- お役立ち記事
- Measures to improve the flexibility of a multi-product production line at the prototyping stage
月間76,176名の
製造業ご担当者様が閲覧しています*
*2025年3月31日現在のGoogle Analyticsのデータより
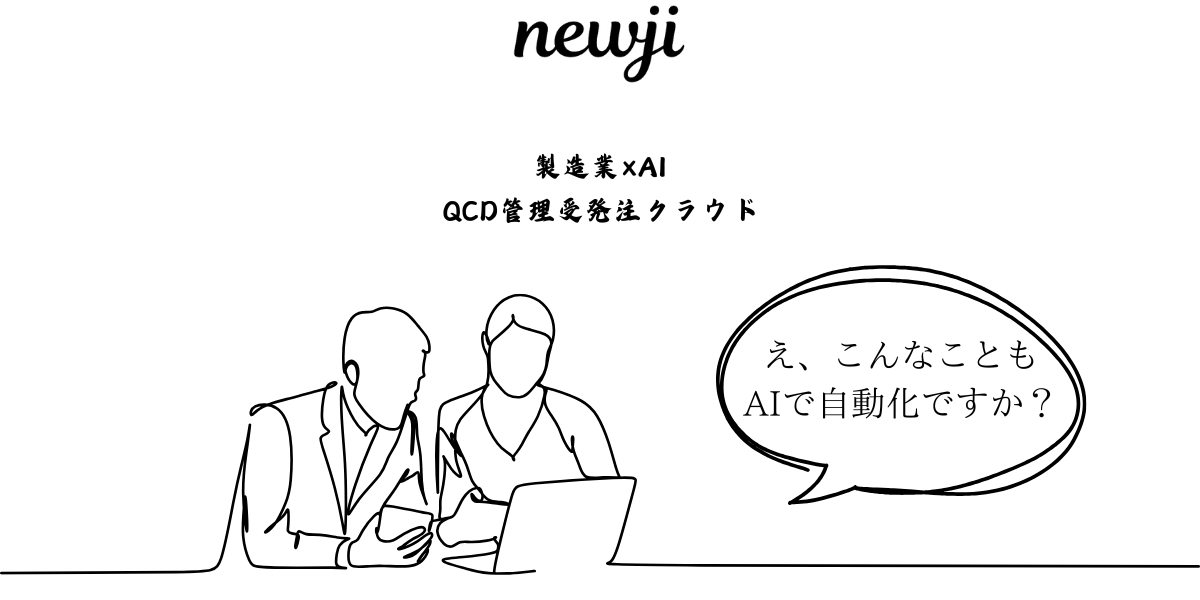
Measures to improve the flexibility of a multi-product production line at the prototyping stage
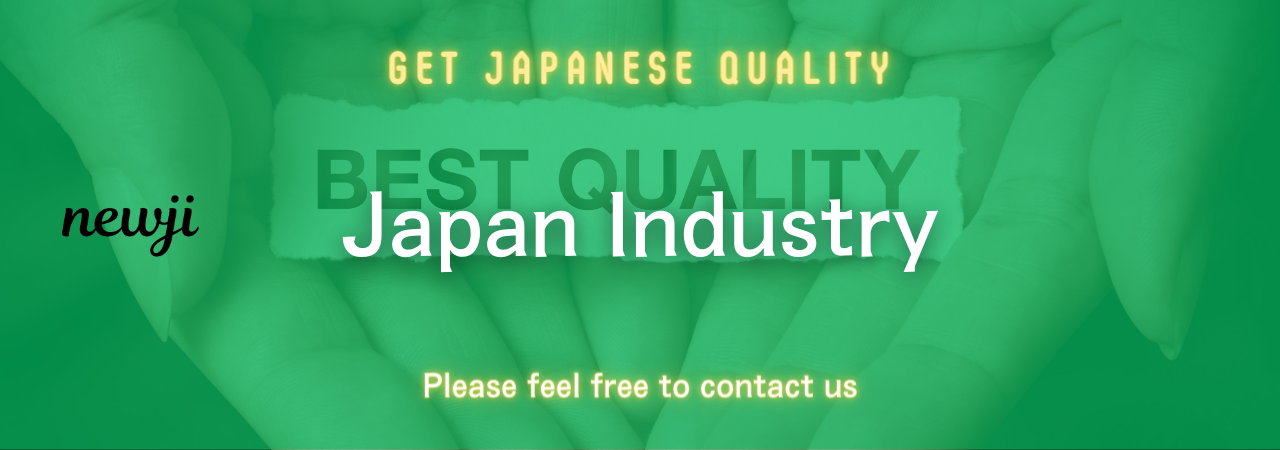
目次
Introduction
In today’s rapidly evolving market landscape, flexibility is a key factor that defines the success of manufacturing industries.
The need to adapt to various product requirements with minimal downtime has become paramount.
This is especially true at the prototyping stage of a multi-product production line.
The ability to switch between products seamlessly and efficiently can significantly improve productivity and save costs.
This article delves into practical measures for enhancing the flexibility of a multi-product production line at the prototyping stage.
Understanding the Challenges
Before moving into the solutions, it is crucial to understand the challenges faced by production lines during the prototyping phase.
Multi-product lines encounter issues like frequent changes in specifications, varying production volumes, and unique tooling requirements.
These challenges can lead to bottlenecks and increased lead times if not managed properly.
Frequent Changes in Specifications
During the prototyping stage, specifications often change as products evolve based on testing and feedback.
This requires the production line to adjust swiftly without affecting other processes.
The inability to accommodate these changes can result in delays and increased production costs.
Varying Production Volumes
Products in the prototyping phase usually have lower production volumes which can fluctuate based on demand and development progress.
A production line must efficiently handle these variations without compromising the quality and cost-effectiveness.
Unique Tooling Requirements
Each product may require specific tools or equipment, especially when new technologies or components are involved.
The need to set up and adjust tools quickly without minimizing downtime is imperative.
Measures to Enhance Flexibility
To address these challenges, there are specific measures that can be taken to improve the flexibility of a multi-product production line during the prototyping stage.
Implement Modular Production Systems
Modular production systems divide the production line into independent, interchangeable modules.
These modules can be reconfigured to accommodate different products and specifications easily.
By using standardized interfaces and connections, modules can be swapped or adjusted without requiring extensive downtime.
This approach allows for rapid changes and enhances the line’s adaptability to new products.
Adopt Lean Manufacturing Principles
Lean manufacturing focuses on reducing waste and improving process efficiency.
Principles like Just-In-Time (JIT) production ensure that parts and materials are available when needed, reducing inventory costs.
By streamlining workflows, lean practices help in maintaining high flexibility at the prototyping stage.
Invest in Advanced Technologies
The use of advanced technologies like robotics, IoT, and AI can significantly contribute to a flexible production line.
Robots can be programmed to handle various tasks, and changes in product designs can be managed efficiently.
IoT devices provide real-time data on the production process, allowing managers to make informed decisions quickly.
AI can optimize scheduling and resource allocation, enhancing the overall flexibility of the production line.
Embrace Quick Changeover Techniques
Quick changeover techniques, also known as Single-Minute Exchange of Dies (SMED), reduce the time it takes to switch from one product to another.
This involves pre-planning and organizing the changeover process to eliminate unnecessary steps.
Techniques include using jigs, fixtures, and scribing marks for rapid tool position adjustments.
Focus on Workforce Training
Employees play a vital role in the adaptability and efficiency of the production line.
Investing in workforce training programs equips workers with the skills needed to handle multiple products and processes.
A flexible and well-trained workforce can quickly adapt to changes, reducing downtime and production delays.
Case Study: Successful Implementation
To illustrate the effectiveness of these measures, let’s take a look at a case study from the automotive industry.
A car manufacturer faced significant challenges in its multi-product prototyping line due to varying customer demands.
The implementation of modular production systems allowed them to switch between different car models without impacting productivity.
Additionally, adopting lean manufacturing principles reduced waste and improved process efficiency.
The workforce underwent extensive training to ensure adaptability to new technologies and processes.
As a result, the manufacturer saw a 30% reduction in lead time and a substantial increase in flexibility.
Conclusion
Improving the flexibility of a multi-product production line at the prototyping stage is vital for maintaining competitiveness in today’s market.
By implementing modular systems, adopting lean principles, investing in advanced technologies, embracing quick changeover techniques, and focusing on workforce training, production lines can become more adaptable and efficient.
Ultimately, these measures can lead to substantial cost savings, reduced lead times, and the ability to meet diverse product requirements seamlessly.
資料ダウンロード
QCD管理受発注クラウド「newji」は、受発注部門で必要なQCD管理全てを備えた、現場特化型兼クラウド型の今世紀最高の受発注管理システムとなります。
ユーザー登録
受発注業務の効率化だけでなく、システムを導入することで、コスト削減や製品・資材のステータス可視化のほか、属人化していた受発注情報の共有化による内部不正防止や統制にも役立ちます。
NEWJI DX
製造業に特化したデジタルトランスフォーメーション(DX)の実現を目指す請負開発型のコンサルティングサービスです。AI、iPaaS、および先端の技術を駆使して、製造プロセスの効率化、業務効率化、チームワーク強化、コスト削減、品質向上を実現します。このサービスは、製造業の課題を深く理解し、それに対する最適なデジタルソリューションを提供することで、企業が持続的な成長とイノベーションを達成できるようサポートします。
製造業ニュース解説
製造業、主に購買・調達部門にお勤めの方々に向けた情報を配信しております。
新任の方やベテランの方、管理職を対象とした幅広いコンテンツをご用意しております。
お問い合わせ
コストダウンが利益に直結する術だと理解していても、なかなか前に進めることができない状況。そんな時は、newjiのコストダウン自動化機能で大きく利益貢献しよう!
(β版非公開)