- お役立ち記事
- Material Management for Streamlining Work Scheduling
月間76,176名の
製造業ご担当者様が閲覧しています*
*2025年3月31日現在のGoogle Analyticsのデータより
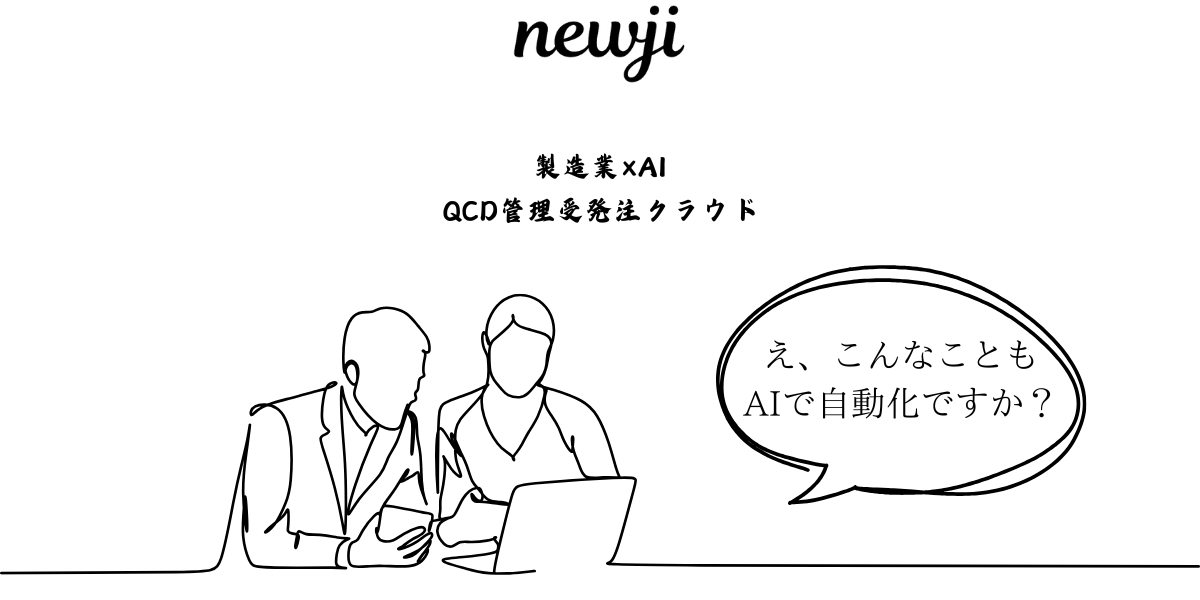
Material Management for Streamlining Work Scheduling
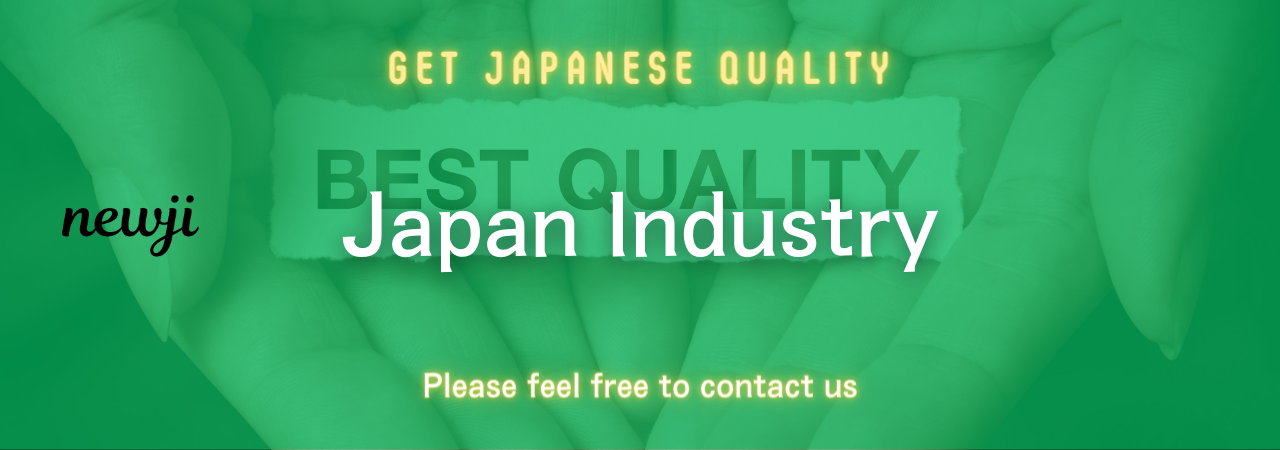
Managing materials effectively is pivotal for streamlining work scheduling in various industries, from manufacturing to construction.
Without proper material management, projects can face delays, higher costs, and reduced efficiency.
This discussion will explore the best practices for material management and how they contribute to more efficient work scheduling.
目次
Understanding Material Management
Material management involves the planning, procurement, handling, and monitoring of materials required for production or project execution.
It ensures that the right materials are available at the right time, in the right quantity, and at the right cost.
Effective material management minimizes waste, reduces storage costs, and enhances productivity.
Importance of Material Management in Work Scheduling
Work scheduling involves organizing tasks and resources to complete a project on time.
Effective material management is crucial for accurate work scheduling because it ensures that necessary resources are available when needed.
When materials are managed efficiently, project timelines are more predictable and easier to manage.
Key Elements of Material Management
Several key elements contribute to effective material management.
Understanding these elements can help businesses streamline their processes and improve work scheduling.
1. Inventory Control
Inventory control involves tracking and managing the materials on hand to ensure that stock levels are maintained.
This helps prevent overstocking or understocking, both of which can impede productivity.
Regular inventory audits and the use of inventory management software can greatly enhance this process.
2. Supply Chain Coordination
Coordination with suppliers ensures that materials are delivered on time and meet quality standards.
Building strong relationships with reliable suppliers can lead to better pricing, improved quality, and timely delivery of materials, all of which are essential for streamlined work scheduling.
3. Demand Forecasting
Accurate demand forecasting helps in predicting material requirements based on upcoming projects and production schedules.
Using historical data and market analysis, businesses can anticipate material needs and plan accordingly.
This reduces the risk of delays caused by material shortages.
4. Procurement Management
Efficient procurement management involves selecting the right suppliers, negotiating favorable terms, and ensuring timely delivery of materials.
This requires a well-defined procurement process and ongoing evaluation of supplier performance.
5. Material Handling
Proper material handling ensures that materials are stored, transported, and utilized efficiently.
This includes effective storage solutions, appropriate handling equipment, and trained personnel.
Good material handling practices reduce damage and waste, contributing to more efficient work scheduling.
Best Practices for Material Management
Implementing best practices in material management can significantly streamline work scheduling.
Here are some strategies to consider:
1. Implement an Inventory Management System
Using an inventory management system helps track inventory levels, monitor usage, and automatically reorder materials when stocks are low.
This system can provide real-time data, reducing the risk of overstocking or understocking and ensuring that materials are available when needed.
2. Develop Strong Supplier Relationships
Building strong relationships with suppliers can lead to better pricing, improved material quality, and more reliable delivery schedules.
Regular communication and collaboration with suppliers can help address any issues promptly and maintain a smooth supply chain.
3. Use Just-In-Time (JIT) Inventory
JIT inventory management involves ordering and receiving materials only when they are needed for production.
This reduces storage costs and minimizes waste but requires precise planning and strong supplier relationships to be effective.
4. Conduct Regular Audits
Regular audits of inventory and material management processes help identify inefficiencies and areas for improvement.
Audits can uncover discrepancies in stock levels, highlight issues with material handling, and ensure compliance with industry standards.
5. Train Staff on Material Handling
Training staff on proper material handling techniques reduces the risk of damage and waste.
This includes training on the use of equipment, storage solutions, and safety protocols.
Trained personnel can handle materials more efficiently, contributing to smoother work scheduling.
The Role of Technology in Material Management
Advancements in technology have revolutionized material management, offering tools and systems that enhance efficiency.
1. Inventory Management Software
Inventory management software provides real-time data on stock levels, material usage, and reorder points.
These systems can automate many aspects of inventory control, reducing the risk of human error and improving accuracy.
2. Supply Chain Management Tools
Supply chain management tools help businesses coordinate with suppliers, track shipments, and monitor delivery schedules.
These tools can provide insights into the entire supply chain, helping to identify potential delays and bottlenecks.
3. Automation and Robotics
Automation and robotics can streamline material handling processes, reducing the need for manual labor and minimizing errors.
Automated storage and retrieval systems, for example, can quickly and accurately store and retrieve materials, improving efficiency.
4. Data Analytics
Data analytics can provide valuable insights into material usage, supply chain performance, and inventory levels.
By analyzing data, businesses can make informed decisions, anticipate future material needs, and optimize their material management processes.
Conclusion
Effective material management is essential for streamlining work scheduling and improving overall productivity.
By implementing best practices such as inventory control, supply chain coordination, demand forecasting, and the use of technology, businesses can ensure that materials are available when needed, reducing delays and costs.
Continuous improvement and regular audits of material management processes will help maintain efficiency and support successful project completion.
資料ダウンロード
QCD管理受発注クラウド「newji」は、受発注部門で必要なQCD管理全てを備えた、現場特化型兼クラウド型の今世紀最高の受発注管理システムとなります。
ユーザー登録
受発注業務の効率化だけでなく、システムを導入することで、コスト削減や製品・資材のステータス可視化のほか、属人化していた受発注情報の共有化による内部不正防止や統制にも役立ちます。
NEWJI DX
製造業に特化したデジタルトランスフォーメーション(DX)の実現を目指す請負開発型のコンサルティングサービスです。AI、iPaaS、および先端の技術を駆使して、製造プロセスの効率化、業務効率化、チームワーク強化、コスト削減、品質向上を実現します。このサービスは、製造業の課題を深く理解し、それに対する最適なデジタルソリューションを提供することで、企業が持続的な成長とイノベーションを達成できるようサポートします。
製造業ニュース解説
製造業、主に購買・調達部門にお勤めの方々に向けた情報を配信しております。
新任の方やベテランの方、管理職を対象とした幅広いコンテンツをご用意しております。
お問い合わせ
コストダウンが利益に直結する術だと理解していても、なかなか前に進めることができない状況。そんな時は、newjiのコストダウン自動化機能で大きく利益貢献しよう!
(β版非公開)