- お役立ち記事
- Material and Tool Selection Contributing to Cost Reduction Activities
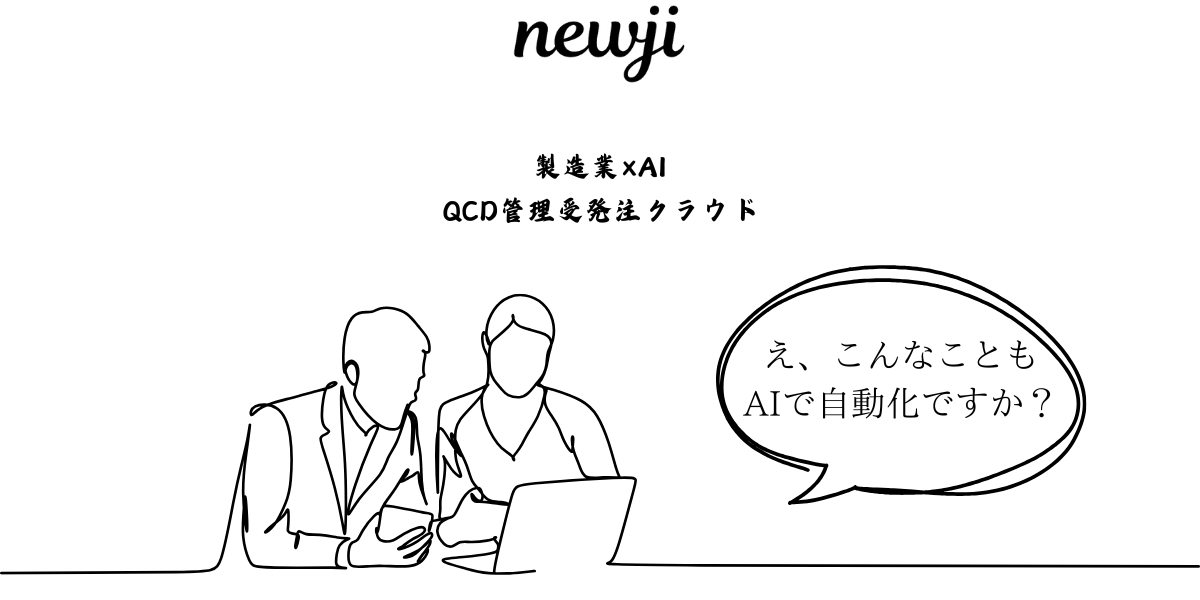
Material and Tool Selection Contributing to Cost Reduction Activities
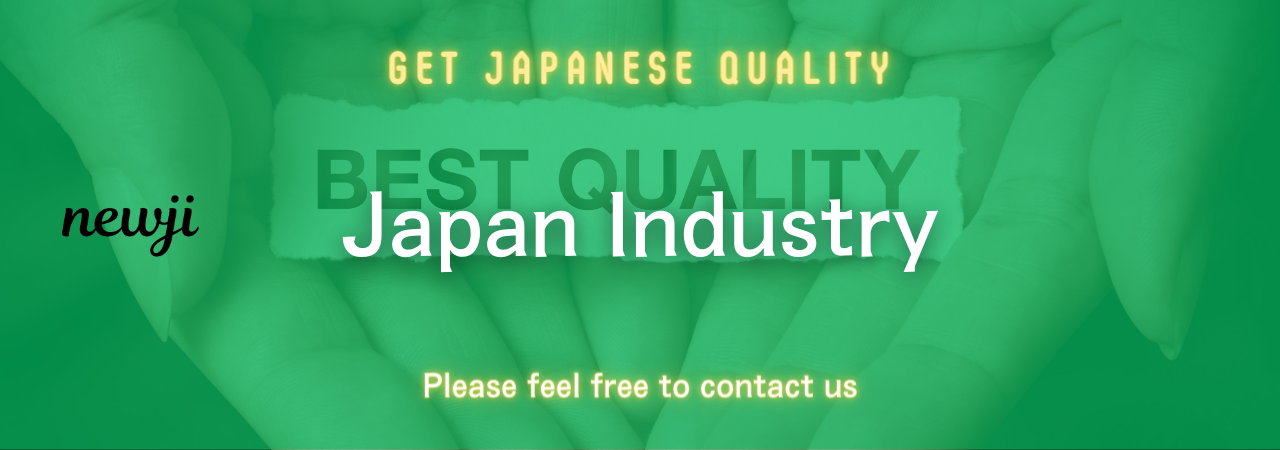
Companies continuously strive to enhance their operations, and one important approach is cost reduction.
Selecting the right materials and tools is a critical factor in achieving this goal.
In this article, we’ll explore how material and tool selection can contribute to cost reduction activities.
We’ll cover the significance of making informed choices and provide practical tips to help your organization save money.
目次
The Importance of Material Selection in Cost Reduction
Understanding Material Properties
Every material has unique properties that influence its performance and cost.
For example, metals have different degrees of strength, flexibility, and weight.
Similarly, plastics offer a range of durability and resistance to various chemicals.
By understanding these properties, you can select the most cost-effective material for your application.
Durability and Longevity
Choosing a material that is durable and long-lasting can significantly reduce costs in the long run.
For instance, opting for a high-quality steel alloy instead of a cheaper alternative can decrease the frequency of replacements and maintenance.
By investing in materials that last longer, you avoid unnecessary expenses and improve the overall efficiency of your operations.
Availability and Cost
Material availability can fluctuate based on market conditions, which in turn affects costs.
Selecting materials that are readily available ensures consistent pricing and supply.
For example, locally sourced materials can be less expensive than imported ones and have shorter lead times.
Additionally, consider the economic aspects of bulk purchasing to achieve cost reductions.
The Role of Tool Selection in Cost Reduction
Precision and Quality
High-quality tools ensure precise and accurate production, which minimizes waste and reduces costs.
For example, using advanced CNC machines instead of manual tools can significantly enhance the quality of your products.
These machines offer more accuracy and consistency, which translates to more efficient production runs and lower costs.
Tool Longevity and Maintenance
Just like with materials, the durability of tools is a major factor.
Investing in tools that require less maintenance and have longer lifespans can save money over time.
For instance, carbide-tipped cutting tools tend to last longer than standard high-speed steel tools.
By reducing the need for frequent replacements, you decrease both downtime and overall expenses.
Adaptability and Versatility
Tools that can perform multiple functions add flexibility to your operations, which can save costs.
For example, a multi-functional machine that performs drilling, cutting, and sanding tasks eliminates the need for separate pieces of equipment.
Similarly, adjustable tools that adapt to various sizes and specifications reduce the number of specific tools you need to purchase.
This adaptability also helps in streamlining processes and enhancing productivity.
Practical Tips for Cost-Effective Material and Tool Selection
Assess Your Needs
Before choosing materials and tools, thoroughly assess your production needs.
Understand the specific requirements for strength, durability, and performance in your applications.
This initial assessment guides you in selecting the most cost-effective options.
Consult Industry Experts
Industry experts can provide valuable insights into the best materials and tools for your applications.
Consulting with suppliers and engineers helps you make informed decisions based on performance and cost considerations.
These experts often have access to the latest trends and technologies, helping you stay ahead of the curve.
Perform Cost-Benefit Analysis
Conduct a thorough cost-benefit analysis of potential materials and tools.
Evaluate not only the initial purchase price but also the long-term savings.
Consider factors like durability, maintenance needs, and potential for reducing waste.
This analysis helps you pinpoint the options that offer the best value for your investment.
Explore Alternatives
Don’t limit your choices to traditional materials and tools.
Explore alternatives that might offer cost-efficiency without compromising on quality.
For instance, composite materials might offer similar strength and durability as metals but at a lower cost.
Similarly, advanced tool designs could enhance efficiency and reduce long-term costs.
Keep an open mind to innovative solutions that can contribute to cost reduction.
Monitor and Review
Regularly monitor the performance of your chosen materials and tools.
Keep track of metrics like lifespan, maintenance needs, and any cost savings achieved.
Review these metrics periodically to ensure that your choices continue to offer the best value.
This ongoing review process enables you to make adjustments and improvements as needed.
Case Studies: Successful Cost Reduction through Material and Tool Selection
Case Study 1: Automotive Manufacturer
An automotive manufacturer faced high costs due to the frequent replacement of metal parts.
By switching to a high-strength, lightweight aluminum alloy, they reduced the frequency of part replacements and decreased overall vehicle weight.
This switch not only saved material costs but also improved fuel efficiency, further reducing expenses.
Case Study 2: Electronics Assembly Company
An electronics assembly company was experiencing increased downtime due to tool malfunctions.
By investing in high-precision, durable soldering equipment, they significantly reduced tool failures.
This investment led to higher productivity, less downtime, and considerable cost savings.
Case Study 3: Furniture Manufacturer
A furniture manufacturer used traditional methods and tools for wood cutting and shaping, leading to high material waste.
By adopting a CNC router, they increased precision and reduced waste.
This change resulted in lower material costs and faster production times, contributing to substantial savings.
Conclusion
In the quest for cost reduction, the selection of materials and tools plays a pivotal role.
By understanding material properties, prioritizing durability, and choosing high-quality, versatile tools, businesses can achieve significant cost savings.
Applying practical tips like consulting experts, performing cost-benefit analyses, and regularly reviewing performance can further enhance these savings.
Take a proactive approach to material and tool selection, and watch your organization reap the benefits of reduced costs and improved efficiency.
資料ダウンロード
QCD調達購買管理クラウド「newji」は、調達購買部門で必要なQCD管理全てを備えた、現場特化型兼クラウド型の今世紀最高の購買管理システムとなります。
ユーザー登録
調達購買業務の効率化だけでなく、システムを導入することで、コスト削減や製品・資材のステータス可視化のほか、属人化していた購買情報の共有化による内部不正防止や統制にも役立ちます。
NEWJI DX
製造業に特化したデジタルトランスフォーメーション(DX)の実現を目指す請負開発型のコンサルティングサービスです。AI、iPaaS、および先端の技術を駆使して、製造プロセスの効率化、業務効率化、チームワーク強化、コスト削減、品質向上を実現します。このサービスは、製造業の課題を深く理解し、それに対する最適なデジタルソリューションを提供することで、企業が持続的な成長とイノベーションを達成できるようサポートします。
オンライン講座
製造業、主に購買・調達部門にお勤めの方々に向けた情報を配信しております。
新任の方やベテランの方、管理職を対象とした幅広いコンテンツをご用意しております。
お問い合わせ
コストダウンが利益に直結する術だと理解していても、なかなか前に進めることができない状況。そんな時は、newjiのコストダウン自動化機能で大きく利益貢献しよう!
(Β版非公開)