- お役立ち記事
- “Mastering the Art of Soldering: A Deep Dive into Japanese Manufacturing Techniques”
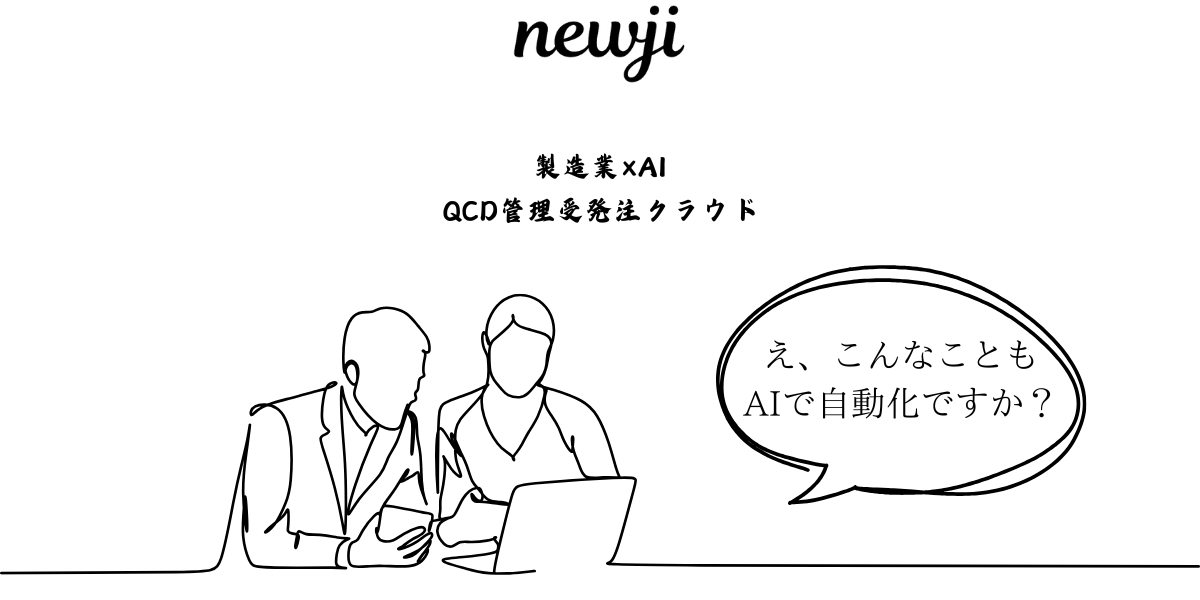
“Mastering the Art of Soldering: A Deep Dive into Japanese Manufacturing Techniques”
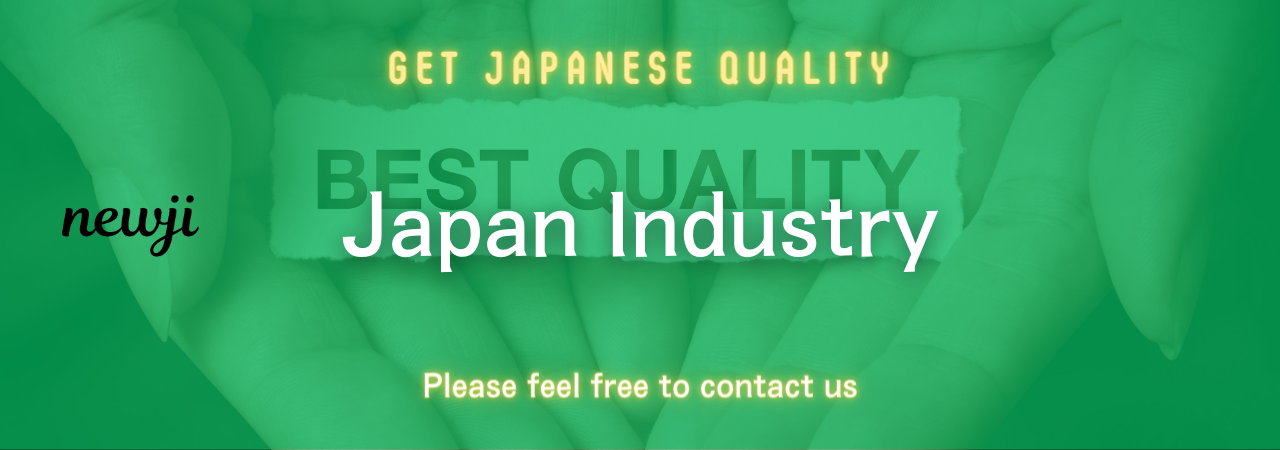
目次
Introduction to Japanese Soldering Techniques
Japanese manufacturing has long been revered for its precision, efficiency, and unwavering commitment to quality. When it comes to soldering—a critical process in electronics manufacturing—the Japanese approach stands out for its meticulous attention to detail and innovative practices. This article explores the intricacies of Japanese soldering techniques, offering insights from a procurement and purchasing perspective. We will delve into the advantages and disadvantages of these methods, effective supplier negotiation strategies, current market conditions, and best practices for integrating Japanese soldering expertise into your manufacturing processes.
The Foundations of Japanese Soldering Excellence
Precision Engineering and Quality Control
At the heart of Japanese soldering techniques lies a foundation of precision engineering. Japanese manufacturers employ highly specialized equipment that ensures each solder joint meets exact specifications. This commitment to precision reduces the likelihood of defects, enhancing the overall reliability of electronic products.
Quality control in Japanese manufacturing is stringent. Every step of the soldering process is monitored, and continuous improvements are made based on feedback and analysis. This proactive approach minimizes errors and ensures that the final product adheres to the highest standards.
Lean Manufacturing and Efficiency
Japanese soldering practices are deeply influenced by lean manufacturing principles. By eliminating waste and optimizing workflows, Japanese manufacturers achieve remarkable efficiency in their soldering operations. This efficiency translates to faster production times and lower costs without compromising quality.
The Just-In-Time (JIT) production system is a cornerstone of Japanese manufacturing. It ensures that components are delivered precisely when needed, reducing inventory costs and minimizing storage requirements. In soldering, this means having the right materials and components available at the right time, enhancing the overall production flow.
Advantages of Japanese Soldering Techniques
Superior Product Quality
One of the most significant advantages of Japanese soldering techniques is the superior quality of the end product. The emphasis on precision and rigorous quality control ensures that solder joints are reliable and durable, reducing the likelihood of product failures and recalls.
Enhanced Efficiency and Cost-Effectiveness
Japanese manufacturers excel in maximizing efficiency through lean manufacturing principles. This results in cost savings that can be passed on to customers or reinvested into further innovation. Efficient soldering processes also enable quicker turnaround times, enhancing overall competitiveness in the market.
Strong Supplier Relationships
Japanese companies are known for fostering long-term relationships with their suppliers. This collaborative approach ensures a steady supply of high-quality materials and components, which is essential for maintaining the integrity of the soldering process. Reliable supplier partnerships also facilitate smoother negotiations and better terms.
Disadvantages and Challenges
Higher Initial Costs
While Japanese soldering techniques offer long-term savings through efficiency and quality, the initial investment in specialized equipment and training can be substantial. Smaller companies or those new to Japanese manufacturing practices may find these upfront costs challenging.
Cultural and Communication Barriers
Working with Japanese suppliers often involves navigating cultural and language differences. Misunderstandings can arise, potentially affecting negotiations and collaboration. It is crucial to invest in cultural training and effective communication strategies to mitigate these challenges.
Supply Chain Dependencies
Relying heavily on Japanese suppliers for critical components can create vulnerabilities in the supply chain. Disruptions due to geopolitical tensions, natural disasters, or other unforeseen events can impact production schedules and overall business operations.
Supplier Negotiation Techniques
Building Trust and Long-Term Relationships
Japanese business culture places a strong emphasis on trust and long-term relationships. Building a rapport with suppliers through regular communication, mutual respect, and reliability can lead to more favorable negotiation outcomes. Suppliers are more likely to offer competitive pricing and prioritize your orders if a trusting relationship is established.
Understanding Cultural Nuances
Successful negotiations require an understanding of Japanese business etiquette and cultural norms. Patience, indirect communication, and a focus on consensus-building are key traits appreciated in Japanese business settings. Demonstrating respect for these cultural elements can facilitate smoother negotiations.
Leveraging Technical Expertise
Japanese suppliers often pride themselves on their technical expertise. Engaging in technical discussions and demonstrating an understanding of soldering processes can earn their respect and cooperation. This technical alignment can open doors to customized solutions and better pricing structures.
Market Conditions Affecting Japanese Soldering Suppliers
Global Supply Chain Dynamics
The global supply chain landscape is continually evolving, influenced by factors such as trade policies, tariffs, and geopolitical tensions. Japanese soldering suppliers must navigate these dynamics to maintain a stable supply of materials and components. Understanding these factors is crucial for procurement professionals to anticipate potential disruptions and adapt strategies accordingly.
Technological Advancements
Advancements in soldering technology, such as automation and precision machinery, are shaping the capabilities of Japanese suppliers. Staying abreast of these developments allows purchasers to leverage the latest innovations, ensuring their products remain competitive in the market.
Environmental Regulations
Increasingly stringent environmental regulations are impacting manufacturing processes worldwide, including soldering. Japanese suppliers are at the forefront of developing environmentally friendly soldering techniques and materials. Aligning with suppliers who prioritize sustainability can enhance your company’s environmental footprint and compliance with regulatory standards.
Best Practices for Integrating Japanese Soldering Techniques
Comprehensive Supplier Evaluation
Before partnering with a Japanese soldering supplier, conduct a thorough evaluation of their capabilities, quality standards, and reliability. This includes assessing their manufacturing processes, quality control measures, and ability to meet your specific requirements. Visiting facilities and auditing processes can provide valuable insights into their operational excellence.
Collaborative Planning and Forecasting
Engage in collaborative planning with your Japanese suppliers to align production schedules and inventory management. Sharing forecasts and demand projections can help suppliers prepare adequately, reducing lead times and ensuring timely delivery of soldered components.
Continuous Improvement and Feedback Loops
Adopt a mindset of continuous improvement by regularly providing feedback to your suppliers and encouraging them to do the same. Implementing feedback loops fosters a culture of mutual growth and innovation, leading to enhancements in soldering techniques and overall product quality.
Investing in Training and Development
To effectively integrate Japanese soldering techniques, invest in training your procurement and quality control teams. Understanding the technical aspects of soldering and the specific practices of your Japanese suppliers will enable more informed decision-making and better collaboration.
Case Studies: Success Stories in Japanese Soldering Integration
Automotive Electronics Manufacturer
A leading automotive electronics manufacturer sought to enhance the reliability of its soldered connections in critical vehicle components. By partnering with a Japanese soldering supplier known for its precision and quality, the company was able to reduce defect rates by 15% and decrease production costs by 10%. The collaboration also led to the development of a customized soldering process tailored to the company’s specific needs.
Consumer Electronics Company
A consumer electronics company aiming to innovate its product lineup turned to Japanese soldering experts to integrate advanced soldering techniques into its manufacturing process. The result was a series of high-performance devices with superior durability and performance, boosting the company’s market share and customer satisfaction ratings.
Future Trends in Japanese Soldering Techniques
Automation and Industry 4.0 Integration
The future of soldering in Japanese manufacturing is closely tied to the advancements in automation and Industry 4.0. Smart factories equipped with IoT devices and AI-driven analytics will further enhance the precision and efficiency of soldering processes. Procurement professionals should be prepared to engage with suppliers who are at the cutting edge of these technological trends.
Sustainable Soldering Practices
As sustainability becomes increasingly important, Japanese soldering techniques are evolving to minimize environmental impact. This includes the development of lead-free solder alternatives and processes that reduce energy consumption. Companies that prioritize sustainability will benefit from partnering with suppliers who are leaders in eco-friendly soldering practices.
Customization and Flexibility
The demand for highly customized electronic components continues to grow. Japanese suppliers are responding by offering more flexible soldering solutions tailored to specific client requirements. This trend highlights the importance of agility and responsiveness in supplier relationships, ensuring that manufacturers can meet diverse and evolving market demands.
Conclusion
Mastering the art of soldering through Japanese manufacturing techniques offers significant advantages in terms of quality, efficiency, and innovation. However, it also presents challenges related to initial investments, cultural differences, and supply chain dependencies. By adopting best practices in supplier evaluation, negotiation, and collaboration, procurement and purchasing professionals can successfully integrate these advanced soldering methods into their operations. Staying informed about market conditions and future trends will further ensure that your manufacturing processes remain competitive and aligned with global standards. Embracing the meticulous and innovative spirit of Japanese soldering techniques can ultimately lead to superior products and sustained business success.
資料ダウンロード
QCD調達購買管理クラウド「newji」は、調達購買部門で必要なQCD管理全てを備えた、現場特化型兼クラウド型の今世紀最高の購買管理システムとなります。
ユーザー登録
調達購買業務の効率化だけでなく、システムを導入することで、コスト削減や製品・資材のステータス可視化のほか、属人化していた購買情報の共有化による内部不正防止や統制にも役立ちます。
NEWJI DX
製造業に特化したデジタルトランスフォーメーション(DX)の実現を目指す請負開発型のコンサルティングサービスです。AI、iPaaS、および先端の技術を駆使して、製造プロセスの効率化、業務効率化、チームワーク強化、コスト削減、品質向上を実現します。このサービスは、製造業の課題を深く理解し、それに対する最適なデジタルソリューションを提供することで、企業が持続的な成長とイノベーションを達成できるようサポートします。
オンライン講座
製造業、主に購買・調達部門にお勤めの方々に向けた情報を配信しております。
新任の方やベテランの方、管理職を対象とした幅広いコンテンツをご用意しております。
お問い合わせ
コストダウンが利益に直結する術だと理解していても、なかなか前に進めることができない状況。そんな時は、newjiのコストダウン自動化機能で大きく利益貢献しよう!
(Β版非公開)