- お役立ち記事
- Maximizing Efficiency in Japanese Manufacturing: The Importance of Shot Count
月間76,176名の
製造業ご担当者様が閲覧しています*
*2025年3月31日現在のGoogle Analyticsのデータより
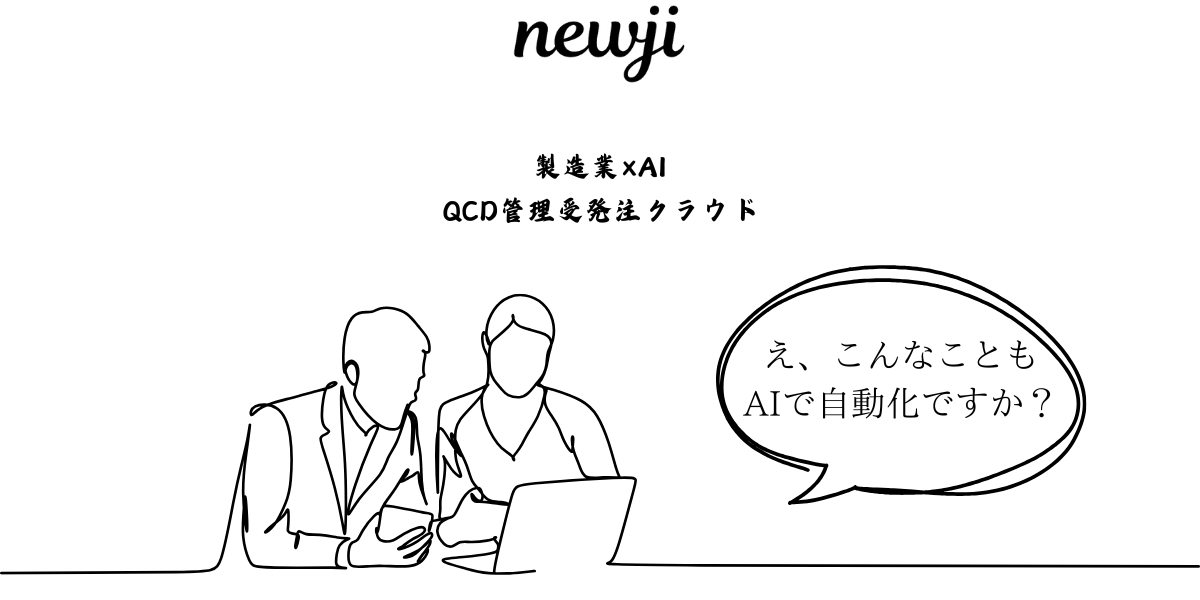
Maximizing Efficiency in Japanese Manufacturing: The Importance of Shot Count
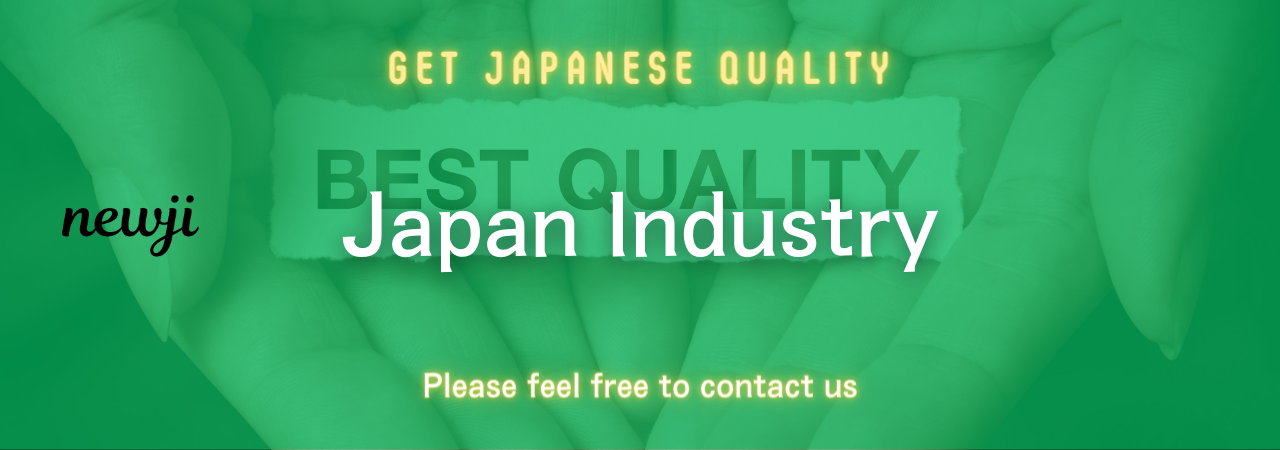
目次
Introduction to Shot Count in Japanese Manufacturing
Japanese manufacturing is renowned for its precision, efficiency, and high-quality output. A critical factor contributing to this reputation is the effective management of shot count in production processes. Understanding and optimizing shot count is essential for maximizing efficiency, reducing costs, and maintaining competitive advantage in the global market.
Shot count refers to the number of times a machine, such as an injection molding machine, cycles to produce a part within a given timeframe.
Accurate shot count management ensures that production processes are streamlined and resources are utilized effectively.
In the context of Japanese manufacturing, shot count is meticulously monitored and optimized to align with production goals and quality standards.
This article delves into the importance of shot count, exploring its impact on procurement and purchasing, supplier negotiations, market conditions, and best practices for achieving maximum efficiency.
Understanding Shot Count
Definition and Relevance
Shot count is a measure of the number of production cycles a machine completes within a specific period.
It is commonly used in industries such as injection molding, where precision and consistency are paramount.
The relevance of shot count lies in its ability to directly influence production efficiency and overall output.
By monitoring shot count, manufacturers can assess the performance of their machinery and identify areas for improvement.
Factors Affecting Shot Count
Several factors can affect the shot count, including machine speed, cycle time, and material handling.
Machine speed determines how quickly a machine can complete each cycle.
Cycle time encompasses the entire process from loading materials to producing the final part.
Efficient material handling ensures that machines operate continuously without interruptions.
Environmental factors, such as temperature and humidity, can also impact shot count by influencing material properties and machine performance.
Proper maintenance of equipment is crucial to sustaining optimal shot count levels.
The Importance of Shot Count in Japanese Manufacturing
Enhancing Production Efficiency
Maximizing shot count is vital for enhancing production efficiency.
Higher shot counts indicate that machinery is operating at peak performance, leading to increased output without compromising quality.
Japanese manufacturers prioritize efficiency to remain competitive in global markets.
By optimizing shot count, they can produce more goods in less time, reducing lead times and meeting customer demands promptly.
Cost Management
Effective shot count management contributes to cost control.
Higher shot counts can lower the cost per unit by distributing fixed costs over a larger number of products.
Additionally, optimizing shot count reduces energy consumption and minimizes material waste, further contributing to cost savings.
Quality Assurance
Maintaining an optimal shot count is essential for consistent product quality.
Frequent cycles can lead to wear and tear on machinery, potentially affecting precision.
Japanese manufacturers implement stringent quality control measures to balance shot count with product integrity.
Competitive Advantage
Japanese manufacturing’s focus on shot count optimization provides a competitive edge.
Efficient production processes enable faster turnaround times and the ability to adapt to market changes swiftly.
This agility allows Japanese companies to maintain leadership in various sectors, including automotive, electronics, and consumer goods.
Shot Count from the Perspective of Procurement and Purchasing
Supplier Selection and Evaluation
In procurement and purchasing, understanding a supplier’s shot count capabilities is crucial.
Suppliers that can achieve high shot counts consistently are preferred, as they contribute to reliable and efficient production.
Evaluating a supplier’s machinery, maintenance practices, and production processes helps assess their shot count potential.
Negotiating Terms and Pricing
Shot count plays a role in negotiating favorable terms and pricing with suppliers.
Manufacturers may leverage high shot count capabilities to negotiate bulk pricing or better payment terms.
Conversely, if a supplier has limited shot count capacity, it may influence pricing models or lead to seeking alternative suppliers.
Supply Chain Efficiency
Efficient shot count management ensures a smooth supply chain.
High shot counts enable suppliers to meet demand fluctuations without delays, enhancing overall supply chain resilience.
Procurement teams must consider shot count capabilities when designing supply chain strategies to mitigate risks associated with production bottlenecks.
Long-term Partnerships
Building long-term partnerships with suppliers requires alignment in shot count management.
Shared goals in optimizing shot count foster collaboration, leading to mutual benefits such as innovation and sustained quality improvements.
Consistent communication and performance monitoring are essential to maintain these partnerships.
Advantages and Disadvantages of Focusing on Shot Count
Advantages
Focusing on shot count offers several advantages:
- Increased Productivity: Higher shot counts lead to greater output without additional resources.
- Cost Efficiency: Optimizing shot count reduces per-unit costs and minimizes waste.
- Competitive Edge: Enhanced efficiency and quality provide a market advantage.
- Scalability: Efficient shot count management facilitates scaling production to meet market demands.
Disadvantages
However, excessive focus on shot count can present challenges:
- Quality Compromise: Pushing shot counts too high may lead to decreased product quality.
- Increased Wear and Tear: Higher shot counts accelerate machinery wear, leading to more frequent maintenance and replacements.
- Resource Strain: Sustaining high shot counts can strain resources, including energy and raw materials.
- Flexibility Limitations: High shot counts may reduce the flexibility to adapt to changes in production requirements.
Balancing shot count optimization with these potential drawbacks is essential for sustainable manufacturing practices.
Supplier Negotiation Techniques Related to Shot Count
Understanding Supplier Capabilities
Before entering negotiations, it’s vital to thoroughly understand a supplier’s shot count capabilities.
Assessing their machinery, maintenance schedules, and production processes provides insight into their potential performance.
This knowledge forms the foundation for effective negotiation strategies tailored to both parties’ strengths and limitations.
Setting Clear Expectations
Communicate clear expectations regarding shot count targets and quality standards.
Establishing mutually agreed-upon benchmarks ensures alignment and fosters a collaborative relationship.
Clarity in expectations minimizes misunderstandings and sets the stage for achieving shared goals.
Leveraging Data and Analytics
Utilize data and analytics to support negotiation discussions.
Presenting concrete data on shot count performance and its impact on overall production can strengthen your negotiation position.
Data-driven arguments are more persuasive and can lead to more favorable terms.
Exploring Incentive Structures
Incorporate incentive structures related to shot count performance.
Offering rewards for exceeding shot count targets or maintaining high efficiency can motivate suppliers to prioritize optimization.
Incentives align the supplier’s objectives with your company’s production goals, fostering a win-win scenario.
Flexibility and Compromise
Maintain flexibility and be willing to compromise during negotiations.
Understanding the supplier’s constraints and finding middle ground can lead to sustainable agreements.
Flexibility helps in building long-term partnerships based on trust and mutual benefit.
Market Conditions Affecting Shot Count Importance
Demand Fluctuations
Market demand can significantly impact the importance of shot count.
During periods of high demand, optimizing shot count ensures that production scales efficiently to meet customer needs.
Conversely, during low demand, maintaining flexibility in shot count allows manufacturers to adjust production without incurring excessive costs.
Technological Advancements
Advancements in manufacturing technology influence shot count management.
Innovations such as automation and smart manufacturing systems enable higher shot counts with improved precision and reduced downtime.
Staying abreast of technological trends is essential for maintaining shot count optimization in a rapidly evolving market.
Global Competition
Intense global competition heightens the need for efficient shot count management.
Manufacturers must optimize shot count to reduce costs and enhance quality, thereby sustaining competitiveness in international markets.
Benchmarking against global standards can drive continuous improvements in shot count practices.
Supply Chain Disruptions
Supply chain disruptions can affect shot count management.
Challenges such as material shortages or logistical delays require flexible shot count strategies to maintain production continuity.
Developing resilient supply chain practices ensures that shot count optimization is sustainable even in adverse conditions.
Best Practices for Maximizing Efficiency Through Shot Count
Regular Maintenance and Upgrades
Conduct regular maintenance and timely upgrades of machinery to sustain high shot counts.
Preventive maintenance minimizes unexpected downtimes and ensures machines operate at peak efficiency.
Investing in advanced machinery can also enhance shot count capabilities, contributing to overall production efficiency.
Employee Training and Engagement
Invest in training programs to educate employees on the importance of shot count and effective management techniques.
Engaged and knowledgeable staff are more likely to identify and implement improvements in shot count processes.
Fostering a culture of continuous improvement encourages proactive efforts to optimize shot counts.
Implementing Lean Manufacturing Principles
Adopt lean manufacturing principles to streamline processes and eliminate waste.
Techniques such as just-in-time production and value stream mapping support shot count optimization by enhancing workflow efficiency.
Lean practices contribute to sustaining high shot counts while maintaining quality and reducing costs.
Utilizing Advanced Analytics
Leverage advanced analytics to monitor and analyze shot count performance.
Data-driven insights enable informed decision-making and the identification of trends that affect shot count efficiency.
Implementing real-time monitoring systems can facilitate immediate adjustments to maintain optimal shot counts.
Collaborative Supplier Relationships
Cultivate collaborative relationships with suppliers focused on shared shot count optimization goals.
Joint initiatives, such as co-development projects or shared best practices, can lead to mutual improvements in shot count management.
Strong supplier partnerships enhance overall supply chain efficiency and support sustained production performance.
Case Studies: Shot Count Optimization in Japanese Manufacturing
Automotive Industry
In the Japanese automotive sector, shot count optimization is critical for manufacturing components with high precision.
Companies implement advanced injection molding techniques to achieve high shot counts while maintaining stringent quality standards.
These practices enable the production of complex automotive parts efficiently, supporting the industry’s reputation for reliability and performance.
Electronics Manufacturing
Japanese electronics manufacturers rely on shot count optimization to produce intricate components for devices such as smartphones and computers.
High shot counts allow for mass production without sacrificing the fine detail required for electronic assemblies.
Continuous improvement initiatives ensure that shot count optimization aligns with the fast-paced nature of the electronics market.
Consumer Goods
In the consumer goods sector, shot count management supports the production of a wide range of products, from household appliances to personal care items.
Efficient shot counts enable manufacturers to meet diverse consumer demands and adapt to market trends swiftly.
This flexibility is essential for maintaining market relevance and customer satisfaction in a competitive landscape.
Challenges in Shot Count Optimization
Balancing Quantity and Quality
One of the primary challenges in shot count optimization is balancing the need for high production volumes with maintaining quality standards.
Pushing for higher shot counts can lead to increased wear on machinery and potential quality issues if not managed carefully.
Manufacturers must implement rigorous quality control measures to ensure that shot count increases do not compromise product integrity.
Technical Limitations
Technical limitations of machinery can pose obstacles to shot count optimization.
Older equipment may not support higher shot counts without significant upgrades or modifications.
Investing in modern, high-performance machinery is often necessary to overcome these limitations and achieve desired shot counts.
Resource Constraints
Resource constraints, including energy consumption and material costs, can impact shot count management.
High shot counts typically require more energy and raw materials, which can strain budgets and sustainability goals.
Implementing energy-efficient practices and optimizing material usage are essential strategies to address resource constraints while maintaining high shot counts.
Market Volatility
Market volatility introduces uncertainty that can affect shot count planning.
Fluctuating demand requires adaptable shot count strategies to scale production up or down as needed.
Developing flexible manufacturing processes allows companies to respond swiftly to market changes without disrupting production efficiency.
Future Trends in Shot Count Management
Automation and Robotics
The integration of automation and robotics into manufacturing processes is set to revolutionize shot count management.
Automated systems can achieve higher shot counts with greater precision and reduced human error.
Robotics enhance the consistency and speed of production cycles, contributing to overall efficiency gains.
Artificial Intelligence and Machine Learning
Artificial intelligence (AI) and machine learning (ML) are increasingly being used to optimize shot counts.
AI-driven analytics can predict machine performance and identify optimal shot count levels based on real-time data.
Machine learning algorithms can continuously improve shot count strategies by learning from past performance and adapting to changing conditions.
Sustainable Manufacturing Practices
Sustainable manufacturing practices are influencing shot count management.
Efforts to reduce energy consumption and material waste align with optimizing shot counts for efficiency.
Eco-friendly approaches ensure that shot count optimization contributes to both economic and environmental sustainability.
Advanced Material Technologies
Advances in material technologies, such as high-performance polymers and composites, impact shot count optimization.
New materials may require adjustments in shot count strategies to accommodate their unique properties and processing requirements.
Staying informed about material innovations allows manufacturers to adapt shot count practices effectively, maintaining production efficiency and quality.
Conclusion
Shot count is a pivotal element in Japanese manufacturing that drives efficiency, cost management, and quality assurance.
From the perspectives of procurement and purchasing to supplier negotiations and market adaptability, shot count optimization plays a central role in sustaining competitive advantage.
By implementing best practices such as regular maintenance, employee training, and advanced analytics, manufacturers can maximize shot count efficiency while addressing challenges and embracing future trends.
In the rapidly evolving global market, the importance of shot count in Japanese manufacturing remains steadfast, underpinning the industry’s reputation for excellence and innovation.
Emphasizing shot count management fosters a culture of continuous improvement, ensuring that Japanese manufacturers continue to lead in quality and productivity on the international stage.
資料ダウンロード
QCD管理受発注クラウド「newji」は、受発注部門で必要なQCD管理全てを備えた、現場特化型兼クラウド型の今世紀最高の受発注管理システムとなります。
ユーザー登録
受発注業務の効率化だけでなく、システムを導入することで、コスト削減や製品・資材のステータス可視化のほか、属人化していた受発注情報の共有化による内部不正防止や統制にも役立ちます。
NEWJI DX
製造業に特化したデジタルトランスフォーメーション(DX)の実現を目指す請負開発型のコンサルティングサービスです。AI、iPaaS、および先端の技術を駆使して、製造プロセスの効率化、業務効率化、チームワーク強化、コスト削減、品質向上を実現します。このサービスは、製造業の課題を深く理解し、それに対する最適なデジタルソリューションを提供することで、企業が持続的な成長とイノベーションを達成できるようサポートします。
製造業ニュース解説
製造業、主に購買・調達部門にお勤めの方々に向けた情報を配信しております。
新任の方やベテランの方、管理職を対象とした幅広いコンテンツをご用意しております。
お問い合わせ
コストダウンが利益に直結する術だと理解していても、なかなか前に進めることができない状況。そんな時は、newjiのコストダウン自動化機能で大きく利益貢献しよう!
(β版非公開)