- お役立ち記事
- Material properties of steel cutting tools and appropriate selection Key points for improving processing efficiency
月間77,185名の
製造業ご担当者様が閲覧しています*
*2025年2月28日現在のGoogle Analyticsのデータより
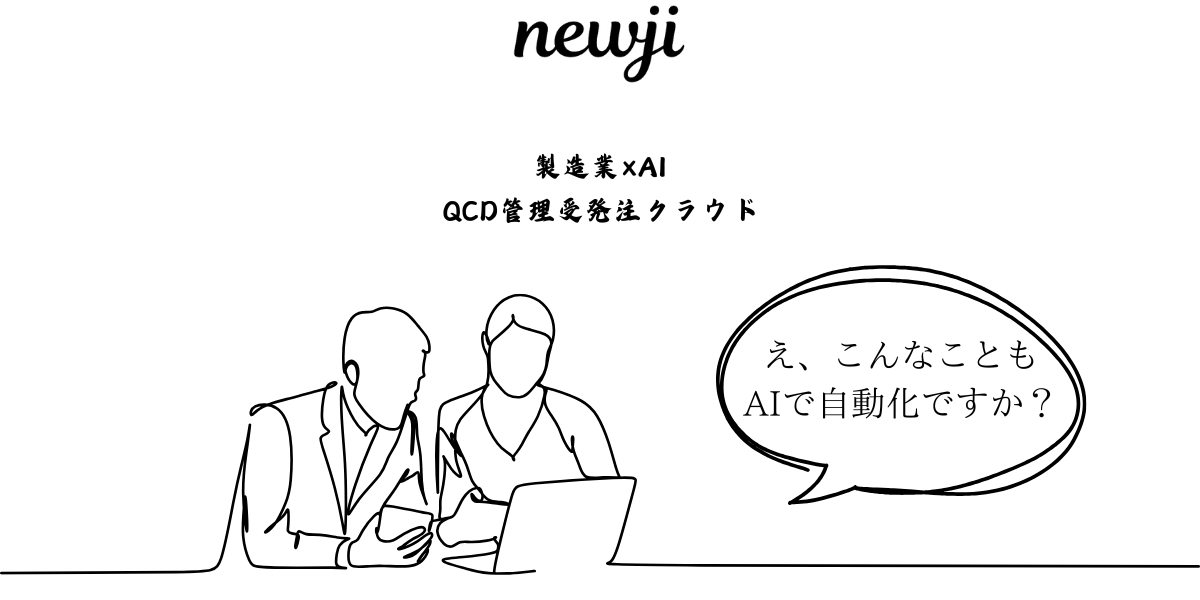
Material properties of steel cutting tools and appropriate selection Key points for improving processing efficiency
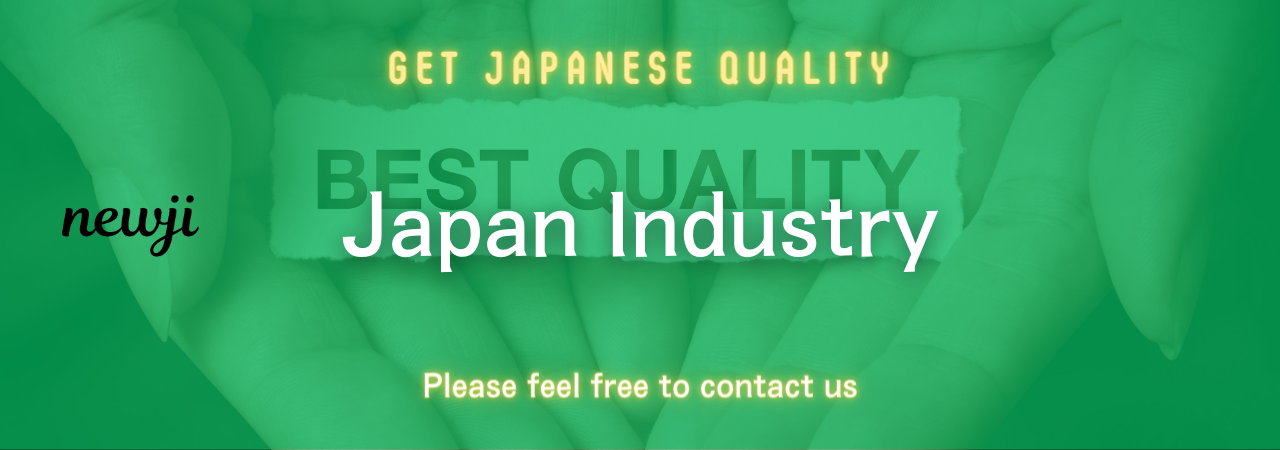
目次
Understanding Material Properties of Steel Cutting Tools
Steel cutting tools are essential components in the manufacturing and metalworking industries.
Their efficiency and effectiveness heavily depend on the material properties they possess.
Understanding these properties can significantly affect the quality of the work and the longevity of the tool itself.
Steel cutting tools are primarily made from high-speed steel (HSS), carbon steel, and tool steel.
Each of these materials has distinct properties that make them suitable for different applications.
High-speed steel (HSS) is known for maintaining its hardness at high temperatures, making it ideal for high-speed machining operations.
It can withstand the heat generated during cutting without losing its form or sharpness.
This makes HSS suitable for cutting tools like drills and end mills, where precision and durability are critical.
Carbon steel, on the other hand, is less expensive but tends to lose its hardness at elevated temperatures.
It is often used for simpler, low-speed cutting tools such as hand tools and woodcutting saws.
Though not suitable for high-speed applications, carbon steel tools are valued for their affordability and ease of sharpening.
Tool steel is specifically designed for making cutting tools.
It offers a good balance between hardness and toughness, making it perfect for creating die-cutting tools and punches.
Tool steel’s high resistance to deformation makes it a popular choice for applications requiring precision and longevity.
The Importance of Appropriate Tool Selection
Selecting the right material for a cutting tool depends on several factors, including the type of material being machined, the speed of operation, and the desired precision.
Choosing the appropriate tool can significantly improve processing efficiency and reduce costs in the long term.
When machining harder materials like stainless steel or titanium, tools made from tougher materials like HSS or tool steel are preferred.
These tools can handle the stresses and heat generated, leading to longer tool life and less downtime for replacements.
For softer materials like aluminum or plastic, a tool with a sharper edge and a softer material like carbon steel might be sufficient.
This is because the lower cutting forces and temperatures involved do not require the durability offered by more expensive materials.
Tool coatings also play a crucial role in enhancing tool performance.
Coatings like titanium nitride (TiN) or diamond-like carbon (DLC) can increase the hardness of the tool surface, reduce friction, and improve heat resistance, further extending tool life.
Factors to Consider in Tool Selection
When selecting cutting tools, several specific factors should be considered to optimize performance.
These include tool geometry, surface coating, and the machining environment.
Tool geometry, including the angle and sharpness of cutting edges, greatly affects cutting efficiency and surface finish.
A well-designed tool geometry can minimize cutting forces and reduce tool wear.
Surface coatings, as mentioned earlier, can enhance performance by reducing friction and improving thermal resistance.
The choice of coating should align with the material being processed and the operational conditions.
The machining environment, such as coolant usage and machine stability, also influences tool performance.
Proper coolant application can help control temperature, reduce tool wear, and improve surface finish.
A stable machine setup minimizes vibrations that could lead to premature tool failure or poor workpiece quality.
Improving Processing Efficiency with the Right Tools
An appropriate selection of steel cutting tools can lead to significant improvements in processing efficiency.
Efficiency gains can come from various aspects such as faster cutting speeds, prolonged tool life, and better quality of the finished product.
Faster cutting speeds are achievable when using the right tool material and design.
By reducing machining time, productivity increases, leading to higher output and potentially reduced costs.
Prolonged tool life is a direct result of selecting quality materials and proper coatings.
Fewer tool replacements mean less downtime, which translates to a more efficient operation.
Improved quality of finished products is another advantage.
Choosing the right tools can lead to smoother finishes and more accurate dimensions, reducing the need for additional finishing operations.
Conclusion
Understanding the material properties of steel cutting tools and making informed selections is critical for any manufacturing operation.
It affects not only the tool’s performance but also impacts productivity and quality outcomes.
By considering factors such as material hardness, application speed, and environmental conditions, manufacturers can select tools that not only meet their needs but also contribute to a more efficient and cost-effective production process.
This knowledge empowers industries to optimize their processes, innovate with confidence, and stay competitive in a demanding market.
資料ダウンロード
QCD管理受発注クラウド「newji」は、受発注部門で必要なQCD管理全てを備えた、現場特化型兼クラウド型の今世紀最高の受発注管理システムとなります。
ユーザー登録
受発注業務の効率化だけでなく、システムを導入することで、コスト削減や製品・資材のステータス可視化のほか、属人化していた受発注情報の共有化による内部不正防止や統制にも役立ちます。
NEWJI DX
製造業に特化したデジタルトランスフォーメーション(DX)の実現を目指す請負開発型のコンサルティングサービスです。AI、iPaaS、および先端の技術を駆使して、製造プロセスの効率化、業務効率化、チームワーク強化、コスト削減、品質向上を実現します。このサービスは、製造業の課題を深く理解し、それに対する最適なデジタルソリューションを提供することで、企業が持続的な成長とイノベーションを達成できるようサポートします。
製造業ニュース解説
製造業、主に購買・調達部門にお勤めの方々に向けた情報を配信しております。
新任の方やベテランの方、管理職を対象とした幅広いコンテンツをご用意しております。
お問い合わせ
コストダウンが利益に直結する術だと理解していても、なかなか前に進めることができない状況。そんな時は、newjiのコストダウン自動化機能で大きく利益貢献しよう!
(β版非公開)