- お役立ち記事
- Maximizing Operational Time in Manufacturing with Reduced MTTR (Mean Time to Repair)
月間76,176名の
製造業ご担当者様が閲覧しています*
*2025年3月31日現在のGoogle Analyticsのデータより
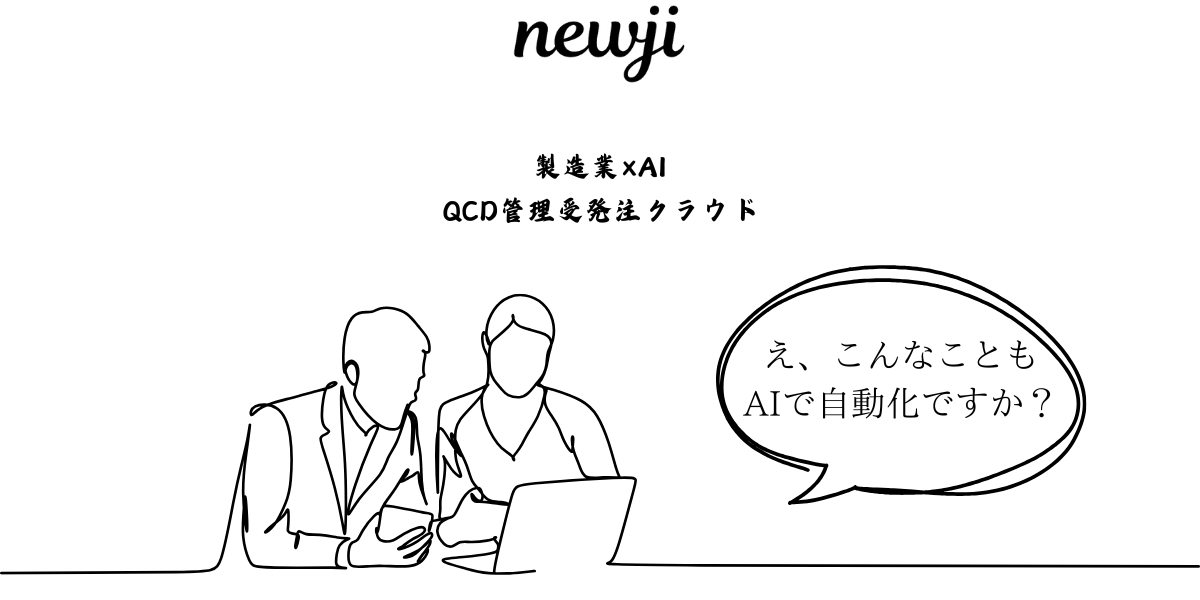
Maximizing Operational Time in Manufacturing with Reduced MTTR (Mean Time to Repair)
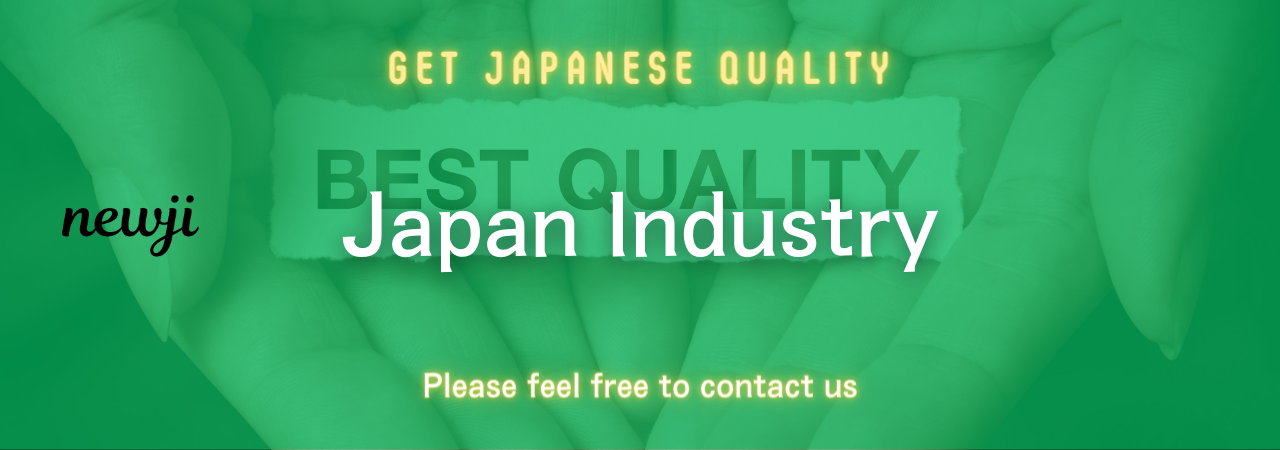
In the competitive world of manufacturing, maintaining operational efficiency is crucial.
One key metric that can help achieve this is the Mean Time to Repair (MTTR).
By focusing on reducing MTTR, manufacturers can significantly maximize their operational time.
This article explores the strategies to reduce MTTR and highlights how it positively impacts the manufacturing process.
目次
Understanding MTTR
MTTR stands for Mean Time to Repair, a metric used to measure the average time required to repair a machine or system.
It includes the time taken to diagnose the issue, fix it, and bring the equipment back to full operational status.
A lower MTTR indicates a more efficient repair process, which results in minimized downtime.
Importance of Reducing MTTR in Manufacturing
In the manufacturing industry, unplanned downtime can be costly.
When machines are down, production halts, and deadlines can be missed.
Reducing MTTR helps minimize these disruptions, ensuring that machinery is back up and running as quickly as possible.
This leads to higher productivity, better resource utilization, and ultimately, increased profits.
Enhancing Maintenance Procedures
One of the most effective ways to reduce MTTR is by enhancing maintenance procedures.
Preventative maintenance, where regular checks and servicing are carried out, can help identify potential issues before they result in significant downtime.
Predictive maintenance uses data and analytics to anticipate potential failures, allowing for timely interventions.
Training maintenance teams on best practices and ensuring they have access to the latest tools and technology can also aid in quicker repairs.
Standardizing maintenance procedures across the facility ensures a consistent approach to repairs, reducing the time taken to diagnose and fix issues.
Utilizing Advanced Diagnostics
Advanced diagnostic tools can play a crucial role in reducing MTTR.
These tools help in quickly identifying the root cause of a problem.
Modern diagnostic tools often come with features like remote monitoring and real-time data analysis, which can significantly cut down on the time needed for troubleshooting.
By integrating Internet of Things (IoT) devices into machinery, manufacturers can collect valuable data on machine performance.
This data can be analyzed to predict potential breakdowns and plan maintenance activities accordingly.
Using augmented reality (AR) technology, technicians can access step-by-step repair guides, visualize internal machinery components, and collaborate with remote experts in real-time, enhancing repair efficiency.
Streamlining Spare Parts Management
Having the right spare parts available when needed is essential for reducing MTTR.
A well-managed spare parts inventory ensures that technicians do not waste time searching for or waiting for parts.
Implementing a computerized maintenance management system (CMMS) can help track inventory levels and automatically reorder parts when they reach a specified threshold.
Organizing spare parts storage by categorizing items, labeling them clearly, and keeping detailed records of their locations can save valuable time during repairs.
Developing strong relationships with reliable suppliers can also ensure quick delivery of parts, further minimizing downtime.
Implementing Standardized Work Instructions
Creating standardized work instructions for common repair tasks can significantly reduce the time technicians spend trying to figure out how to fix an issue.
These instructions should be easily accessible and include detailed, step-by-step guidelines that technicians can follow.
Including visual aids such as diagrams, photos, and videos in the work instructions can make them even more user-friendly.
Regularly updating these instructions to reflect new processes or equipment changes ensures they remain relevant and effective.
Leveraging Team Collaboration
Encouraging collaboration among maintenance teams can lead to quicker problem-solving and reduced MTTR.
When technicians work together, they can share their expertise and experiences, helping to identify and fix issues more efficiently.
Establishing a collaborative culture involves regular team meetings to discuss ongoing projects, challenges, and solutions.
Using digital collaboration tools can facilitate communication and information sharing, even when team members are not physically together.
Continuous Improvement and Training
Continuous improvement is a philosophy that emphasizes the need for ongoing efforts to improve processes, products, and services.
In the context of reducing MTTR, this means regularly reviewing and refining maintenance procedures, diagnostic tools, and spare parts management strategies.
Providing continuous training for maintenance teams ensures they stay updated with the latest techniques and technologies.
This not only enhances their skills but also boosts their confidence and efficiency in carrying out repairs.
Conclusion
Reducing Mean Time to Repair (MTTR) is a powerful strategy for maximizing operational time in manufacturing.
By enhancing maintenance procedures, utilizing advanced diagnostics, streamlining spare parts management, implementing standardized work instructions, fostering team collaboration, and committing to continuous improvement and training, manufacturers can achieve significant reductions in MTTR.
As a result, they can enjoy increased productivity, better resource utilization, and higher profits.
In today’s competitive market, focusing on MTTR is not just an option but a necessity for staying ahead.
Do remember, always consider the specifics of your operations and tailor these strategies to fit your unique needs.
Ultimately, the goal is to create a more efficient, responsive, and resilient manufacturing environment.
資料ダウンロード
QCD管理受発注クラウド「newji」は、受発注部門で必要なQCD管理全てを備えた、現場特化型兼クラウド型の今世紀最高の受発注管理システムとなります。
ユーザー登録
受発注業務の効率化だけでなく、システムを導入することで、コスト削減や製品・資材のステータス可視化のほか、属人化していた受発注情報の共有化による内部不正防止や統制にも役立ちます。
NEWJI DX
製造業に特化したデジタルトランスフォーメーション(DX)の実現を目指す請負開発型のコンサルティングサービスです。AI、iPaaS、および先端の技術を駆使して、製造プロセスの効率化、業務効率化、チームワーク強化、コスト削減、品質向上を実現します。このサービスは、製造業の課題を深く理解し、それに対する最適なデジタルソリューションを提供することで、企業が持続的な成長とイノベーションを達成できるようサポートします。
製造業ニュース解説
製造業、主に購買・調達部門にお勤めの方々に向けた情報を配信しております。
新任の方やベテランの方、管理職を対象とした幅広いコンテンツをご用意しております。
お問い合わせ
コストダウンが利益に直結する術だと理解していても、なかなか前に進めることができない状況。そんな時は、newjiのコストダウン自動化機能で大きく利益貢献しよう!
(β版非公開)