- お役立ち記事
- Maximizing Production Efficiency Through Measuring Equipment Selection
月間76,176名の
製造業ご担当者様が閲覧しています*
*2025年3月31日現在のGoogle Analyticsのデータより
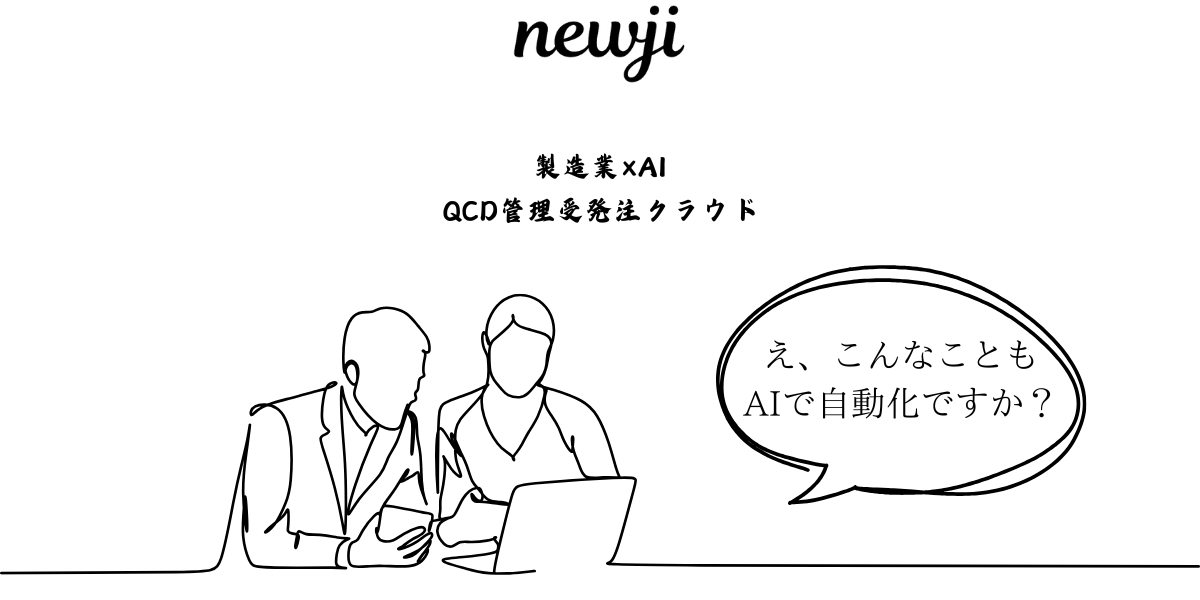
Maximizing Production Efficiency Through Measuring Equipment Selection
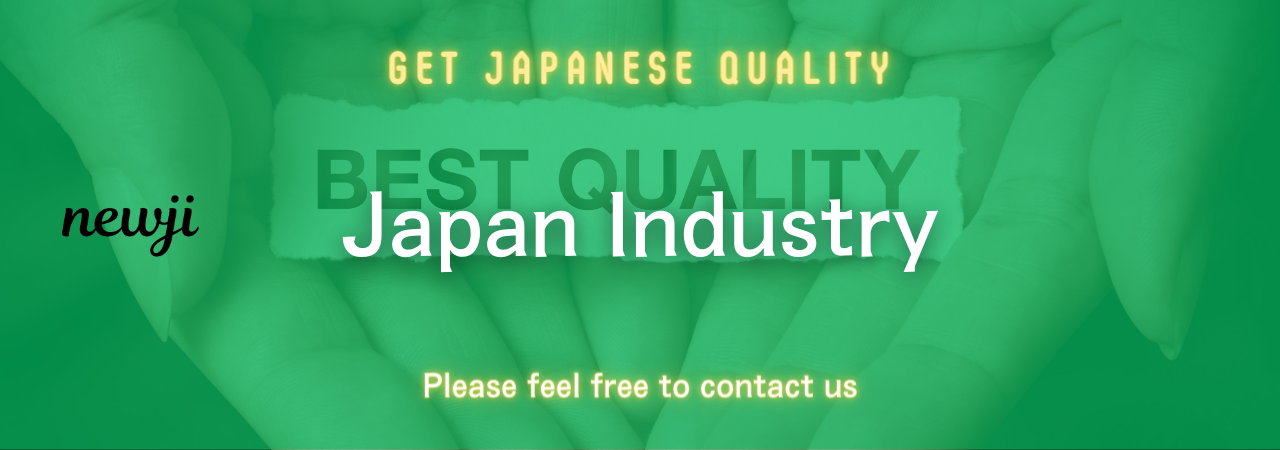
In the fast-paced world of manufacturing, maximizing production efficiency is a priority.
One of the critical aspects to achieve this goal is the careful selection of measuring equipment.
Proper measurement tools can significantly impact the overall production process, leading to better quality control and reduced waste.
By understanding and implementing the right equipment, manufacturers can streamline their operations and enhance their profitability.
目次
Understanding Production Efficiency
Before diving into the selection of measuring equipment, it’s important to understand what production efficiency actually means.
Production efficiency refers to the ability of a manufacturing system to produce the desired output at the least cost and in the shortest possible time.
It involves minimizing the use of resources while maximizing output, ensuring that each component is produced to specifications and within the allotted time frame.
The Role of Measuring Equipment in Manufacturing
Measuring equipment plays a crucial role in achieving production efficiency.
These tools are used to ensure that components are manufactured to precise specifications and tolerances.
By accurately measuring dimensions, thickness, weight, and other parameters, manufacturers can maintain consistency and quality in their products.
Proper measurement ensures that components fit together correctly, reducing the need for rework and minimizing material waste.
It also helps in identifying defects early in the production process, allowing for timely corrective actions.
Factors to Consider When Selecting Measuring Equipment
Choosing the right measuring equipment requires careful consideration of several factors.
Each factor plays a significant role in optimizing production efficiency.
1. Accuracy and Precision
One of the fundamental factors to consider is the accuracy and precision of the measuring equipment.
Accuracy refers to how close a measured value is to the true value, while precision indicates the ability of the instrument to produce consistent results.
In production, even a slight deviation can result in significant issues.
Therefore, selecting equipment with high accuracy and precision is paramount.
2. Compatibility with Production Environment
The production environment can greatly affect the performance of measuring equipment.
Factors such as temperature, humidity, and cleanliness need to be considered.
For instance, highly sensitive equipment might not function well in a dusty or high-temperature environment.
Choosing equipment that is compatible with the specific conditions of your production facility ensures reliable measurements.
3. Ease of Use
Complex measuring equipment can slow down the production process if it requires extensive training or is difficult to use.
Equipment that is user-friendly and provides clear, easy-to-understand readings can help operators quickly and accurately measure components.
This reduces downtime and increases overall efficiency.
Types of Measuring Equipment and Their Applications
There are various types of measuring equipment available, each serving different applications in manufacturing.
Here are some common types and their uses:
1. Calipers
Calipers are versatile tools used to measure the distance between two opposite sides of an object.
They can be used for both internal and external measurements.
Digital calipers offer precise readings and are widely used in industries such as automotive and aerospace for detailed measurements.
2. Micrometers
Micrometers provide high-precision measurements of small distances.
They are commonly used to measure the thickness of materials and are essential in industries where accuracy to the micrometer level is required.
Mechanical, digital, and laser micrometers are among the variations available based on the specific needs of the industry.
3. Coordinate Measuring Machines (CMM)
Coordinate Measuring Machines (CMM) are used to measure the physical geometrical characteristics of an object.
They are highly accurate and can measure complex shapes and surfaces.
CMMs are used in quality control processes to ensure that parts meet precise specifications.
4. Optical Comparators
Optical comparators project an image of a part onto a screen and magnify it for inspection.
This allows operators to compare the part against a standard template.
They are commonly used for inspecting small parts and ensuring they meet the required geometric specifications.
5. Laser Measurement Systems
Laser measurement systems use laser technology to measure distances, lengths, and other dimensions with high precision.
They are particularly useful in industries that require non-contact measurements and are often used in automated production lines.
Benefits of Using the Right Measuring Equipment
Investing in the right measuring equipment offers numerous benefits to production efficiency.
1. Improved Quality Control
Accurate measurements ensure that each component meets the required specifications.
This reduces the occurrence of defects and increases the overall quality of the products.
Consistent quality control helps build a strong reputation for the company and increases customer satisfaction.
2. Reduced Material Waste
Precise measurements minimize the need for rework and reduce material waste.
By ensuring that components are manufactured correctly the first time, manufacturers can save on raw materials and reduce production costs.
3. Enhanced Production Speed
Accurate and easy-to-use measuring equipment speeds up the production process.
Operators can measure components quickly without the need for recalibration or extensive training.
This leads to higher productivity and faster turnaround times.
Conclusion
Maximizing production efficiency is essential for manufacturers to remain competitive in today’s market.
Selecting the right measuring equipment plays a crucial role in achieving this goal.
By considering factors such as accuracy, compatibility with the production environment, and ease of use, manufacturers can ensure they are using the most effective tools for their specific needs.
Various types of measuring equipment, including calipers, micrometers, CMMs, optical comparators, and laser measurement systems, offer tailored solutions for different applications.
The right equipment not only improves quality control but also reduces material waste and enhances production speed.
By investing in proper measurement tools, manufacturers can streamline their operations, ensure consistent product quality, and ultimately increase profitability.
資料ダウンロード
QCD管理受発注クラウド「newji」は、受発注部門で必要なQCD管理全てを備えた、現場特化型兼クラウド型の今世紀最高の受発注管理システムとなります。
ユーザー登録
受発注業務の効率化だけでなく、システムを導入することで、コスト削減や製品・資材のステータス可視化のほか、属人化していた受発注情報の共有化による内部不正防止や統制にも役立ちます。
NEWJI DX
製造業に特化したデジタルトランスフォーメーション(DX)の実現を目指す請負開発型のコンサルティングサービスです。AI、iPaaS、および先端の技術を駆使して、製造プロセスの効率化、業務効率化、チームワーク強化、コスト削減、品質向上を実現します。このサービスは、製造業の課題を深く理解し、それに対する最適なデジタルソリューションを提供することで、企業が持続的な成長とイノベーションを達成できるようサポートします。
製造業ニュース解説
製造業、主に購買・調達部門にお勤めの方々に向けた情報を配信しております。
新任の方やベテランの方、管理職を対象とした幅広いコンテンツをご用意しております。
お問い合わせ
コストダウンが利益に直結する術だと理解していても、なかなか前に進めることができない状況。そんな時は、newjiのコストダウン自動化機能で大きく利益貢献しよう!
(β版非公開)