- お役立ち記事
- Measures to improve market responsiveness achieved by the purchasing department by shortening the material procurement process
月間76,176名の
製造業ご担当者様が閲覧しています*
*2025年3月31日現在のGoogle Analyticsのデータより
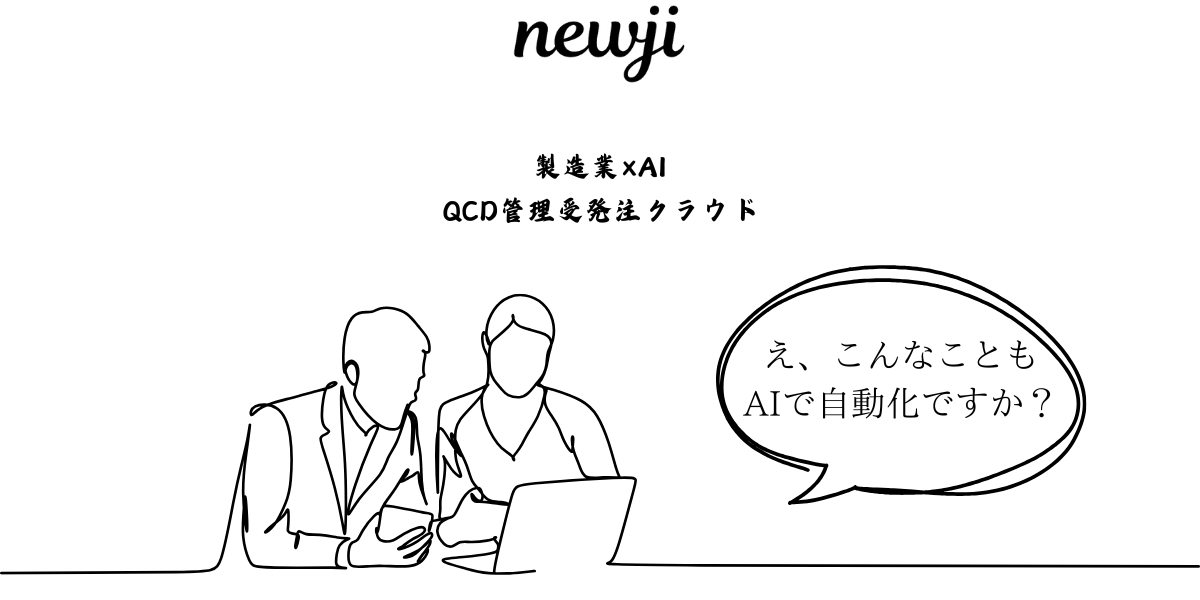
Measures to improve market responsiveness achieved by the purchasing department by shortening the material procurement process
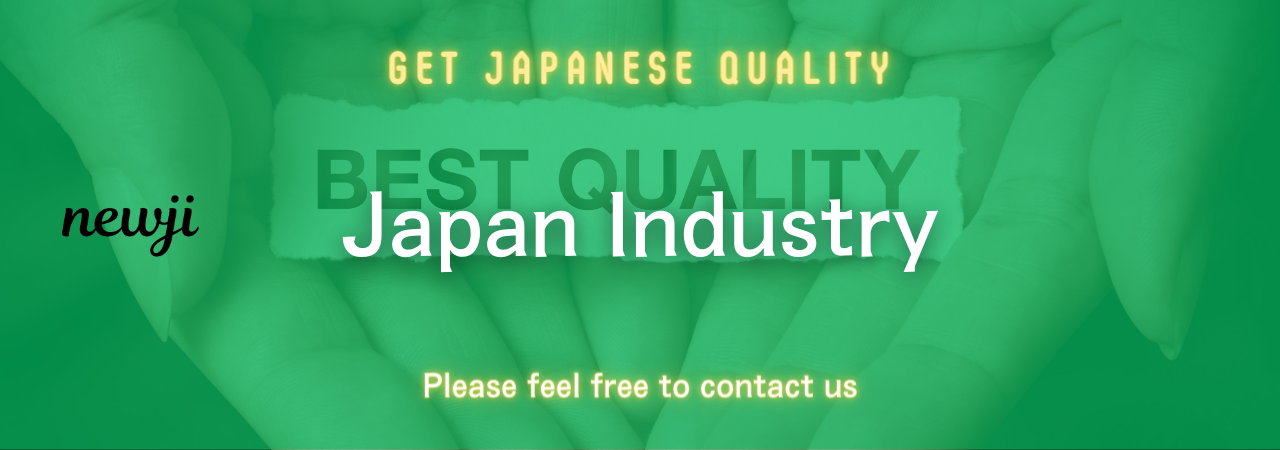
目次
Understanding Market Responsiveness
Market responsiveness refers to a company’s ability to react quickly and effectively to changes in the market environment.
This adaptability is crucial in the modern business landscape, where consumer preferences, technological advancements, and competitive dynamics evolve rapidly.
Companies that fail to respond to these changes risk losing their competitive edge.
For businesses, being responsive can mean different things.
It can involve adjusting product offerings, updating marketing strategies, or refining customer service approaches.
However, one of the most critical areas that often require quick adaptation is the procurement process.
This is where the purchasing department plays a pivotal role.
The Role of the Purchasing Department
The purchasing department is responsible for acquiring the necessary materials and services that a company needs to function efficiently.
Its core responsibilities include managing supplier relationships, negotiating contracts, and ensuring the timely delivery of goods.
With market demands constantly in flux, the purchasing department must consistently evaluate and refine its processes to respond effectively.
A streamlined procurement process can significantly enhance a company’s market responsiveness.
It enables a business to adapt to market changes by quickly securing the right materials at the right time, thereby minimizing disruptions in production and meeting customer demands promptly.
Challenges in Material Procurement
The material procurement process is fraught with challenges that can impede a company’s ability to respond to market changes.
These include long lead times, supplier dependencies, fluctuating material costs, and internal procedural delays.
Lead times in procurement can vary widely depending on the material and supplier.
Prolonged lead times can leave a company vulnerable to shortages or excess inventory, both of which are costly.
Dependence on a limited number of suppliers can pose significant risks if these suppliers face disruptions.
Moreover, fluctuating costs can strain budgets and affect pricing strategies.
Internally, bureaucratic processes can slow down procurement, adding to delays.
Strategies to Shorten the Procurement Process
To overcome these challenges, the purchasing department can implement several strategies to shorten the material procurement process.
These strategies are designed to enhance efficiency, reduce lead times, and improve supplier management.
1. Digital Transformation in Procurement
Leveraging digital tools and technologies is a crucial step towards modernizing the procurement process.
Implementing procurement software can automate routine tasks, facilitate better communication with suppliers, and provide real-time tracking of orders.
This digital transformation not only speeds up the process but also increases accuracy and reduces errors.
2. Supplier Relationship Management
Building strong relationships with suppliers is essential for streamlined procurement.
By working closely with suppliers, companies can negotiate better terms, secure priority delivery, and gain insights into potential market changes.
Regular communication and collaboration can help anticipate and mitigate risks before they become problematic.
3. Strategic Sourcing
Strategic sourcing involves analyzing and selecting suppliers based on a comprehensive evaluation of their capabilities, costs, and reliability.
By choosing the right suppliers and maintaining a diversified supplier base, companies can minimize dependencies and improve their agility in responding to market changes.
4. Inventory Management
Effective inventory management is crucial for reducing lead times and mitigating market volatility.
Adopting techniques such as Just-In-Time (JIT) can help align production schedules with market demand.
This minimizes excess inventory and the associated carrying costs, while ensuring materials are available as needed.
5. Simplifying Internal Processes
Internal procedures in the purchasing department should be regularly reviewed and optimized.
Streamlining approval processes, reducing paperwork, and enabling cross-departmental collaboration can remove bottlenecks and accelerate procurement decisions.
The Impact of a Shortened Procurement Process
Shortening the material procurement process significantly impacts a company’s ability to be responsive to market needs.
A faster procurement cycle enables businesses to adjust their production schedules more swiftly, ensuring that they can meet customer demand promptly.
By reducing lead times and enhancing supply chain efficiency, companies improve their operational agility.
This flexibility allows businesses to capitalize on emerging market opportunities, adapt to competitive pressures, and deliver greater value to customers.
Moreover, a responsive procurement process can lead to cost savings through reduced inventory holding costs and optimized supplier terms.
These savings can be reinvested into other areas of the business, fueling innovation and growth.
Conclusion
In today’s dynamic market environment, the purchasing department must play an active role in enhancing a company’s responsiveness.
By implementing strategies to shorten the material procurement process, businesses can respond to market changes efficiently and effectively.
The journey towards an agile procurement process begins with embracing digital transformation, fostering robust supplier relationships, engaging in strategic sourcing, managing inventory effectively, and simplifying internal processes.
These efforts not only improve market responsiveness but also strengthen a company’s overall competitiveness in the marketplace.
By recognizing the importance of a streamlined procurement process, companies can position themselves for long-term success in an ever-changing business landscape.
資料ダウンロード
QCD管理受発注クラウド「newji」は、受発注部門で必要なQCD管理全てを備えた、現場特化型兼クラウド型の今世紀最高の受発注管理システムとなります。
ユーザー登録
受発注業務の効率化だけでなく、システムを導入することで、コスト削減や製品・資材のステータス可視化のほか、属人化していた受発注情報の共有化による内部不正防止や統制にも役立ちます。
NEWJI DX
製造業に特化したデジタルトランスフォーメーション(DX)の実現を目指す請負開発型のコンサルティングサービスです。AI、iPaaS、および先端の技術を駆使して、製造プロセスの効率化、業務効率化、チームワーク強化、コスト削減、品質向上を実現します。このサービスは、製造業の課題を深く理解し、それに対する最適なデジタルソリューションを提供することで、企業が持続的な成長とイノベーションを達成できるようサポートします。
製造業ニュース解説
製造業、主に購買・調達部門にお勤めの方々に向けた情報を配信しております。
新任の方やベテランの方、管理職を対象とした幅広いコンテンツをご用意しております。
お問い合わせ
コストダウンが利益に直結する術だと理解していても、なかなか前に進めることができない状況。そんな時は、newjiのコストダウン自動化機能で大きく利益貢献しよう!
(β版非公開)