacturing
The integration of Internet of Things (IoT) technologies into high-pressure heat lamination processes enables real-time monitoring and data-driven decision-making. Smart manufacturing enhances process efficiency, predictive maintenance, and quality control.
Advanced Materials Development
Ongoing research into advanced materials, such as nanocomposites and smart polymers, expands the possibilities of high-pressure heat lamination. These materials offer superior properties, enabling the creation of innovative and high-performance products.
Automation and Robotics
The adoption of automation and robotics in the lamination process increases precision, reduces labor costs, and enhances production scalability. Automated systems can handle complex tasks with greater speed and accuracy, fostering higher productivity.
Sustainability Enhancements
Future advancements will focus on making high-pressure heat lamination more sustainable. This includes developing energy-efficient processes, utilizing eco-friendly materials, and implementing recycling practices to minimize environmental impact.
Conclusion
Mastering high-pressure heat lamination is a multifaceted endeavor that combines technical expertise, strategic procurement, and a commitment to quality and innovation. Japanese manufacturers have set a benchmark in this field through their precision engineering, lean manufacturing practices, and unwavering focus on quality. By understanding and implementing the best practices outlined in this article, manufacturers globally can harness the benefits of high-pressure heat lamination, achieving superior product quality and competitive advantage in the marketplace. As the industry continues to evolve, embracing new technologies and sustainable practices will be essential in maintaining excellence and driving future growth.
資料ダウンロード
QCD調達購買管理クラウド「newji」は、調達購買部門で必要なQCD管理全てを備えた、現場特化型兼クラウド型の今世紀最高の購買管理システムとなります。
ユーザー登録
調達購買業務の効率化だけでなく、システムを導入することで、コスト削減や製品・資材のステータス可視化のほか、属人化していた購買情報の共有化による内部不正防止や統制にも役立ちます。
NEWJI DX
製造業に特化したデジタルトランスフォーメーション(DX)の実現を目指す請負開発型のコンサルティングサービスです。AI、iPaaS、および先端の技術を駆使して、製造プロセスの効率化、業務効率化、チームワーク強化、コスト削減、品質向上を実現します。このサービスは、製造業の課題を深く理解し、それに対する最適なデジタルソリューションを提供することで、企業が持続的な成長とイノベーションを達成できるようサポートします。
オンライン講座
製造業、主に購買・調達部門にお勤めの方々に向けた情報を配信しております。
新任の方やベテランの方、管理職を対象とした幅広いコンテンツをご用意しております。
お問い合わせ
コストダウンが利益に直結する術だと理解していても、なかなか前に進めることができない状況。そんな時は、newjiのコストダウン自動化機能で大きく利益貢献しよう!
(Β版非公開)