- お役立ち記事
- Measures taken by the purchasing department to reduce transportation costs and stabilize supply
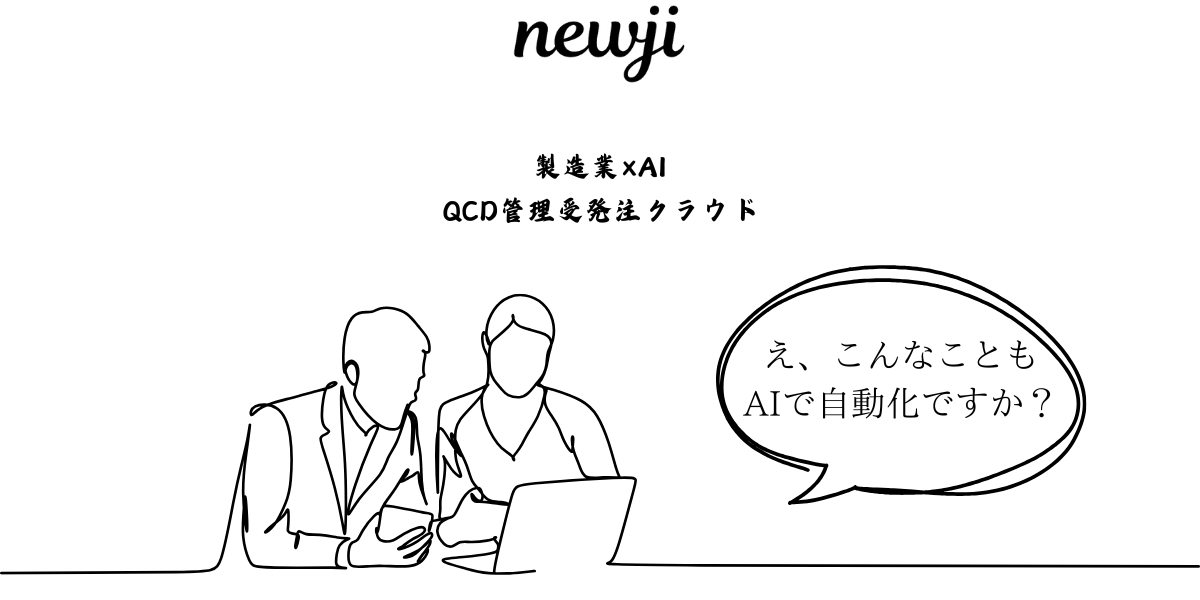
Measures taken by the purchasing department to reduce transportation costs and stabilize supply
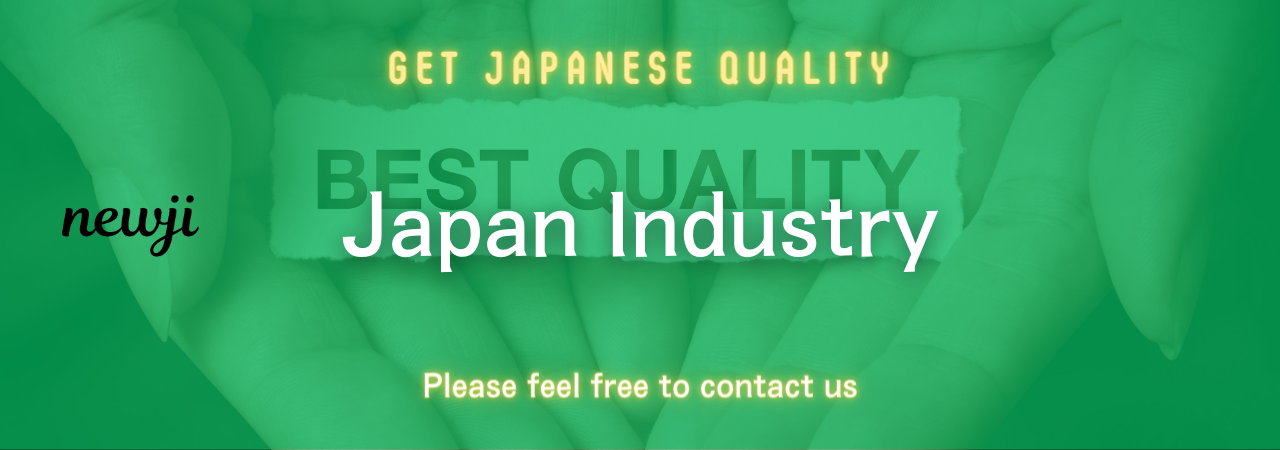
目次
Understanding the Role of the Purchasing Department
The purchasing department plays a critical role in any organization, especially when it comes to managing costs and ensuring stable supply chains.
Its primary responsibility is to procure goods and services that a company needs at the best possible prices and terms.
Beyond the procurement itself, the department also seeks to optimize logistics to minimize transportation costs and maintain a steady supply of materials.
In today’s globalized market, transportation costs can significantly impact a company’s bottom line.
They are influenced by factors like fuel prices, shipping routes, and logistics efficiency.
Thus, the purchasing department must adopt innovative strategies to control these costs while ensuring that supplies are delivered on time.
Strategies to Reduce Transportation Costs
Reducing transportation costs is a multifaceted challenge that requires strategic planning and execution.
Here are some of the measures purchasing departments commonly take:
1. Optimizing Supplier Selection
Choosing the right suppliers can make a significant difference in transportation costs.
The purchasing department assesses suppliers based on their proximity, reliability, and the transportation networks they use.
By selecting suppliers closer to production or distribution centers, companies can drastically cut shipping expenses.
Additionally, using suppliers with efficient logistics can improve delivery speeds and reduce costs.
2. Consolidating Shipments
Another effective method to reduce transportation costs is through shipment consolidation.
By combining several smaller shipments into one larger shipment, companies can take advantage of bulk shipping discounts.
The purchasing department coordinates with suppliers to schedule deliveries that maximize shipping efficiency.
3. Negotiating Better Freight Rates
Effective negotiation is key to reducing transportation expenses.
Purchasing departments often work with freight carriers to negotiate better rates.
They leverage the volume of goods shipped and long-term business potential to secure competitive pricing.
Relationships with carriers can help organizations benefit from favorable terms, leading to lower costs.
4. Exploring Alternative Transportation Modes
Depending on the nature of goods and required delivery timelines, alternative modes of transport may offer cost savings.
For instance, using rail instead of road transport, where feasible, can be more economical.
Similarly, sea freight is generally less expensive than air freight when time constraints allow.
The purchasing department evaluates these options to determine the most cost-effective solution for their logistics needs.
Ensuring Supply Stability
In addition to managing transportation costs, the purchasing department is responsible for ensuring a stable supply of materials.
Supply chain disruptions can severely affect production schedules and company performance.
Here are some strategies employed to enhance supply stability:
1. Building Strong Supplier Relationships
Strong supplier relationships are fundamental to supply chain stability.
The purchasing department invests time in maintaining open communication and fostering collaboration with suppliers.
By building trust and mutual understanding, companies can gain insights into supplier capabilities and potential risks.
This engagement allows for proactive problem-solving and ensures smoother operations.
2. Diversifying the Supplier Base
Relying on a single supplier can be risky, particularly if they face operational disruptions.
Diversifying the supplier base reduces dependency on one source and enhances supply chain resilience.
The purchasing department identifies and evaluates multiple suppliers for each critical component to mitigate risks associated with supplier failure.
3. Monitoring and Forecasting Demand
A forward-looking approach is crucial for supply stability.
The purchasing department closely monitors market trends and collaborates with sales and operations teams to anticipate changes in demand.
Regular forecasting allows them to adjust procurement plans accordingly, avoiding stockouts or excess inventory.
4. Implementing Inventory Management Systems
Advanced inventory management systems help optimize stock levels and improve supply chain efficiency.
By using technologies like just-in-time (JIT) inventory, companies can reduce carrying costs while ensuring they have enough stock to meet demand.
The purchasing department employs these systems to maintain the right balance between inventory costs and supply reliability.
Leveraging Technology and Innovation
Modern technology offers numerous opportunities for purchasing departments to enhance transportation cost management and supply stability.
Digital tools and software enable better data analysis, forecasting, and logistics management.
For example, using advanced analytics, departments can track shipment patterns, identify inefficiencies, and optimize routes.
Automation plays an increasing role in streamlining procurement processes.
Automated systems can handle order processing, supplier communication, and inventory management with minimal human intervention.
This reduces human error and saves time, allowing the purchasing department to focus on strategic initiatives.
Furthermore, investing in sustainable procurement practices can align transportation and supply strategies with environmental goals.
Green logistics, such as using eco-friendly packaging and adopting fuel-efficient transportation modes, can lead to cost savings and reduce the company’s carbon footprint.
Conclusion
The purchasing department’s efforts to reduce transportation costs and stabilize supply are vital to an organization’s success.
By strategically selecting suppliers, negotiating freight rates, and employing technology, they can optimize transportation expenses.
Moreover, maintaining supplier relationships and diversifying sources ensure a stable supply chain.
In a competitive market, these initiatives can provide a company with a significant advantage, helping it deliver products efficiently and sustainably.
By continuously adapting to market changes and leveraging innovation, the purchasing department remains a cornerstone of operational efficiency.
資料ダウンロード
QCD調達購買管理クラウド「newji」は、調達購買部門で必要なQCD管理全てを備えた、現場特化型兼クラウド型の今世紀最高の購買管理システムとなります。
ユーザー登録
調達購買業務の効率化だけでなく、システムを導入することで、コスト削減や製品・資材のステータス可視化のほか、属人化していた購買情報の共有化による内部不正防止や統制にも役立ちます。
NEWJI DX
製造業に特化したデジタルトランスフォーメーション(DX)の実現を目指す請負開発型のコンサルティングサービスです。AI、iPaaS、および先端の技術を駆使して、製造プロセスの効率化、業務効率化、チームワーク強化、コスト削減、品質向上を実現します。このサービスは、製造業の課題を深く理解し、それに対する最適なデジタルソリューションを提供することで、企業が持続的な成長とイノベーションを達成できるようサポートします。
オンライン講座
製造業、主に購買・調達部門にお勤めの方々に向けた情報を配信しております。
新任の方やベテランの方、管理職を対象とした幅広いコンテンツをご用意しております。
お問い合わせ
コストダウンが利益に直結する術だと理解していても、なかなか前に進めることができない状況。そんな時は、newjiのコストダウン自動化機能で大きく利益貢献しよう!
(Β版非公開)