- お役立ち記事
- Measures to avoid supply chain disruption risks that purchasing departments are paying attention to
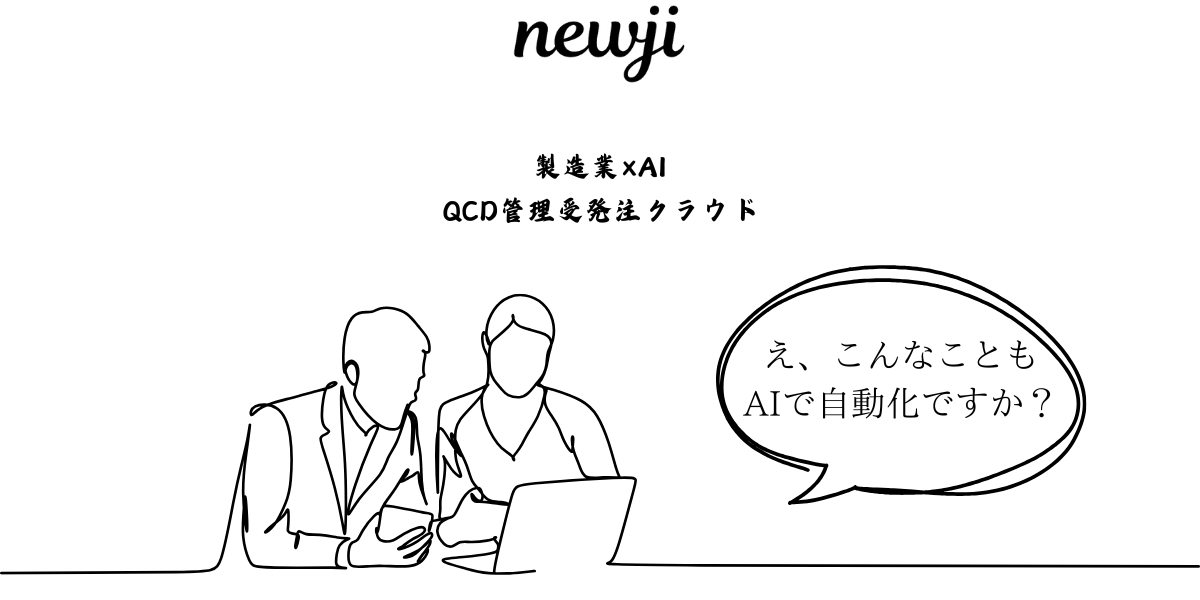
Measures to avoid supply chain disruption risks that purchasing departments are paying attention to
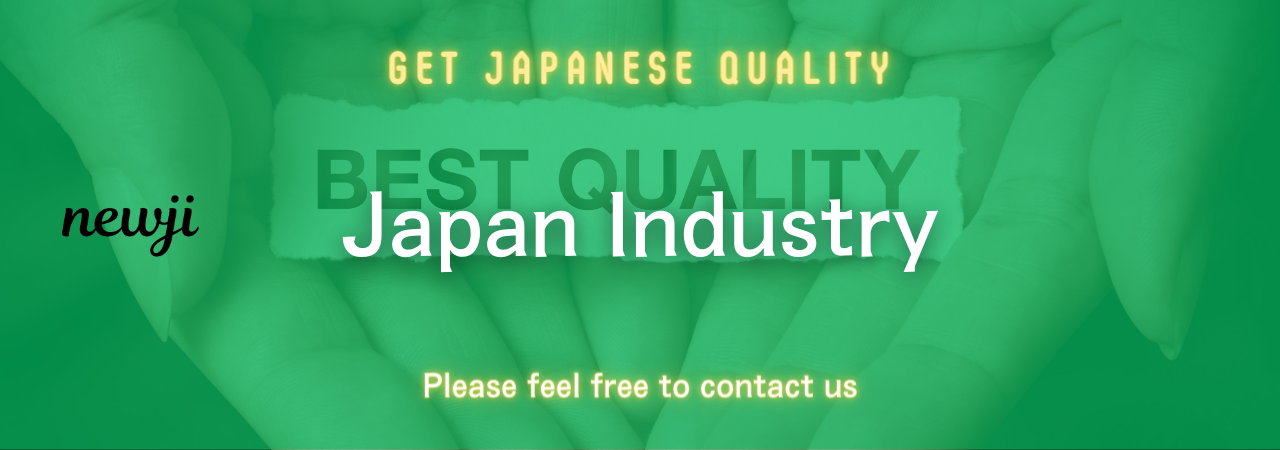
目次
Understanding Supply Chain Disruption Risks
The supply chain is the backbone of any business that deals with production, distribution, or retail.
A single hiccup in the chain can lead to significant disruptions that affect the entire business.
With globalization and increasing complexity in supply chains, the risk of disruptions has heightened.
The purchasing departments in companies play a pivotal role in identifying and mitigating these risks.
Their proactive measures are crucial to ensure smooth operations and sustain a competitive edge.
The Causes of Supply Chain Disruptions
Before we delve into the measures to avoid disruptions, it’s essential to understand what causes these hiccups in the first place.
Some common causes include:
1. **Natural Disasters:**
Earthquakes, floods, hurricanes, or any other natural disasters can stall production or transport processes.
2. **Political Instability:**
Changes in government policies, trade wars, sanctions, or political unrest can affect supply chain continuity.
3. **Economic Shifts:**
Recessions, currency fluctuations, and changes in global economic policies can cause supply chain stress.
4. **Supplier Issues:**
Supplier bankruptcy, quality issues, or production failures can lead to bottlenecks.
5. **Technological Failures:**
Cyber-attacks, system failures, or outdated technology can disrupt supply chain operations.
By understanding these causes, purchasing departments can implement strategies to mitigate potential risks proactively.
Measures to Avoid Supply Chain Disruption Risks
Purchasing departments can adopt several strategies to reduce the impact of disruptions and maintain a steady supply chain flow.
Diversification of Suppliers
Relying on a single supplier or a concentrated geographic location for all your materials and products can be risky.
By diversifying the supplier base, businesses can reduce dependency and spread the risk.
This means reaching out to suppliers in different regions and having multiple sources for the same product.
While it may take more effort to establish relationships with various suppliers, the benefits far outweigh the risks in times of crisis.
Building Strong Supplier Relationships
Investing time and resources in building strong relationships with suppliers can bear fruit during challenging times.
Establishing a collaborative partnership fosters trust and transparency.
It encourages suppliers to prioritize your needs, offer innovative solutions, and provide support during disruptions.
Regular communication and joint planning can strengthen these bonds, making the supply chain more resilient.
Implementing Advanced Technology
Leveraging technology can significantly improve supply chain visibility and efficiency.
Implementing tools like artificial intelligence, big data analytics, and Internet of Things (IoT) can help in real-time monitoring and predictive analysis.
These technologies allow businesses to foresee potential disruptions and make data-driven decisions to mitigate risks.
Automation and digital transformation also streamline processes, reducing the dependency on manual operations which might be vulnerable to errors.
Inventory Management Optimization
Balancing inventory levels is crucial in mitigating supply chain risks.
While holding excess inventory can be costly, having too little can lead to shortages during unexpected disruptions.
Purchasing departments must work on optimizing inventory levels through just-in-time inventory systems or safety stock strategies.
This ensures there is enough buffer to withstand supply chain shocks without overburdening the business financially.
Risk Assessment and Management Strategies
Conducting regular risk assessments helps identify vulnerabilities within the supply chain.
Purchasing departments can work alongside risk management experts to develop strategies tailored to their business needs.
This includes business continuity planning, disaster recovery plans, and insurance solutions.
Having a structured risk management strategy in place allows businesses to respond swiftly and effectively when a disruption occurs.
The Role of Communication
Communication is a vital aspect of supply chain management and plays a significant role in avoiding disruptions.
Purchasing departments must foster open lines of communication not only internally but also with suppliers, logistic partners, and all stakeholders involved in the supply chain.
Transparent Communication with Suppliers
Engage in regular discussions with suppliers about supply projections, demand forecasts, and potential risks.
Sharing appropriate information ensures everyone is on the same page and can collaboratively work toward minimizing disruption risks.
Internal Stakeholder Collaboration
Purchasing departments should maintain seamless communication with other departments such as production, sales, and finance.
Cross-departmental collaboration ensures that any changes or updates in the supply chain are efficiently communicated and managed.
Conclusion
Supply chain disruptions pose significant risks to businesses, affecting everything from production efficiency to customer satisfaction.
By implementing the aforementioned measures, purchasing departments can play a pivotal role in minimizing these risks.
Diversifying suppliers, building robust relationships, leveraging technology, optimizing inventory, and enhancing communication are just some ways to protect the supply chain from potential disruptions.
With these proactive strategies in place, businesses can ensure continuous and efficient operations, safeguarding their reputation and profitability.
資料ダウンロード
QCD調達購買管理クラウド「newji」は、調達購買部門で必要なQCD管理全てを備えた、現場特化型兼クラウド型の今世紀最高の購買管理システムとなります。
ユーザー登録
調達購買業務の効率化だけでなく、システムを導入することで、コスト削減や製品・資材のステータス可視化のほか、属人化していた購買情報の共有化による内部不正防止や統制にも役立ちます。
NEWJI DX
製造業に特化したデジタルトランスフォーメーション(DX)の実現を目指す請負開発型のコンサルティングサービスです。AI、iPaaS、および先端の技術を駆使して、製造プロセスの効率化、業務効率化、チームワーク強化、コスト削減、品質向上を実現します。このサービスは、製造業の課題を深く理解し、それに対する最適なデジタルソリューションを提供することで、企業が持続的な成長とイノベーションを達成できるようサポートします。
オンライン講座
製造業、主に購買・調達部門にお勤めの方々に向けた情報を配信しております。
新任の方やベテランの方、管理職を対象とした幅広いコンテンツをご用意しております。
お問い合わせ
コストダウンが利益に直結する術だと理解していても、なかなか前に進めることができない状況。そんな時は、newjiのコストダウン自動化機能で大きく利益貢献しよう!
(Β版非公開)