- お役立ち記事
- Maximizing Equipment Uptime in Manufacturing with TPM (Total Productive Maintenance)
Maximizing Equipment Uptime in Manufacturing with TPM (Total Productive Maintenance)
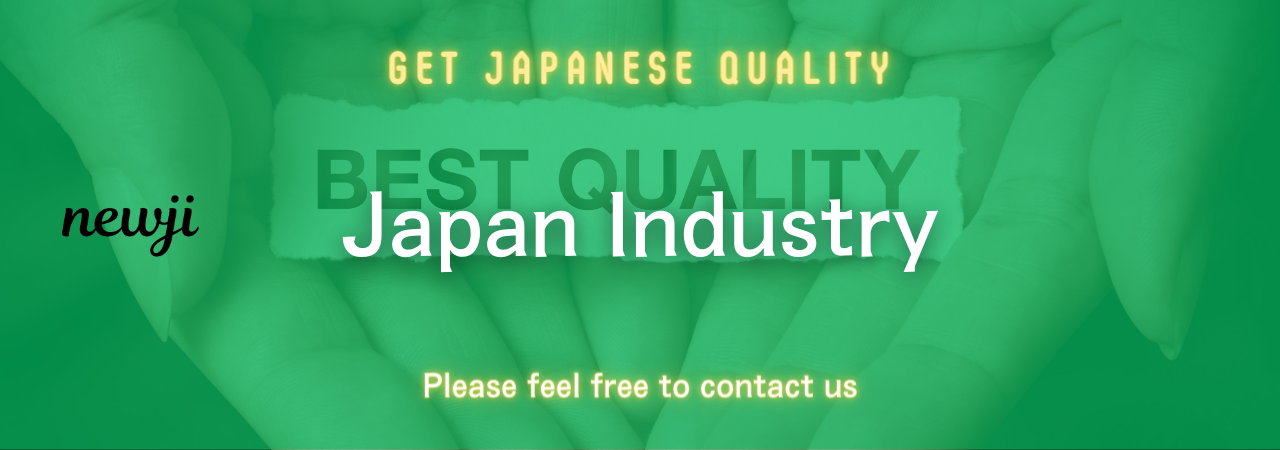
In the fast-paced world of manufacturing, keeping equipment running smoothly is crucial.
One powerful strategy to achieve this is Total Productive Maintenance (TPM).
Let’s dive into how TPM can help maximize equipment uptime and its importance in the manufacturing industry.
目次
Understanding Total Productive Maintenance (TPM)
TPM stands for Total Productive Maintenance.
It is a proactive maintenance approach that involves everyone in the organization.
From the top management to the shop floor workers, everyone plays a role in maintaining and improving equipment performance.
The main goal of TPM is to prevent equipment failures and maximize production efficiency.
The Eight Pillars of TPM
TPM is built on eight fundamental pillars that guide its implementation.
These pillars are designed to address different aspects of equipment maintenance and improvement.
1. **Autonomous Maintenance**: Operators take responsibility for the routine maintenance of their equipment.
This includes tasks like cleaning, lubricating, and inspecting for signs of wear and tear.
2. **Planned Maintenance**: Scheduled maintenance activities are planned in advance to prevent unexpected breakdowns.
This helps ensure that equipment is always in optimal condition.
3. **Quality Maintenance**: This focuses on identifying and eliminating the root causes of defects.
By maintaining high-quality standards, manufacturers can reduce rework and scrap costs.
4. **Focused Improvement**: Continuous improvement initiatives are undertaken to enhance equipment performance.
Teams work together to identify areas of improvement and implement solutions.
5. **Early Equipment Management**: When new equipment is introduced, it is designed and installed with maintenance in mind.
This helps ensure that the equipment is reliable and easy to maintain from the start.
6. **Training and Education**: Employees are provided with the necessary training to perform maintenance tasks effectively.
This empowers them to take responsibility for equipment upkeep.
7. **Safety, Health, and Environment**: Safety protocols are put in place to protect workers and the environment.
Regular inspections and safety drills are conducted to maintain a secure working environment.
8. **Office TPM**: Administrative functions are also streamlined to support maintenance activities.
This includes optimizing procurement processes and ensuring timely availability of spare parts.
Benefits of Implementing TPM
Implementing TPM can have a profound impact on manufacturing operations.
Here are some of the key benefits:
Increased Equipment Reliability
TPM helps in maintaining equipment at optimal performance levels.
Regular maintenance and inspections help identify potential issues before they lead to breakdowns.
This ensures that equipment is reliable and available when needed.
Reduced Downtime
By preventing unexpected breakdowns, TPM significantly reduces downtime.
Scheduled maintenance activities are planned during non-peak hours, minimizing disruptions to production.
Improved Productivity
With equipment operating at peak efficiency, production processes become more efficient.
This leads to increased output and faster delivery times.
Manufacturers can meet customer demands consistently.
Lower Maintenance Costs
Preventive maintenance activities help detect issues early, reducing the need for costly repairs.
Well-maintained equipment also has a longer lifespan, reducing the frequency of replacements.
Enhanced Employee Involvement
TPM encourages a sense of ownership among employees.
Operators take pride in maintaining their equipment, leading to higher morale and job satisfaction.
Steps to Implement TPM in Your Manufacturing Facility
Successfully implementing TPM requires careful planning and execution.
Here are the key steps to follow:
1. Gain Management Support
Top management must understand the importance of TPM and provide their full support.
Without their commitment, it will be challenging to implement TPM effectively.
2. Train Your Team
Provide comprehensive training to all employees on the principles and practices of TPM.
Everyone should understand their role and responsibilities in the maintenance process.
3. Conduct Initial Assessments
Perform a thorough assessment of your current equipment and maintenance practices.
Identify areas that need improvement and set clear goals for TPM implementation.
4. Create a TPM Team
Form a dedicated TPM team comprising members from different departments.
This team will be responsible for driving TPM initiatives and monitoring progress.
5. Develop a TPM Plan
Create a detailed plan outlining the steps and timelines for TPM implementation.
Specify the tasks, responsibilities, and resources required for each phase.
6. Implement Autonomous Maintenance
Start with autonomous maintenance, where operators take responsibility for basic maintenance tasks.
Provide them with the necessary training and tools to perform these tasks efficiently.
7. Schedule Planned Maintenance
Establish a schedule for planned maintenance activities.
Coordinate with production schedules to minimize disruptions.
8. Monitor and Evaluate
Regularly monitor the progress of TPM implementation.
Evaluate the results against your goals and make necessary adjustments.
Conduct periodic audits to ensure compliance with TPM practices.
Challenges of TPM and How to Overcome Them
While TPM offers numerous benefits, its implementation can face several challenges.
Understanding these challenges and how to overcome them is crucial for success.
Resistance to Change
Employees may resist the changes brought about by TPM, fearing additional workload or job insecurity.
To overcome this, involve employees in the TPM process from the beginning.
Communicate the benefits of TPM and how it will positively impact their work.
Lack of Training
Insufficient training can lead to improper maintenance practices.
Ensure that comprehensive training programs are in place to equip employees with the necessary skills.
Regular refresher courses can also help reinforce the training.
Resource Constraints
Implementing TPM requires resources such as time, money, and personnel.
Prioritize TPM activities and allocate resources effectively.
Start with small, manageable projects and gradually scale up as resources become available.
Inadequate Measurement
Without proper metrics, it can be challenging to track the progress of TPM initiatives.
Implement key performance indicators (KPIs) to measure the effectiveness of TPM.
Regularly review these metrics to identify areas that need improvement.
Conclusion
Total Productive Maintenance (TPM) is a powerful strategy for maximizing equipment uptime in manufacturing.
By involving everyone in the organization, TPM ensures that equipment is maintained and improved continuously.
This proactive approach leads to increased reliability, reduced downtime, and improved productivity.
While implementing TPM can be challenging, the benefits far outweigh the efforts required.
With proper planning, training, and commitment, your manufacturing facility can achieve significant gains in performance and efficiency through TPM.
資料ダウンロード
QCD調達購買管理クラウド「newji」は、調達購買部門で必要なQCD管理全てを備えた、現場特化型兼クラウド型の今世紀最高の購買管理システムとなります。
ユーザー登録
調達購買業務の効率化だけでなく、システムを導入することで、コスト削減や製品・資材のステータス可視化のほか、属人化していた購買情報の共有化による内部不正防止や統制にも役立ちます。
NEWJI DX
製造業に特化したデジタルトランスフォーメーション(DX)の実現を目指す請負開発型のコンサルティングサービスです。AI、iPaaS、および先端の技術を駆使して、製造プロセスの効率化、業務効率化、チームワーク強化、コスト削減、品質向上を実現します。このサービスは、製造業の課題を深く理解し、それに対する最適なデジタルソリューションを提供することで、企業が持続的な成長とイノベーションを達成できるようサポートします。
オンライン講座
製造業、主に購買・調達部門にお勤めの方々に向けた情報を配信しております。
新任の方やベテランの方、管理職を対象とした幅広いコンテンツをご用意しております。
お問い合わせ
コストダウンが利益に直結する術だと理解していても、なかなか前に進めることができない状況。そんな時は、newjiのコストダウン自動化機能で大きく利益貢献しよう!
(Β版非公開)