- お役立ち記事
- “Mastering the Circular Economy: Innovative Strategies in Japanese Manufacturing”
“Mastering the Circular Economy: Innovative Strategies in Japanese Manufacturing”
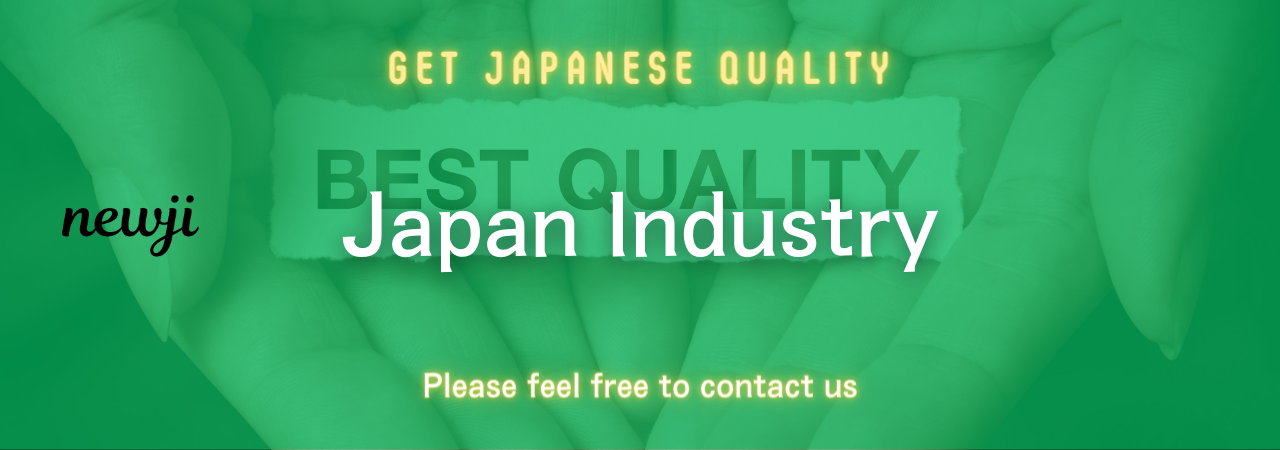
目次
Understanding the Circular Economy in Manufacturing
The circular economy is a novel concept that extends well beyond traditional methods of production and consumption.
Unlike the linear economy, which typically follows a “take, make, waste” approach, the circular economy aims to minimize waste and make the most of resources.
The core idea is to create a closed-loop system where product life cycles are extended, resources are reused, and waste is minimized.
This approach has garnered significant attention worldwide, but Japan has been at the forefront of implementing circular economy principles in its manufacturing sector.
The Evolution and Importance of the Circular Economy in Japan
Japan has a rich history of resource conservation and efficient manufacturing practices.
The country’s high population density and limited natural resources have necessitated efficient use of available resources.
This cultural and economic context made Japan an early adopter of what we now term the circular economy.
In the 1990s, the Japanese government introduced policies that emphasized recycling and resource efficiency.
By 2000, significant legislative measures like the Basic Act on Establishing a Sound Material-Cycle Society were put into place.
These initiatives aimed to reduce waste and promote recycling, setting the foundation for today’s advanced circular economy practices.
The Role of the Automotive Industry
One of the most impactful applications of the circular economy in Japan is seen in the automotive sector.
Japanese automakers like Toyota and Nissan have introduced comprehensive recycling and remanufacturing programs.
These companies have developed methods to recycle materials such as metals, plastics, and glass from end-of-life vehicles (ELVs).
Amazingly, nearly 95% of the materials from ELVs are now reused or recycled, exemplifying the circular economy in action.
Consumer Electronics and E-Waste Management
Another sector where Japan excels in circular economy practices is consumer electronics.
With rapid technological advancements, e-waste has become a global issue.
Japanese companies like Sony and Panasonic have developed strategies to recycle and refurbish electronic products efficiently.
Incorporating eco-design principles, companies make easier-to-disassemble products, facilitating component reuse and recycling.
Advantages of Adopting Circular Economy Practices
Switching to a circular economy framework presents numerous advantages for manufacturers.
Here we outline some of the most compelling benefits:
Cost Savings and Efficiency
One of the primary benefits of the circular economy is the cost savings achieved through efficient resource utilization.
By reusing materials and components, manufacturers can significantly reduce their raw material costs.
Additionally, optimized production processes can minimize waste, lowering disposal costs and improving factory efficiency.
This focus on efficiency directly translates into higher profit margins.
Environmental Impact
The circular economy substantially reduces environmental footprints.
By reusing and recycling materials, manufacturers can decrease the amount of waste sent to landfills.
This contributes to lower greenhouse gas emissions and less environmental degradation.
Such benefits not only meet regulatory requirements but also enhance the company’s brand image as an environmentally responsible entity.
Innovation and Competitiveness
Adopting circular economy principles fosters a culture of innovation within the organization.
Manufacturers must continually seek new ways to reuse materials, optimize processes, and design sustainable products.
This drive for innovation can result in products that meet consumer demands for sustainability and quality.
By staying ahead of the curve, companies position themselves as industry leaders, attracting more customers and talent.
Challenges and Disadvantages
While the circular economy offers numerous benefits, it’s essential to acknowledge the associated challenges and disadvantages:
Initial Investment Costs
Transitioning to a circular economy model often requires substantial initial investments.
Businesses may need to upgrade machinery, redesign products, or establish new recycling systems.
These costs can be significant, particularly for small and medium-sized enterprises (SMEs).
Supply Chain Complexity
Integrating circular economy practices can complicate the supply chain.
Companies need to establish reliable channels for collecting and processing returned products.
This adds a layer of complexity, requiring robust logistics and excellent coordination with suppliers and recycling facilities.
Technological and Skill Barriers
The successful implementation of a circular economy relies on advanced technologies and specialized skills.
Manufacturers must invest in research and development to create innovative recycling and reusing techniques.
Additionally, employees need training to adapt to new processes, necessitating time and resources.
Best Practices for Implementing Circular Economy Principles
To effectively implement circular economy principles, manufacturers can follow these best practices:
Design for Longevity
Products should be designed to last longer, be easily repairable, and upgradeable.
This approach reduces the need for frequent replacement, aligning with circular economy goals.
Emphasize modular design, which allows for straightforward disassembly, repair, and component replacement.
Material Selection
Opt for materials that are recyclable or biodegradable.
Prioritize the use of secondary raw materials derived from recycling processes.
Leveraging digital tools like material databases can help identify sustainable alternatives.
Reverse Logistics Systems
Develop efficient reverse logistics systems to manage the return, recycling, and refurbishing of products.
Establish partnerships with logistics providers specializing in product take-back systems.
Implement tracking technologies to monitor the flow and status of returned items.
Stakeholder Engagement
Engage with all stakeholders, including suppliers, consumers, and regulators, to build a collaborative ecosystem.
Transparency and communication are key to fostering trust and ensuring the success of circular economy practices.
Involve suppliers in the design process to ensure material suitability and recyclability.
Supplier Negotiation Techniques
Dealing with Japanese suppliers requires a nuanced approach, one that balances cultural sensitivity with strategic acumen.
Here are some techniques to consider:
Building Long-Term Relationships
Japanese business culture places a high value on long-term relationships.
Prioritize building trust and mutual respect through consistent and transparent communication.
A long-term partnership can lead to more favorable terms and better collaboration for circular economy initiatives.
Understanding Cultural Nuances
Familiarize yourself with Japanese business etiquette and negotiation styles.
For instance, patience is crucial, as negotiations may proceed more slowly than in Western contexts.
Understanding these nuances can help navigate discussions more effectively.
Focus on Shared Goals
Frame your discussions around shared goals, such as sustainability and innovation.
Highlight how adopting circular economy practices can benefit both parties.
This approach can foster cooperation and create a win-win scenario.
Market Conditions and Trends
The market conditions in Japan provide a fertile ground for circular economy practices.
Several trends indicate a growing emphasis on sustainability:
Government Policies and Regulations
Japan’s government continues to push for stringent environmental regulations.
Policies such as the Act on Promotion of Resource Circulation for Plastics and the Green Growth Strategy are driving businesses to adopt circular economy principles.
These regulations create a favorable environment for manufacturers committed to sustainability.
Consumer Awareness
Japanese consumers are increasingly aware of environmental issues and are demanding sustainable products.
Companies that prioritize circular economy practices can appeal to this growing demographic.
Marketing campaigns that highlight sustainability efforts can attract these environmentally conscious consumers.
Technological Advancements
Japan remains a hub of technological innovation, which is pivotal in advancing circular economy practices.
From AI-driven recycling systems to advanced material sciences, the technological ecosystem supports the development of sustainable solutions.
Manufacturers can leverage these advancements to enhance their circular economy initiatives.
Case Studies
Examining successful case studies can provide valuable insights into effectively implementing circular economy principles.
Toyota’s Eco-Car Program
Toyota’s Eco-Car Program is an excellent example of circular economy in action.
The program focuses on designing cars that are easy to disassemble and recyclable.
Through its initiative, Toyota has achieved a recycling rate of over 95% for its vehicles.
This case study illustrates the importance of eco-design and efficient reverse logistics.
Panasonic’s Recycling Initiatives
Panasonic has launched several programs aimed at recycling end-of-life electronics.
The company has developed automated systems for efficiently disassembling and recycling electronic components.
This approach not only reduces e-waste but also recovers valuable materials for reuse.
Conclusion
The shift towards a circular economy is not just a trend but a necessity for sustainable growth.
Japan’s advanced manufacturing sector offers numerous lessons in effectively implementing these principles.
By embracing circular economy practices, manufacturers can achieve cost savings, reduce environmental impact, and drive innovation.
However, it’s important to be aware of the challenges and continuously refine strategies to overcome them.
Careful planning, stakeholder engagement, and a focus on sustainability can make the transition to a circular economy successful.
As global awareness of environmental issues grows, adopting these innovative strategies will position companies to lead in a highly competitive market.
資料ダウンロード
QCD調達購買管理クラウド「newji」は、調達購買部門で必要なQCD管理全てを備えた、現場特化型兼クラウド型の今世紀最高の購買管理システムとなります。
ユーザー登録
調達購買業務の効率化だけでなく、システムを導入することで、コスト削減や製品・資材のステータス可視化のほか、属人化していた購買情報の共有化による内部不正防止や統制にも役立ちます。
NEWJI DX
製造業に特化したデジタルトランスフォーメーション(DX)の実現を目指す請負開発型のコンサルティングサービスです。AI、iPaaS、および先端の技術を駆使して、製造プロセスの効率化、業務効率化、チームワーク強化、コスト削減、品質向上を実現します。このサービスは、製造業の課題を深く理解し、それに対する最適なデジタルソリューションを提供することで、企業が持続的な成長とイノベーションを達成できるようサポートします。
オンライン講座
製造業、主に購買・調達部門にお勤めの方々に向けた情報を配信しております。
新任の方やベテランの方、管理職を対象とした幅広いコンテンツをご用意しております。
お問い合わせ
コストダウンが利益に直結する術だと理解していても、なかなか前に進めることができない状況。そんな時は、newjiのコストダウン自動化機能で大きく利益貢献しよう!
(Β版非公開)