- お役立ち記事
- Mastering the Craft: How Japanese Manufacturing Perfects the Circular Disc
Mastering the Craft: How Japanese Manufacturing Perfects the Circular Disc
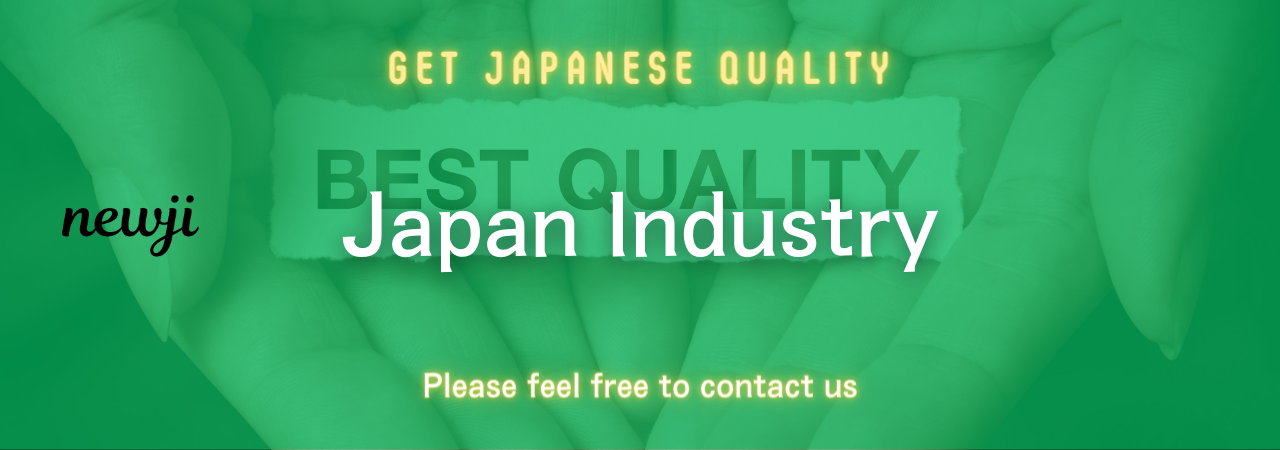
目次
Introduction to Japanese Manufacturing Excellence
Japanese manufacturing has long been synonymous with quality, precision, and innovation. Renowned globally for its meticulous craftsmanship, Japan has established itself as a leader in various manufacturing sectors, including automotive, electronics, and precision machinery. This reputation stems from a combination of advanced technology, rigorous quality control, and a commitment to continuous improvement, often encapsulated in philosophies like Kaizen and Total Quality Management (TQM).
The success of Japanese manufacturing is not only a testament to the technical prowess of its industries but also to the strategic approaches employed in procurement and purchasing. Understanding these strategies provides valuable insights for international companies looking to collaborate with Japanese suppliers and harness the benefits of their expertise.
Understanding the Circular Disc in Manufacturing
Circular discs are fundamental components in various industries, including automotive, aerospace, electronics, and machinery. Their applications range from brake discs in vehicles to precision components in electronic devices. The manufacturing of circular discs demands high precision, consistent quality, and adherence to strict tolerances.
In Japan, the production of circular discs exemplifies the country’s manufacturing excellence. Japanese manufacturers employ advanced techniques such as Computer Numerical Control (CNC) machining, precision casting, and surface finishing to produce discs that meet the highest standards of performance and durability.
Advantages of Japanese Manufacturing Processes
1. Superior Quality Control
Japanese manufacturers prioritize quality at every stage of the production process. The implementation of rigorous quality control systems ensures that each circular disc meets predefined specifications. Techniques such as Six Sigma and Total Quality Management (TQM) are integral to maintaining consistency and minimizing defects.
2. Advanced Technology and Innovation
Japan invests heavily in research and development, leading to the adoption of cutting-edge technologies in manufacturing. The use of laser cutting, CNC machining, and automated inspection systems enhances precision and efficiency in the production of circular discs. Continuous innovation enables Japanese manufacturers to stay ahead of industry trends and meet evolving market demands.
3. Efficient Supply Chain Management
Japanese companies excel in supply chain management, ensuring seamless coordination between suppliers, manufacturers, and distributors. Practices like Just-In-Time (JIT) inventory management reduce waste, lower holding costs, and ensure timely delivery of components. This efficiency is crucial in the production of circular discs, where delays can impact the overall manufacturing timeline.
4. Skilled Workforce and Expertise
The Japanese workforce is known for its dedication, attention to detail, and expertise in manufacturing processes. Skilled technicians and engineers collaborate to optimize production methods, troubleshoot issues, and implement improvements. This human capital is a significant asset in maintaining the high standards of Japanese manufacturing.
Challenges and Disadvantages
1. High Production Costs
While the quality of Japanese manufacturing is unparalleled, it often comes with higher production costs. Advanced technologies, skilled labor, and stringent quality control measures contribute to increased expenses. For companies operating with tight budgets, these costs can be a barrier to sourcing from Japanese suppliers.
2. Language and Cultural Differences
Effective communication is crucial in international procurement and purchasing. Language barriers and cultural differences can pose challenges in negotiations, contract management, and day-to-day interactions with Japanese suppliers. Misunderstandings can lead to delays, errors, and strained business relationships.
3. Longer Lead Times
Japan’s geographic location may result in longer lead times for shipping compared to domestic suppliers. This can impact inventory management and responsiveness to market changes. Additionally, the time required for quality inspections and compliance with Japanese standards may further extend lead times.
4. Rigid Business Practices
Japanese companies are often perceived as having rigid business practices, emphasizing hierarchy and consensus in decision-making. This can result in slower response times to market changes and less flexibility in adapting to specific customer requirements.
Supplier Negotiation Techniques with Japanese Suppliers
1. Building Trust and Relationships
In Japanese business culture, building trust and long-term relationships is paramount. Investing time in face-to-face meetings, understanding the supplier’s values, and demonstrating commitment can foster a strong partnership. Trust is the foundation upon which successful negotiations and collaborations are built.
2. Understanding Cultural Norms
Familiarity with Japanese cultural norms and business etiquette is essential. Practices such as bowing, exchanging business cards respectfully, and adhering to formal communication protocols show respect and facilitate smoother negotiations. Understanding the importance of hierarchy and group consensus can also aid in effective interaction.
3. Clear and Detailed Communication
Given the potential for language barriers, clear and detailed communication is critical. Providing comprehensive specifications, expectations, and contractual terms can prevent misunderstandings. Utilizing visual aids, diagrams, and detailed documentation can enhance clarity.
4. Patience and Persistence
Japanese negotiations may take longer due to the emphasis on thoroughness and consensus-building. Demonstrating patience and persistence shows respect for the supplier’s process and commitment to a mutually beneficial agreement. Rushing negotiations can be counterproductive and damage the relationship.
5. Leveraging Mutual Benefits
Highlighting the benefits for both parties can create a collaborative atmosphere. Emphasizing how the partnership can lead to shared success, innovation, and market expansion encourages suppliers to invest in the relationship. Focusing on mutual gain fosters a win-win scenario.
Market Conditions in Japan’s Manufacturing Sector
1. Technological Advancements
Japan remains at the forefront of technological innovation, particularly in manufacturing. The integration of Industry 4.0 technologies, including the Internet of Things (IoT), artificial intelligence (AI), and robotics, has enhanced production capabilities and efficiency. These advancements enable Japanese manufacturers to produce high-quality circular discs with precision and consistency.
2. Economic Stability
Japan’s economic stability provides a favorable environment for manufacturing. A robust infrastructure, reliable energy supply, and supportive government policies contribute to a conducive business climate. Stability reduces risks associated with currency fluctuations and supply chain disruptions, offering assurance to international purchasers.
3. Supply Chain Resilience
In response to global disruptions, Japanese manufacturers have strengthened their supply chain resilience. Diversifying suppliers, maintaining strategic stockpiles, and investing in local production capabilities have minimized vulnerabilities. This resilience ensures continuity in the production and supply of circular discs despite external challenges.
4. Sustainability and Environmental Standards
Japan places a strong emphasis on sustainability and environmental responsibility in manufacturing. Compliance with stringent environmental regulations and the adoption of eco-friendly practices are integral to operations. Manufacturers investing in sustainable methods appeal to environmentally conscious international buyers and align with global sustainability goals.
Best Practices in Procurement and Purchasing from Japan
1. Conduct Thorough Supplier Evaluation
Before entering into procurement agreements, conduct comprehensive evaluations of potential Japanese suppliers. Assess their financial stability, production capabilities, quality control measures, and compliance with industry standards. Visiting manufacturing facilities and engaging in direct discussions can provide deeper insights into their operations.
2. Establish Clear Contracts and Agreements
Develop clear, detailed contracts that outline specifications, delivery schedules, payment terms, and quality standards. Including clauses that address potential disputes, warranties, and performance metrics ensures both parties have a mutual understanding of expectations and responsibilities.
3. Implement Effective Communication Channels
Establish robust communication channels to facilitate timely and transparent interactions with suppliers. Regular meetings, updates, and feedback loops help address issues promptly and maintain alignment throughout the procurement process. Utilizing digital communication tools can enhance efficiency and accessibility.
4. Foster Collaborative Relationships
Adopt a collaborative approach to partnerships with Japanese suppliers. Sharing market insights, technological advancements, and strategic plans can lead to joint innovations and improvements. Collaboration fosters a sense of partnership, encouraging suppliers to invest in mutual growth and success.
5. Emphasize Continuous Improvement
Align procurement strategies with the principles of continuous improvement. Encourage suppliers to adopt Kaizen practices, seek feedback on performance, and implement enhancements. Continuous improvement leads to higher quality products, increased efficiency, and stronger supplier relationships.
6. Prioritize Sustainability and Compliance
Ensure that procurement practices align with sustainability goals and regulatory compliance. Select suppliers that adhere to environmental standards, ethical labor practices, and industry certifications. Prioritizing sustainability not only mitigates risks but also enhances the company’s reputation among stakeholders.
Leveraging Japanese Manufacturing Skills for Circular Disc Production
Japanese manufacturers excel in the production of circular discs through a combination of precision engineering, advanced materials, and innovative manufacturing processes. By leveraging these skills, international companies can enhance the quality and performance of their products.
1. Precision Engineering and Tolerances
Japanese manufacturers utilize precision engineering to achieve tight tolerances in circular disc production. Advanced CNC machines and meticulous machining processes ensure that each disc meets exact specifications. This precision is critical in applications where performance and safety depend on the accuracy of components.
2. Advanced Materials and Treatments
The use of high-grade materials and specialized surface treatments is a hallmark of Japanese manufacturing. Selecting appropriate materials enhances the durability and performance of circular discs, while surface treatments such as heat treatment, coating, and finishing improve resistance to wear and corrosion.
3. Automation and Robotics
Automation and robotics play a significant role in Japanese manufacturing, increasing efficiency and consistency in production. Automated systems handle repetitive tasks with high precision, reducing the likelihood of human error and ensuring uniformity across batches of circular discs.
4. Rigorous Testing and Quality Assurance
Comprehensive testing and quality assurance practices are integral to Japanese manufacturing. Each circular disc undergoes thorough inspections, including dimensional checks, material analysis, and performance testing. This rigorous approach ensures that only discs meeting the highest standards proceed to final delivery.
5. Customization and Flexibility
Japanese manufacturers offer a high degree of customization to meet specific client requirements. Flexibility in design modifications, material selection, and production volumes allows for tailored solutions that align with the unique needs of international buyers.
Case Studies: Success Stories in Japanese Circular Disc Manufacturing
1. Automotive Industry Collaboration
A leading automotive manufacturer partnered with a Japanese supplier to develop high-performance brake discs. By leveraging the supplier’s expertise in precision engineering and advanced materials, the collaboration resulted in brake discs that offered superior stopping power and longevity. The partnership also facilitated joint research initiatives, leading to continuous improvements in brake disc technology.
2. Electronics Sector Innovation
In the electronics sector, a global consumer electronics company sourced circular discs from a Japanese manufacturer to enhance the performance of cooling systems in their devices. The supplier’s innovative design and manufacturing processes produced discs with optimized heat dissipation properties, contributing to more efficient and reliable electronic products.
3. Aerospace Component Manufacturing
An aerospace company collaborated with a Japanese supplier to produce specialized circular discs for jet engines. The supplier’s precision manufacturing capabilities ensured that the discs met stringent aerospace standards. The partnership not only improved the quality of the components but also streamlined the supply chain, reducing lead times and ensuring timely delivery.
Strategies for Maximizing Benefits from Japanese Procurement
1. Strategic Sourcing
Identify key suppliers that offer the best combination of quality, reliability, and cost-effectiveness. Strategic sourcing involves evaluating multiple suppliers, assessing their strengths, and selecting those that align with the company’s strategic objectives. This approach ensures access to high-quality circular discs while optimizing procurement costs.
2. Continuous Supplier Development
Invest in the development of supplier capabilities through training, technology transfer, and collaborative projects. Continuous supplier development enhances the supplier’s ability to meet evolving quality and performance standards, fostering long-term partnerships and mutual growth.
3. Risk Management
Implement robust risk management practices to mitigate potential disruptions in the supply chain. Identify risks related to supplier dependency, geopolitical factors, and natural disasters, and develop contingency plans to address them. Diversifying suppliers and maintaining safety stocks can reduce the impact of unforeseen events.
4. Leveraging Technology for Procurement Efficiency
Utilize digital procurement platforms and tools to streamline the procurement process. Technologies such as e-procurement systems, supplier relationship management (SRM) software, and data analytics can enhance visibility, improve decision-making, and increase procurement efficiency.
5. Aligning Procurement with Business Goals
Ensure that procurement strategies align with the broader business objectives. Whether it’s achieving cost leadership, enhancing product quality, or driving innovation, aligning procurement activities with business goals ensures that sourcing from Japanese suppliers contributes directly to the company’s success.
Future Trends in Japanese Manufacturing and Procurement
1. Emphasis on Sustainability
Sustainability will continue to be a key focus in Japanese manufacturing. Manufacturers are investing in green technologies, renewable energy, and sustainable materials. This trend aligns with global sustainability goals and responds to increasing consumer demand for eco-friendly products.
2. Digital Transformation
The ongoing digital transformation in Japanese manufacturing includes the adoption of Industry 4.0 technologies. The integration of IoT, AI, and big data analytics enhances production capabilities, predictive maintenance, and supply chain optimization, leading to smarter and more efficient manufacturing processes.
3. Reshoring and Localization
In response to global supply chain disruptions, some Japanese manufacturers are reshoring or localizing their production facilities. This move reduces dependency on international logistics, shortens lead times, and increases supply chain resilience, benefiting international procurement partners through more reliable sourcing options.
4. Advanced Customization
Japanese manufacturers are advancing in their ability to offer highly customized products. Utilizing flexible manufacturing systems and modular production techniques, they can cater to specific client needs without compromising on quality or efficiency, providing tailored solutions for diverse applications of circular discs.
5. Collaborative Innovation
Collaborative innovation between Japanese suppliers and international partners will drive advancements in circular disc technology. Joint research and development initiatives can lead to breakthroughs in materials, design, and manufacturing processes, fostering a culture of shared innovation and continuous improvement.
Conclusion
Mastering the procurement and purchasing processes with Japanese manufacturers offers significant advantages in terms of quality, precision, and technological innovation, particularly in the production of circular discs. However, navigating the challenges of higher costs, cultural differences, and longer lead times requires strategic approaches and a deep understanding of Japanese business practices.
By building strong, trust-based relationships, implementing best practices in procurement, and leveraging the strengths of Japanese manufacturing, international companies can achieve superior product quality and gain a competitive edge in the global market. As the manufacturing landscape continues to evolve, embracing the lessons and strategies from Japanese suppliers will be instrumental in driving sustained success and innovation.
資料ダウンロード
QCD調達購買管理クラウド「newji」は、調達購買部門で必要なQCD管理全てを備えた、現場特化型兼クラウド型の今世紀最高の購買管理システムとなります。
ユーザー登録
調達購買業務の効率化だけでなく、システムを導入することで、コスト削減や製品・資材のステータス可視化のほか、属人化していた購買情報の共有化による内部不正防止や統制にも役立ちます。
NEWJI DX
製造業に特化したデジタルトランスフォーメーション(DX)の実現を目指す請負開発型のコンサルティングサービスです。AI、iPaaS、および先端の技術を駆使して、製造プロセスの効率化、業務効率化、チームワーク強化、コスト削減、品質向上を実現します。このサービスは、製造業の課題を深く理解し、それに対する最適なデジタルソリューションを提供することで、企業が持続的な成長とイノベーションを達成できるようサポートします。
オンライン講座
製造業、主に購買・調達部門にお勤めの方々に向けた情報を配信しております。
新任の方やベテランの方、管理職を対象とした幅広いコンテンツをご用意しております。
お問い合わせ
コストダウンが利益に直結する術だと理解していても、なかなか前に進めることができない状況。そんな時は、newjiのコストダウン自動化機能で大きく利益貢献しよう!
(Β版非公開)