- お役立ち記事
- Material lot size optimization undertaken by the purchasing department and its results
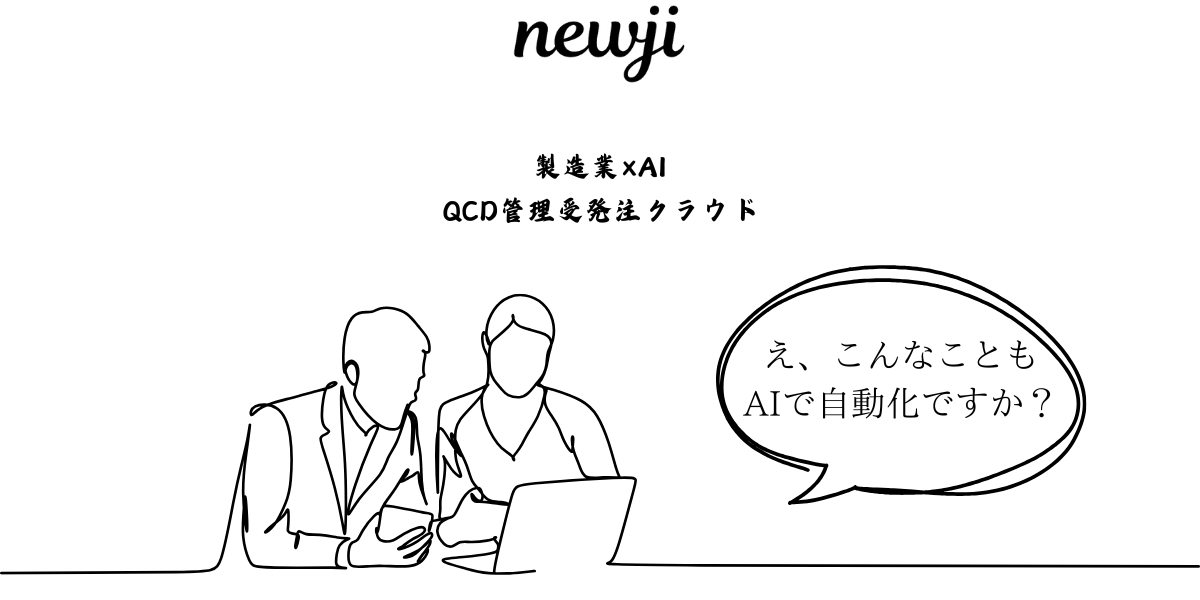
Material lot size optimization undertaken by the purchasing department and its results
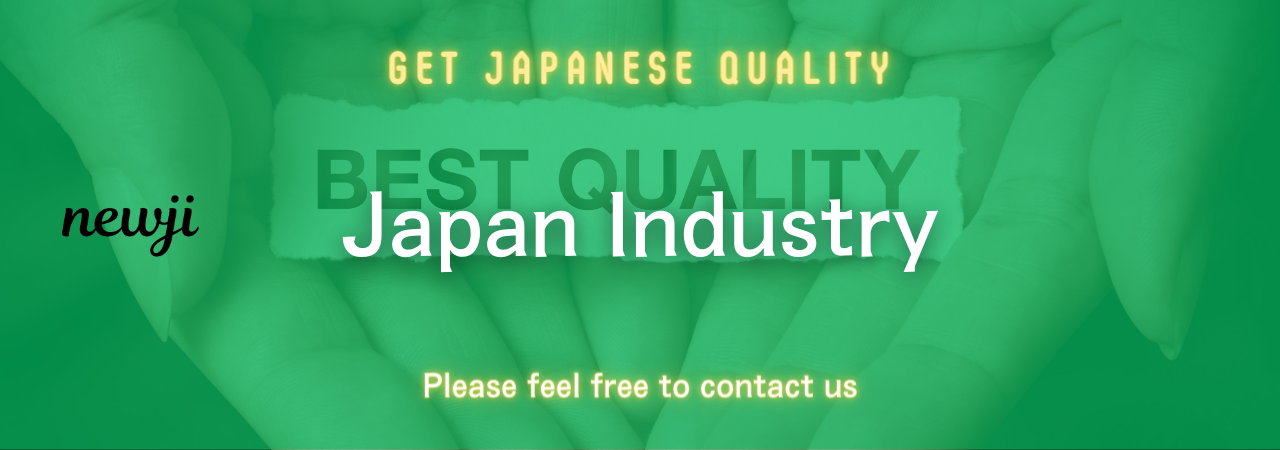
Understanding Material Lot Size Optimization
Material lot size optimization is a crucial strategy in supply chain management aimed at improving efficiency and reducing costs within the purchasing department.
This process involves determining the most cost-effective quantity of materials to order in one batch, balancing the costs associated with ordering, holding, and stockouts.
By optimizing lot sizes, companies can ensure they have the right amount of inventory to meet demand without overstocking, which can tie up capital and increase storage costs.
The Role of the Purchasing Department
The purchasing department plays a pivotal role in material lot size optimization.
Their responsibility is to analyze and forecast the demand for materials, negotiate with suppliers, and establish contracts that reflect the company’s needs.
Purchasing professionals must be skilled in assessing market conditions and trends that could affect material costs and availability.
Effective communication between the purchasing department and other departments such as production, logistics, and sales is essential.
This collaboration ensures that purchasing decisions support the overall operational goals of the company, such as meeting production schedules and customer demand efficiently.
Key Factors in Lot Size Optimization
Several factors influence material lot size optimization. The first is demand variability.
Highly variable demand can lead to either excess inventory or stockouts, making it crucial to choose a lot size that can accommodate fluctuations without significant excess costs.
Lead time is another critical factor.
If a supplier has a long lead time, the purchasing department may need to order larger lot sizes to cover unexpected delays in supply.
Conversely, with shorter lead times, smaller and more frequent orders might be more feasible.
Cost considerations also play a significant role.
These include ordering costs, which are expenses associated with placing and receiving an order, and holding costs, which are incurred for storing inventory.
The goal is to minimize these costs while ensuring inventory is available when needed.
Strategies for Optimizing Lot Sizes
To optimize lot sizes, companies often employ inventory management techniques.
One popular method is the Economic Order Quantity (EOQ) model, which calculates the ideal order quantity a company should purchase to minimize total inventory costs.
The EOQ formula considers demand rate, ordering cost, and holding cost to suggest the optimal lot size.
Another approach is Just-In-Time (JIT) inventory, which aims to reduce inventory levels by receiving goods only as they are needed in the production process.
This method can be effective in minimizing holding costs, though it requires precise demand forecasting and reliable suppliers with short lead times.
ABC analysis is yet another strategy, where inventory items are categorized into three groups: A (high-value but low-frequency), B (moderate-value and frequency), and C (low-value but high-frequency).
Each category can have a different approach to lot sizing based on its unique contribution to overall inventory value.
Benefits of Lot Size Optimization
Optimizing material lot sizes brings various benefits that enhance operational efficiency and cost savings.
One major advantage is the reduction in inventory holding costs, as companies have less excess stock occupying storage space and fewer resources tied up in unsold goods.
Additionally, optimized lot sizes can lead to better supplier relationships.
With clearer and more predictable purchasing patterns, suppliers can also plan their production schedules more effectively, possibly resulting in better pricing agreements or terms for the company.
Improved cash flow is another benefit.
By avoiding overstocking, businesses maintain better cash flow, freeing up capital for investment in other areas or for responding to market opportunities.
Challenges in Implementing Lot Size Optimization
While the benefits of lot size optimization are clear, several challenges can hinder its implementation.
Accurate demand forecasting is paramount, but forecasting errors can lead to either shortages or surpluses, both of which can be costly.
Coordination across departments can also pose a challenge.
Different departments may have conflicting goals or priorities, which can complicate decisions regarding lot sizes.
For instance, production may prefer larger batches to reduce setup times, while purchasing may aim for smaller orders to lower holding costs.
Supply chain disruptions pose another hurdle.
Unexpected events such as supplier delays, natural disasters, or geopolitical issues can affect material availability, leading to the need for quick adjustments in order sizes.
Results of Successful Lot Size Optimization
When effectively implemented, material lot size optimization leads to significant improvements in a company’s operational performance.
Businesses see streamlined inventory levels, which reduces waste and enhances the efficiency of manufacturing processes.
Companies that succeed in optimizing their lot sizes often gain a competitive edge through improved service levels and customer satisfaction.
With the right inventory at hand, they can meet customer demands promptly and consistently.
Moreover, the financial outcomes can be substantial, with reductions in both variable and fixed costs contributing to increased profitability.
The monetary savings from efficient inventory management enable further investment in business growth initiatives.
In conclusion, material lot size optimization is a strategic approach that requires careful analysis, planning, and cooperation across a company’s departments.
Though it presents several challenges, the potential rewards far outweigh the risks, leading to a leaner, more efficient, and financially sound operation.
As organizations continue to adapt to changing market conditions, the role of lot size optimization remains a fundamental pillar of effective supply chain management.
資料ダウンロード
QCD調達購買管理クラウド「newji」は、調達購買部門で必要なQCD管理全てを備えた、現場特化型兼クラウド型の今世紀最高の購買管理システムとなります。
ユーザー登録
調達購買業務の効率化だけでなく、システムを導入することで、コスト削減や製品・資材のステータス可視化のほか、属人化していた購買情報の共有化による内部不正防止や統制にも役立ちます。
NEWJI DX
製造業に特化したデジタルトランスフォーメーション(DX)の実現を目指す請負開発型のコンサルティングサービスです。AI、iPaaS、および先端の技術を駆使して、製造プロセスの効率化、業務効率化、チームワーク強化、コスト削減、品質向上を実現します。このサービスは、製造業の課題を深く理解し、それに対する最適なデジタルソリューションを提供することで、企業が持続的な成長とイノベーションを達成できるようサポートします。
オンライン講座
製造業、主に購買・調達部門にお勤めの方々に向けた情報を配信しております。
新任の方やベテランの方、管理職を対象とした幅広いコンテンツをご用意しております。
お問い合わせ
コストダウンが利益に直結する術だと理解していても、なかなか前に進めることができない状況。そんな時は、newjiのコストダウン自動化機能で大きく利益貢献しよう!
(Β版非公開)