- お役立ち記事
- Material supply quality standards and supplier evaluation points that are important to the purchasing department
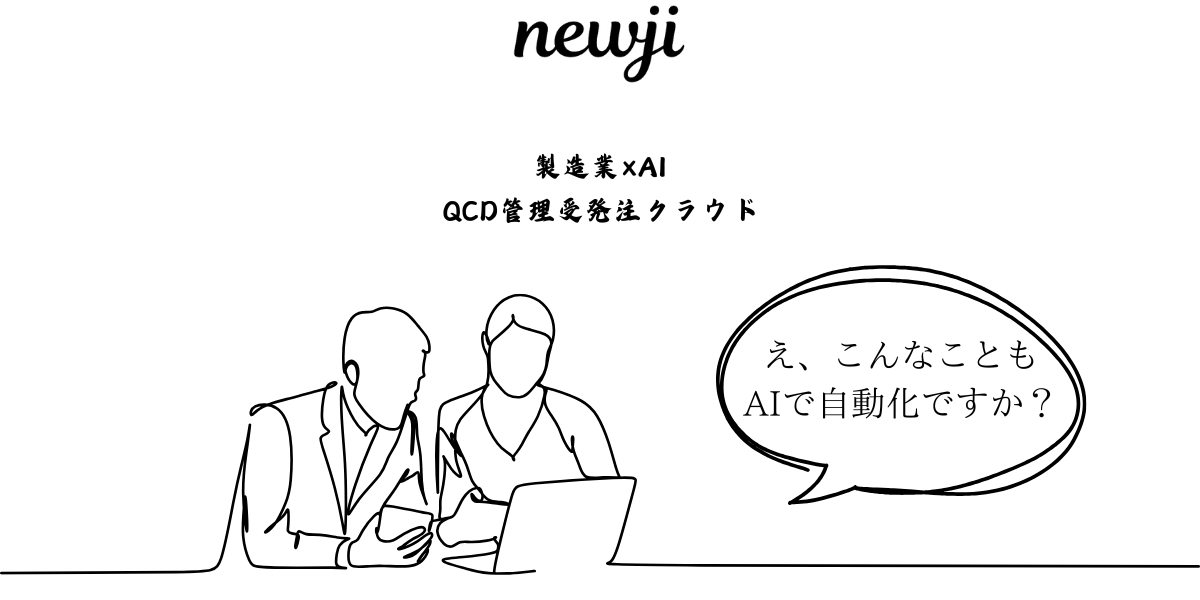
Material supply quality standards and supplier evaluation points that are important to the purchasing department
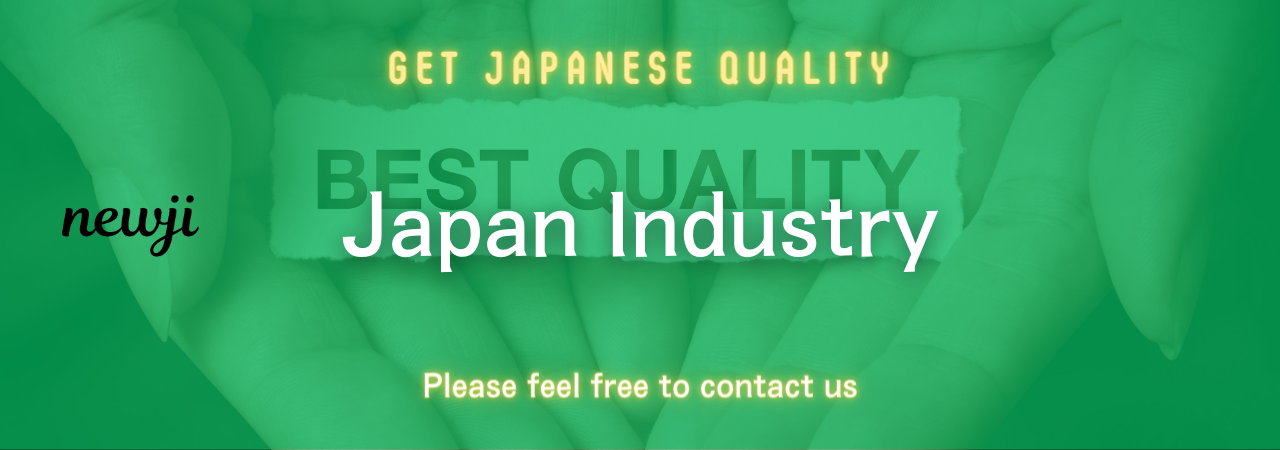
目次
Understanding Material Supply Quality Standards
In the world of purchasing and supply chain management, ensuring high-quality materials is paramount.
Material supply quality standards serve as the benchmark to measure whether the materials we receive align with our company’s requirements.
This involves assessing various factors such as durability, performance, safety, and compliance with legal regulations.
These standards help minimize risks associated with product defects and ensure customer satisfaction.
Quality in material supply involves both qualitative and quantitative measures.
Quantitative measures refer to specifications that can be counted or measured, such as dimensions and resistance levels.
For instance, a purchasing department might require a specific thickness or tensile strength for raw materials.
Qualitative measures focus on attributes like appearance, texture, and odor, which are often more subjective.
Both types of measures are crucial in evaluating the quality of materials supplied.
Key Components of Material Supply Quality Standards
When developing quality standards for material supply, it is important to focus on several key components.
These include:
1. **Specifications and Requirements**: Clearly defined specifications for materials are essential.
These include dimensions, tolerances, chemical compositions, and other technical criteria.
A detailed specification ensures that everyone in the supply chain understands what is required.
2. **Testing and Inspection**: Rigorous testing and inspection are vital to ensure that materials meet the required standards.
This can include visual inspections, physical tests, and chemical analyses depending on the material and its intended use.
Gathering data from these tests can indicate whether the materials meet the desired quality levels.
3. **Compliance and Certifications**: Many industries require specific certifications or safety compliance for materials.
These can include ISO certifications, safety data sheets, or environmental compliance regulations.
Ensuring that suppliers meet these certifications is a critical part of quality assurance.
4. **Risk Management**: Identifying potential risks associated with material supply is essential.
This includes addressing potential disruptions, quality defects, or delivery failures.
Effective risk management strategies can mitigate potential issues before they impact the supply chain.
Supplier Evaluation Points for the Purchasing Department
The purchasing department plays a crucial role in selecting and evaluating suppliers to ensure a reliable and high-quality material supply.
The evaluation process should be thorough and holistic, considering various criteria to assess a supplier’s ability to deliver consistently.
Here are some important supplier evaluation points:
Consistency and Reliability
Consistency in delivering quality materials on time is one of the most critical factors in supplier evaluation.
Purchasing departments must assess a supplier’s track record for reliability.
This includes evaluating the supplier’s history of meeting delivery deadlines and maintaining material quality over time.
Consistent suppliers significantly reduce disruptions and enhance supply chain efficiency.
Financial Stability
A supplier’s financial health can directly impact its ability to deliver materials over the long term.
Conducting financial assessments, such as analyzing credit ratings and financial statements, can offer insight into a supplier’s stability.
Choosing suppliers with sound financial footing helps minimize the risk of interruptions due to financial difficulties.
Capacity and Flexibility
Evaluating a supplier’s production capacity is crucial, particularly for businesses with fluctuating demand.
Suppliers need to have the capacity to meet increased orders and the flexibility to adapt to any changes in requirements.
This adaptability ensures that the purchasing department can respond effectively to market dynamics without facing material shortages.
Compliance and Sustainability
Ensuring that suppliers adhere to legal, environmental, and industry standards is essential.
This involves verifying that suppliers have the necessary certifications and compliance with safety and environmental regulations.
Increasingly, sustainability is also a vital criterion, with many organizations prioritizing suppliers who promote sustainable practices.
Building Strong Supplier Relationships
Effective supplier management is not just about evaluation and selection; it’s also about fostering strong relationships.
Open and transparent communication forms the foundation of a productive partnership with suppliers.
Regular meetings and performance reviews can help maintain alignment on quality standards and expectations.
Collaboration with suppliers can lead to innovations and improvements in the supply chain.
By working together to solve problems and enhance processes, both parties can benefit from increased efficiency and reduced costs.
Strong relationships can also provide the flexibility needed during unforeseen disruptions, further securing the supply chain.
The Role of Technology
Leveraging technology can improve the efficiency and effectiveness of supplier evaluations and relationships.
Tools such as supplier management software allow purchasing departments to track supplier performance, streamline communication, and manage contracts efficiently.
These technologies can assist in maintaining up-to-date information on suppliers and quickly address any issues that may arise.
In conclusion, adhering to stringent material supply quality standards and implementing comprehensive supplier evaluations are critical functions of the purchasing department.
By focusing on these areas, organizations can ensure a steady supply of high-quality materials, minimize risks, and enhance operational efficiency.
Building robust supplier relationships and leveraging technology further solidify this process, ensuring long-term success and competitiveness in the market.
資料ダウンロード
QCD調達購買管理クラウド「newji」は、調達購買部門で必要なQCD管理全てを備えた、現場特化型兼クラウド型の今世紀最高の購買管理システムとなります。
ユーザー登録
調達購買業務の効率化だけでなく、システムを導入することで、コスト削減や製品・資材のステータス可視化のほか、属人化していた購買情報の共有化による内部不正防止や統制にも役立ちます。
NEWJI DX
製造業に特化したデジタルトランスフォーメーション(DX)の実現を目指す請負開発型のコンサルティングサービスです。AI、iPaaS、および先端の技術を駆使して、製造プロセスの効率化、業務効率化、チームワーク強化、コスト削減、品質向上を実現します。このサービスは、製造業の課題を深く理解し、それに対する最適なデジタルソリューションを提供することで、企業が持続的な成長とイノベーションを達成できるようサポートします。
オンライン講座
製造業、主に購買・調達部門にお勤めの方々に向けた情報を配信しております。
新任の方やベテランの方、管理職を対象とした幅広いコンテンツをご用意しております。
お問い合わせ
コストダウンが利益に直結する術だと理解していても、なかなか前に進めることができない状況。そんな時は、newjiのコストダウン自動化機能で大きく利益貢献しよう!
(Β版非公開)