- お役立ち記事
- Measurement of the Coefficient of Friction and Countermeasures in Manufacturing
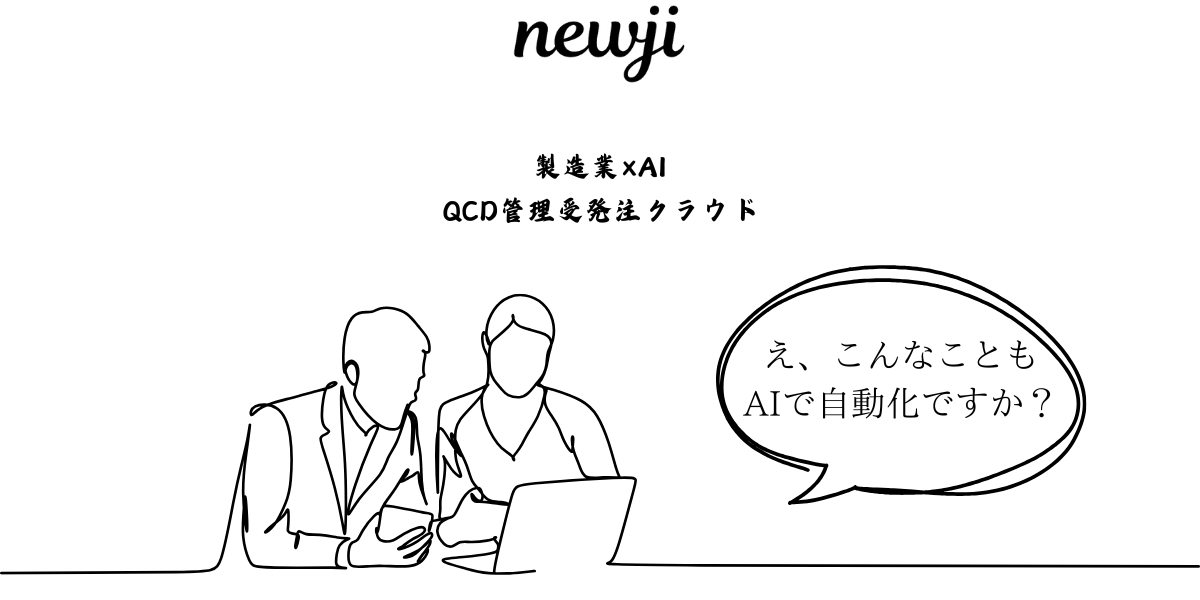
Measurement of the Coefficient of Friction and Countermeasures in Manufacturing
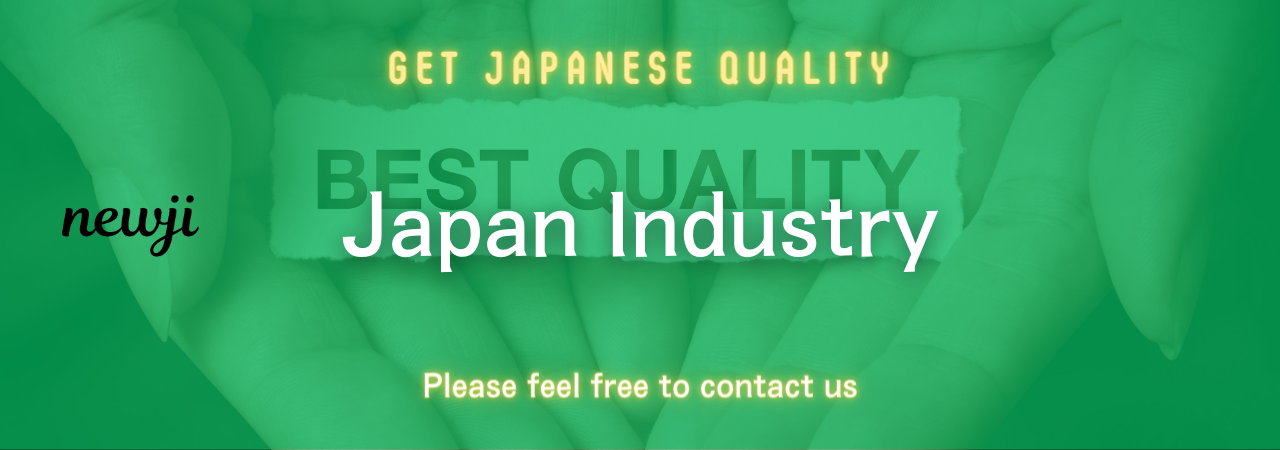
The coefficient of friction is a critical parameter in manufacturing processes.
Understanding and managing it can significantly impact the efficiency and quality of production.
In this article, we will explore the measurement of the coefficient of friction and discuss various countermeasures to optimize manufacturing operations.
目次
What is the Coefficient of Friction?
The coefficient of friction (COF) is a dimensionless number that describes the amount of friction between two surfaces in contact.
It is calculated as the ratio of the force of friction between the objects and the force pressing them together.
There are two types of friction: static and kinetic.
Static friction occurs when the objects are not moving relative to each other, while kinetic friction happens when there is relative motion.
Importance of Measuring COF in Manufacturing
Measuring the coefficient of friction is crucial in manufacturing for several reasons.
Firstly, it helps in predicting product performance.
A better understanding of frictional forces can lead to the production of high-quality goods with better durability.
Secondly, it enhances process efficiency.
By optimizing friction, manufacturers can reduce wear and tear on machinery, leading to lower maintenance costs and longer equipment lifespan.
Lastly, COF measurement supports compliance with safety standards.
Many industries have specific regulations regarding acceptable levels of frictional forces to prevent accidents and ensure safe operation.
Methods for Measuring the Coefficient of Friction
There are several techniques to measure the coefficient of friction in a manufacturing setting.
Here are some common methods:
1. Pin-on-Disk Test
This method involves a pin (or a ball) pressed against a rotating disk.
The force required to move the pin across the disk is measured.
This technique is widely used due to its simplicity and accuracy.
2. Inclined Plane Test
In this test, an object is placed on an inclined plane, which is gradually tilted until the object starts to slide.
The angle at which the object begins to move is noted, and the COF is calculated using trigonometric functions.
Although this method is less precise, it is useful for quick, rough estimates.
3. Tribometer Devices
Tribometers are specialized instruments designed to measure friction, wear, and lubrication properties.
They generally provide high precision and can be used for a wide variety of materials and surfaces.
Factors Affecting the Coefficient of Friction
Several factors can influence the COF between two surfaces.
Understanding these factors can help in choosing appropriate countermeasures to manage friction.
1. Material Properties
The type of material significantly affects friction.
Metals, plastics, and ceramics each have different frictional characteristics.
The surface roughness, hardness, and elasticity of the materials also play a crucial role.
2. Surface Treatment
Surface coatings, treatments, and lubricants can drastically alter the COF.
For example, adding a thin layer of lubrication can significantly reduce friction.
3. Environment
Temperature, humidity, and presence of contaminants (like dust or oil) can impact friction.
Ensuring a controlled environment is essential for reliable COF measurements and consistent manufacturing outcomes.
Countermeasures to Manage Friction in Manufacturing
Once the COF is understood, several countermeasures can be implemented to optimize friction levels in manufacturing processes:
1. Surface Coatings
Applying coatings like Teflon or ceramics can significantly reduce friction.
These coatings also offer additional benefits like increased resistance to wear, corrosion, and heat.
2. Lubricants
Using the right type of lubricant can hugely impact the COF.
Liquid, solid, or gaseous lubricants can be used depending on the application.
Regular maintenance is required to ensure that the lubrication remains effective.
3. Material Selection
Choosing materials with favorable frictional properties can eliminate issues from the outset.
Advanced materials like composites and specialized alloys often have better performance concerning friction.
4. Surface Texturing
Micro-texturing surfaces using advanced techniques like laser texturing can create controlled patterns that optimize friction.
These technologies allow for highly tailored friction management.
5. Environmental Control
Maintaining a controlled environment in terms of temperature and humidity helps in achieving consistent COF results.
This can be crucial in precision manufacturing settings.
Conclusion
The measurement of the coefficient of friction and its proper management are vital aspects of modern manufacturing.
By understanding the factors that affect COF and utilizing the appropriate countermeasures, manufacturers can improve product quality, enhance process efficiency, and ensure compliance with safety standards.
Leveraging advanced measurement techniques and innovative solutions such as surface coatings, lubricants, and material selection can lead to optimal friction management.
This, in turn, will contribute significantly to the overall success and sustainability of manufacturing operations.
資料ダウンロード
QCD調達購買管理クラウド「newji」は、調達購買部門で必要なQCD管理全てを備えた、現場特化型兼クラウド型の今世紀最高の購買管理システムとなります。
ユーザー登録
調達購買業務の効率化だけでなく、システムを導入することで、コスト削減や製品・資材のステータス可視化のほか、属人化していた購買情報の共有化による内部不正防止や統制にも役立ちます。
NEWJI DX
製造業に特化したデジタルトランスフォーメーション(DX)の実現を目指す請負開発型のコンサルティングサービスです。AI、iPaaS、および先端の技術を駆使して、製造プロセスの効率化、業務効率化、チームワーク強化、コスト削減、品質向上を実現します。このサービスは、製造業の課題を深く理解し、それに対する最適なデジタルソリューションを提供することで、企業が持続的な成長とイノベーションを達成できるようサポートします。
オンライン講座
製造業、主に購買・調達部門にお勤めの方々に向けた情報を配信しております。
新任の方やベテランの方、管理職を対象とした幅広いコンテンツをご用意しております。
お問い合わせ
コストダウンが利益に直結する術だと理解していても、なかなか前に進めることができない状況。そんな時は、newjiのコストダウン自動化機能で大きく利益貢献しよう!
(Β版非公開)