- お役立ち記事
- Maximizing Manufacturing Efficiency with OEE (Overall Equipment Effectiveness)
Maximizing Manufacturing Efficiency with OEE (Overall Equipment Effectiveness)
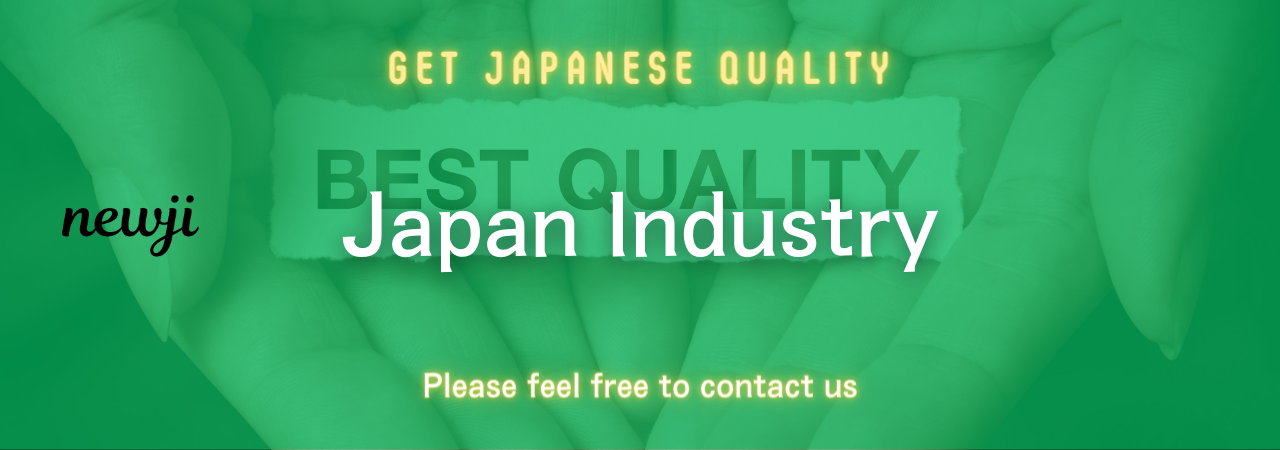
Manufacturing is a complex world where every second counts. Ensuring that your production line operates as smoothly and efficiently as possible is crucial for maintaining competitiveness and profitability.
One effective way to achieve this is by measuring and improving Overall Equipment Effectiveness (OEE).
OEE is a metric that helps manufacturers assess how well their equipment is performing.
目次
What is OEE?
OEE, or Overall Equipment Effectiveness, is a key performance indicator (KPI) used in manufacturing to measure the efficiency and effectiveness of equipment.
It considers three main factors: Availability, Performance, and Quality.
When these factors are considered together, they provide a comprehensive view of how manufacturing equipment is utilized and where improvements can be made.
Availability
Availability refers to the proportion of time that equipment is actually operational compared to the total time it is available for use.
This takes into account both scheduled downtime, such as maintenance, and unscheduled downtime, like breakdowns.
High availability indicates that equipment is consistently operational, while low availability signifies frequent stoppages.
Performance
Performance measures how quickly equipment operates compared to its designed speed.
It factors in speed losses, such as those caused by slow cycles and minor stops.
If your equipment is running slower than it should be, performance will be negatively impacted.
Quality
Quality assesses how many good parts are produced compared to the total number of parts produced.
This metric takes into account defects and rework.
High-quality rates mean fewer defective products and more efficient use of materials and labor.
Calculating OEE
Calculating OEE involves multiplying the three OEE factors: Availability, Performance, and Quality.
The formula for OEE is:
OEE = (Availability) x (Performance) x (Quality)
Each factor is expressed as a percentage, and their product gives the overall OEE score.
For example, if Availability is 90%, Performance is 95%, and Quality is 98%, the OEE would be:
OEE = 0.90 x 0.95 x 0.98 = 0.8361 or 83.61%
An OEE score of 100% represents perfect production, meaning your manufacturing process is running smoothly with no downtime, optimal speed, and no defects.
Benefits of Measuring OEE
Improved Productivity
One of the primary benefits of measuring OEE is the improvement in productivity.
By identifying and reducing downtime, optimizing performance, and enhancing quality, manufacturers can produce more with the same resources.
This leads to increased output and, ultimately, higher profitability.
Informed Decision-Making
OEE provides valuable data that can help in making informed decisions.
By understanding where inefficiencies lie, manufacturers can allocate resources more effectively, prioritize maintenance tasks, and implement targeted improvements.
This data-driven approach ensures that actions are taken based on evidence rather than guesswork.
Cost Savings
Inefficiencies in the manufacturing process often lead to increased costs, whether due to wasted materials, excessive labor, or unnecessary downtime.
By improving OEE, manufacturers can reduce these costs and improve their bottom line.
Enhanced Competitiveness
In today’s competitive market, maintaining high levels of efficiency is crucial for staying ahead.
By consistently measuring and improving OEE, manufacturers can ensure they are operating at peak efficiency, giving them a competitive edge.
Employee Engagement
Measuring and improving OEE can also have a positive impact on employee engagement.
When workers see that their efforts lead to tangible improvements in efficiency, they are more likely to feel valued and motivated.
This can lead to higher morale and lower turnover rates.
Strategies for Maximizing OEE
Regular Maintenance
One of the simplest ways to improve Availability is by scheduling regular maintenance.
Preventive and predictive maintenance can help to identify and address issues before they lead to downtime.
This ensures that equipment is kept in optimal condition and reduces the likelihood of unexpected breakdowns.
Training and Education
Ensuring that employees are well-trained and knowledgeable about the equipment they are operating can significantly improve Performance and Quality.
Offering regular training sessions and providing easy access to operation manuals and troubleshooting guides can help to minimize errors and optimize performance.
Implementing Lean Manufacturing Principles
Lean manufacturing principles, such as the 5S methodology (Sort, Set in order, Shine, Standardize, Sustain), can help to create a more organized and efficient workplace.
By eliminating waste, standardizing processes, and maintaining a clean work environment, manufacturers can improve all aspects of OEE.
Using Technology and Automation
Investing in technology and automation can also play a significant role in maximizing OEE.
Real-time monitoring systems can provide valuable data on equipment performance, allowing for timely interventions.
Automation can reduce human error and ensure that equipment operates at optimal speeds.
Continuous Improvement
Lastly, fostering a culture of continuous improvement is essential for maximizing OEE.
Encouraging employees to identify and report inefficiencies and implementing a structured approach to improvement, such as PDCA (Plan, Do, Check, Act), can lead to sustained enhancements in OEE.
Conclusion
Overall Equipment Effectiveness (OEE) is a powerful tool for manufacturers looking to maximize efficiency and productivity.
By understanding and addressing the factors of Availability, Performance, and Quality, manufacturers can make informed decisions that lead to significant improvements.
The benefits of measuring and improving OEE are numerous, from cost savings and increased competitiveness to enhanced employee engagement.
By implementing strategies such as regular maintenance, employee training, lean manufacturing principles, technology, and continuous improvement, manufacturers can ensure they are operating at peak efficiency.
Embracing OEE as a key performance indicator can have a profound impact on a manufacturing operation’s success, making it an essential focus for any manufacturer aiming to thrive in today’s competitive landscape.
資料ダウンロード
QCD調達購買管理クラウド「newji」は、調達購買部門で必要なQCD管理全てを備えた、現場特化型兼クラウド型の今世紀最高の購買管理システムとなります。
ユーザー登録
調達購買業務の効率化だけでなく、システムを導入することで、コスト削減や製品・資材のステータス可視化のほか、属人化していた購買情報の共有化による内部不正防止や統制にも役立ちます。
NEWJI DX
製造業に特化したデジタルトランスフォーメーション(DX)の実現を目指す請負開発型のコンサルティングサービスです。AI、iPaaS、および先端の技術を駆使して、製造プロセスの効率化、業務効率化、チームワーク強化、コスト削減、品質向上を実現します。このサービスは、製造業の課題を深く理解し、それに対する最適なデジタルソリューションを提供することで、企業が持続的な成長とイノベーションを達成できるようサポートします。
オンライン講座
製造業、主に購買・調達部門にお勤めの方々に向けた情報を配信しております。
新任の方やベテランの方、管理職を対象とした幅広いコンテンツをご用意しております。
お問い合わせ
コストダウンが利益に直結する術だと理解していても、なかなか前に進めることができない状況。そんな時は、newjiのコストダウン自動化機能で大きく利益貢献しよう!
(Β版非公開)