- お役立ち記事
- Maximizing Efficiency in Japanese Manufacturing: The Strategic “Make or Buy” Decision
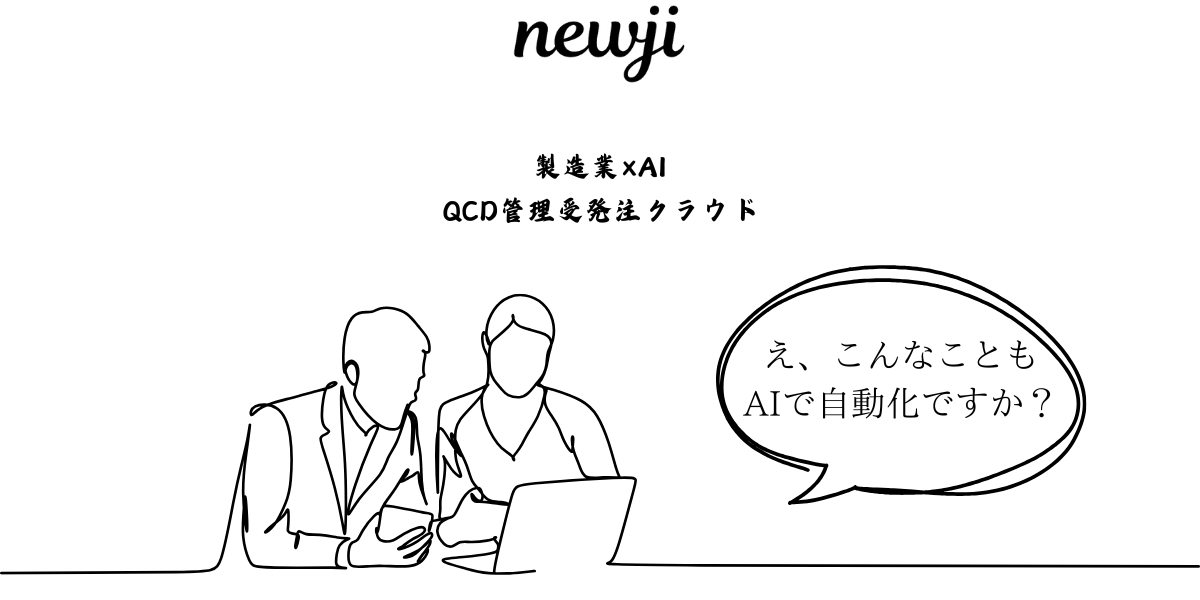
Maximizing Efficiency in Japanese Manufacturing: The Strategic “Make or Buy” Decision
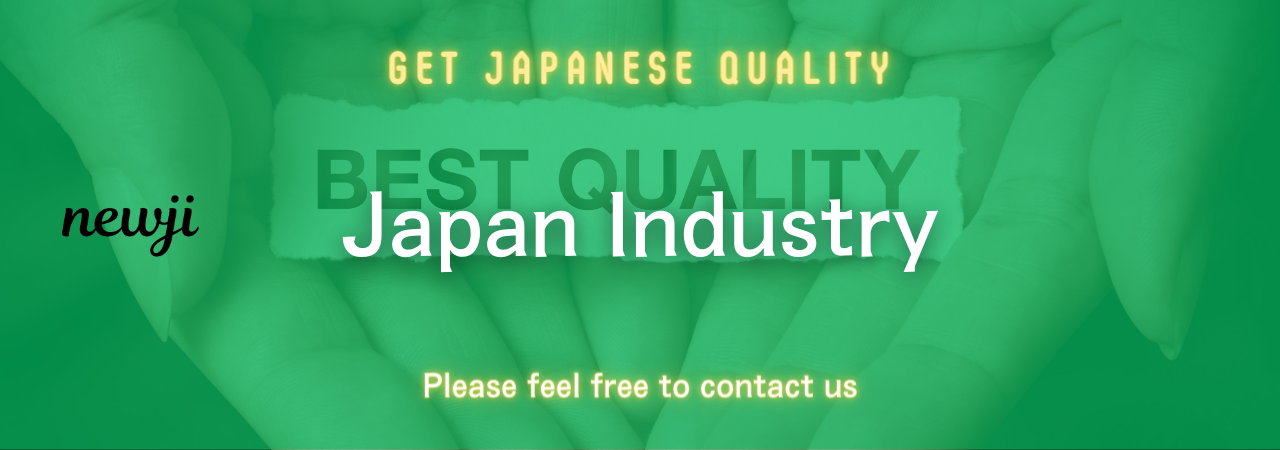
目次
Introduction
In the dynamic landscape of modern manufacturing, the “make or buy” decision stands as a pivotal consideration.
This decision, whether to produce in-house or to outsource from external suppliers, can significantly impact efficiency, quality, and profitability.
When dealing with Japanese suppliers, this decision takes on an added layer of complexity and opportunity.
Known for their meticulous craftsmanship, robust quality controls, and cutting-edge technologies, Japanese manufacturers bring incomparable advantages to the table.
However, making the right “make or buy” decision requires a deep understanding of various facets such as market conditions, supplier negotiation techniques, and logistics.
Understanding the “Make or Buy” Decision
The “make or buy” decision is fundamentally a strategic choice, involving various factors that range from cost and capacity to long-term strategic goals.
Manufacturing in-house (make) provides greater control over quality and schedule, while outsourcing (buy) can offer cost savings and access to specialized expertise.
Key Considerations for the “Make” Decision
1. **Control Over Quality**: In-house production offers unmatched control over the quality of your products.
This is crucial for industries where product standards are imperative, like aerospace, medical devices, and automotive.
2. **Intellectual Property Protection**: Keeping production within your organization helps protect sensitive intellectual property and proprietary technologies.
3. **Customization and Flexibility**: In-house production allows for greater customization and flexibility to adapt to market demands and changes in customer preferences.
Key Considerations for the “Buy” Decision
1. **Cost Efficiency**: Outsourcing can significantly reduce costs, especially when leveraging the scale and expertise of specialized suppliers.
2. **Access to Technology**: Purchasing from suppliers can provide access to state-of-the-art technologies and innovations without the need for heavy capital investment.
3. **Speed to Market**: By leveraging the capabilities of specialized suppliers, companies can often bring products to market faster, satisfying market demands more promptly.
Advantages of Dealing with Japanese Suppliers
Japanese suppliers have developed a global reputation for excellence, particularly in the manufacturing space.
Here are some key benefits:
High Standards of Quality
Japanese companies are renowned for their rigorous quality control standards.
The principle of “Kaizen,” or continuous improvement, ensures that the quality of their products is perpetually refined.
This commitment to quality translates into a superior end product, which can enhance your brand’s reputation.
Technological Advancements
Japan is a global leader in technological innovation.
By partnering with Japanese suppliers, your company can gain access to cutting-edge technologies and manufacturing processes.
This advantage can differentiate your products in a competitive market.
Reliability and Punctuality
Japanese suppliers are well known for their reliability and punctuality.
Their meticulous planning and efficient logistics frameworks ensure timely delivery of products.
This reliability reduces downtime and helps maintain smooth operations.
Challenges in Dealing with Japanese Suppliers
While there are considerable advantages, working with Japanese suppliers also comes with its own set of challenges.
Cultural Differences
Navigating cultural differences can be a significant challenge.
Japanese business culture places a strong emphasis on relationships and trust.
Understanding nuances in communication and business etiquette is essential for successful partnerships.
Language Barriers
Language can be another barrier.
Although many Japanese professionals speak English, complexities of technical and legal details may still pose challenges.
Employing skilled translators or interpreters can mitigate these issues.
Supply Chain Complexity
Distance and complex logistics can complicate the supply chain.
Careful planning and robust logistics management are required to ensure timely deliveries and avoid disruptions.
Best Practices for Supplier Negotiation
Negotiating effectively with Japanese suppliers requires a blend of preparation, cultural understanding, and strategic acumen.
Building Relationships and Trust
Long-term relationships and trust are the cornerstones of Japanese business culture.
Focus on building a strong relationship before diving into hard negotiations.
Attend meetings, visit their facilities, and take the time to understand their business.
Transparent and Detailed Communication
Ensure that your communication is transparent and detailed.
Clear and comprehensive documentation helps avoid misunderstandings and aligns both parties on expectations and deliverables.
Flexible Yet Firm Negotiations
While it is important to be flexible and accommodating, don’t be afraid to stand firm on your critical requirements.
Balance is key; be prepared to seek mutually beneficial solutions.
Market Conditions and Trends
Understanding the current market conditions and trends is essential for making an informed “make or buy” decision.
Economic Factors
Monitor the economic factors such as exchange rates, inflation, and labor costs in Japan.
These elements can significantly impact the cost-effectiveness of your decision.
Technological Developments
Stay updated on the latest technological advancements in your industry.
New technologies can shift the balance in favor of making or buying, depending on their impact on cost and efficiency.
Regulatory Environment
Japan has stringent regulatory standards, especially for industries like pharmaceuticals, automotive, and electronics.
Ensure compliance with both Japanese regulations and international standards.
Implementing Factory Efficiency and Automation
Leveraging the expertise of Japanese suppliers can significantly enhance factory efficiency and automation practices.
Adopting Lean Manufacturing Practices
Japanese suppliers often employ lean manufacturing practices.
Adopt these methodologies to minimize waste, optimize resources, and improve overall efficiency.
Integrating Advanced Automation Technologies
Japanese manufacturers are leaders in automation technologies.
Implementing advanced automation solutions can boost productivity and reduce human error.
Continuous Improvement and Training
Encourage a culture of continuous improvement within your organization.
Regular training and upskilling of your workforce are crucial to maintain high standards of efficiency and quality.
Conclusion
The “make or buy” decision is a strategic choice that requires careful consideration of various factors.
When dealing with Japanese suppliers, the advantages are significant, from exceptional quality standards to technological advancements.
However, challenges like cultural differences and supply chain complexities must be navigated thoughtfully.
Building strong relationships, transparent communication, and staying updated on market conditions are key elements for successful procurement.
By strategically leveraging Japanese suppliers, companies can maximize efficiency, enhance product quality, and achieve their business objectives.
In the ever-evolving landscape of global manufacturing, making informed and strategic decisions will enable your organization to thrive and stay ahead of the competition.
資料ダウンロード
QCD調達購買管理クラウド「newji」は、調達購買部門で必要なQCD管理全てを備えた、現場特化型兼クラウド型の今世紀最高の購買管理システムとなります。
ユーザー登録
調達購買業務の効率化だけでなく、システムを導入することで、コスト削減や製品・資材のステータス可視化のほか、属人化していた購買情報の共有化による内部不正防止や統制にも役立ちます。
NEWJI DX
製造業に特化したデジタルトランスフォーメーション(DX)の実現を目指す請負開発型のコンサルティングサービスです。AI、iPaaS、および先端の技術を駆使して、製造プロセスの効率化、業務効率化、チームワーク強化、コスト削減、品質向上を実現します。このサービスは、製造業の課題を深く理解し、それに対する最適なデジタルソリューションを提供することで、企業が持続的な成長とイノベーションを達成できるようサポートします。
オンライン講座
製造業、主に購買・調達部門にお勤めの方々に向けた情報を配信しております。
新任の方やベテランの方、管理職を対象とした幅広いコンテンツをご用意しております。
お問い合わせ
コストダウンが利益に直結する術だと理解していても、なかなか前に進めることができない状況。そんな時は、newjiのコストダウン自動化機能で大きく利益貢献しよう!
(Β版非公開)