- お役立ち記事
- Material selection method for each manufacturing process to achieve cost reduction efforts by the purchasing department
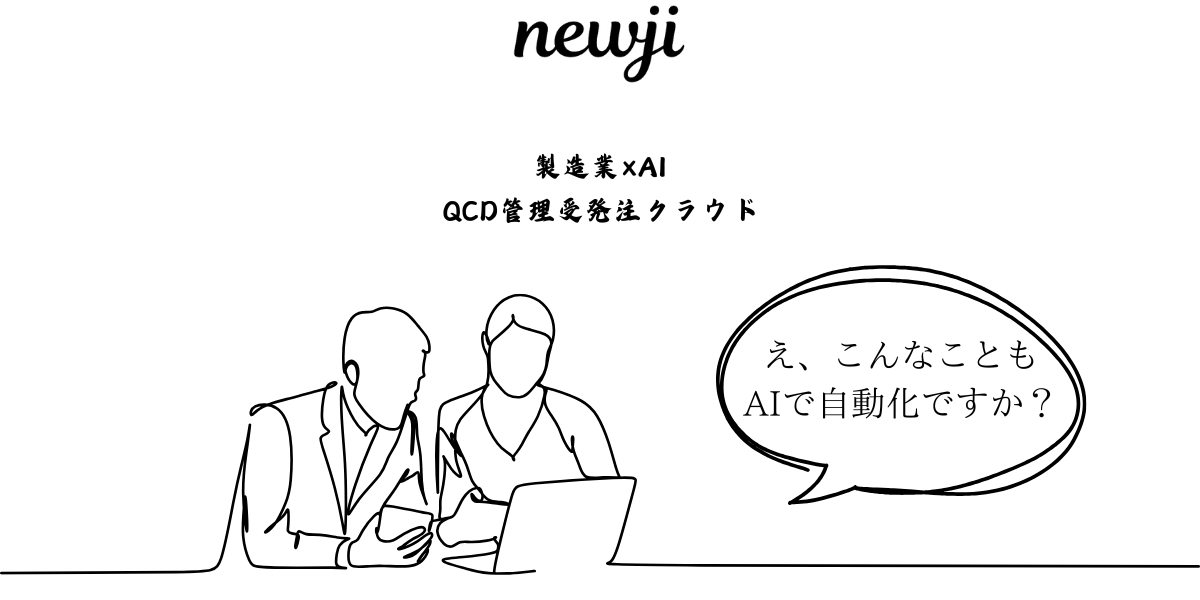
Material selection method for each manufacturing process to achieve cost reduction efforts by the purchasing department
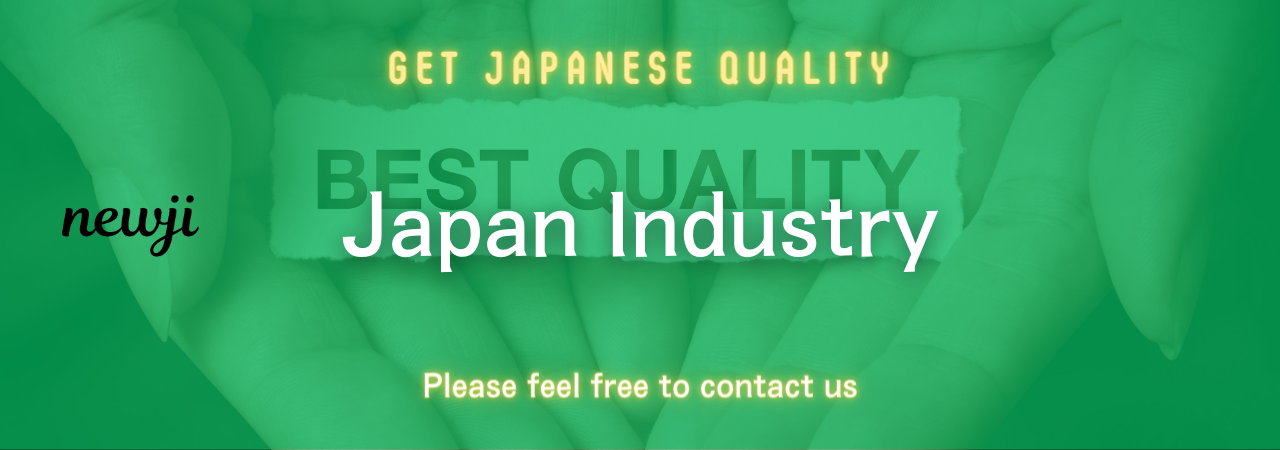
目次
Understanding the Importance of Material Selection
Material selection plays a crucial role in the manufacturing process.
It is a key factor that directly impacts the cost, quality, and efficiency of production.
The purchasing department has a significant responsibility in choosing the right materials to achieve cost reduction while maintaining product standards.
By selecting the most appropriate materials for each manufacturing process, companies can save on costs and boost profitability.
The Role of the Purchasing Department
The purchasing department acts as a bridge between suppliers and the manufacturing team.
They are tasked with sourcing materials that meet both quality and budgetary requirements.
This involves negotiating with suppliers, understanding market trends, and staying updated with technological advancements in materials.
Their job is not just to purchase but to make informed decisions that align with the company’s cost-saving objectives.
Steps in Material Selection
To achieve cost reduction through material selection, the purchasing department can follow a structured approach.
Here are the key steps:
1. Identify the Requirements
The first step is to clearly understand the requirements of the product.
This includes knowing the mechanical properties, chemical resistance, thermal performance, and any other specific needs of the material.
By working closely with the design and engineering teams, the purchasing department can gather detailed information about what is needed.
2. Evaluate Available Materials
Once the requirements are identified, the next step is to assess the available materials in the market.
This involves researching different types of materials and their properties.
Considerations should include cost, availability, and how they perform in the desired manufacturing process.
It’s important to shortlist materials that align with the project’s goals, balancing both performance and cost.
3. Analyze Cost vs. Performance
After shortlisting potential materials, conduct a cost-performance analysis.
This involves evaluating the price of each material against its performance capabilities.
A material that is cheaper might seem appealing, but it may not perform well, leading to higher long-term costs due to defects or inefficiencies.
Choosing a slightly more expensive material that performs better can result in cost savings in the long run.
4. Consider Supply Chain Factors
Supply chain factors such as material lead times, transportation costs, and supplier reliability must be considered as well.
A cheaper material from an unreliable supplier can cause production delays and may lead to higher costs.
The purchasing department needs to ensure that suppliers are capable of providing consistent quality and timely deliveries.
5. Test and Validate
Before making a final decision, it’s advisable to conduct tests and validations.
Prototype testing can help ensure that the selected material meets all the necessary requirements in real-world scenarios.
This step helps in verifying all assumptions made during the material evaluation process.
6. Implement and Monitor
Once a material is selected, it’s essential to implement it in the production process and monitor its performance continuously.
Regular feedback should be gathered from the manufacturing team to ensure that the material is meeting expectations.
Any issues or discrepancies should be addressed promptly to avoid unnecessary costs.
Strategies for Cost Reduction Through Material Selection
There are several strategies the purchasing department can employ to maximize cost-efficiency through material selection:
Leverage Volume Discounts
Purchasing materials in larger volumes can help secure discounts from suppliers.
By consolidating orders or aligning with production schedules, companies can benefit from economies of scale.
Effective planning and forecasting can help identify opportunities for bulk purchasing, thus saving costs.
Explore Alternative Materials
Sometimes, alternative materials can offer cost savings without compromising on quality.
The purchasing department should continuously explore new materials or technologies that can be adopted into the manufacturing process.
Staying current with industry trends and innovations can reveal materials that are both cost-effective and suitable for production needs.
Optimize Material Usage
Reducing waste is another effective way to cut costs.
Optimizing the usage of materials ensures that less is wasted during the manufacturing process.
This might involve refining production techniques or implementing quality control measures that reduce scrap.
Conclusion
Material selection is a critical aspect of manufacturing that directly influences a company’s cost structure.
The purchasing department plays a pivotal role in this process by carefully evaluating, selecting, and procuring materials that align with quality and cost targets.
By following a structured material selection approach and employing cost-reduction strategies, a company can significantly enhance its profitability.
Ultimately, the goal is to strike a balance between material cost and performance, ensuring that products are of high quality while keeping production costs low.
資料ダウンロード
QCD調達購買管理クラウド「newji」は、調達購買部門で必要なQCD管理全てを備えた、現場特化型兼クラウド型の今世紀最高の購買管理システムとなります。
ユーザー登録
調達購買業務の効率化だけでなく、システムを導入することで、コスト削減や製品・資材のステータス可視化のほか、属人化していた購買情報の共有化による内部不正防止や統制にも役立ちます。
NEWJI DX
製造業に特化したデジタルトランスフォーメーション(DX)の実現を目指す請負開発型のコンサルティングサービスです。AI、iPaaS、および先端の技術を駆使して、製造プロセスの効率化、業務効率化、チームワーク強化、コスト削減、品質向上を実現します。このサービスは、製造業の課題を深く理解し、それに対する最適なデジタルソリューションを提供することで、企業が持続的な成長とイノベーションを達成できるようサポートします。
オンライン講座
製造業、主に購買・調達部門にお勤めの方々に向けた情報を配信しております。
新任の方やベテランの方、管理職を対象とした幅広いコンテンツをご用意しております。
お問い合わせ
コストダウンが利益に直結する術だと理解していても、なかなか前に進めることができない状況。そんな時は、newjiのコストダウン自動化機能で大きく利益貢献しよう!
(Β版非公開)