- お役立ち記事
- Mastering the Art of Production Line Design: Insights from Japanese Manufacturing Excellence
月間77,185名の
製造業ご担当者様が閲覧しています*
*2025年2月28日現在のGoogle Analyticsのデータより
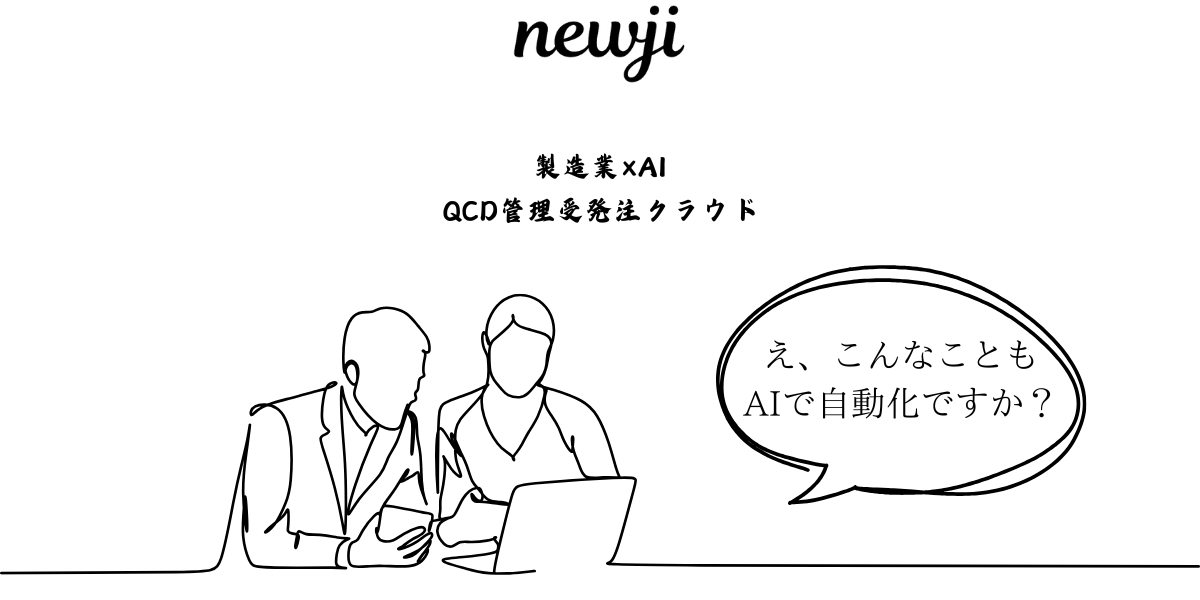
Mastering the Art of Production Line Design: Insights from Japanese Manufacturing Excellence
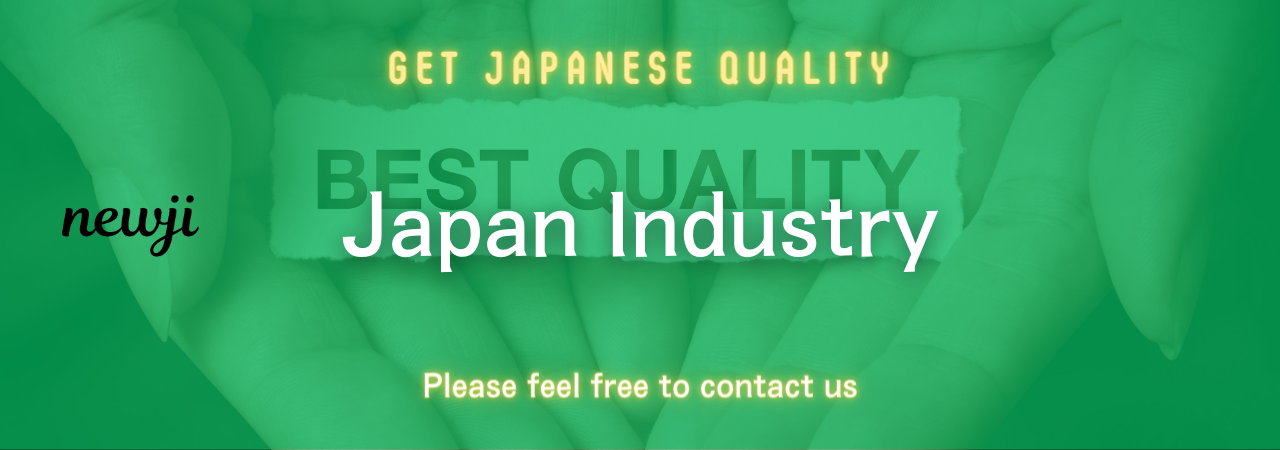
目次
Introduction to Japanese Manufacturing Excellence
Japanese manufacturing is renowned worldwide for its efficiency, quality, and innovation.
The principles and practices developed in Japan have revolutionized production line design across various industries.
Understanding these principles provides valuable insights for companies aiming to enhance their manufacturing processes.
This article delves into the art of production line design, drawing lessons from Japanese manufacturing excellence.
The Importance of Production Line Design
Effective production line design is crucial for optimizing manufacturing processes.
It directly impacts productivity, quality, and cost-efficiency.
A well-designed production line ensures smooth workflow, minimizes waste, and maximizes output.
In the competitive landscape of global manufacturing, mastering production line design is essential for sustainability and growth.
Core Principles of Japanese Manufacturing
Japanese manufacturing is built on several core principles that contribute to its success.
These principles emphasize efficiency, quality, and continuous improvement.
Lean Manufacturing
Lean manufacturing focuses on eliminating waste within a manufacturing system.
By identifying and removing non-value-adding activities, companies can streamline operations.
This approach leads to reduced costs, shorter lead times, and improved product quality.
Just-In-Time (JIT)
Just-In-Time is a strategy that strives to improve a business’s return on investment by reducing in-process inventory and associated carrying costs.
JIT ensures that materials are delivered exactly when needed in the production process, minimizing inventory levels.
This approach enhances flexibility and responsiveness to market demands.
Kaizen
Kaizen, meaning “continuous improvement,” is a philosophy that encourages ongoing, incremental improvements in all aspects of a business.
It involves every employee, from the CEO to assembly line workers, in the problem-solving process.
Kaizen fosters a culture of excellence and innovation, driving long-term success.
Advantages of Japanese Production Line Design
Adopting Japanese production line design principles offers several advantages:
Enhanced Efficiency
Japanese methodologies streamline production processes, reducing waste and increasing productivity.
Efficient workflows lead to faster turnaround times and higher output with the same resources.
Improved Quality
Emphasis on quality control ensures that products meet high standards consistently.
Techniques like Total Quality Management (TQM) and Six Sigma are integral to maintaining excellence.
Flexibility and Responsiveness
Japanese production systems are designed to be flexible, allowing for quick adjustments in response to changing market demands.
This adaptability enhances a company’s ability to compete in dynamic environments.
Employee Engagement
Involving employees in continuous improvement processes fosters a sense of ownership and commitment.
Engaged employees are more motivated to contribute to the company’s success.
Challenges and Disadvantages
While Japanese production line design offers numerous benefits, there are challenges to consider:
Initial Implementation Costs
Implementing advanced production systems and training employees can be costly upfront.
Companies must be prepared for initial investments to realize long-term gains.
Cultural Differences
Japanese manufacturing principles are deeply rooted in their culture, making them challenging to adopt in different cultural contexts.
Adapting these practices requires sensitivity to local work environments and employee mindsets.
Change Management
Transitioning to a new production line design involves significant changes in processes and workflows.
Effective change management strategies are essential to ensure smooth adoption and minimize disruptions.
Procurement and Purchasing in Production Line Design
Procurement and purchasing play a vital role in the success of production line design.
Effective management of these functions ensures that the right materials and components are available when needed, supporting efficient operations.
Supplier Selection and Relationships
Choosing the right suppliers is critical.
Japanese manufacturers often build long-term relationships with trusted suppliers, fostering collaboration and reliability.
Strong supplier relationships can lead to better quality materials, timely deliveries, and favorable terms.
Cost Management
Effective procurement strategies help manage costs by negotiating favorable prices and terms.
Bulk purchasing and strategic sourcing contribute to cost savings without compromising quality.
Quality Assurance
Ensuring that suppliers adhere to quality standards is essential for maintaining overall production quality.
Implementing rigorous quality control measures and regular audits helps maintain high standards.
Supplier Negotiation Techniques
Negotiating with suppliers is a critical aspect of procurement and purchasing.
Japanese negotiation techniques emphasize respect, mutual benefit, and long-term relationships.
Building Trust and Respect
Japanese negotiations prioritize building trust and mutual respect between parties.
Establishing a strong relationship lays the foundation for successful negotiations and ongoing collaboration.
Win-Win Approach
The goal is to create agreements that benefit both parties, ensuring long-term partnerships rather than short-term gains.
This approach fosters cooperation and reduces conflicts, leading to more sustainable agreements.
Patience and Persistence
Japanese negotiations often involve a deliberate and patient approach, allowing time for thorough discussions and consensus-building.
Patience ensures that all aspects are considered, leading to well-rounded agreements.
Attention to Detail
Being meticulous about details and clearly understanding all terms and conditions is crucial.
This thoroughness helps prevent misunderstandings and ensures that both parties are aligned.
Market Conditions and Production Line Design
Market conditions significantly influence production line design.
Understanding and adapting to these conditions ensures that production processes remain efficient and competitive.
Demand Fluctuations
Production lines must be adaptable to handle variations in demand.
Scalable and flexible designs allow companies to ramp up or downproduction as needed, minimizing waste and maximizing efficiency.
Technological Advancements
Staying abreast of technological advancements is essential for maintaining competitive advantage.
Integrating new technologies can enhance production capabilities, improve quality, and reduce costs.
Globalization and Supply Chain Dynamics
Global market trends and supply chain dynamics impact production line design.
Understanding these factors helps in designing adaptable and resilient production systems that can navigate global challenges.
Best Practices from Japanese Manufacturing
Implementing best practices derived from Japanese manufacturing can transform production line design:
Standardization
Standardizing processes ensures consistency and quality across the production line.
It simplifies training, reduces errors, and facilitates continuous improvement.
Visual Management
Using visual tools to monitor and manage production processes enhances transparency and communication.
Visual aids help identify issues quickly and facilitate prompt resolution.
Total Productive Maintenance (TPM)
TPM focuses on maintaining and improving production equipment to prevent downtime and defects.
Regular maintenance and proactive problem-solving enhance equipment reliability and longevity.
5S Methodology
The 5S methodology (Sort, Set in order, Shine, Standardize, Sustain) organizes the workplace for efficiency and effectiveness.
Implementing 5S leads to improved productivity, safety, and morale.
Continuous Improvement Culture
Fostering a culture of continuous improvement encourages ongoing enhancements in processes and products.
Empowering employees to suggest and implement improvements drives innovation and excellence.
Case Studies: Success Stories from Japanese Manufacturers
Examining real-world examples of Japanese manufacturers can provide practical insights into successful production line design:
Toyota Production System
The Toyota Production System (TPS) is a benchmark for lean manufacturing.
TPS emphasizes waste reduction, just-in-time production, and respect for people, leading to enhanced efficiency and quality.
Panasonic’s Automation Strategies
Panasonic integrates advanced automation technologies to streamline production processes.
Their focus on automation enhances consistency, reduces labor costs, and increases production capacity.
Honda’s Flexible Manufacturing
Honda employs flexible manufacturing systems that allow for rapid adjustments to production lines based on changing demand.
This flexibility ensures responsiveness and minimizes downtime during transitions.
Implementing Japanese Practices in Your Manufacturing Process
Adopting Japanese production line design principles requires careful planning and execution.
Here are steps to integrate these practices into your manufacturing operations:
Assess Current Processes
Conduct a thorough evaluation of existing production processes to identify areas for improvement.
Understanding current strengths and weaknesses guides the implementation of new practices.
Train and Educate Employees
Provide training to employees on Japanese manufacturing principles and practices.
Educated and skilled employees are essential for successful implementation and continuous improvement.
Customize Practices to Your Context
Adapt Japanese practices to fit your company’s specific needs and cultural context.
Customization ensures that practices are relevant and effective in your operational environment.
Implement Incrementally
Introduce new practices gradually to allow for adjustment and minimize disruptions.
Phased implementation helps manage change effectively and sustain momentum.
Monitor and Evaluate
Regularly monitor the impact of implemented practices and evaluate their effectiveness.
Continuous assessment enables timely adjustments and reinforces a culture of improvement.
Leveraging Technology for Production Line Design
Technology plays a pivotal role in modern production line design.
Japanese manufacturers leverage advanced technologies to enhance efficiency and quality.
Automation and Robotics
Integrating automation and robotics streamlines repetitive tasks, reduces errors, and increases production speed.
Advanced robotics contribute to higher precision and consistency in manufacturing processes.
Data Analytics
Utilizing data analytics enables informed decision-making by providing insights into production performance.
Analyzing data helps identify bottlenecks, optimize workflows, and predict maintenance needs.
Internet of Things (IoT)
IoT devices facilitate real-time monitoring and control of production lines.
Connecting machines and systems enhances visibility, coordination, and responsiveness to changes.
Artificial Intelligence (AI) and Machine Learning
AI and machine learning optimize production processes by predicting outcomes and automating complex tasks.
These technologies enable proactive adjustments and continuous improvement in manufacturing operations.
Quality Control and Assurance
Maintaining high-quality standards is a hallmark of Japanese manufacturing.
Quality control and assurance are integral to production line design, ensuring that products meet or exceed expectations.
In-Process Inspection
Conducting inspections at various stages of production helps identify and address defects early.
In-process inspections prevent defective products from advancing further, reducing waste and rework.
Statistical Process Control (SPC)
SPC uses statistical methods to monitor and control production processes.
By analyzing process data, companies can detect variations and implement corrective actions promptly.
Root Cause Analysis
Investigating the underlying causes of defects or issues ensures effective resolution and prevents recurrence.
Root cause analysis promotes long-term improvements and enhances overall quality.
Total Quality Management (TQM)
TQM is a holistic approach that involves every employee in the pursuit of quality.
By fostering a company-wide commitment to quality, TQM ensures consistent excellence in products and services.
Supply Chain Management and Production Line Design
Effective supply chain management is essential for seamless production line operations.
Japanese manufacturing emphasizes integrated and responsive supply chains to support efficient production.
Integrated Supply Chains
Integrating supply chain functions enhances coordination and collaboration among suppliers, manufacturers, and distributors.
Seamless integration ensures timely delivery of materials and reduces delays in production.
Supplier Collaboration
Collaborating closely with suppliers fosters mutual understanding and alignment of goals.
Effective collaboration leads to improved quality, innovation, and responsiveness in the supply chain.
Inventory Management
Optimizing inventory levels balances the need for sufficient materials with the goal of minimizing excess stock.
Effective inventory management reduces carrying costs and ensures materials are available when needed.
Risk Management
Identifying and mitigating risks in the supply chain safeguards production continuity.
Proactive risk management addresses potential disruptions and enhances supply chain resilience.
Environmental Sustainability in Production Line Design
Sustainability is increasingly important in modern manufacturing.
Japanese production line design integrates environmentally friendly practices to minimize ecological impact.
Energy Efficiency
Implementing energy-efficient technologies and processes reduces energy consumption and costs.
Energy-efficient production lines contribute to environmental sustainability and operational savings.
Waste Reduction
Minimizing waste through lean manufacturing and recycling initiatives reduces environmental footprint.
Waste reduction strategies enhance resource utilization and sustainability.
Green Manufacturing Practices
Adopting green manufacturing practices involves using eco-friendly materials and sustainable processes.
Green practices align production line design with environmental stewardship and regulatory requirements.
Corporate Social Responsibility (CSR)
Integrating CSR into production line design reflects a commitment to ethical and sustainable practices.
CSR initiatives enhance brand reputation and meet stakeholder expectations for responsible manufacturing.
Human Factors in Production Line Design
Human factors are critical in ensuring the effectiveness of production line design.
Japanese manufacturing emphasizes ergonomic and human-centered approaches to enhance employee well-being and productivity.
Ergonomics
Designing workstations and processes to accommodate human capabilities reduces physical strain and injuries.
Ergonomic designs improve comfort, safety, and efficiency for employees.
Employee Training and Development
Providing comprehensive training ensures that employees are skilled and knowledgeable in operating production lines.
Continuous development programs foster a culture of learning and adaptability.
Workplace Culture
Cultivating a positive workplace culture promotes collaboration, motivation, and satisfaction among employees.
A supportive environment enhances productivity and reduces turnover rates.
Safety Practices
Implementing stringent safety protocols safeguards employees and ensures compliance with regulations.
A safe workplace minimizes accidents and promotes a culture of responsibility and care.
Continuous Improvement and Innovation
Continuous improvement and innovation are pillars of Japanese manufacturing excellence.
These practices drive ongoing enhancements in production line design and overall manufacturing performance.
Encouraging Innovation
Fostering an environment that encourages creativity and innovation leads to the development of new ideas and solutions.
Innovative approaches enhance production processes and keep companies competitive.
Feedback Mechanisms
Implementing feedback mechanisms enables the collection of insights from employees and stakeholders.
Feedback drives improvements and ensures that production line design evolves with changing needs.
Benchmarking
Benchmarking against industry standards and best practices helps identify areas for improvement and set performance targets.
Continuous benchmarking ensures that production lines remain competitive and efficient.
Adopting Emerging Technologies
Staying informed about emerging technologies and integrating them into production processes supports ongoing innovation.
Adopting new technologies enhances capabilities and drives continuous improvement in manufacturing operations.
Conclusion: Embracing Japanese Manufacturing Excellence
Mastering the art of production line design draws valuable lessons from Japanese manufacturing excellence.
By adopting principles such as lean manufacturing, just-in-time, and continuous improvement, companies can enhance efficiency, quality, and flexibility.
Effective procurement and purchasing, strong supplier relationships, and advanced technologies further support optimized production lines.
While challenges exist, the advantages of Japanese production line design make it a worthwhile investment for companies seeking sustained success in the competitive global market.
Embracing these practices fosters a culture of excellence, innovation, and continuous growth, ensuring long-term manufacturing excellence.
資料ダウンロード
QCD管理受発注クラウド「newji」は、受発注部門で必要なQCD管理全てを備えた、現場特化型兼クラウド型の今世紀最高の受発注管理システムとなります。
ユーザー登録
受発注業務の効率化だけでなく、システムを導入することで、コスト削減や製品・資材のステータス可視化のほか、属人化していた受発注情報の共有化による内部不正防止や統制にも役立ちます。
NEWJI DX
製造業に特化したデジタルトランスフォーメーション(DX)の実現を目指す請負開発型のコンサルティングサービスです。AI、iPaaS、および先端の技術を駆使して、製造プロセスの効率化、業務効率化、チームワーク強化、コスト削減、品質向上を実現します。このサービスは、製造業の課題を深く理解し、それに対する最適なデジタルソリューションを提供することで、企業が持続的な成長とイノベーションを達成できるようサポートします。
製造業ニュース解説
製造業、主に購買・調達部門にお勤めの方々に向けた情報を配信しております。
新任の方やベテランの方、管理職を対象とした幅広いコンテンツをご用意しております。
お問い合わせ
コストダウンが利益に直結する術だと理解していても、なかなか前に進めることができない状況。そんな時は、newjiのコストダウン自動化機能で大きく利益貢献しよう!
(β版非公開)